- お役立ち記事
- Fundamentals of material mechanics and analysis points in the finite element method
月間77,185名の
製造業ご担当者様が閲覧しています*
*2025年2月28日現在のGoogle Analyticsのデータより
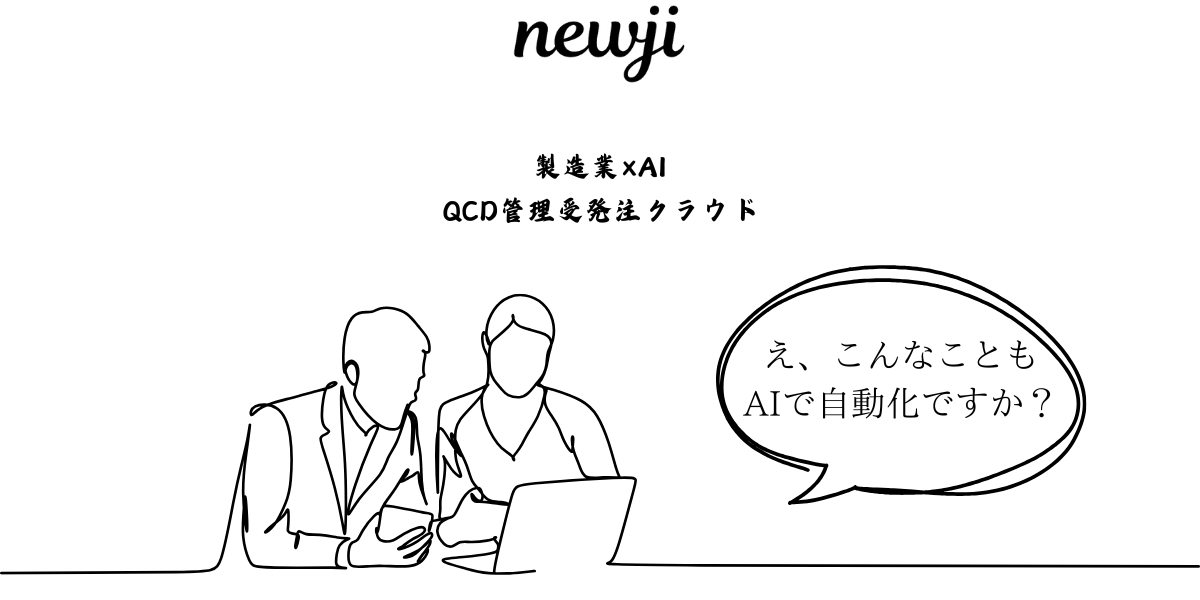
Fundamentals of material mechanics and analysis points in the finite element method
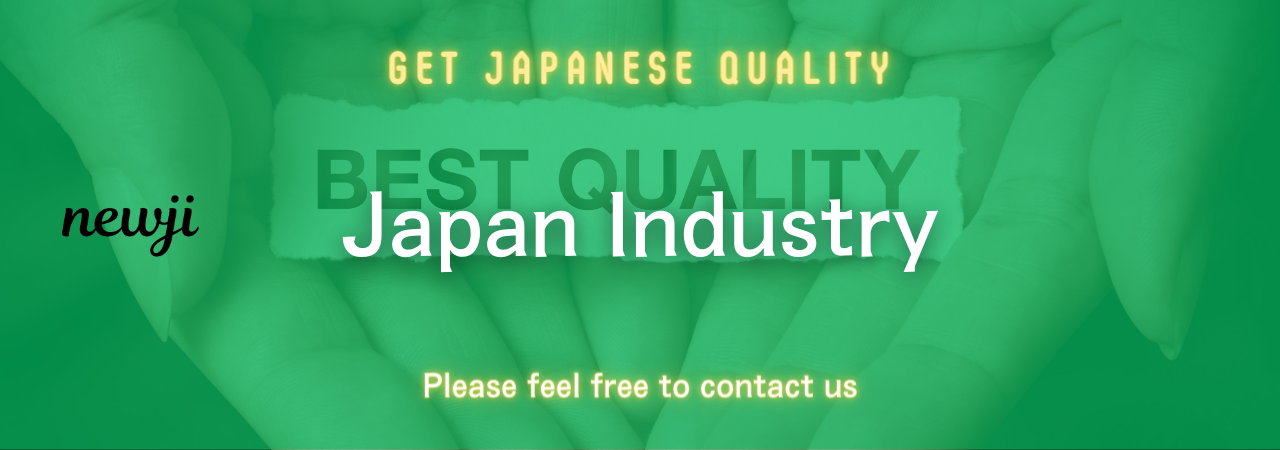
目次
Understanding Material Mechanics
Material mechanics is a fundamental part of engineering and physics that involves studying the behavior of solid objects under various forces and conditions.
It helps in analyzing how materials deform, break, or change shape when subjected to different kinds of loads such as tension, compression, torsion, and bending.
Understanding these mechanics is crucial for designing structures, machinery, and even everyday items safely and effectively.
At its core, material mechanics revolves around understanding the properties of materials.
These include strength, elasticity, plasticity, ductility, hardness, and toughness.
Each property affects how a material behaves under specific conditions and what role it can play in structural applications.
For example, elasticity refers to a material’s ability to return to its original shape after deformation, while plasticity involves permanent deformation.
A key component of material mechanics is stress and strain analysis.
Stress is the internal force per area within a material resulting from external forces.
Strain, on the other hand, is the deformation or change in size or shape due to stress.
Analyzing stress and strain helps predict potential structural failures and guides improvements in design and manufacturing processes.
The Basics of Finite Element Method (FEM)
The Finite Element Method (FEM) is a powerful computational tool used to simulate and analyze the physical behavior of complex structures and systems.
It’s extensively employed in engineering for solving structural, thermal, electromagnetic, and fluid dynamics problems.
FEM breaks down a large, complex problem into smaller, simpler parts known as finite elements.
This method begins by discretizing or dividing a structure into a finite number of elements.
Each element is connected at points called nodes.
These elements are assumed to be simpler geometries where the unknown quantities are calculated.
The elements are then assembled into a larger system to form a global matrix equation that models the entire problem.
One of the biggest advantages of FEM is its flexibility.
It can handle complex geometries and boundary conditions with great precision.
The method is capable of modeling irregular shapes, and it provides detailed insight into how different materials will react under various forces.
Furthermore, FEM is an iterative method, allowing for gradual refinement of the mesh or the collection of elements over multiple simulations.
This iterative refinement leads to more accurate approximations of the actual problem.
Application of Material Mechanics in FEM
Material mechanics and the Finite Element Method (FEM) work intricately together in various applications.
When employing FEM, understanding the material properties and behavior under different loads becomes indispensable.
Mechanical properties such as elasticity, plastic limit, and yield strength must be input into the model to simulate realistic scenarios.
FEM uses these material properties to calculate how structures will respond.
For instance, engineers can simulate how a bridge will hold up under heavy traffic or how a building will react to an earthquake.
These analyses are crucial for optimizing material designs, reducing costs, and ensuring safety.
Furthermore, FEM can help identify stress concentrations and potential points of failure in a material.
Engineers can use this information to redesign parts and assemblies to improve performance and extend the lifespan of products.
By accurately predicting responses, FEM saves both time and resources in the development process.
Key Points in Analyzing Material Mechanics with FEM
Proper Mesh Design
Creating an appropriate mesh is crucial for the success of any FEM analysis.
The mesh should be fine enough to capture all necessary details yet coarse enough to avoid excessive computation time.
Areas with high stress concentrations often require a denser mesh, while regions experiencing uniform stress may suffice with a coarser one.
Material Property Accuracy
The accuracy of FEM predictions heavily relies on correctly defining the material’s mechanical properties.
Inaccurate or incomplete data on material properties can lead to incorrect analysis results.
Hence, obtaining precise data through experiments or reliable literature is essential.
Boundary Conditions
Properly applying boundary conditions is paramount in FEM analysis.
These include constraints like fixed supports or applied forces.
Incorrect boundary conditions can drastically affect the results, leading to erroneous conclusions.
Validation and Verification
Validating and verifying the results is the final step in ensuring the reliability of an FEM analysis.
Comparing simulation outcomes with physical experiments can provide confidence in the model’s accuracy.
Discrepancies often indicate areas where the model requires refinement or improvement.
The Importance of Material Mechanics and FEM in Engineering
Combining material mechanics with the Finite Element Method extends the capabilities of engineers to solve complex real-world problems efficiently.
It allows for advances in design, improves product reliability, and reduces unnecessary material use, leading to more sustainable engineering practices.
Both material mechanics and FEM play an essential role in various industries, including aerospace, automotive, civil engineering, and biomedical fields.
Through proper understanding and application of these principles, engineers can anticipate and overcome potential challenges in their designs.
This ensures that the infrastructure, machinery, and everyday products are safe, reliable, and built to last.
資料ダウンロード
QCD管理受発注クラウド「newji」は、受発注部門で必要なQCD管理全てを備えた、現場特化型兼クラウド型の今世紀最高の受発注管理システムとなります。
ユーザー登録
受発注業務の効率化だけでなく、システムを導入することで、コスト削減や製品・資材のステータス可視化のほか、属人化していた受発注情報の共有化による内部不正防止や統制にも役立ちます。
NEWJI DX
製造業に特化したデジタルトランスフォーメーション(DX)の実現を目指す請負開発型のコンサルティングサービスです。AI、iPaaS、および先端の技術を駆使して、製造プロセスの効率化、業務効率化、チームワーク強化、コスト削減、品質向上を実現します。このサービスは、製造業の課題を深く理解し、それに対する最適なデジタルソリューションを提供することで、企業が持続的な成長とイノベーションを達成できるようサポートします。
製造業ニュース解説
製造業、主に購買・調達部門にお勤めの方々に向けた情報を配信しております。
新任の方やベテランの方、管理職を対象とした幅広いコンテンツをご用意しております。
お問い合わせ
コストダウンが利益に直結する術だと理解していても、なかなか前に進めることができない状況。そんな時は、newjiのコストダウン自動化機能で大きく利益貢献しよう!
(β版非公開)