- お役立ち記事
- Fundamentals of material mechanics and application to strength design, improving elastic toughness and preventing fatigue fractures
月間77,185名の
製造業ご担当者様が閲覧しています*
*2025年2月28日現在のGoogle Analyticsのデータより
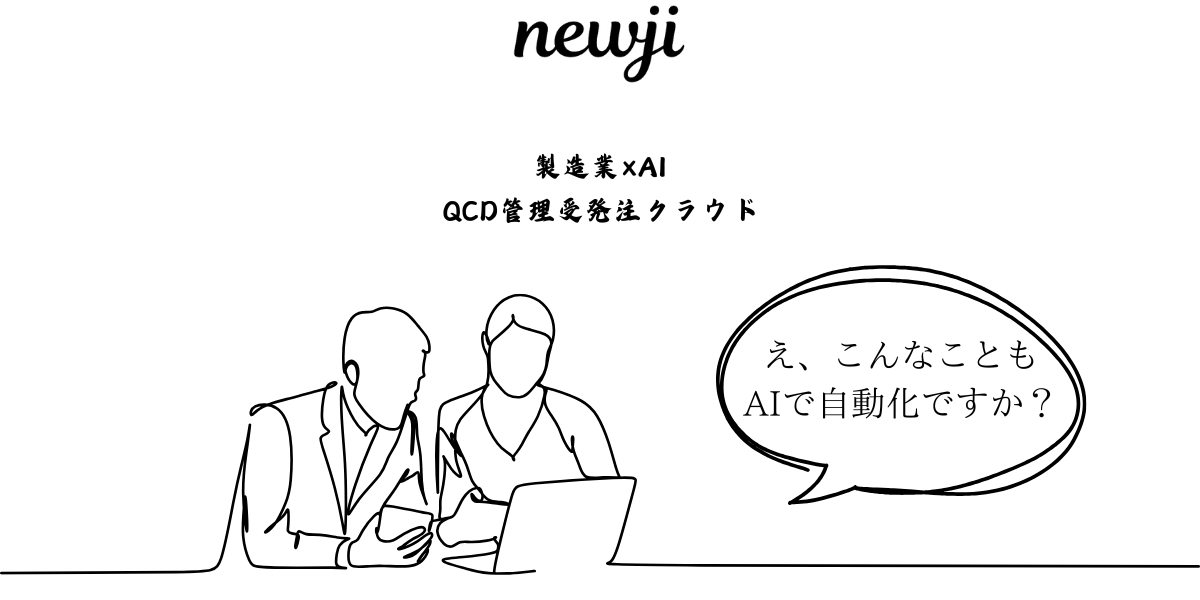
Fundamentals of material mechanics and application to strength design, improving elastic toughness and preventing fatigue fractures
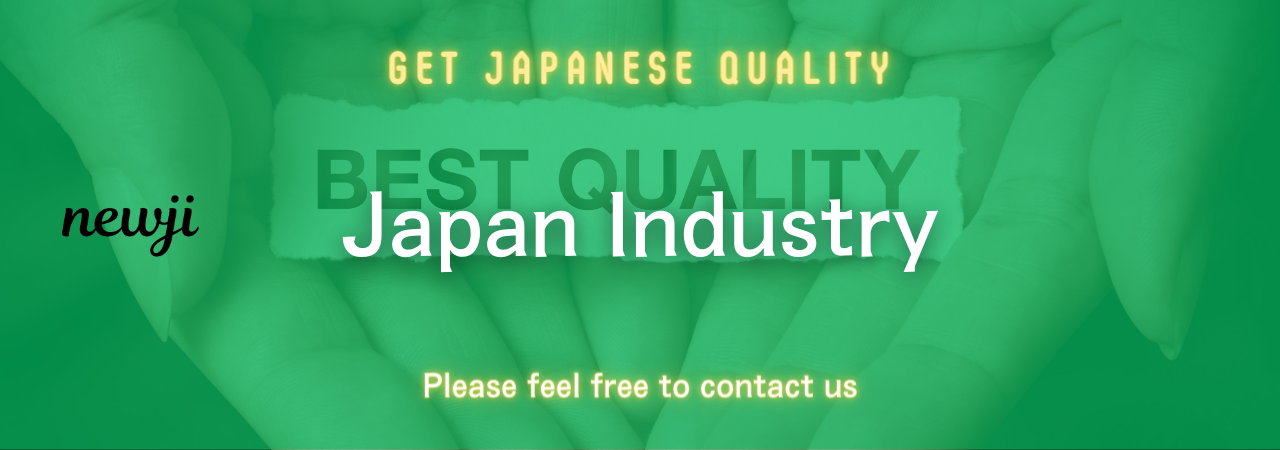
Understanding the fundamentals of material mechanics is crucial for engineers and designers who aim to create structures and components that perform reliably and safely under various conditions.
This knowledge is vital for improving elastic toughness and preventing fatigue fractures, which are common challenges in material design and engineering.
In this article, we’ll explore some basic principles of material mechanics and their application to strength design.
目次
Introduction to Material Mechanics
Material mechanics, also known as mechanics of materials, deals with the behavior of solid objects subject to stresses and strains.
It involves studying how materials deform, fail, and the factors affecting their mechanical properties.
Understanding these principles is essential in the design and analysis of structures and machines to ensure they can withstand the loads and stresses encountered during use.
Key Concepts in Material Mechanics
Stress and Strain
Stress is a measure of the internal force acting on an object, while strain is the deformation or displacement it undergoes due to the applied stress.
The relationship between stress and strain helps determine a material’s mechanical properties, which are critical for design calculations.
Stress is typically measured in units of force per area, such as Pascals (Pa), while strain is a dimensionless measure expressing the percentage of deformation.
Elasticity and Plasticity
Elasticity refers to a material’s ability to return to its original shape after the stress is removed.
Materials exhibit elastic behavior within their elastic limit, beyond which they experience permanent deformation, known as plasticity.
Understanding these properties helps in selecting materials that can endure specific loads without permanent deformation.
Ductility and Brittleness
Ductility is the ability of a material to undergo significant plastic deformation before breaking, while brittleness refers to a material’s tendency to fracture with minimal plastic deformation.
Materials such as metals are known for their ductility, whereas ceramics and glass often exhibit brittleness.
Selecting the right material involves considering these properties in relation to the intended application and anticipated loads.
Toughness
Toughness is a measure of a material’s ability to absorb energy and plastically deform without fracturing.
It’s an essential property for materials expected to undergo impact or shock loading.
The ability to absorb energy before failure makes materials tougher and more reliable under dynamic loading conditions.
Improving Elastic Toughness
Enhancing a material’s elastic toughness is key to extending its life and performance under varying operational conditions.
There are several approaches engineers can take to improve this property.
Material Selection
Selecting the right material is the first step in enhancing toughness.
Composites, alloys, and advanced polymer materials often offer superior toughness and can be tailored for specific applications.
Understanding the operational environment and load conditions is critical in making an informed material choice.
Heat Treatment
Heat treatment processes such as annealing, quenching, and tempering can significantly improve a material’s ductility and toughness.
These processes alter the microstructure of the materials, enhancing their mechanical properties and making them more resistant to stress-induced failures.
Cold Working
Cold working involves deforming a material at temperatures below its recrystallization point.
This process increases the dislocation density in the material, enhancing its strength and toughness.
Cold working is commonly used in metal forming operations to improve mechanical properties.
Surface Treatments
Applying surface treatments such as coating, carburizing, or nitriding can improve a material’s resistance to wear and fatigue.
These treatments often form a hard layer on the surface, reducing the risk of surface cracks and improving overall toughness.
Preventing Fatigue Fractures
Fatigue fractures occur when materials are subjected to repeated cyclic loading, eventually leading to failure.
Preventing fatigue fractures is crucial for ensuring the long-term safety and reliability of structures and components.
Understanding Fatigue Life
Fatigue life is the number of cycles a material can withstand before failure.
It’s influenced by factors such as material properties, surface finish, and type of loading.
Accurate prediction of fatigue life can help determine maintenance schedules and prevent unexpected failures.
Fatigue Testing
Conducting fatigue tests is essential for understanding a material’s behavior under cyclic loading.
These tests help determine the endurance limit or fatigue strength, guiding designers in setting appropriate safety margins for structures.
Design for Fatigue Resistance
Incorporating features such as fillets and rounded corners can reduce stress concentrations and enhance fatigue resistance.
Proper design and engineering practices help distribute loads more evenly, reducing the likelihood of fatigue fractures.
Material and Surface Treatments
Applying surface treatments such as shot peening or surface hardening can improve fatigue resistance by introducing compressive residual stresses on the surface.
Using advanced materials with superior fatigue properties in critical areas can also enhance durability.
Conclusion
Understanding the fundamentals of material mechanics and its application in strength design is essential for engineers and designers.
By improving elastic toughness and preventing fatigue fractures, they can ensure the safety and reliability of components and structures.
Through careful material selection, design optimization, and appropriate treatment processes, improved performance and longer service life of materials can be achieved.
資料ダウンロード
QCD管理受発注クラウド「newji」は、受発注部門で必要なQCD管理全てを備えた、現場特化型兼クラウド型の今世紀最高の受発注管理システムとなります。
ユーザー登録
受発注業務の効率化だけでなく、システムを導入することで、コスト削減や製品・資材のステータス可視化のほか、属人化していた受発注情報の共有化による内部不正防止や統制にも役立ちます。
NEWJI DX
製造業に特化したデジタルトランスフォーメーション(DX)の実現を目指す請負開発型のコンサルティングサービスです。AI、iPaaS、および先端の技術を駆使して、製造プロセスの効率化、業務効率化、チームワーク強化、コスト削減、品質向上を実現します。このサービスは、製造業の課題を深く理解し、それに対する最適なデジタルソリューションを提供することで、企業が持続的な成長とイノベーションを達成できるようサポートします。
製造業ニュース解説
製造業、主に購買・調達部門にお勤めの方々に向けた情報を配信しております。
新任の方やベテランの方、管理職を対象とした幅広いコンテンツをご用意しております。
お問い合わせ
コストダウンが利益に直結する術だと理解していても、なかなか前に進めることができない状況。そんな時は、newjiのコストダウン自動化機能で大きく利益貢献しよう!
(β版非公開)