- お役立ち記事
- Fundamentals of metal 3D printing and application to defect suppression technology for printed objects
Fundamentals of metal 3D printing and application to defect suppression technology for printed objects
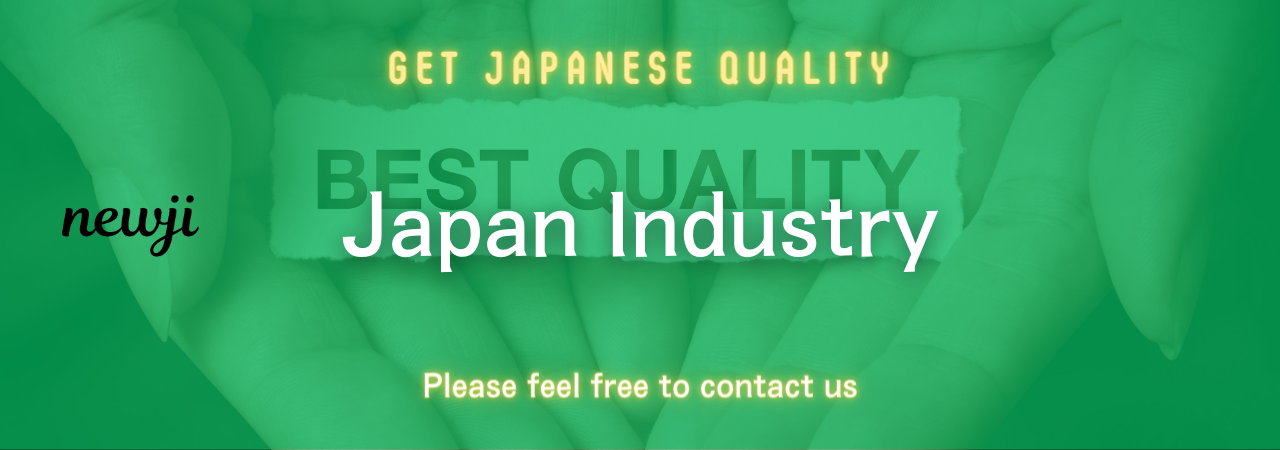
目次
Introduction to Metal 3D Printing
Metal 3D printing, a revolutionary advancement in manufacturing technologies, has opened new doors for industry and innovation.
Unlike traditional methods, which often involve machining away material, 3D printing creates objects by adding material layer by layer.
This approach can lead to less waste and allows for the creation of highly complex designs that might be impossible with conventional manufacturing methods.
In metal 3D printing, metals like aluminum, titanium, and stainless steel are the primary materials used.
These metals are either in powder form or wire, which are then melted by a high-energy source, such as a laser or electron beam, to build the object.
The precision in this process ensures that the resulting products meet strict standards required in industries like aerospace, automotive, and healthcare, where reliability and durability are essential.
Common Techniques in Metal 3D Printing
Selective Laser Melting (SLM)
One popular method of metal 3D printing is Selective Laser Melting (SLM).
In this technique, a high-powered laser selectively melts metal powder spread across a build platform.
The laser traces the cross-section of the part to form solid layers, which are stacked upon each other to complete the build.
SLM is known for creating strong, dense metal parts and is used when precision is critical.
Electron Beam Melting (EBM)
Another significant technique is Electron Beam Melting (EBM).
This method also uses powders but employs an electron beam instead of a laser to melt the material.
EBM typically operates at higher temperatures and in a vacuum, which can lead to faster build times.
This makes EBM particularly suitable for manufacturing components where high strength and thermal stability are paramount.
Direct Metal Laser Sintering (DMLS)
Direct Metal Laser Sintering (DMLS) works by sintering metal powder particles to create a solid structure.
While similar to SLM, DMLS is often used with metal alloys and can handle more challenging material combinations.
It enables the production of intricate geometries without sacrificing strength or durability and is frequently employed in the orthopedic implant sector.
Applications of Metal 3D Printing
Metal 3D printing has diverse applications across various industries.
In aerospace, the technology is crucial for making lightweight yet strong components.
This reduces fuel consumption and emissions.
The automotive industry uses metal 3D printing to produce complex parts quickly, enabling rapid prototyping and custom car manufacturing.
In healthcare, personalized surgical implants and prosthetics are increasingly created through metal 3D printing, tailored specifically for each patient, enhancing effectiveness and comfort.
Furthermore, metal 3D printing is extensively used in the tooling industry, where it aids in producing custom tools and fixtures rapidly, reducing downtime and increasing production efficiency.
Jewelry design has also embraced this technology, allowing for intricate and precise creations that would be challenging to achieve with traditional methods.
Challenges in Metal 3D Printing
Despite its advantages, metal 3D printing faces several challenges.
One significant issue is the presence of defects in printed parts.
These defects might include porosity, residual stresses, and incomplete melting of powders or wires.
Such imperfections can lead to weaker mechanical properties, rendering parts unsuitable for critical applications.
The high cost of materials and machinery is another challenge, making entry difficult for smaller companies.
Metal powders, particularly those that meet aerospace or medical standards, can be expensive.
Additionally, maintaining a stable environment during the printing process is crucial but can be costly.
Technology for Defect Suppression in Metal 3D Printing
Advanced technology aims to suppress defects in metal 3D printing to enhance quality and expand its applications.
One approach involves refining process parameters to optimize the conditions under which materials are melted and solidified.
This fine-tuning can minimize issues like porosity and cracking.
Real-time monitoring systems are also being developed to detect defects as they occur during the printing process.
These systems use sensors and cameras to track the build process and identify anomalies that could indicate a defect.
This allows for immediate intervention, potentially saving materials and reducing waste.
Furthermore, simulation software is playing an increasingly vital role.
These programs model the physical phenomena occurring during the print and predict areas where defects might arise.
Armed with this information, operators can adjust their approach, preemptively addressing issues.
Finally, post-processing techniques such as heat treatment and surface finishing are employed to enhance part integrity and smoothness.
These processes can relieve internal stresses and improve the mechanical properties of printed objects.
The Future of Metal 3D Printing
As technology advances, metal 3D printing is poised to overcome its current limitations and redefine manufacturing.
Ongoing research is likely to yield new alloys and materials specifically engineered for additive manufacturing.
These materials could provide novel properties not attainable with traditional metals.
Additionally, automation and artificial intelligence hold the promise of making metal 3D printing more efficient and accessible.
As these technologies are integrated, they might lead to reduced costs and even more sophisticated design capabilities.
In the foreseeable future, as defect suppression technology continues to improve, metal 3D printing could become a cornerstone of industries that demand high-performance materials.
This shift will not only improve production processes but also lead to innovations yet to be imagined.
資料ダウンロード
QCD調達購買管理クラウド「newji」は、調達購買部門で必要なQCD管理全てを備えた、現場特化型兼クラウド型の今世紀最高の購買管理システムとなります。
ユーザー登録
調達購買業務の効率化だけでなく、システムを導入することで、コスト削減や製品・資材のステータス可視化のほか、属人化していた購買情報の共有化による内部不正防止や統制にも役立ちます。
NEWJI DX
製造業に特化したデジタルトランスフォーメーション(DX)の実現を目指す請負開発型のコンサルティングサービスです。AI、iPaaS、および先端の技術を駆使して、製造プロセスの効率化、業務効率化、チームワーク強化、コスト削減、品質向上を実現します。このサービスは、製造業の課題を深く理解し、それに対する最適なデジタルソリューションを提供することで、企業が持続的な成長とイノベーションを達成できるようサポートします。
オンライン講座
製造業、主に購買・調達部門にお勤めの方々に向けた情報を配信しております。
新任の方やベテランの方、管理職を対象とした幅広いコンテンツをご用意しております。
お問い合わせ
コストダウンが利益に直結する術だと理解していても、なかなか前に進めることができない状況。そんな時は、newjiのコストダウン自動化機能で大きく利益貢献しよう!
(Β版非公開)