- お役立ち記事
- Fundamentals of material mechanics and its application to molding and rigidity/strength design of composite materials (CFRP)
月間77,185名の
製造業ご担当者様が閲覧しています*
*2025年2月28日現在のGoogle Analyticsのデータより
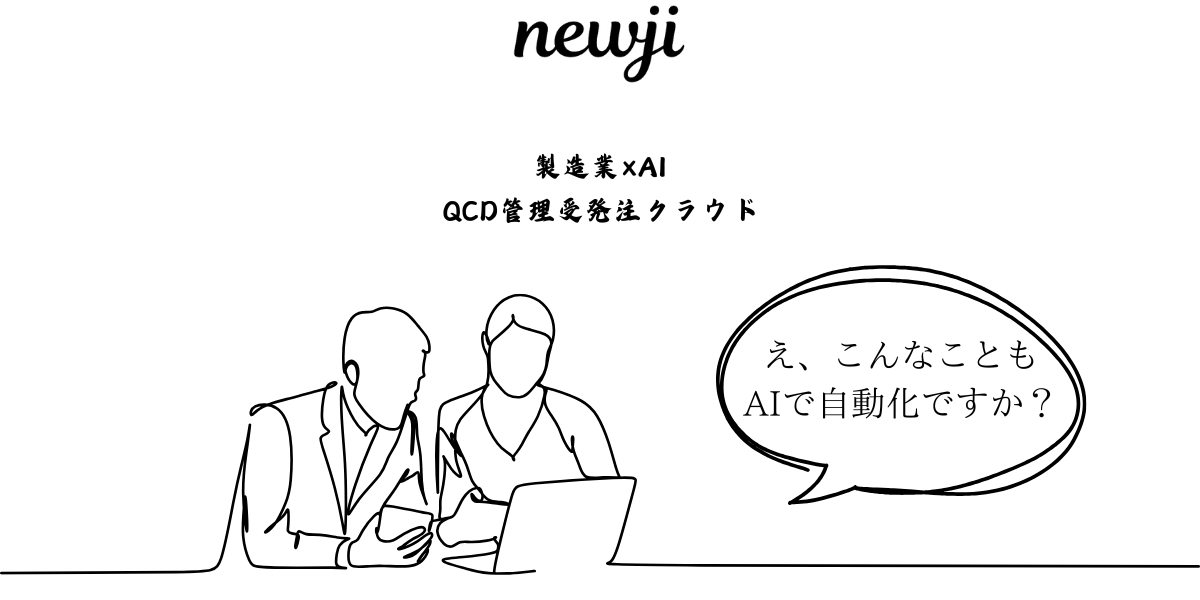
Fundamentals of material mechanics and its application to molding and rigidity/strength design of composite materials (CFRP)
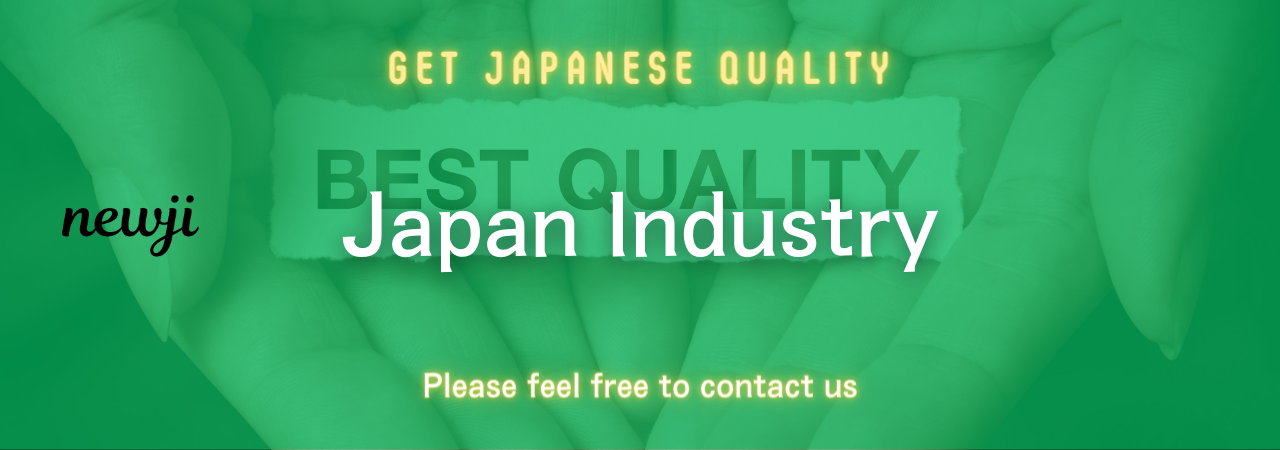
Understanding the fundamentals of material mechanics is crucial, especially when it comes to the design and application of composite materials like Carbon Fiber Reinforced Polymers (CFRP). These materials are widely used due to their high strength-to-weight ratio and stiffness, making them ideal for various engineering applications.
目次
What is Material Mechanics?
Material mechanics is a field of engineering that studies the behavior of materials under various forces and conditions. It involves understanding how materials deform, fail, and behave when subjected to different stresses. This branch of mechanics helps engineers design structures that can resist external loads without deforming or breaking.
Key Concepts in Material Mechanics
Several key concepts are fundamental to material mechanics, each playing a vital role in understanding material behavior.
– **Stress and Strain**: Stress is the internal force per unit area within a material, arising from externally applied forces. Strain, on the other hand, is the deformation or displacement experienced by the material due to applied stress. Understanding these concepts is crucial for analyzing how materials respond to different loads.
– **Elasticity and Plasticity**: Elasticity refers to the ability of a material to return to its original shape after the removal of a load. Plasticity is the characteristic of a material to undergo permanent deformation. Some materials behave elastically up to a certain point, known as the yield point, beyond which they behave plastically.
– **Young’s Modulus**: This is a measure of a material’s stiffness, defined as the ratio of stress to strain in the elastic region of the material’s deformation. A high Young’s modulus indicates that a material is stiff, meaning it will deform less under load.
– **Shear Modulus and Bulk Modulus**: These are measures of a material’s ability to withstand shearing forces and changes in volume under pressure, respectively.
– **Fatigue and Creep**: Fatigue is the weakening of a material caused by repeatedly applied loads. Creep is the slow, progressive deformation of a material under constant stress, typically at high temperature.
Composite Materials (CFRP)
Composite materials are engineered by combining two or more distinct materials to achieve properties that are superior to those of the individual components. CFRP, a popular composite material, is renowned for its exceptional strength-to-weight ratio.
Properties of CFRP
CFRP is composed of a polymer matrix reinforced with carbon fibers, offering numerous advantageous properties:
– **High Strength and Stiffness**: Carbon fibers provide CFRP with superior strength and stiffness, making it suitable for applications where these characteristics are essential.
– **Lightweight**: The density of CFRP is significantly lower than materials like steel, making it ideal for applications, such as in the aerospace and automotive industries, where reducing weight is crucial.
– **Corrosion Resistance**: Unlike metals, CFRP does not corrode, which extends the lifespan of components and structures made from this material.
– **Thermal Conductivity**: While not as conductive as metals, CFRP has moderate thermal conductivity, which can be an advantage in certain applications.
Application of Material Mechanics to CFRP Design
Understanding material mechanics is essential in designing with CFRP to ensure components meet performance expectations. Here are the vital steps in the design process:
1. Understanding Load Requirements
Before design, it’s essential to understand the loads the composite part will encounter during its service life. This includes tensile, compressive, and shear loads. Engineers must also consider dynamic loads, such as vibrations and impacts.
2. Determining Material Properties
Assessing the properties of CFRP, like stress-strain behavior, fatigue resistance, and thermal expansion, is critical. These properties help in predicting how the composite will behave under various conditions.
3. Designing for Rigidity and Strength
The design should focus on achieving the required stiffness and strength. This involves selecting appropriate fiber orientations, layer sequences, and thicknesses to meet the performance criteria while minimizing weight.
4. Simulation and Testing
Before mass production, simulation tools like finite element analysis (FEA) are used to model the behavior of the composite under different loading conditions. Physical prototyping and testing further validate the design, ensuring safety and performance.
5. Manufacturing Considerations
The chosen design must be manufacturable. Engineers need to consider the fabrication processes, such as lay-up and curing, and how they influence the final properties of CFRP.
Advancements in CFRP Design
With advancements in technology, CFRP design continues to evolve:
Advanced Simulation Techniques
Modern simulation tools offer more accurate predictions of material behavior, helping optimize CFRP structures for better performance and efficiency.
Innovative Reinforcement Techniques
New fibers and matrix materials are being developed, enhancing the mechanical properties and broadening potential applications of CFRP.
Sustainable Practices
Efforts to produce CFRP in environmentally friendly ways are underway, with recycling and bio-based materials being explored to reduce the ecological footprint of composite production.
In conclusion, understanding the fundamentals of material mechanics is foundational for the effective application of composite materials like CFRP in modern engineering. By mastering these principles, engineers can design robust, lightweight, and durable components that meet the demands of today’s innovative industries.
資料ダウンロード
QCD管理受発注クラウド「newji」は、受発注部門で必要なQCD管理全てを備えた、現場特化型兼クラウド型の今世紀最高の受発注管理システムとなります。
ユーザー登録
受発注業務の効率化だけでなく、システムを導入することで、コスト削減や製品・資材のステータス可視化のほか、属人化していた受発注情報の共有化による内部不正防止や統制にも役立ちます。
NEWJI DX
製造業に特化したデジタルトランスフォーメーション(DX)の実現を目指す請負開発型のコンサルティングサービスです。AI、iPaaS、および先端の技術を駆使して、製造プロセスの効率化、業務効率化、チームワーク強化、コスト削減、品質向上を実現します。このサービスは、製造業の課題を深く理解し、それに対する最適なデジタルソリューションを提供することで、企業が持続的な成長とイノベーションを達成できるようサポートします。
製造業ニュース解説
製造業、主に購買・調達部門にお勤めの方々に向けた情報を配信しております。
新任の方やベテランの方、管理職を対象とした幅広いコンテンツをご用意しております。
お問い合わせ
コストダウンが利益に直結する術だと理解していても、なかなか前に進めることができない状況。そんな時は、newjiのコストダウン自動化機能で大きく利益貢献しよう!
(β版非公開)