- お役立ち記事
- Fundamentals of material mechanics and fatigue strength and how to utilize them for fracture surface analysis and countermeasures for fracture causes
月間76,176名の
製造業ご担当者様が閲覧しています*
*2025年3月31日現在のGoogle Analyticsのデータより
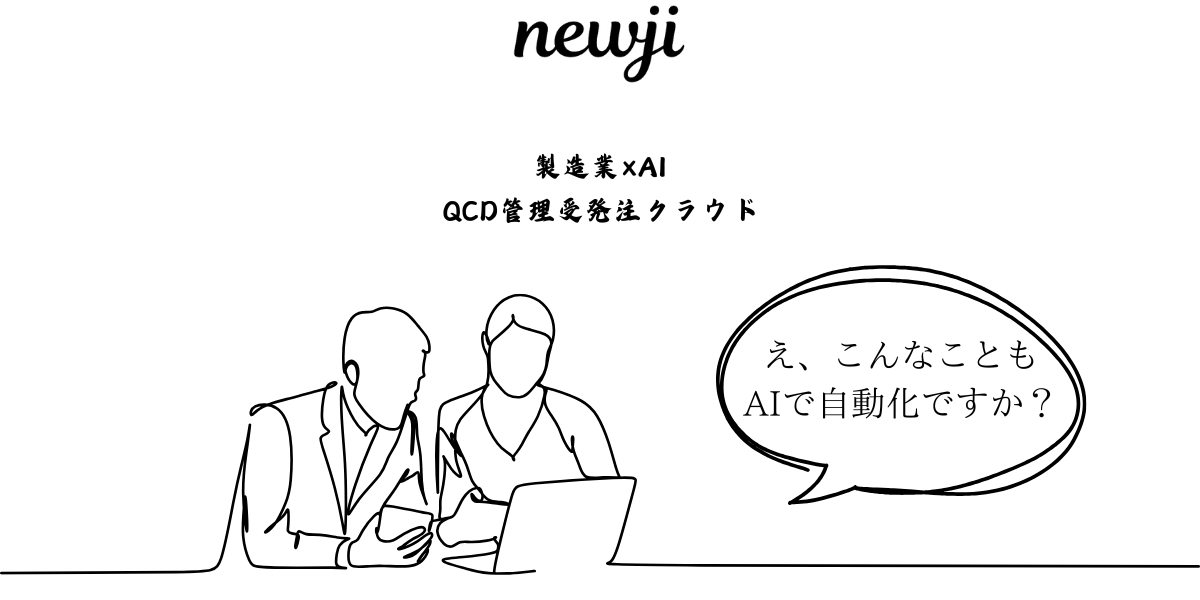
Fundamentals of material mechanics and fatigue strength and how to utilize them for fracture surface analysis and countermeasures for fracture causes
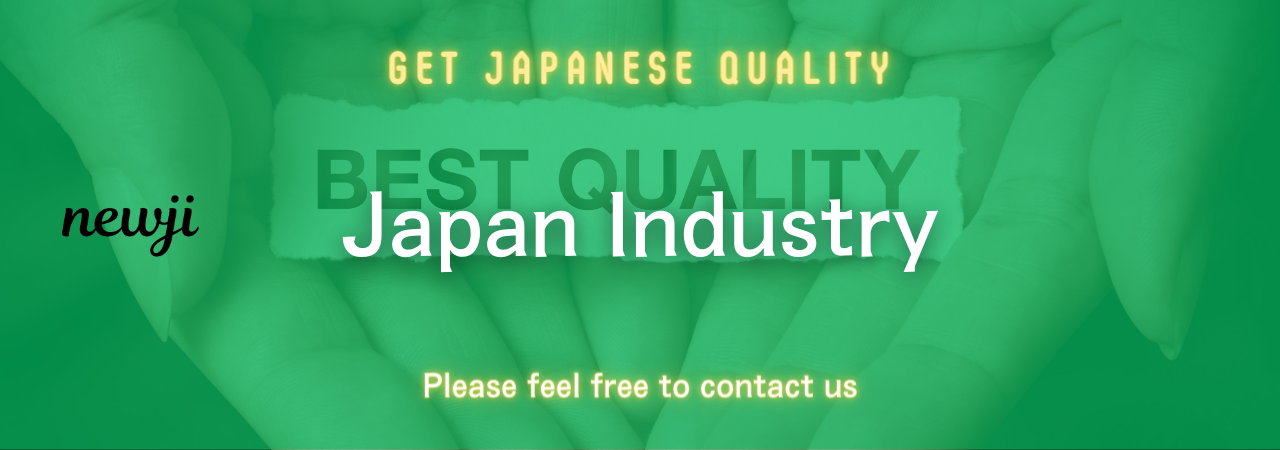
目次
Understanding Material Mechanics
Material mechanics is a branch of engineering that focuses on the behavior of solid materials under external forces and deformations.
At its core, material mechanics is about understanding the relationship between forces, stresses, and the resulting deformation of materials.
This knowledge is crucial for designing structures and components that are safe and efficient.
The key concepts in material mechanics include stress, strain, and elasticity.
Stress is the internal force per unit area within a material, while strain is the measure of deformation experienced by the material when subjected to stress.
Elasticity, on the other hand, refers to the ability of a material to return to its original shape after deformation once the external forces are removed.
Materials with high elasticity, like rubber, can withstand significant deformation, whereas materials with low elasticity, like glass, are more brittle.
Fatigue Strength and Its Importance
Fatigue strength is a crucial concept in material mechanics, particularly in understanding how materials behave under repeated loading and unloading cycles.
It refers to the maximum stress a material can withstand for a specified number of cycles without failing.
Fatigue failure occurs when a material, though subjected to stresses lower than its yield or ultimate tensile strength, breaks due to the repetitive application of those stresses over time.
Fatigue strength is essential in applications where materials are exposed to fluctuating forces, such as in bridges, vehicles, and machinery components.
Engineers must carefully consider fatigue strength to ensure the longevity and reliability of structures and mechanical parts.
Ignoring fatigue strength can lead to catastrophic failures, as exemplified in historical incidents involving aircraft and bridges.
Fracture Surface Analysis
Fracture surface analysis is a powerful tool in understanding the root causes of material failure.
By examining the surface of a fractured material, engineers and scientists can gain insights into the failure mechanism and the conditions that led to it.
The process typically involves visual inspection, microscopy, and sometimes chemical analysis to identify the fracture mode and the presence of any defects or inclusions.
There are generally three main modes of fracture: ductile, brittle, and fatigue.
– Ductile fractures are characterized by significant plastic deformation before failure and appear rough and fibrous.
– Brittle fractures, on the other hand, happen with little to no plastic deformation and usually have a smooth, granular appearance.
– Fatigue fractures have distinct features such as striations and beach marks, which indicate progressive crack growth over time.
Utilizing Fracture Analysis for Countermeasures
Once the cause of fracture is identified through surface analysis, steps can be taken to prevent future occurrences.
Implementing countermeasures involves making adjustments to design, material selection, and manufacturing processes.
One effective approach to countermeasure against fatigue failures is to enhance the material’s fatigue strength.
This can be achieved through various means, such as using high-quality materials that have undergone processes like heat treatment or surface hardening.
Design modifications can also play a critical role in improving fatigue life by reducing stress concentrations at vulnerable points in the structure.
For brittle fractures, selecting more ductile materials and adjusting operating conditions to avoid sharp temperature or pressure changes may help prevent failure.
Manufacturing processes should ensure high-quality control to eliminate defects and inclusions in materials that can act as crack initiation sites.
Counteracting Fracture Causes
Addressing fracture causes requires a multidisciplinary approach involving materials science, engineering design, and process optimization.
Material Selection and Processing
Choosing the right material for a specific application is paramount in mitigating fracture risks.
Materials should be selected based on their mechanical properties, environmental resistance, and suitability for the intended use case.
In addition to material selection, processing techniques such as casting, forging, and machining must be controlled to prevent defects that could initiate cracks.
Regular inspections and quality assurances throughout the manufacturing process are vital to ensure material integrity.
Design Considerations
Effective design is critical in preventing fractures.
Engineers must incorporate features that distribute stress evenly and minimize concentration points where cracks are likely to start.
This can include using fillets instead of sharp corners, optimizing geometries, and considering the load paths in complex structures.
Simulation tools and finite element analysis (FEA) can aid in predicting stresses and potential failure points during the design phase, enabling engineers to make informed decisions before manufacturing begins.
Operational and Maintenance Strategies
Regular inspection and maintenance play a key role in early detection of potential failures.
Implementing scheduled inspections can help identify cracks or wear before they lead to catastrophic failures.
Condition monitoring techniques, like vibration analysis and non-destructive testing (NDT), provide real-time data on the health of materials and structures.
Finally, operational protocols should consider the limits of material strength to avoid exceeding stress thresholds.
Operators should be trained to recognize signs of wear and stress, ensuring that machinery and structures are used within their designed capacities.
Conclusion
Understanding the fundamentals of material mechanics and fatigue strength is essential for anyone involved in engineering and design.
By recognizing how materials respond to forces and deformations, and by utilizing fracture surface analysis, engineers can effectively prevent material failure.
Through careful material selection, robust designs, and strategic operational practices, the longevity and reliability of structures and components can be significantly improved, leading to safer environments and more durable products.
資料ダウンロード
QCD管理受発注クラウド「newji」は、受発注部門で必要なQCD管理全てを備えた、現場特化型兼クラウド型の今世紀最高の受発注管理システムとなります。
ユーザー登録
受発注業務の効率化だけでなく、システムを導入することで、コスト削減や製品・資材のステータス可視化のほか、属人化していた受発注情報の共有化による内部不正防止や統制にも役立ちます。
NEWJI DX
製造業に特化したデジタルトランスフォーメーション(DX)の実現を目指す請負開発型のコンサルティングサービスです。AI、iPaaS、および先端の技術を駆使して、製造プロセスの効率化、業務効率化、チームワーク強化、コスト削減、品質向上を実現します。このサービスは、製造業の課題を深く理解し、それに対する最適なデジタルソリューションを提供することで、企業が持続的な成長とイノベーションを達成できるようサポートします。
製造業ニュース解説
製造業、主に購買・調達部門にお勤めの方々に向けた情報を配信しております。
新任の方やベテランの方、管理職を対象とした幅広いコンテンツをご用意しております。
お問い合わせ
コストダウンが利益に直結する術だと理解していても、なかなか前に進めることができない状況。そんな時は、newjiのコストダウン自動化機能で大きく利益貢献しよう!
(β版非公開)