- お役立ち記事
- Fundamentals of material mechanics, fracture mechanics, and FEM, and applications to fracture prediction using FEM
月間76,176名の
製造業ご担当者様が閲覧しています*
*2025年3月31日現在のGoogle Analyticsのデータより
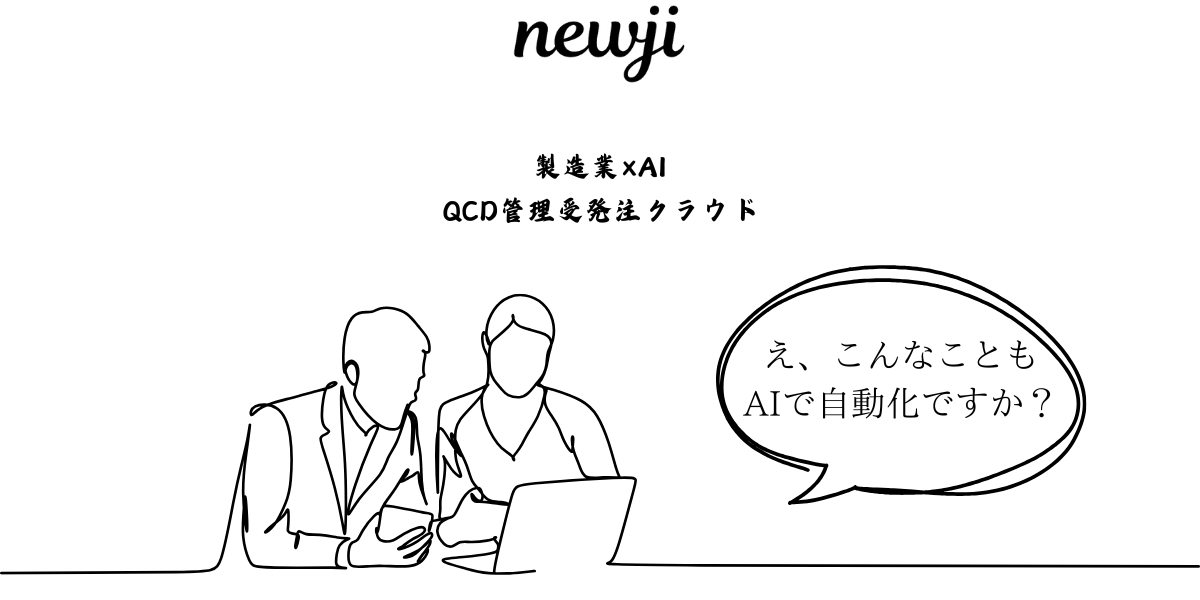
Fundamentals of material mechanics, fracture mechanics, and FEM, and applications to fracture prediction using FEM
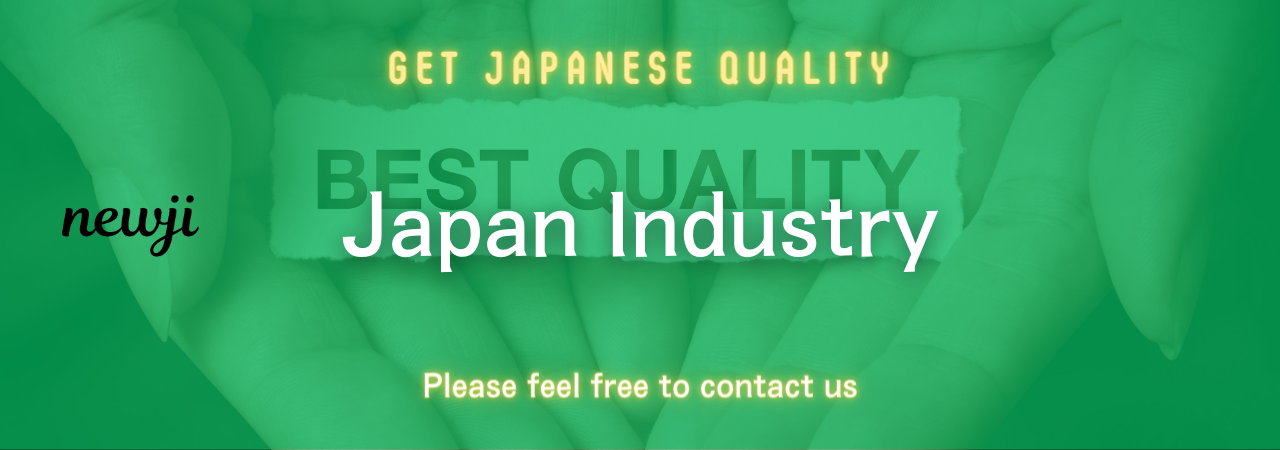
目次
Understanding Material Mechanics
Material mechanics is a branch of physics that focuses on the behavior of solid materials under various forces and conditions.
It forms the foundation for engineering and design practices, ensuring that structures are safe, efficient, and reliable.
This subject explores concepts like stress, strain, elasticity, and plasticity, which are crucial for comprehending how materials react when subjected to different loads.
By examining these reactions, engineers can predict how materials will perform in real-world applications, such as in constructions, machines, and everyday objects.
Stress and Strain
Stress is the internal force exerted by a material per unit area, while strain is the deformation or displacement it undergoes as a result of stress.
These concepts are fundamental in material mechanics, as they help predict how materials will respond to external forces.
Stress can be caused by tension, compression, or shear, each impacting the material in unique ways.
Understanding stress and strain is essential for analyzing and designing structures that can safely withstand various forces.
Elasticity and Plasticity
Elasticity refers to the ability of a material to return to its original shape after being deformed by an external force.
Materials like rubber and steel exhibit elastic behavior within certain limits, making them ideal for applications where temporary deformation is required.
In contrast, plasticity describes the permanent deformation of a material when the stress applied exceeds its elastic limit.
Materials such as clay and certain metals display plastic behavior, which is crucial for applications involving shaping or forming materials into different structures.
Exploring Fracture Mechanics
Fracture mechanics is a specialized field within material mechanics that investigates how and why materials crack or break.
By understanding the principles of fracture mechanics, engineers can prevent catastrophic failures in structures and prolong their lifespan.
This field focuses on the behavior of cracks in materials, analyzing factors such as stress intensity, crack propagation, and fracture toughness.
It is particularly important in industries like aerospace, automotive, and civil engineering, where material failure can have dire consequences.
Crack Propagation
Crack propagation is the process by which a crack in a material grows under repeated or sustained stress.
This phenomenon can lead to sudden and unexpected failure if not properly managed.
Understanding the conditions that lead to crack propagation is essential for developing safe and reliable structures.
Factors such as the material’s fracture toughness, the size and shape of the crack, and external environmental conditions all play a role in crack propagation.
Engineers use this knowledge to design materials and structures that can resist crack growth and prevent catastrophic failure.
Fracture Toughness
Fracture toughness is a measure of a material’s ability to resist crack propagation and subsequent failure.
Materials with high fracture toughness can withstand significant stress before a crack begins to grow, making them ideal for critical applications.
Testing and improving fracture toughness is a key aspect of fracture mechanics, as it ensures that materials are strong enough to meet safety and performance standards.
By selecting materials with appropriate fracture toughness, engineers can design structures that are both efficient and durable.
Introduction to Finite Element Method (FEM)
The Finite Element Method (FEM) is a powerful computational technique used to simulate and analyze the behavior of materials and structures under various conditions.
It divides a complex structure into smaller, manageable elements, allowing for a detailed examination of each component’s response to external forces.
FEM has become an essential tool in engineering and design, as it provides accurate predictions of material behavior, even in complex scenarios.
By using FEM, engineers can optimize designs, improve safety, and reduce the need for costly physical testing.
Applications of FEM
FEM is widely used across various industries, from automotive and aerospace to civil engineering and biomedical applications.
Its versatility and accuracy make it indispensable for solving complex engineering problems and optimizing designs for performance and safety.
In the automotive industry, FEM is used to simulate crash tests and analyze vehicle dynamics, ensuring that cars meet safety standards and perform efficiently.
In aerospace, FEM aids in the design of aircraft structures that can withstand extreme conditions while minimizing weight.
In civil engineering, FEM helps in designing safe and efficient structures like bridges and buildings by predicting their response to various loads and conditions.
Additionally, in biomedical applications, FEM is employed to simulate the behavior of biological tissues and medical devices, contributing to the development of safer and more efficient healthcare solutions.
Predicting Fracture Using FEM
One of the most valuable applications of FEM is in predicting and preventing material fracture.
By simulating the behavior of materials under stress, FEM can identify potential weak points and prevent catastrophic failures.
Simulating Stress and Strain
FEM allows engineers to simulate stress and strain distribution across a material or structure, providing insight into how it will respond to various loads.
This information is crucial for identifying areas that are susceptible to crack initiation and propagation.
By accurately predicting stress and strain, FEM enables engineers to optimize designs and improve material performance, reducing the risk of fracture and extending the life of structures.
Identifying Critical Points
Through FEM simulations, engineers can identify critical points in a structure where stress concentration is highest, increasing the likelihood of fracture.
This information is vital for improving the design and reinforcing these areas with stronger materials or additional support.
By addressing these critical points, engineers can enhance the overall safety and durability of structures, preventing failures that could lead to costly repairs or accidents.
In conclusion, the fields of material mechanics, fracture mechanics, and the Finite Element Method are integral to the design and analysis of reliable and efficient structures.
By understanding the principles of stress, strain, elasticity, plasticity, and fracture, engineers can predict material behavior and prevent failures.
FEM further enhances this capability by providing detailed simulations that aid in optimizing designs and ensuring safety across various industries.
As technology advances, these disciplines will continue to play a crucial role in developing innovative solutions to engineering challenges.
資料ダウンロード
QCD管理受発注クラウド「newji」は、受発注部門で必要なQCD管理全てを備えた、現場特化型兼クラウド型の今世紀最高の受発注管理システムとなります。
ユーザー登録
受発注業務の効率化だけでなく、システムを導入することで、コスト削減や製品・資材のステータス可視化のほか、属人化していた受発注情報の共有化による内部不正防止や統制にも役立ちます。
NEWJI DX
製造業に特化したデジタルトランスフォーメーション(DX)の実現を目指す請負開発型のコンサルティングサービスです。AI、iPaaS、および先端の技術を駆使して、製造プロセスの効率化、業務効率化、チームワーク強化、コスト削減、品質向上を実現します。このサービスは、製造業の課題を深く理解し、それに対する最適なデジタルソリューションを提供することで、企業が持続的な成長とイノベーションを達成できるようサポートします。
製造業ニュース解説
製造業、主に購買・調達部門にお勤めの方々に向けた情報を配信しております。
新任の方やベテランの方、管理職を対象とした幅広いコンテンツをご用意しております。
お問い合わせ
コストダウンが利益に直結する術だと理解していても、なかなか前に進めることができない状況。そんな時は、newjiのコストダウン自動化機能で大きく利益貢献しよう!
(β版非公開)