- お役立ち記事
- Fundamentals of material mechanics and application to fatigue fracture prevention measures and strength design
Fundamentals of material mechanics and application to fatigue fracture prevention measures and strength design
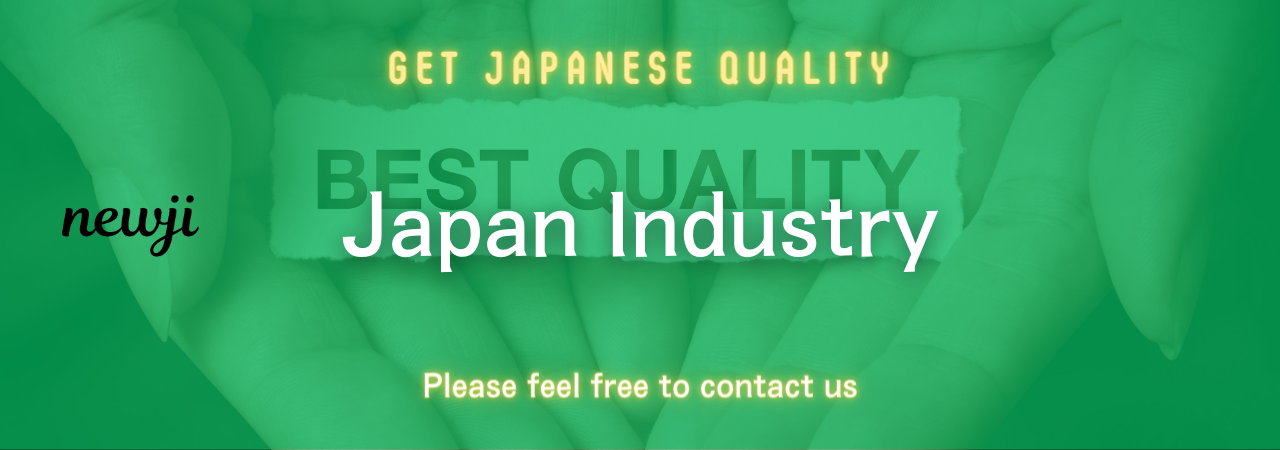
Material mechanics is an essential field of study within engineering and physics, focused on understanding how materials behave under various forces and conditions.
This knowledge is crucial in designing structures and components that can withstand stress, pressure, and the test of time.
By exploring material mechanics, engineers can work to prevent fatigue fractures and design structures with sufficient strength.
In this article, we will explore the fundamentals of material mechanics and the application of these principles to fatigue fracture prevention and strength design.
目次
Understanding Material Mechanics
Material mechanics deals with the internal forces present within solid bodies and how these forces affect the physical structure.
Central to this are concepts such as stress, strain, elasticity, plasticity, and the stress-strain curve.
Stress and Strain
Stress is the force applied to a material divided by the area over which the force is distributed.
It is measured in units called Pascals (Pa).
Strain, on the other hand, is the deformation experienced by the material due to the applied stress.
Elasticity and Plasticity
Elasticity refers to a material’s ability to return to its original shape after the removal of applied stress.
Materials with a high degree of elasticity, like rubber, can endure considerable deformation and still return to their original shape.
Plasticity indicates a permanent deformation after the applied stress has surpassed a certain limit.
The Stress-Strain Curve
The stress-strain curve is a graphical representation of a material’s response to stress.
This curve helps engineers understand the point at which a material will experience permanent deformation.
There are key points on this curve, such as the proportional limit, yield point, and ultimate tensile strength, that determine how a material will behave under different forces.
Fatigue and Fracture Mechanics
Fatigue refers to the progressive and localized damage that materials can undergo when subjected to cyclic loading.
It is a common issue, especially in structural components that experience repeated stress over time, such as bridges, aircraft, and engine parts.
What is Fatigue Fracture?
A fatigue fracture occurs when there is a failure in a material due to repeated or fluctuating stress levels.
Despite the stress being below the material’s ultimate tensile strength, the continuous exposure can lead to cracks and eventual failure.
Mechanism of Fatigue Fracture
The fatigue fracture process is divided into three stages:
1. Crack Initiation: A small crack forms on the surface due to repeated stress cycles.
2. Crack Propagation: The crack gradually spreads as more stress cycles are experienced.
3. Final Fracture: The remaining cross-section becomes too weak to carry the stress, leading to sudden fracture.
Preventing Fatigue Fracture
To mitigate the risk of fatigue fractures, engineers often adopt several strategies:
Design Optimization
By optimizing designs to minimize stress concentrators such as sharp corners, engineers can reduce initial crack formations.
The use of smooth transitions and rounded edges can distribute stress more evenly.
Material Selection
Choosing materials with high fatigue resistance is crucial in applications where cyclic loading is expected.
Alloys with good fatigue properties and composites are often preferred in critical components.
Surface Treatments
Surface treatments like polishing, shot peening, or coating can improve fatigue resistance by creating a compressive layer on the surface.
These treatments hinder initial crack formation.
Strength Design Considerations
Strength design is pivotal in ensuring that structures and components are safe and functional throughout their intended lifespan.
Understanding Load Types
Engineers must determine the types of loads a structure will face, such as static loads, dynamic loads, and environmental impacts like temperature and corrosion.
By understanding these loads, engineers can design structures that withstand all anticipated forces.
Safety Factors
A safety factor, or factor of safety, is introduced to account for uncertainties in material properties, load estimations, and potential flaws in the construction process.
This factor ensures a conservative design, providing the structure with an additional strength buffer.
Compliance with Standards
Designs must comply with relevant industry standards and regulations to ensure safety and reliability.
Adhering to these guidelines is essential for the certification and approval of engineering projects.
In summary, the field of material mechanics provides invaluable insights into how materials behave under various forces and conditions.
By understanding these fundamentals, engineers can create designs that are not only strong but also resilient to fatigue and fracture failure.
By optimizing design, selecting the right materials, considering load types, and applying safety factors, we can ensure that structures and components are built to last—resisting wear and tear over time while maintaining their integrity and functionality.
資料ダウンロード
QCD調達購買管理クラウド「newji」は、調達購買部門で必要なQCD管理全てを備えた、現場特化型兼クラウド型の今世紀最高の購買管理システムとなります。
ユーザー登録
調達購買業務の効率化だけでなく、システムを導入することで、コスト削減や製品・資材のステータス可視化のほか、属人化していた購買情報の共有化による内部不正防止や統制にも役立ちます。
NEWJI DX
製造業に特化したデジタルトランスフォーメーション(DX)の実現を目指す請負開発型のコンサルティングサービスです。AI、iPaaS、および先端の技術を駆使して、製造プロセスの効率化、業務効率化、チームワーク強化、コスト削減、品質向上を実現します。このサービスは、製造業の課題を深く理解し、それに対する最適なデジタルソリューションを提供することで、企業が持続的な成長とイノベーションを達成できるようサポートします。
オンライン講座
製造業、主に購買・調達部門にお勤めの方々に向けた情報を配信しております。
新任の方やベテランの方、管理職を対象とした幅広いコンテンツをご用意しております。
お問い合わせ
コストダウンが利益に直結する術だと理解していても、なかなか前に進めることができない状況。そんな時は、newjiのコストダウン自動化機能で大きく利益貢献しよう!
(Β版非公開)