- お役立ち記事
- Fundamentals of material mechanics and application to fatigue strength design
月間77,185名の
製造業ご担当者様が閲覧しています*
*2025年2月28日現在のGoogle Analyticsのデータより
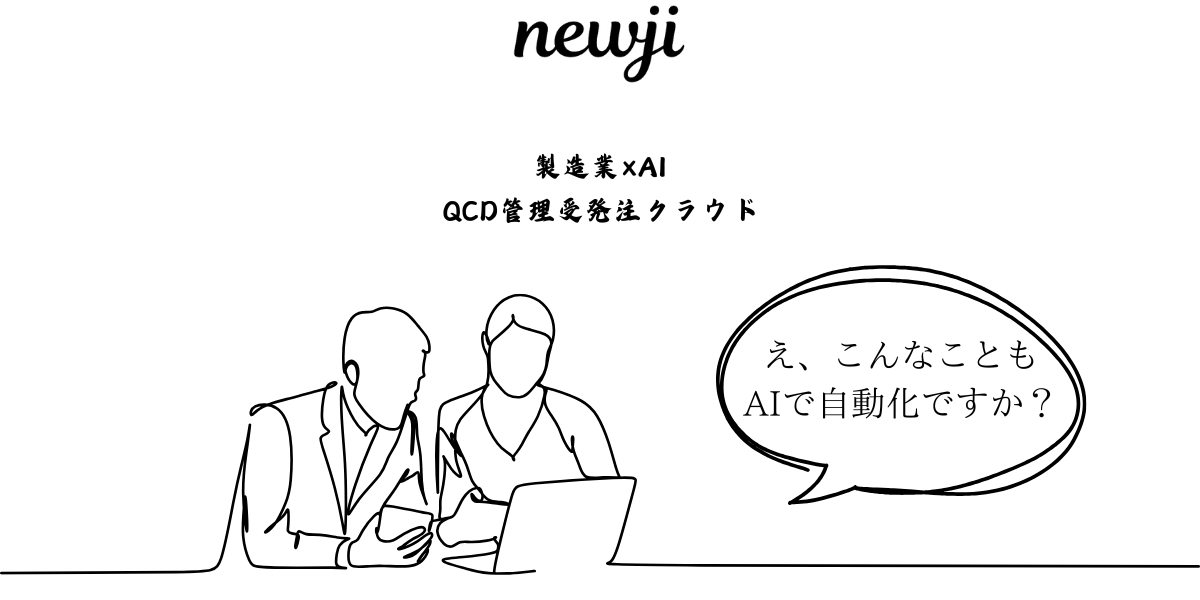
Fundamentals of material mechanics and application to fatigue strength design
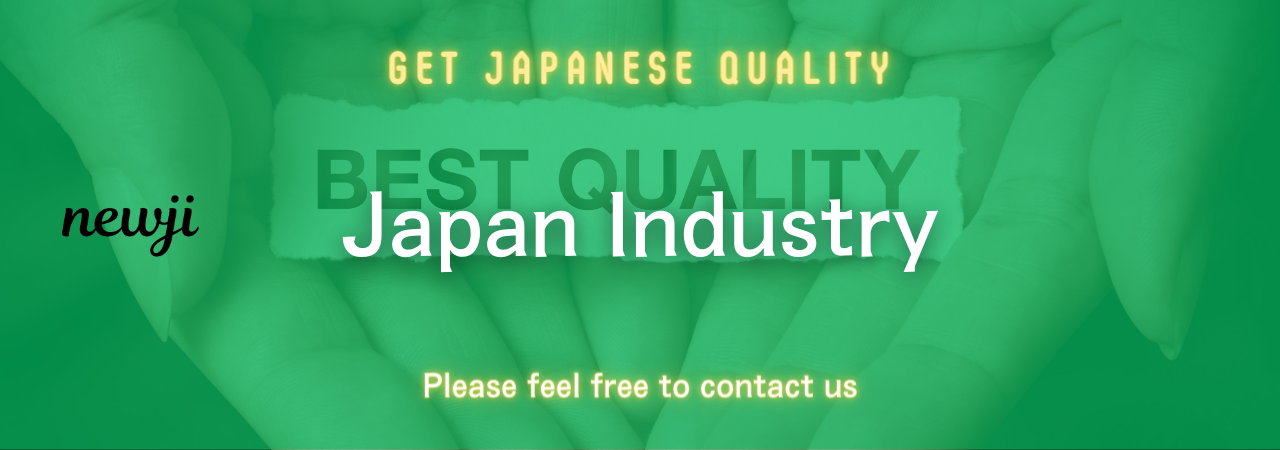
目次
Introduction to Material Mechanics
Material mechanics is a fundamental area of engineering that focuses on understanding how materials behave under various forces and conditions.
It is essential for engineers who design, analyze, and ensure the structural integrity of various products, from simple tools to complex machines and structures.
By grasping the principles of material mechanics, engineers can predict how materials will react under different loads, helping them design products that are both safe and efficient.
Basic Concepts in Material Mechanics
Stress and Strain
At the core of material mechanics are the concepts of stress and strain.
Stress is the internal force per unit area within a material that arises due to externally applied forces.
Strain, on the other hand, is the deformation or displacement a material experiences as a result of this stress.
There are different types of stress, such as tensile, compressive, and shear.
Tensile stress occurs when a material is stretched, compressive stress when it is compressed, and shear stress when it is subjected to opposing forces.
Elasticity and Plasticity
Materials exhibit either elastic or plastic behavior when they are subjected to stress.
Elastic materials return to their original shape when the applied stress is removed, while plastic materials retain some degree of deformation.
The elastic limit of a material is the maximum stress it can withstand while still being able to return to its original shape.
Beyond this limit, the material enters the plastic region, where permanent deformation occurs.
Young’s Modulus
Young’s Modulus is a crucial parameter in material mechanics that measures a material’s stiffness.
It is the ratio of tensile stress to tensile strain in the elastic region of a material’s stress-strain curve.
Materials with a high Young’s Modulus are stiffer and less prone to deformation under load.
Poisson’s Ratio
When a material is compressed or stretched, it tends to expand or contract in the perpendicular direction.
Poisson’s Ratio quantifies this phenomenon.
It is the ratio of transverse strain to axial strain.
Certain materials such as rubber have a high Poisson’s Ratio, meaning they undergo significant lateral strain when stretched.
Fatigue Strength Design
Understanding Fatigue
Fatigue is a progressive and localized structural damage that occurs when a material is subjected to cyclic loading.
Even if the applied stress is below the ultimate tensile strength of the material, repeated loading can lead to fatigue failure.
Fatigue is a crucial consideration in the design of components that will undergo repeated use over their lifetime.
S-N Curves
The S-N curve is an essential tool in fatigue strength design.
It represents the relationship between the stress amplitude and the number of cycles to failure.
By analyzing the S-N curve, engineers can predict the lifespan of a material subjected to specific cyclic loading conditions.
Factors Influencing Fatigue Strength
Several factors can affect the fatigue strength of a material.
Surface finish is one such factor, as rough surfaces can serve as initiation sites for cracks.
Notches and sharp corners also concentrate stress and can lead to premature fatigue failure.
In addition, the presence of corrosive environments can significantly decrease the fatigue strength of materials.
This is known as corrosion fatigue.
Therefore, understanding these influencers is essential in designing against fatigue.
Applications in Engineering Design
Structural Engineering
In structural engineering, materials are selected and analyzed to withstand various loads and forces, ensuring safety and reliability.
Fatigue strength is particularly important in bridges, buildings, and other infrastructures that experience dynamic and cyclic forces daily.
Automotive and Aerospace Industries
The automotive and aerospace industries rely heavily on fatigue strength design for components such as car engines, aircraft wings, and fuselages.
These components undergo repeated stress during operation, making it essential to design with fatigue in mind to prevent catastrophic failures.
Manufacturing and Industrial Equipment
In manufacturing, machines and tools often operate for long periods under continuous stress.
Designing components that can resist fatigue ensures longevity and efficiency in industrial applications.
Conclusion
Understanding the fundamentals of material mechanics is essential for engineers tasked with designing reliable and efficient products.
By mastering the concepts of stress, strain, elasticity, and fatigue strength, engineers can make informed decisions that enhance safety and performance.
Whether in structural engineering, automotive, aerospace, or manufacturing, the application of these principles is crucial in developing durable and sustainable designs.
資料ダウンロード
QCD管理受発注クラウド「newji」は、受発注部門で必要なQCD管理全てを備えた、現場特化型兼クラウド型の今世紀最高の受発注管理システムとなります。
ユーザー登録
受発注業務の効率化だけでなく、システムを導入することで、コスト削減や製品・資材のステータス可視化のほか、属人化していた受発注情報の共有化による内部不正防止や統制にも役立ちます。
NEWJI DX
製造業に特化したデジタルトランスフォーメーション(DX)の実現を目指す請負開発型のコンサルティングサービスです。AI、iPaaS、および先端の技術を駆使して、製造プロセスの効率化、業務効率化、チームワーク強化、コスト削減、品質向上を実現します。このサービスは、製造業の課題を深く理解し、それに対する最適なデジタルソリューションを提供することで、企業が持続的な成長とイノベーションを達成できるようサポートします。
製造業ニュース解説
製造業、主に購買・調達部門にお勤めの方々に向けた情報を配信しております。
新任の方やベテランの方、管理職を対象とした幅広いコンテンツをご用意しております。
お問い合わせ
コストダウンが利益に直結する術だと理解していても、なかなか前に進めることができない状況。そんな時は、newjiのコストダウン自動化機能で大きく利益貢献しよう!
(β版非公開)