- お役立ち記事
- Fundamentals of material mechanics and application points for strength design
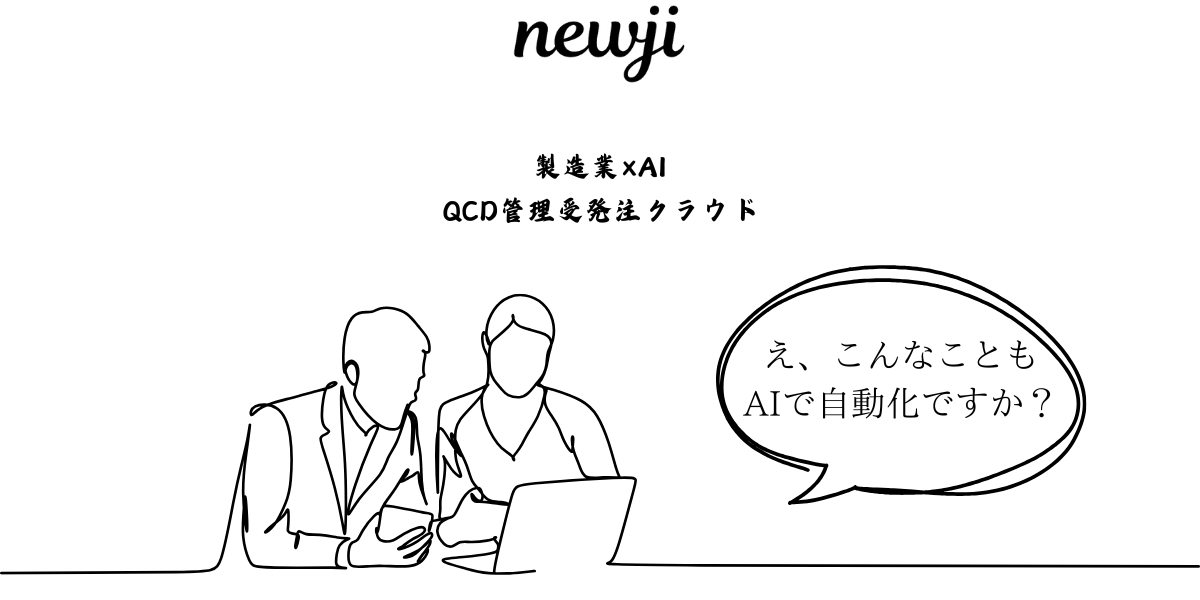
Fundamentals of material mechanics and application points for strength design
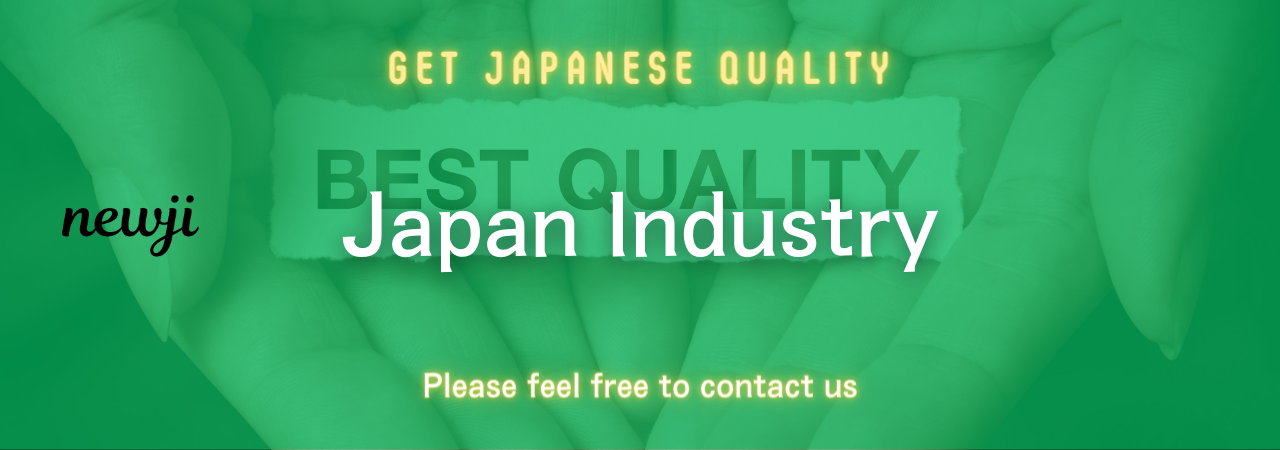
目次
Understanding Material Mechanics
Material mechanics is a field of study which focuses on the behavior of solid materials under various forces and conditions.
Knowing how materials respond to forces and stress is crucial for designing safe and efficient structures and machines.
Engineers use principles from material mechanics to analyze and plan constructions, ensuring they can withstand anticipated loads.
Key Concepts in Material Mechanics
Before diving into applications, it’s important to understand some fundamental concepts in material mechanics.
**Stress and Strain:**
Stress refers to the force applied to a material, typically measured in units like Pascals (Pa).
Strain, on the other hand, measures how much a material deforms in response to stress.
Understanding the relationship between stress and strain is crucial for predicting how materials will behave under different conditions.
**Elasticity and Plasticity:**
Elasticity is the ability of a material to return to its original shape after being deformed.
Plasticity occurs when a material permanently changes shape after the stress exceeds a certain limit.
Materials such as rubber display high elasticity, while metals might show plastic behavior after exceeding their yield strength.
**Young’s Modulus:**
Also known as the modulus of elasticity, Young’s Modulus is a measure of a material’s stiffness.
It represents the ratio of stress to strain in the elastic region of the material’s stress-strain curve.
A high Young’s Modulus indicates a stiff material, while a low value suggests a more flexible material.
**Shear and Torsion:**
Shear stress occurs when forces are applied parallel to the surface of a material, while torsion refers to twisting forces.
Both are critical in the analysis of mechanical structures, as improper management can lead to failures such as cracks or complete structural collapse.
Applications of Material Mechanics
With a grasp of these concepts, engineers can apply material mechanics principles in various fields.
Structural Design
In structural engineering, material mechanics play a vital role in designing buildings, bridges, and other constructions.
Engineers analyze different forces that act on structures, such as gravity, wind, and seismic activities, to ensure stability.
By predicting how materials will respond to these forces, engineers can create designs that avoid failure and prolong the structure’s lifespan.
Automotive and Aerospace Industries
In the automotive industry, understanding the mechanics of materials helps in designing safer and more fuel-efficient vehicles.
Engineers carefully choose materials that can withstand impacts while being lightweight to improve fuel efficiency.
Similarly, in aerospace, material mechanics are critical to ensure that airplanes and spacecraft can handle extreme conditions such as high velocity, atmospheric pressure changes, and temperature fluctuations.
Biomedical Applications
Material mechanics is also essential in the biomedical field, particularly in designing implants and prosthetics.
Engineers create biomaterials that mimic natural body tissues, which must withstand physiological forces while remaining biocompatible.
This ensures that implants, such as artificial joints, function effectively and safely within the human body.
Strength Design Considerations
Strength design aims to ensure that structures and components can safely support anticipated loads without failure.
Several factors influence strength design, some of which are outlined below.
Material Selection
Choosing the right material is paramount to strength design.
Materials must be selected based on their mechanical properties, cost, availability, and environmental impact.
For instance, steel is commonly used in construction due to its high strength and availability, whereas titanium might be selected for aerospace applications due to its strength and lightweight properties.
Load Analysis
Understanding the types of loads a structure will experience is crucial.
Loads can be static, like the weight of a building, or dynamic, such as wind or moving vehicles.
Engineers must analyze these loads to design structures that can absorb and distribute them effectively without compromising integrity.
Safety Factors
Safety factors are multipliers applied to account for uncertainties in load assumptions, material properties, and construction methods.
By incorporating safety factors, designers can provide an additional margin of safety to account for unexpected conditions or errors.
Environmental Conditions
The environment in which a material will be used also plays a significant role in strength design.
Factors like temperature, humidity, and exposure to corrosive elements can affect a material’s performance.
Materials must be selected and designed to endure these conditions over their intended lifespan.
Advanced Techniques in Material Mechanics
Advancements in technology continue to influence the field of material mechanics, providing engineers with more tools for designing strong and resilient structures.
Finite Element Analysis (FEA)
FEA is a computational tool that allows engineers to simulate and analyze the behavior of materials and structures under various conditions.
By breaking down complex structures into smaller elements, designers can predict stress distributions, identify weak points, and optimize designs before physical prototypes are made.
Artificial Intelligence and Machine Learning
These technologies are increasingly being used to improve material mechanics processes.
Machine learning algorithms can analyze large datasets to find patterns and correlations, potentially leading to innovations in material design and improved predictive models for stress and strain analysis.
Conclusion
Understanding the fundamentals of material mechanics is essential for engineers across various industries.
The principles of stress, strain, elasticity, and plasticity, among others, help in designing structures that can handle intended loads and environmental conditions.
Through careful material selection and advanced analytical techniques, engineers can ensure the safety and efficiency of their designs.
As technology advances, the application and understanding of material mechanics continue to evolve, paving the way for more innovative and effective engineering solutions.
資料ダウンロード
QCD調達購買管理クラウド「newji」は、調達購買部門で必要なQCD管理全てを備えた、現場特化型兼クラウド型の今世紀最高の購買管理システムとなります。
ユーザー登録
調達購買業務の効率化だけでなく、システムを導入することで、コスト削減や製品・資材のステータス可視化のほか、属人化していた購買情報の共有化による内部不正防止や統制にも役立ちます。
NEWJI DX
製造業に特化したデジタルトランスフォーメーション(DX)の実現を目指す請負開発型のコンサルティングサービスです。AI、iPaaS、および先端の技術を駆使して、製造プロセスの効率化、業務効率化、チームワーク強化、コスト削減、品質向上を実現します。このサービスは、製造業の課題を深く理解し、それに対する最適なデジタルソリューションを提供することで、企業が持続的な成長とイノベーションを達成できるようサポートします。
オンライン講座
製造業、主に購買・調達部門にお勤めの方々に向けた情報を配信しております。
新任の方やベテランの方、管理職を対象とした幅広いコンテンツをご用意しております。
お問い合わせ
コストダウンが利益に直結する術だと理解していても、なかなか前に進めることができない状況。そんな時は、newjiのコストダウン自動化機能で大きく利益貢献しよう!
(Β版非公開)