- お役立ち記事
- Fundamentals of laser processing technology, bonding technology and its applications for EV/multi-materialization
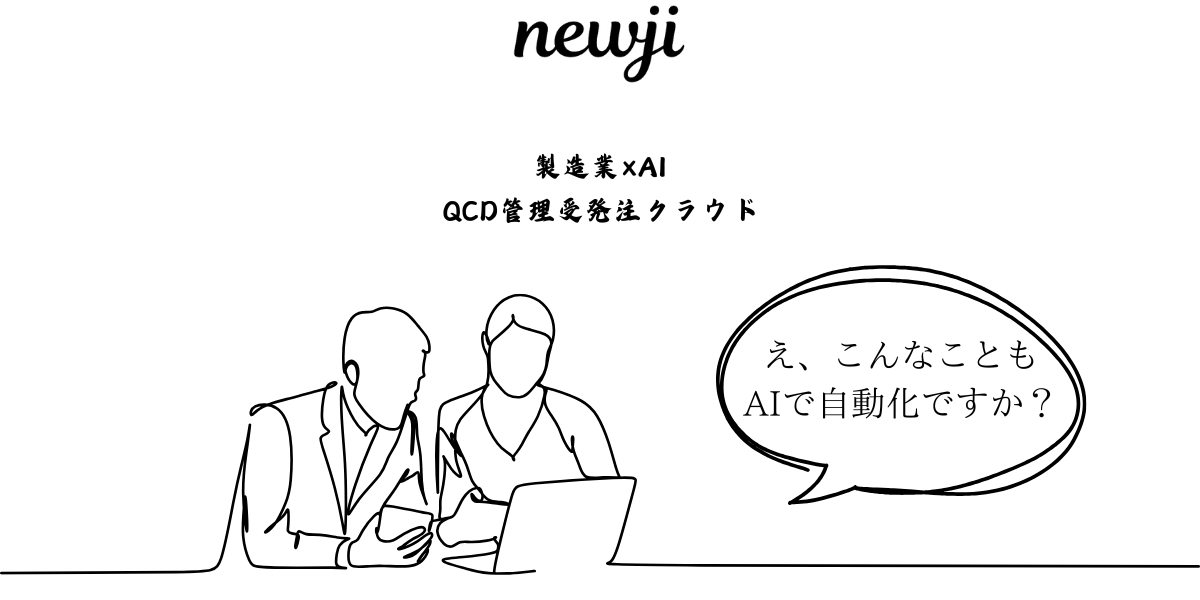
Fundamentals of laser processing technology, bonding technology and its applications for EV/multi-materialization
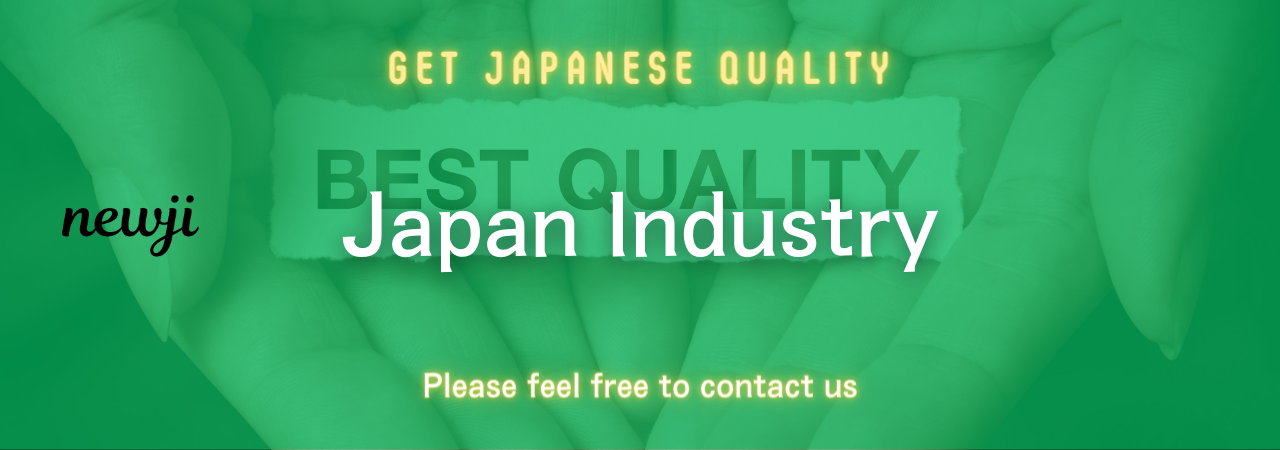
目次
Introduction to Laser Processing Technology
Laser processing technology is a powerful tool used in various industries for its precision and efficiency.
It involves using lasers to cut, weld, mark, or alter the surface of materials.
This technology is crucial for manufacturing processes, particularly when dealing with complex or intricate designs.
Lasers used in processing technology can vary significantly, depending on the task at hand.
They offer unparalleled accuracy, which is why they are highly valued in industries that demand exact specifications, such as electronics, automotive, and aerospace.
With the advent of electric vehicles (EVs) and the push towards multi-materialization, laser processing technology is taking on even more significant roles.
Types of Laser Processing
Laser processing can generally be categorized into three main types: cutting, welding, and marking.
Each type uses different laser properties and techniques to achieve desired results.
Laser Cutting
Laser cutting is a technique that employs focused light beams to cut through materials with high precision.
It is particularly useful for cutting metals, plastics, and textiles.
The process involves the thermal separation of materials, which allows it to achieve clean edges and intricate designs.
This method has become increasingly important in producing components for EVs.
The need for lightweight materials means that manufacturers often use a variety of different materials in one component, and laser cutting is perfect for tailoring materials to exact dimensions.
Laser Welding
Laser welding uses concentrated light to join materials together, typically metals.
The precision of laser welding minimizes heat damage to surrounding areas and allows for strong, clean welds.
In the automotive industry, the application of laser welding technology is expanding, especially with the increasing demand for EVs.
As EVs require lightweight but strong structures, laser welding helps by joining different types of materials efficiently.
This technique is crucial for multi-material assembly, reducing the overall weight while maintaining safety standards.
Laser Marking
Laser marking involves etching or inscribing text, logos, or patterns onto a surface.
It is widely used in various industries for branding, identification, and tracking purposes.
The permanent nature and resistance to wear make laser marking ideal for long-lasting and durable applications.
In the realm of EVs, components require distinct marking to ensure traceability and compliance with industry standards.
Laser marking efficiency and precision excel in marking complex surfaces and small components without altering the material’s properties.
Bonding Technology
Bonding technology is another cornerstone of modern manufacturing, crucial for assembling parts and components across various industries.
It involves different methods like adhesives, mechanical fastening, and welding, each chosen based on specific application needs.
Role of Bonding Technology in Multi-materialization
Multi-materialization refers to the use of more than one material to design and manufacture a single component or product.
This approach is highly beneficial as it allows for optimizing strength, weight, and functionality.
In the context of EVs, multi-material components are essential for improving efficiency and performance.
Bonding technology plays a pivotal role in multi-materialization by allowing different materials to be joined seamlessly.
This is particularly important in automotive manufacturing, where components may involve combinations of metals, composites, and plastics.
Advancements in Bonding Techniques
Recent advancements in bonding techniques have led to more robust and reliable joints.
Adhesive bonding now utilizes advanced formulations that provide higher strength and durability, even in challenging conditions.
In automotive applications, these new adhesives provide flexibility and durability, addressing challenges such as thermal expansion and contraction of different materials.
Mechanical fastening, on the other hand, remains an indispensable method owing to its proven reliability and repairability.
Applications in Electric Vehicles
The combination of laser processing and bonding technology forms a backbone for crafting efficient electric vehicles.
These technologies are essential in integrating different materials like metals and composites in EV manufacturing.
Weight Reduction and Efficiency
Weight reduction is a critical factor for EV efficiency as lighter vehicles require less energy to operate.
Using multiple materials in a single component can reduce weight while maintaining or enhancing strength.
Laser processing ensures accurate shaping of lightweight materials, and bonding technology allows different materials to be united effectively.
Improved Safety Features
Safety is paramount in automobile manufacturing, and EVs are no exception.
The robust construction made possible by advanced bonding methods ensures the integrity and safety of the vehicle, even when using lightweight materials.
Laser processing can create precise and complex safety features that are essential for modern vehicle designs.
Challenges and Future Prospects
Despite the advantages, integrating these technologies also presents challenges, such as ensuring compatibility between materials and maintaining consistent quality in mass production.
Continued research and development are crucial to overcoming these hurdles.
As the demand for EVs rises, innovations in laser processing and bonding technology are likely to continue.
Future advancements may lead to more cost-effective and reliable manufacturing processes, fostering greater adoption of EVs worldwide.
Conclusion
The synergy between laser processing technology and bonding techniques underpins the progression towards efficient and innovative manufacturing strategies, particularly in electric vehicle production.
As industries lean towards lightweight, multi-material components, these technologies will be instrumental in designing and producing the vehicles of the future.
By enhancing precision, promoting durability, and ensuring safety, they will continue to redefine possibilities in the realm of transportation and beyond.
Their ongoing evolution promises exciting opportunities for improvements in efficiency, sustainability, and performance.
資料ダウンロード
QCD調達購買管理クラウド「newji」は、調達購買部門で必要なQCD管理全てを備えた、現場特化型兼クラウド型の今世紀最高の購買管理システムとなります。
ユーザー登録
調達購買業務の効率化だけでなく、システムを導入することで、コスト削減や製品・資材のステータス可視化のほか、属人化していた購買情報の共有化による内部不正防止や統制にも役立ちます。
NEWJI DX
製造業に特化したデジタルトランスフォーメーション(DX)の実現を目指す請負開発型のコンサルティングサービスです。AI、iPaaS、および先端の技術を駆使して、製造プロセスの効率化、業務効率化、チームワーク強化、コスト削減、品質向上を実現します。このサービスは、製造業の課題を深く理解し、それに対する最適なデジタルソリューションを提供することで、企業が持続的な成長とイノベーションを達成できるようサポートします。
オンライン講座
製造業、主に購買・調達部門にお勤めの方々に向けた情報を配信しております。
新任の方やベテランの方、管理職を対象とした幅広いコンテンツをご用意しております。
お問い合わせ
コストダウンが利益に直結する術だと理解していても、なかなか前に進めることができない状況。そんな時は、newjiのコストダウン自動化機能で大きく利益貢献しよう!
(Β版非公開)