- お役立ち記事
- Fundamentals of material mechanics, finite element method, and optimization algorithms
月間76,176名の
製造業ご担当者様が閲覧しています*
*2025年3月31日現在のGoogle Analyticsのデータより
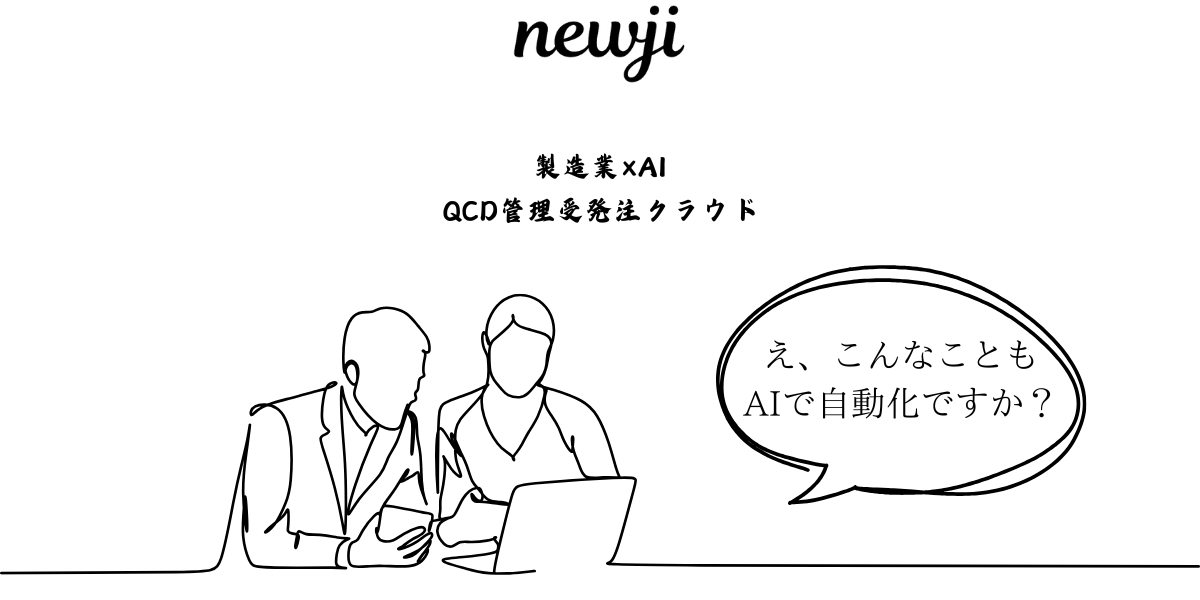
Fundamentals of material mechanics, finite element method, and optimization algorithms
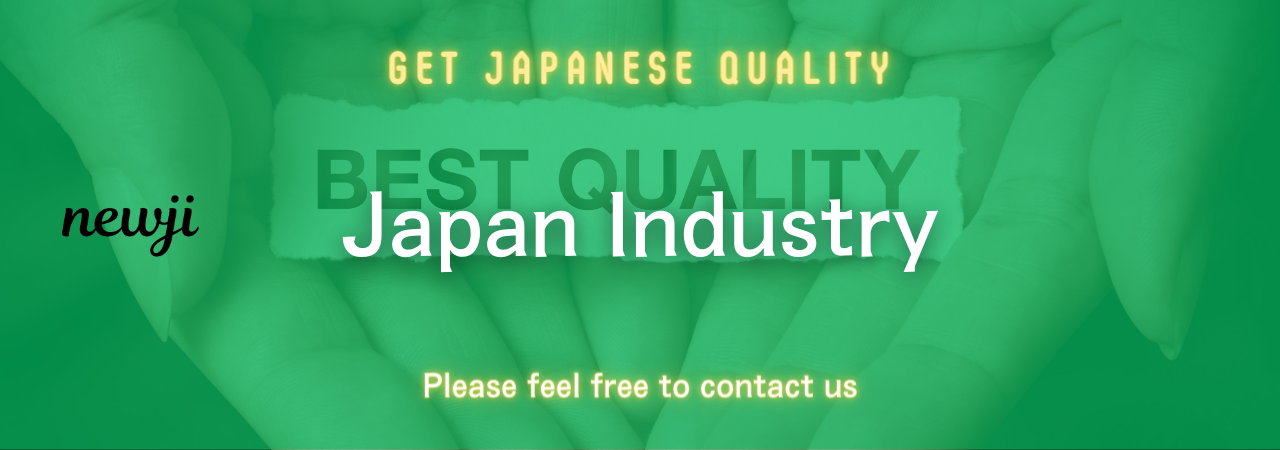
目次
Understanding Material Mechanics
Material mechanics is a branch of physics that studies the behavior of solid materials under various forces and conditions.
At its core, the study involves understanding how materials deform (change shape) and fail when subjected to external forces such as tension, compression, and shear.
One of the fundamental concepts in material mechanics is stress and strain.
Stress is the internal force exerted by a material when subjected to external loads, expressed as force per unit area.
On the other hand, strain refers to the deformation caused by stress and is expressed as the change in length over the original length.
Engineers and scientists use different types of stress and strain relationships to predict how a material will respond to various forces.
These relationships include elastic (reversible deformation), plastic (permanent deformation), and viscoelastic (time-dependent behavior) responses.
Material properties, such as Young’s modulus, yield strength, and Poisson’s ratio, play critical roles in understanding material behavior.
Young’s modulus measures a material’s stiffness or resistance to deformation.
Yield strength defines the stress at which a material begins to deform permanently.
Poisson’s ratio describes the ratio of transverse strain to axial strain in a material under axial loading.
By mastering these properties and behaviors, engineers can design materials and structures that effectively withstand real-world challenges.
Introduction to the Finite Element Method (FEM)
The Finite Element Method (FEM) is a powerful numerical technique used to solve complex engineering problems related to material mechanics and many other fields.
It provides a way to approximate solutions for differential equations that describe physical phenomena.
FEM divides a complex structure or object into smaller, simpler “elements” connected at “nodes.”
This division transforms the structure into a mesh, a network of points and lines representing the object’s geometry.
By analyzing each element individually and then assembling them, engineers can obtain a comprehensive understanding of the structure’s behavior under various conditions.
FEM is particularly valuable because it can easily handle complicated shapes.
It is widely used in industries such as automotive, aerospace, civil engineering, and biomechanics to design, optimize, and test structures and components before physical prototypes are built.
Fields like heat transfer, fluid dynamics, and electromagnetism also benefit from FEM by simulating how different factors affect performance and functionality.
Using FEM involves creating a mathematical model of the object, defining boundary conditions and loads, and selecting a suitable element type.
The method computes approximate values for various results, such as displacements, stresses, and strains.
However, FEM requires significant computational resources and expertise to set up, solve, and interpret the results accurately.
Advancements in computer technology and software have made it possible to utilize FEM in increasingly complex and large-scale problems.
Exploring Optimization Algorithms
Optimization algorithms are essential tools for finding the best solutions in engineering and other disciplines.
These algorithms seek to maximize or minimize an objective function by finding an optimal set of input values within defined constraints.
There are different types of optimization algorithms, including deterministic and stochastic methods.
Deterministic methods, like gradient descent and linear programming, follow a fixed sequence of steps to reach an optimal solution.
These methods are suitable for problems with a well-defined mathematical model and constraints.
On the other hand, stochastic methods like genetic algorithms and particle swarm optimization use random variables to explore the solution space.
These methods are particularly useful for complex, nonlinear problems where traditional approaches may be inefficient or ineffective.
A key aspect of optimization algorithms is their ability to handle multi-objective problems, where multiple conflicting objectives must be optimized simultaneously.
This feature is crucial in real-world applications, such as engineering design and resource allocation, where trade-offs between different goals need to be balanced.
Selecting the right optimization algorithm depends on several factors, including the problem’s complexity, size, constraints, and the desired accuracy of the solution.
By integrating optimization algorithms with advanced techniques like FEM, engineers can develop innovative solutions that meet specific performance criteria while minimizing cost, weight, or energy consumption.
The Intersection of Material Mechanics, FEM, and Optimization
Material mechanics, FEM, and optimization algorithms are interconnected fields that work together to solve complex engineering challenges.
Material mechanics provides the foundational understanding of how materials behave under different conditions.
FEM offers a practical tool for analyzing and predicting these behaviors in complex structures.
Optimization algorithms ensure the most efficient, cost-effective solutions are found.
For example, in designing a new aircraft wing, engineers must understand the mechanical properties of materials used.
They use FEM to simulate the wing’s performance under various loads like lift, drag, and turbulence.
Optimization algorithms then improve the wing’s design, minimizing weight while maximizing strength and aerodynamic efficiency.
These interconnected fields contribute significantly to innovation across industries, leading to safer, more efficient, and sustainable solutions.
By continually advancing our understanding and application of material mechanics, FEM, and optimization algorithms, engineers can push the boundaries of what’s possible in technology and design.
Conclusion
A comprehensive understanding of material mechanics, the finite element method, and optimization algorithms is crucial for anyone involved in engineering and design.
These fields provide powerful tools and frameworks for analyzing the behavior of materials, simulating real-world conditions, and identifying the best solutions to complex problems.
As technology advances, these areas will continue to evolve and offer new possibilities for innovation, driving progress in various industries and contributing to a more sustainable and efficient future.
資料ダウンロード
QCD管理受発注クラウド「newji」は、受発注部門で必要なQCD管理全てを備えた、現場特化型兼クラウド型の今世紀最高の受発注管理システムとなります。
ユーザー登録
受発注業務の効率化だけでなく、システムを導入することで、コスト削減や製品・資材のステータス可視化のほか、属人化していた受発注情報の共有化による内部不正防止や統制にも役立ちます。
NEWJI DX
製造業に特化したデジタルトランスフォーメーション(DX)の実現を目指す請負開発型のコンサルティングサービスです。AI、iPaaS、および先端の技術を駆使して、製造プロセスの効率化、業務効率化、チームワーク強化、コスト削減、品質向上を実現します。このサービスは、製造業の課題を深く理解し、それに対する最適なデジタルソリューションを提供することで、企業が持続的な成長とイノベーションを達成できるようサポートします。
製造業ニュース解説
製造業、主に購買・調達部門にお勤めの方々に向けた情報を配信しております。
新任の方やベテランの方、管理職を対象とした幅広いコンテンツをご用意しております。
お問い合わせ
コストダウンが利益に直結する術だと理解していても、なかなか前に進めることができない状況。そんな時は、newjiのコストダウン自動化機能で大きく利益貢献しよう!
(β版非公開)