- お役立ち記事
- Fundamentals of lubrication technology and effective measures to reduce friction, wear, and surface damage
月間77,185名の
製造業ご担当者様が閲覧しています*
*2025年2月28日現在のGoogle Analyticsのデータより
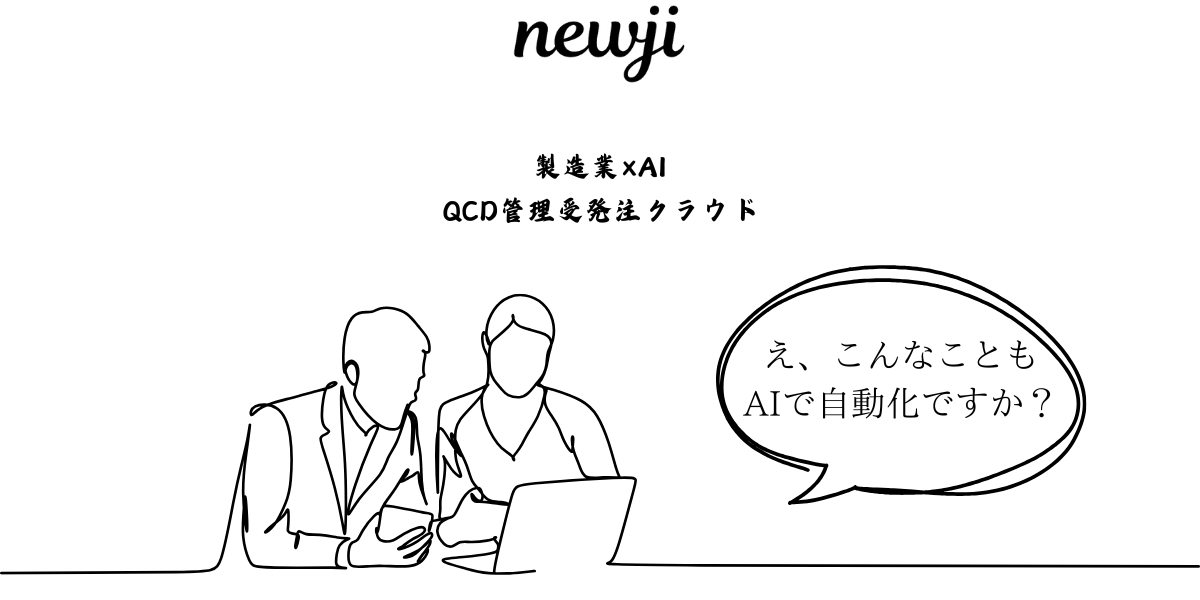
Fundamentals of lubrication technology and effective measures to reduce friction, wear, and surface damage
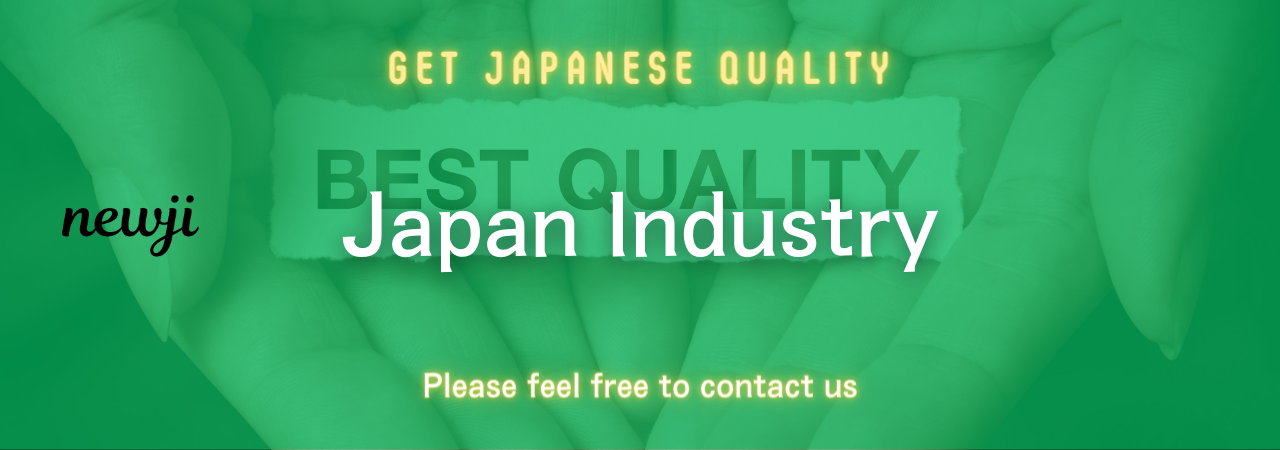
目次
Understanding Lubrication Technology
Lubrication technology is an essential aspect of modern mechanical engineering.
Its primary purpose is to minimize friction between surfaces in motion, which, in turn, helps in reducing wear and surface damage.
The effective use of lubrication can greatly enhance the lifespan and performance of mechanical systems.
To comprehend how lubrication works, it’s important to grasp the basics of friction, wear, and how lubricants function.
Friction and Its Effects
Friction is the resistance encountered when two surfaces slide against each other.
While some level of friction is necessary for certain functions, too much can lead to undesirable outcomes.
Excessive friction causes heat generation, leading to higher energy consumption and, eventually, wear and tear of components.
This wear can shorten the lifespan of mechanical parts, necessitating repairs or replacements that incur additional costs.
Types of Wear and Surface Damage
Wear in mechanical systems can be categorized into several types.
Abrasive wear occurs when rough surfaces or foreign particles grind against each other, removing material from the component surfaces.
Adhesive wear happens when materials transfer between surfaces due to high pressures and temperatures, leading to a breakdown in the contact points.
Fatigue wear arises from repetitive loading and unloading, creating microscopic cracks that expand over time and lead to material failure.
Corrosive wear involves chemical reactions between the surfaces and their environment, degrading the material and causing damage.
Understanding these wear mechanisms is vital to selecting the appropriate lubrication strategies.
Lubricants and Their Role
Lubricants are substances introduced between two moving surfaces to reduce friction and wear.
They can be solid, liquid, or gas-based, with the choice often dependent on the specific application.
The primary functions of lubricants include:
1. Reducing friction by creating a slippery layer between surfaces.
2. Minimizing wear by separating surfaces and preventing direct contact.
3. Transferring heat away from the contact area to prevent overheating.
4. Protecting against corrosion by forming a barrier against environmental exposure.
5. Acting as a seal to keep out contaminants, such as dust and moisture.
Types of Lubricants
Lubricants are generally classified into four main categories: oils, greases, solid lubricants, and gases.
– **Oils**: These are the most common type of lubricants.
They can be further categorized into mineral oils, synthetic oils, and bio-based oils.
Mineral oils are derived from crude oil, synthetic oils are manufactured through chemical processes, and bio-based oils are produced from renewable biological sources.
– **Greases**: These are made by combining oils with a thickening agent, providing a semi-solid consistency.
Greases are useful in applications where the lubricant needs to stay in place for extended periods.
– **Solid Lubricants**: Materials like graphite and molybdenum disulfide are used in situations where liquid lubricants might not be effective, such as extreme temperature or vacuum conditions.
– **Gases**: Although less common, gas lubricants like air or nitrogen can be used for applications requiring low friction and heat removal.
Effective Measures to Reduce Friction and Wear
To minimize friction and wear effectively, selecting the right lubricant and applying it correctly are crucial.
Selecting the Right Lubricant
Choosing the appropriate lubricant depends on the specific application requirements, including the operating environment, load conditions, and temperature range.
The viscosity of the lubricant should also be considered; it must be suitable for the speed and load of the application.
Higher viscosity lubricants are better for heavy loads and slow speeds, while lower viscosity is suited for high-speed applications.
Proper Lubrication Techniques
Applying the right amount of lubricant is critical.
Too little lubricant can lead to increased friction and wear, whereas too much can result in overheating and energy wastage.
Regular monitoring and maintenance are essential to ensure that the lubricant is still effective and that there is no contamination.
Advanced Lubrication Technologies
Recent advancements in lubrication technology have led to the development of smart lubricants and condition monitoring systems.
Smart lubricants are engineered with additives that enhance performance under specific conditions, such as extreme pressure or temperature.
Condition monitoring systems use sensors to track the performance of lubricants in real time, allowing for proactive maintenance and reducing the risk of lubrication-related failures.
Conclusion
Understanding the fundamentals of lubrication technology is essential for optimizing the performance and longevity of mechanical systems.
By selecting the right lubricants and applying them effectively, it’s possible to significantly reduce friction, wear, and surface damage.
With continuous advancements in lubrication technologies, the ability to enhance machinery efficiency and reliability is ever-improving, ultimately leading to cost savings and increased productivity.
資料ダウンロード
QCD管理受発注クラウド「newji」は、受発注部門で必要なQCD管理全てを備えた、現場特化型兼クラウド型の今世紀最高の受発注管理システムとなります。
ユーザー登録
受発注業務の効率化だけでなく、システムを導入することで、コスト削減や製品・資材のステータス可視化のほか、属人化していた受発注情報の共有化による内部不正防止や統制にも役立ちます。
NEWJI DX
製造業に特化したデジタルトランスフォーメーション(DX)の実現を目指す請負開発型のコンサルティングサービスです。AI、iPaaS、および先端の技術を駆使して、製造プロセスの効率化、業務効率化、チームワーク強化、コスト削減、品質向上を実現します。このサービスは、製造業の課題を深く理解し、それに対する最適なデジタルソリューションを提供することで、企業が持続的な成長とイノベーションを達成できるようサポートします。
製造業ニュース解説
製造業、主に購買・調達部門にお勤めの方々に向けた情報を配信しております。
新任の方やベテランの方、管理職を対象とした幅広いコンテンツをご用意しております。
お問い合わせ
コストダウンが利益に直結する術だと理解していても、なかなか前に進めることができない状況。そんな時は、newjiのコストダウン自動化機能で大きく利益貢献しよう!
(β版非公開)