- お役立ち記事
- Fundamentals of impact loads and impact stress, measurement and analysis methods, and application points for strength design
月間77,185名の
製造業ご担当者様が閲覧しています*
*2025年2月28日現在のGoogle Analyticsのデータより
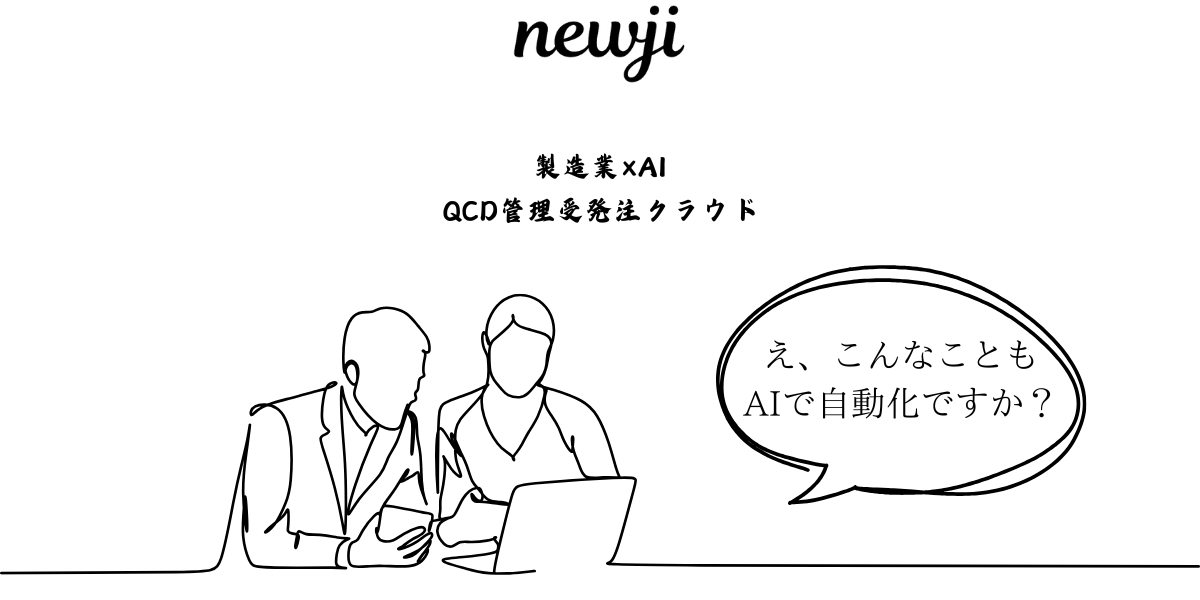
Fundamentals of impact loads and impact stress, measurement and analysis methods, and application points for strength design
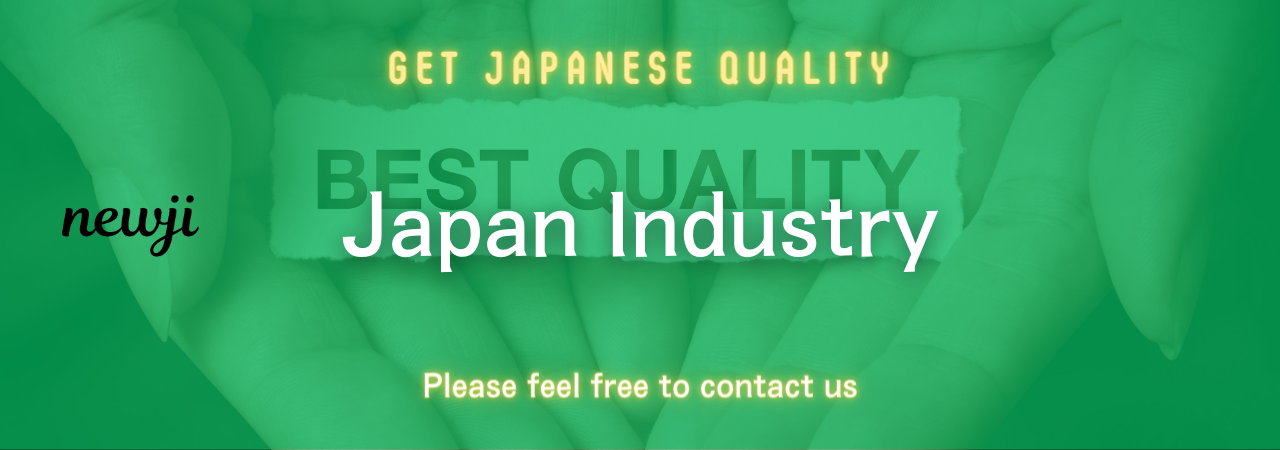
目次
Understanding Impact Loads and Impact Stress
Impact loads and impact stress are crucial concepts in the field of structural engineering and design.
These terms refer to the forces and stresses exerted on a structure when it experiences a sudden impact or collision.
Unlike static loads that remain constant over time, impact loads are dynamic and occur over a very short period, making them more challenging to predict and evaluate.
Understanding these forces is essential for ensuring the safety and integrity of structures, vehicles, and other systems.
What Are Impact Loads?
Impact loads are transient forces that can cause significant stress and deformation within a structure.
These loads are typically characterized by their high-intensity and short-duration nature.
They can originate from various sources, such as collisions, explosions, or falling objects.
For example, when a car crashes into a barrier, the force of the collision is an impact load on both the vehicle and the barrier.
Impact Stress Defined
Impact stress is the stress experienced by a material or structure when subjected to an impact load.
It describes how the structure deforms and absorbs the energy from the impact.
The level of impact stress is influenced by several factors, including the mass and velocity of the impacting object, the material properties of the structure, and the geometry of the impact area.
Measurement and Analysis Methods
Accurate measurement and analysis of impact loads and stresses are crucial for designing structures that can withstand these sudden forces.
Various methods and tools are employed to assess these phenomena.
Experimental Techniques
One common approach to measuring impact loads is through experimental testing.
This can involve using crash test dummies for vehicles or pendulum tests for materials and structures.
Strain gauges and accelerometers are often used to collect data during these tests, providing insights into the magnitude and duration of the impact forces.
Numerical Modeling
Numerical modeling is another vital tool in analyzing impact loads and stresses.
Finite Element Analysis (FEA) is widely used to create digital simulations of impacts.
This method allows engineers to visualize how structures deform under impact loads and identify potential failure points.
By adjusting parameters in the model, engineers can optimize designs to improve performance under impact conditions.
Analytical Methods
Analytical methods involve using mathematical equations and principles to estimate impact loads and stresses.
These methods are typically based on fundamental physics laws, such as conservation of momentum and energy absorption principles.
Analytical calculations provide a preliminary understanding of impact phenomena, which can be validated and refined with experimental and numerical techniques.
Application Points for Strength Design
Designing for impact resistance requires careful consideration of various factors to ensure safety and durability.
Below are key application points for incorporating impact loads and stresses into strength design.
Material Selection
Choosing the right materials is crucial for impact-resistant design.
Materials with high toughness and ductility are preferred as they can absorb and dissipate energy more effectively.
For instance, in automotive design, materials like high-strength steel or advanced composites are commonly used to enhance crashworthiness.
Geometry and Shape Optimization
The geometry and shape of a structure significantly influence how it responds to impact loads.
Engineers often employ optimization techniques to improve the distribution of stress across a structure.
Rounded or streamlined shapes can help reduce the concentration of stress points, thus enhancing the overall impact resistance.
Redundancy and Structural Integrity
Incorporating redundancy into a design ensures that if one part of a structure fails, others can take on the load, maintaining overall integrity.
This concept is particularly important in critical structures such as bridges and aircraft, where failure could lead to catastrophic consequences.
Dynamic Analysis for Design Validation
Dynamic analysis techniques are used to validate the design under simulated impact conditions.
These techniques help engineers assess whether a design can withstand real-world impact scenarios and meet safety standards.
By subjecting prototypes to dynamic testing, engineers can identify and rectify potential weaknesses before deployment.
Conclusion
Understanding and designing for impact loads and stresses are integral to ensuring the safety and reliability of structures and systems.
Through measurement, analysis, and application-focused design strategies, engineers can mitigate the risks associated with impact events.
As technology advances, so do the methodologies for assessing and improving impact resistance, leading to safer, more robust design solutions across various industries.
資料ダウンロード
QCD管理受発注クラウド「newji」は、受発注部門で必要なQCD管理全てを備えた、現場特化型兼クラウド型の今世紀最高の受発注管理システムとなります。
ユーザー登録
受発注業務の効率化だけでなく、システムを導入することで、コスト削減や製品・資材のステータス可視化のほか、属人化していた受発注情報の共有化による内部不正防止や統制にも役立ちます。
NEWJI DX
製造業に特化したデジタルトランスフォーメーション(DX)の実現を目指す請負開発型のコンサルティングサービスです。AI、iPaaS、および先端の技術を駆使して、製造プロセスの効率化、業務効率化、チームワーク強化、コスト削減、品質向上を実現します。このサービスは、製造業の課題を深く理解し、それに対する最適なデジタルソリューションを提供することで、企業が持続的な成長とイノベーションを達成できるようサポートします。
製造業ニュース解説
製造業、主に購買・調達部門にお勤めの方々に向けた情報を配信しております。
新任の方やベテランの方、管理職を対象とした幅広いコンテンツをご用意しております。
お問い合わせ
コストダウンが利益に直結する術だと理解していても、なかなか前に進めることができない状況。そんな時は、newjiのコストダウン自動化機能で大きく利益貢献しよう!
(β版非公開)