- お役立ち記事
- Fundamentals of manipulator control technology and application to robot control using sensors
月間76,176名の
製造業ご担当者様が閲覧しています*
*2025年3月31日現在のGoogle Analyticsのデータより
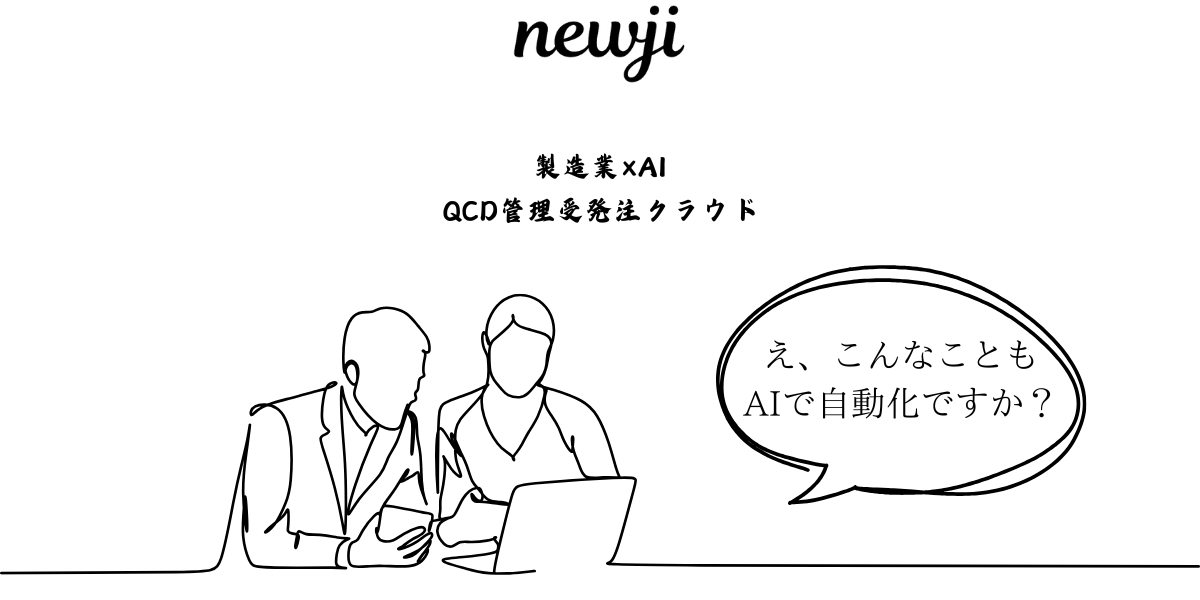
Fundamentals of manipulator control technology and application to robot control using sensors
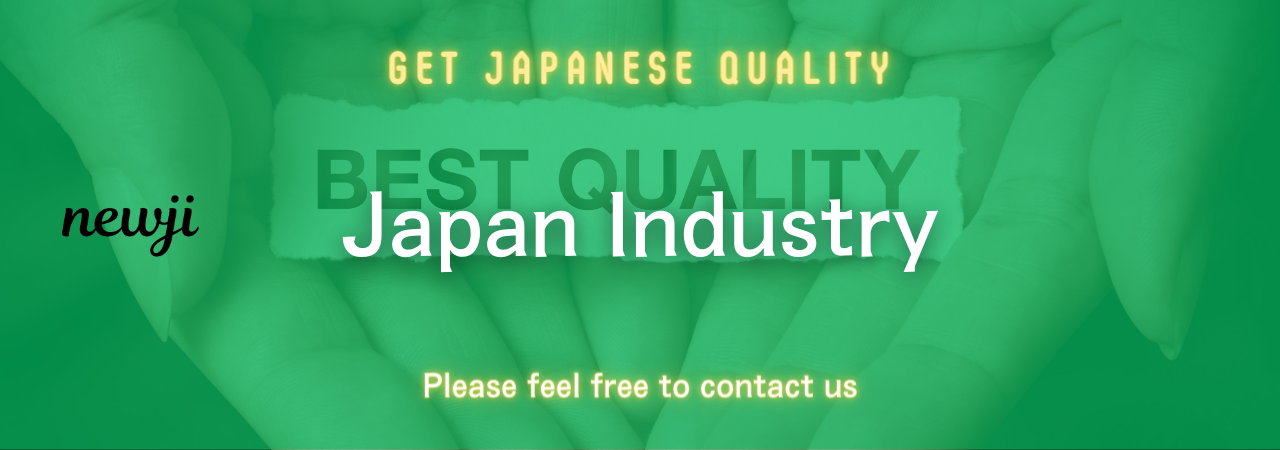
目次
Introduction to Manipulator Control Technology
Manipulator control technology forms the backbone of modern robotics, enabling machines to perform tasks with precision and efficiency.
At its core, this technology involves the control and manipulation of robotic arms or devices that mimic human hand movements.
The objective is to replicate the dexterity and functionality of a human, allowing machines to carry out tasks in diverse environments.
Over the years, advancements in technology have led to significant improvements in manipulator control.
These improvements include the integration of sensors, better algorithms, and enhanced computational power, all contributing to the increased capabilities of robotic manipulators.
The following sections will delve deeper into the components, techniques, and applications of manipulator control technology.
Understanding the Components of Manipulator Systems
A typical manipulator system consists of several key components, each playing a crucial role in its functionality.
These components include actuators, sensors, controllers, and the manipulator’s physical structure.
Actuators
Actuators are responsible for the movement within the manipulator.
They convert electric, hydraulic, or pneumatic inputs into mechanical motion.
The choice of actuators affects the manipulator’s speed, precision, and power.
Sensors
Sensors are used to collect data from the environment and the manipulator itself.
They provide critical feedback to the control system, helping it make informed decisions.
Common sensors include encoders, gyroscopes, and cameras, which capture information about position, orientation, and surroundings.
Controllers
Controllers interpret sensor data and issue commands to the actuators.
They use algorithms to decide the best course of action for the manipulator to achieve its objectives.
Controllers must balance the need for accuracy, speed, and stability in their decision-making processes.
Physical Structure
The physical structure of a manipulator determines its reach, flexibility, and load capacity.
Designs vary greatly depending on the intended application, from simple pick-and-place arms to complex humanoid robots.
Techniques in Manipulator Control
Controlling a manipulator involves a range of techniques to manage its motion and interaction with the environment.
The right combination of these techniques ensures efficient and safe operation.
Inverse Kinematics
Inverse kinematics involves calculating the joint angles required to position the end effector of a manipulator at a desired location.
This technique is fundamental for achieving precise positioning in tasks like assembly or welding.
Motion Planning
Motion planning refers to developing a trajectory or path for the manipulator to follow.
It involves avoiding obstacles and ensuring the path is feasible given the constraints of the system.
Advanced motion planning techniques use algorithms such as Rapidly-exploring Random Trees (RRT) or Probabilistic Roadmaps (PRM).
Feedback Control
Feedback control systems continuously adjust the manipulator’s movements based on sensor inputs.
This real-time adjustment helps correct any deviations from the desired path and compensates for external perturbations or inaccuracies.
Force Control
In tasks requiring interaction with objects, such as gripping or inserting, force control becomes crucial.
Force control ensures that the manipulator applies the right amount of pressure, preventing damage to the object or the manipulator.
Applications of Manipulator Control Using Sensors
The integration of sensors in manipulator systems has expanded their potential applications across various industries.
Manufacturing and Automation
In manufacturing, manipulators are used for tasks such as welding, assembly, and painting.
Sensors enhance precision and adaptability, allowing robots to work safely alongside humans and adapt to changes in the production line.
Healthcare and Surgery
Robotic manipulators with high precision are used in minimally invasive surgeries.
Sensors provide real-time data, enabling surgeons to control the robotic arms with high accuracy during delicate procedures.
Space Exploration
In space missions, manipulators are employed to repair satellites, collect samples, and carry out scientific experiments.
Sensors help with precise navigation and operation in the challenging environment of space.
Defense and Rescue Operations
In defense, manipulators are used in bomb disposal and reconnaissance missions.
The integration of sensors aids in remote operation and enhances the robot’s situational awareness in hazardous environments.
The Future of Manipulator Control Technology
As technology continues to evolve, manipulator control systems are expected to become even more advanced.
Future developments may include further integration of artificial intelligence, making robots smarter and more autonomous.
This could lead to the creation of machines that can learn and adapt to new tasks without explicit programming.
Moreover, advancements in sensor technology will likely lead to improved perception capabilities, enhancing the robot’s ability to interact with complex environments.
This will broaden the scope of applications, potentially revolutionizing industries such as agriculture, mining, and more.
The ongoing research and development in manipulator control technology promise a future where robots seamlessly interact with the world, performing tasks that were once considered beyond the reach of machines.
Conclusion
Manipulator control technology is a critical enabler in the field of robotics, driving innovations across multiple sectors.
Understanding its components, techniques, and applications help us appreciate the complexity and potential of these systems.
As sensors continue to play a pivotal role, the future of manipulator control looks promising, with endless possibilities for enhancing both industrial processes and everyday life.
Whether it’s in factories, hospitals, outer space, or battlefields, robotic manipulators equipped with advanced control systems are set to redefine the way we approach complex challenges.
資料ダウンロード
QCD管理受発注クラウド「newji」は、受発注部門で必要なQCD管理全てを備えた、現場特化型兼クラウド型の今世紀最高の受発注管理システムとなります。
ユーザー登録
受発注業務の効率化だけでなく、システムを導入することで、コスト削減や製品・資材のステータス可視化のほか、属人化していた受発注情報の共有化による内部不正防止や統制にも役立ちます。
NEWJI DX
製造業に特化したデジタルトランスフォーメーション(DX)の実現を目指す請負開発型のコンサルティングサービスです。AI、iPaaS、および先端の技術を駆使して、製造プロセスの効率化、業務効率化、チームワーク強化、コスト削減、品質向上を実現します。このサービスは、製造業の課題を深く理解し、それに対する最適なデジタルソリューションを提供することで、企業が持続的な成長とイノベーションを達成できるようサポートします。
製造業ニュース解説
製造業、主に購買・調達部門にお勤めの方々に向けた情報を配信しております。
新任の方やベテランの方、管理職を対象とした幅広いコンテンツをご用意しております。
お問い合わせ
コストダウンが利益に直結する術だと理解していても、なかなか前に進めることができない状況。そんな時は、newjiのコストダウン自動化機能で大きく利益貢献しよう!
(β版非公開)