- お役立ち記事
- Fundamentals of machine rigidity design and techniques for improving machining accuracy
月間76,176名の
製造業ご担当者様が閲覧しています*
*2025年3月31日現在のGoogle Analyticsのデータより
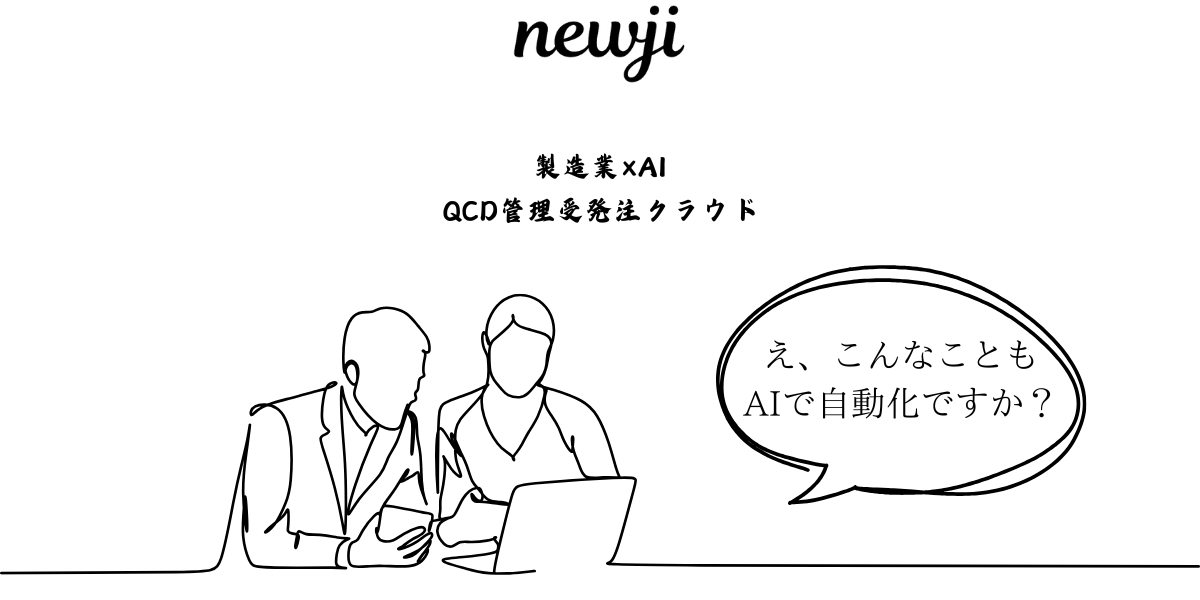
Fundamentals of machine rigidity design and techniques for improving machining accuracy
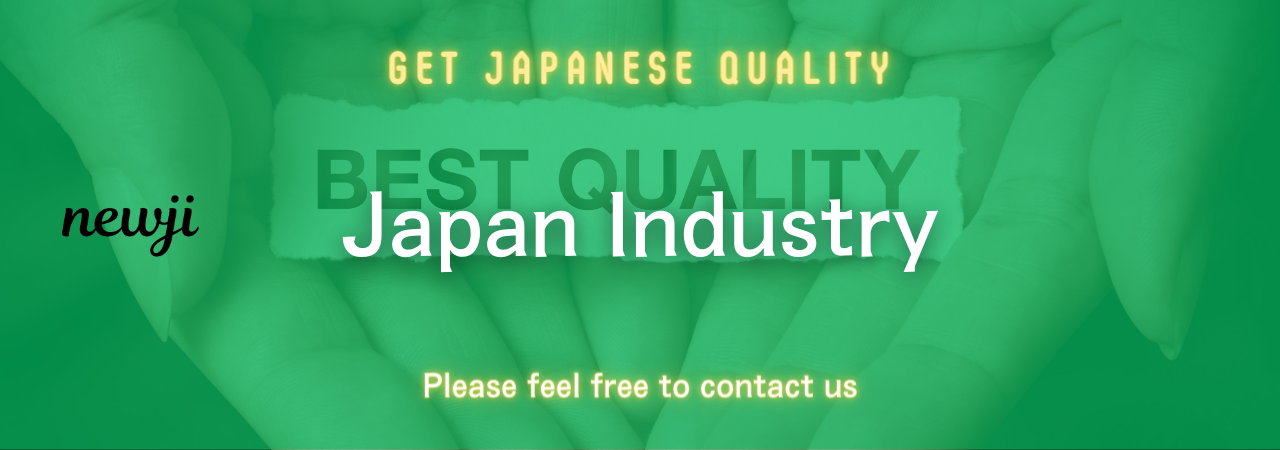
目次
Understanding Machine Rigidity
Machine rigidity refers to the resistance of a machine tool to deformation when subjected to external forces during operation.
To ensure precision, machines must withstand various forces and maintain their structural integrity.
Rigidity is a critical factor in determining the accuracy and quality of the machining process.
It directly influences the machine’s ability to produce parts within specified tolerances and avoid defects.
In machining, every component of the machine tool, including the frame, spindle, and bearings, plays a role in overall rigidity.
The goal is to minimize any deflection or vibrations that can lead to inaccuracies.
Consequently, understanding the principles of machine rigidity is essential for engineers and manufacturers who aim to enhance machining performance.
Components Affecting Rigidity
A machine tool’s rigidity is determined by several factors that work in harmony to ensure overall stability.
Machine Structure
The machine’s structural design is fundamental to its rigidity.
The use of high-quality materials that can withstand stress without bending or deforming is imperative.
Many machine tools are constructed from cast iron or steel, known for their strength and stability.
Additionally, the design should minimize the length of unsupported segments, as shorter spans decrease deflection.
Spindle System
The spindle is a crucial component in machining operations, responsible for holding and rotating the workpiece or cutting tool.
A robust spindle system with precise bearings helps maintain alignment and reduces deflections.
Attention must be paid to the spindle’s material and design, as well as regular maintenance, to ensure a lasting high level of rigidity.
Guiding Systems
Guiding systems provide direction and support to machine components as they move.
Linear guides, often made with hardened steel, offer frictionless movement while maintaining rigidity.
The proper alignment and lubrication of these guides play a significant role in minimizing wear and force transmission.
Mounting and Foundation
A machine’s installation and foundation significantly impact its rigidity.
Machines should be mounted on stable and level surfaces to avoid vibrations.
The foundation should accommodate the weight and forces generated during operation, dissipating vibrations effectively.
Techniques for Improving Machining Accuracy
To achieve high levels of machining accuracy, several techniques and practices can be adopted.
Regular Maintenance
Ensuring machines are regularly maintained is crucial for preserving their performance and rigidity.
Preventive maintenance, including lubrication, aligning components, and replacing worn parts, contributes to maintaining precision.
A well-maintained machine can consistently produce accurate parts, reducing downtime and costs.
Vibration Control
Vibrations can cause significant deviations in machining accuracy.
Using damping materials, balancing rotating elements, and employing vibration isolation systems can mitigate these effects.
Machining strategies, such as consistently monitoring speeds and feeds, further reduce vibration impact.
Tool Selection and Maintenance
Choosing the right tool for the job can dramatically impact machine performance.
Tools should be made from materials that match the requirements of the workpiece and intended operation.
Additionally, regularly inspecting and maintaining tools for sharpness and integrity helps reduce inaccuracies caused by tool wear.
Precision Measurement Systems
Incorporating advanced measurement systems in the machining process ensures higher accuracy levels.
Using laser measurement systems or coordinate measuring machines (CMM) can maintain tight tolerances and quickly identify deviations.
CAD/CAM Integration
Computer-aided design (CAD) and computer-aided manufacturing (CAM) systems allow for precise design and operational control.
Their use in machining helps optimize feed rates, cutting paths, and tool parameters, aligning closely with rigidity requirements.
Advanced Control Systems
Utilizing modern control systems in machine tools can significantly enhance accuracy.
Servo motors, feedback systems, and adaptive control can detect load variations and make real-time adjustments to maintain optimal performance.
Conclusion
A comprehensive understanding of machine rigidity and implementing techniques to enhance machining accuracy is essential in the manufacturing industry.
Focusing on machine structure, maintenance, vibration control, and advanced technologies can lead to improved performance and product quality.
Adopting these practices not only extends the life of the equipment but also ensures consistent, high-quality output essential for competitive advantage.
資料ダウンロード
QCD管理受発注クラウド「newji」は、受発注部門で必要なQCD管理全てを備えた、現場特化型兼クラウド型の今世紀最高の受発注管理システムとなります。
ユーザー登録
受発注業務の効率化だけでなく、システムを導入することで、コスト削減や製品・資材のステータス可視化のほか、属人化していた受発注情報の共有化による内部不正防止や統制にも役立ちます。
NEWJI DX
製造業に特化したデジタルトランスフォーメーション(DX)の実現を目指す請負開発型のコンサルティングサービスです。AI、iPaaS、および先端の技術を駆使して、製造プロセスの効率化、業務効率化、チームワーク強化、コスト削減、品質向上を実現します。このサービスは、製造業の課題を深く理解し、それに対する最適なデジタルソリューションを提供することで、企業が持続的な成長とイノベーションを達成できるようサポートします。
製造業ニュース解説
製造業、主に購買・調達部門にお勤めの方々に向けた情報を配信しております。
新任の方やベテランの方、管理職を対象とした幅広いコンテンツをご用意しております。
お問い合わせ
コストダウンが利益に直結する術だと理解していても、なかなか前に進めることができない状況。そんな時は、newjiのコストダウン自動化機能で大きく利益貢献しよう!
(β版非公開)