- お役立ち記事
- Fundamentals of material mechanics and applications to stress analysis and strength design
Fundamentals of material mechanics and applications to stress analysis and strength design
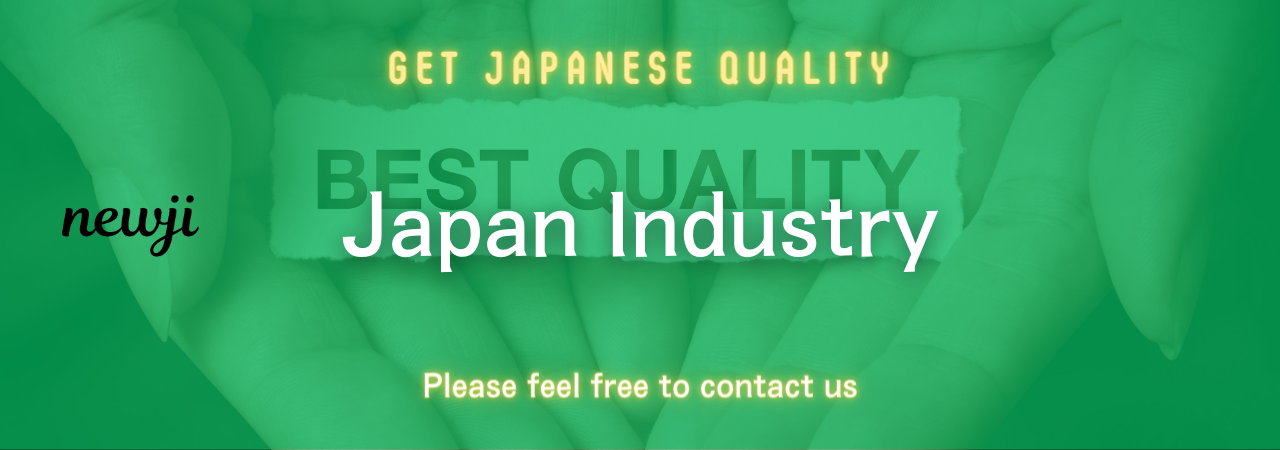
目次
Introduction to Material Mechanics
Material mechanics is a branch of engineering that explains how different materials behave under various forces and moments.
It plays a crucial role in evaluating the performance, safety, and stability of structures and mechanical systems.
Understanding material mechanics is vital for engineers and designers to ensure the strength, durability, and reliability of the structures they create.
In the field of material mechanics, several fundamental principles are used to analyze and predict material behavior.
These principles help us understand how and why materials deform, bend, stretch, or even break under various conditions.
Understanding Stress and Strain
Before we dive into applications, let’s explore two fundamental concepts: stress and strain.
What is Stress?
Stress is the force applied to a material divided by the area over which the force is applied.
Stress is expressed in units such as Pascals (Pa) or pounds per square inch (psi).
There are different types of stress, including tensile stress (pulling apart), compressive stress (pushing together), and shear stress (sliding layers).
What is Strain?
Strain is the measure of deformation representing the displacement between particles in the material body.
Strain is a dimensionless quantity and is usually expressed as a percentage.
When a material is subjected to stress, it may deform or elongate, causing strain.
Elasticity vs. Plasticity
Materials react differently under stress, based on their elastic and plastic properties.
Understanding these properties is vital for selecting the right material for an application.
Elasticity
Elasticity is the ability of a material to return to its original shape after the stress is removed.
Materials exhibiting elasticity obey Hooke’s law, which states that the deformation (strain) is proportional to the applied force (stress) until the yield point.
Plasticity
Plasticity is the property of a material to undergo permanent deformation without breaking when stress is applied.
Once the stress goes beyond the elastic limit, the material won’t regain its original shape.
Applications to Stress Analysis
Stress analysis is the process of analyzing the stresses and strains that occur in materials subjected to forces.
Effective stress analysis ensures safety and efficiency in designing mechanical structures.
Finite Element Analysis (FEA)
One of the most widespread techniques used in stress analysis is Finite Element Analysis (FEA).
It is a numerical method that breaks down complex structures into simpler parts called finite elements.
FEA simulates physical phenomena, predict behavior under certain forces, and optimize designs by evaluating different scenarios.
Fatigue Analysis
Fatigue analysis involves evaluating a material’s ability to withstand cyclic loading over time without failure.
Engineers use this analysis to predict the lifespan of components subjected to repeated loading, such as airplane wings or vehicle chassis, and to optimize their design for durability.
Failure Criteria
Various failure criteria help predict how and when a material will fail under certain conditions.
Common failure criteria include the Maximum Stress Theory, Maximum Strain Theory, and Von Mises Stress criterion.
These tools are essential for ensuring that designs are safe and functional under expected loading conditions.
Strength Design
Strength design focuses on ensuring that materials and structures can withstand the forces and loads they will encounter in real-life scenarios.
Material Selection
Selecting the appropriate material is crucial in strength design.
Different materials have different mechanical properties, including strength, ductility, toughness, and hardness.
Choosing the right material can drastically affect the performance and longevity of the structure.
Design for Safety
Engineers use safety factors to ensure that designs can withstand unexpected stresses or loads beyond the anticipated maximum.
This consideration helps prevent failure or accidents even when unforeseen conditions arise.
Load Considerations
Understanding and predicting the types of loads a structure may face is integral to strength design.
These loads can be static, such as the weight of the structure itself, or dynamic, like wind or earthquake forces.
Conclusion
Material mechanics is foundational to the development and design of robust and efficient engineering solutions.
By understanding stress, strain, and material behavior, engineers can predict performance and ensure the safety and durability of structures and systems.
Applications in stress analysis and strength design not only maximize the utility of materials but also contribute to innovation and the advancement of engineering technologies, ensuring products meet the high demands of modern usage.
Understanding the fundamentals of material mechanics is not just beneficial but essential for those involved in designing and building.
It paves the way for creating sustainable, efficient, and safe environments that support both human activity and technological advancement.
資料ダウンロード
QCD調達購買管理クラウド「newji」は、調達購買部門で必要なQCD管理全てを備えた、現場特化型兼クラウド型の今世紀最高の購買管理システムとなります。
ユーザー登録
調達購買業務の効率化だけでなく、システムを導入することで、コスト削減や製品・資材のステータス可視化のほか、属人化していた購買情報の共有化による内部不正防止や統制にも役立ちます。
NEWJI DX
製造業に特化したデジタルトランスフォーメーション(DX)の実現を目指す請負開発型のコンサルティングサービスです。AI、iPaaS、および先端の技術を駆使して、製造プロセスの効率化、業務効率化、チームワーク強化、コスト削減、品質向上を実現します。このサービスは、製造業の課題を深く理解し、それに対する最適なデジタルソリューションを提供することで、企業が持続的な成長とイノベーションを達成できるようサポートします。
オンライン講座
製造業、主に購買・調達部門にお勤めの方々に向けた情報を配信しております。
新任の方やベテランの方、管理職を対象とした幅広いコンテンツをご用意しております。
お問い合わせ
コストダウンが利益に直結する術だと理解していても、なかなか前に進めることができない状況。そんな時は、newjiのコストダウン自動化機能で大きく利益貢献しよう!
(Β版非公開)