- お役立ち記事
- Fundamentals of involute gears and key points of gear design and strength design
月間76,176名の
製造業ご担当者様が閲覧しています*
*2025年3月31日現在のGoogle Analyticsのデータより
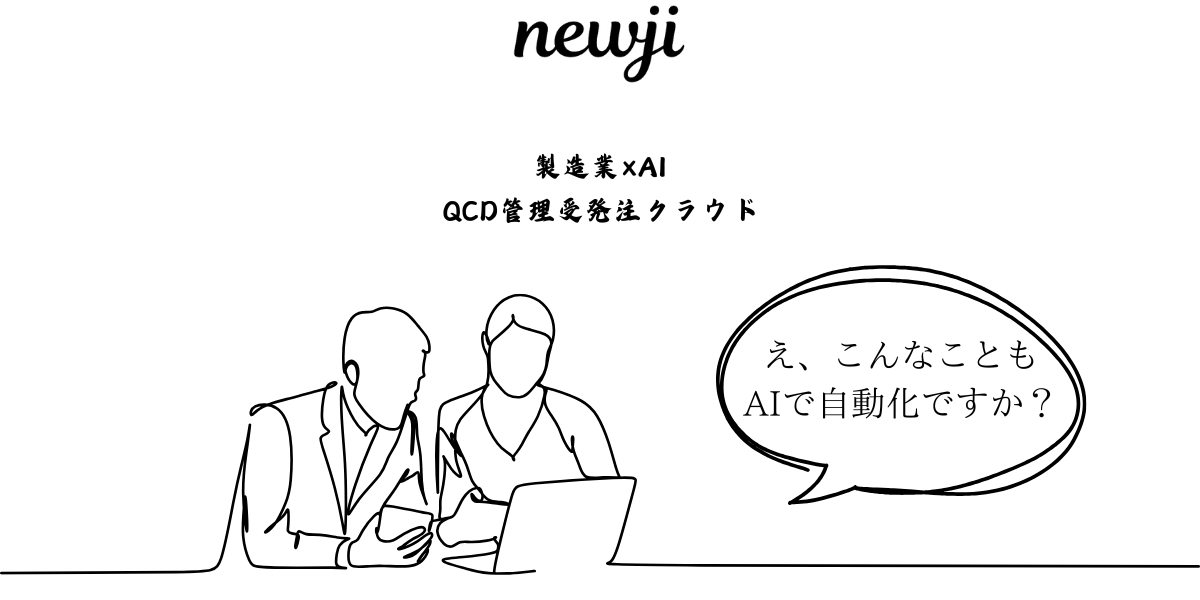
Fundamentals of involute gears and key points of gear design and strength design
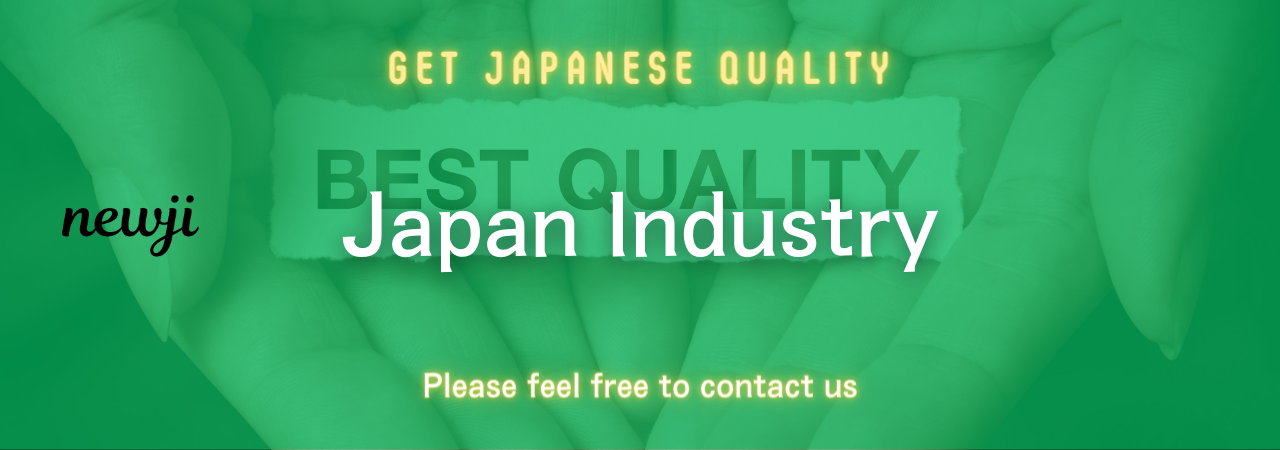
目次
Understanding Involute Gears
Involute gears are among the most common types of gears used in mechanical systems.
Their popularity stems from the involute profile, which ensures a constant velocity ratio during meshing.
This makes them an integral component in numerous applications ranging from automotive transmissions to industrial machinery.
At the core of an involute gear’s design is the involute curve, a geometric shape characterized by its spiral path, which allows it to maintain smooth operation and consistent motion transfer.
The involute shape allows gears to engage with each other smoothly, irrespective of slight misalignments, thus providing superior performance compared to other gear types.
Advantages of Involute Gears
One of the primary advantages of involute gears is their ability to handle loads efficiently.
Their involute shape ensures that contact is maintained at a point known as the line of action, leading to less friction and, consequently, less wear.
This efficiency reduces the need for frequent maintenance and replacements, making them cost-effective over time.
Additionally, involute gears are highly versatile.
They can be used in a wide range of applications and are suitable for high-speed and high-load conditions.
These gears are also known for their robustness, as they are less likely to suffer from tooth breakage due to their design.
Key Points of Gear Design
Designing involute gears requires careful consideration of several factors to ensure optimal performance.
Here are some key points to keep in mind:
Pitch Circle and Modules
The pitch circle plays a critical role in gear design.
It is the circle on which the gear’s teeth are arranged and determines the size and spacing of the gear teeth.
Selecting the appropriate pitch circle is essential for ensuring the gear meshes correctly with its counterpart.
The module is another critical factor in gear design.
It defines the size of the gear teeth and directly impacts the gear’s strength and operational efficiency.
Choosing the right module involves balancing the load requirements with the physical constraints of the mechanism in which the gear will operate.
Pressure Angle
The pressure angle is the angle between the line of action and the tangent to the pitch circle.
It affects the tooth strength and the gear’s load capacity.
A standard pressure angle is typically 20 degrees, but different applications may require adjustments.
Adjusting the pressure angle can help optimize the gear’s performance for specific operational requirements.
Material Selection
The material chosen for gear production affects its durability, performance, and cost.
Common materials include steel, brass, and plastics.
Steel is preferred for high-stress applications due to its strength and wear resistance.
Brass and plastic may be used when weight and cost are more critical factors, though these materials typically offer less durability than steel.
Backlash
Backlash is the slight gap between meshing gear teeth, allowing for thermal expansion and accommodating manufacturing tolerances.
Managing backlash is crucial as it affects the gear’s precision and smoothness of operation.
Insufficient backlash may lead to increased wear and noise, while excessive backlash might reduce the gear’s load-bearing capabilities.
Strength Design of Involute Gears
Strength design ensures that gears can handle their operational loads without failure.
This involves a combination of material selection, tooth geometry optimization, and load analysis.
Load Analysis
Understanding the loads that gears will encounter is paramount.
This includes both static loads, under normal operating conditions, and dynamic loads, which occur during start-up or sudden changes.
Engineers use load analysis to predict gear performance and determine necessary design modifications to prevent failure.
Tooth Geometry Optimization
Tooth shape is crucial for maximizing gear strength and durability.
Gear teeth are optimized using factors like tooth width, profile curvature, and root fillets to distribute load evenly and minimize stress concentrations.
Advanced software tools help designers simulate different geometries and identify optimal configurations.
Finite Element Analysis
Finite Element Analysis (FEA) is a crucial tool in the strength design of gears.
This sophisticated simulation technique helps predict potential failure points and stress distributions within the gear.
By analyzing different scenarios, engineers can tweak gear designs to enhance performance and longevity.
Conclusion
Involute gears continue to be a fundamental element in mechanical systems due to their efficiency and reliability.
By understanding the principles of gear design, including key parameters like pitch circle, module, and material selection, engineers can create gears that perform optimally under various conditions.
With careful strength design through load analysis, tooth geometry optimization, and the use of tools like FEA, involute gears can be tailored to meet specific application requirements, ensuring longevity and efficiency.
Overall, the precise design and engineering of involute gears are essential for the seamless operation of countless mechanical systems globally.
資料ダウンロード
QCD管理受発注クラウド「newji」は、受発注部門で必要なQCD管理全てを備えた、現場特化型兼クラウド型の今世紀最高の受発注管理システムとなります。
ユーザー登録
受発注業務の効率化だけでなく、システムを導入することで、コスト削減や製品・資材のステータス可視化のほか、属人化していた受発注情報の共有化による内部不正防止や統制にも役立ちます。
NEWJI DX
製造業に特化したデジタルトランスフォーメーション(DX)の実現を目指す請負開発型のコンサルティングサービスです。AI、iPaaS、および先端の技術を駆使して、製造プロセスの効率化、業務効率化、チームワーク強化、コスト削減、品質向上を実現します。このサービスは、製造業の課題を深く理解し、それに対する最適なデジタルソリューションを提供することで、企業が持続的な成長とイノベーションを達成できるようサポートします。
製造業ニュース解説
製造業、主に購買・調達部門にお勤めの方々に向けた情報を配信しております。
新任の方やベテランの方、管理職を対象とした幅広いコンテンツをご用意しております。
お問い合わせ
コストダウンが利益に直結する術だと理解していても、なかなか前に進めることができない状況。そんな時は、newjiのコストダウン自動化機能で大きく利益貢献しよう!
(β版非公開)