- お役立ち記事
- Fundamentals of metal 3D printing and application to defect suppression technology for shaped objects
月間76,176名の
製造業ご担当者様が閲覧しています*
*2025年3月31日現在のGoogle Analyticsのデータより
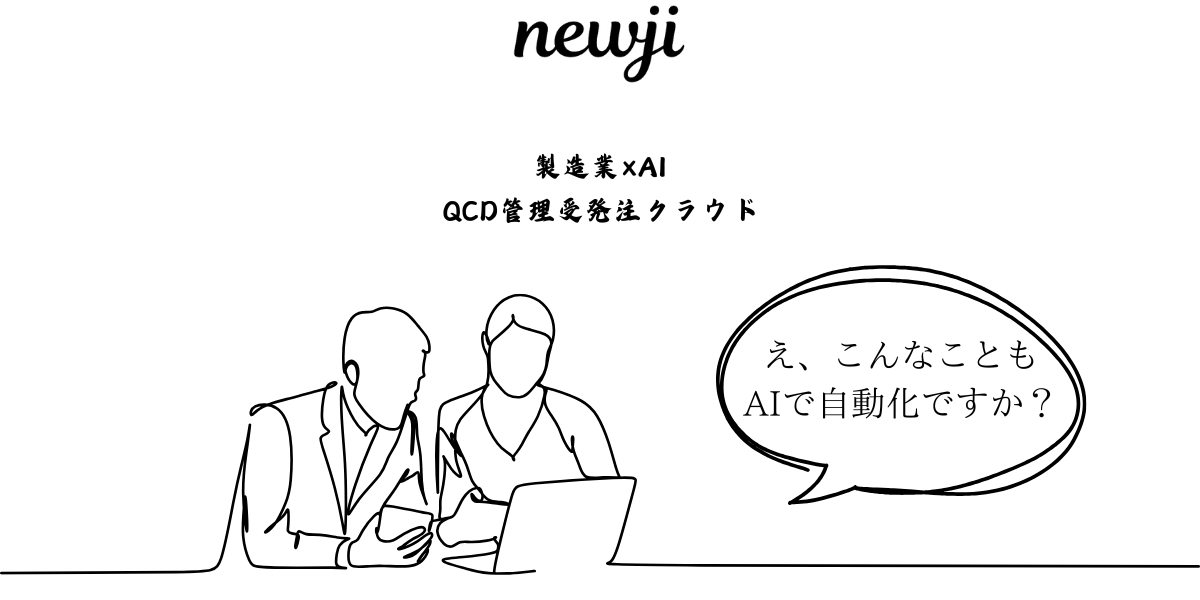
Fundamentals of metal 3D printing and application to defect suppression technology for shaped objects
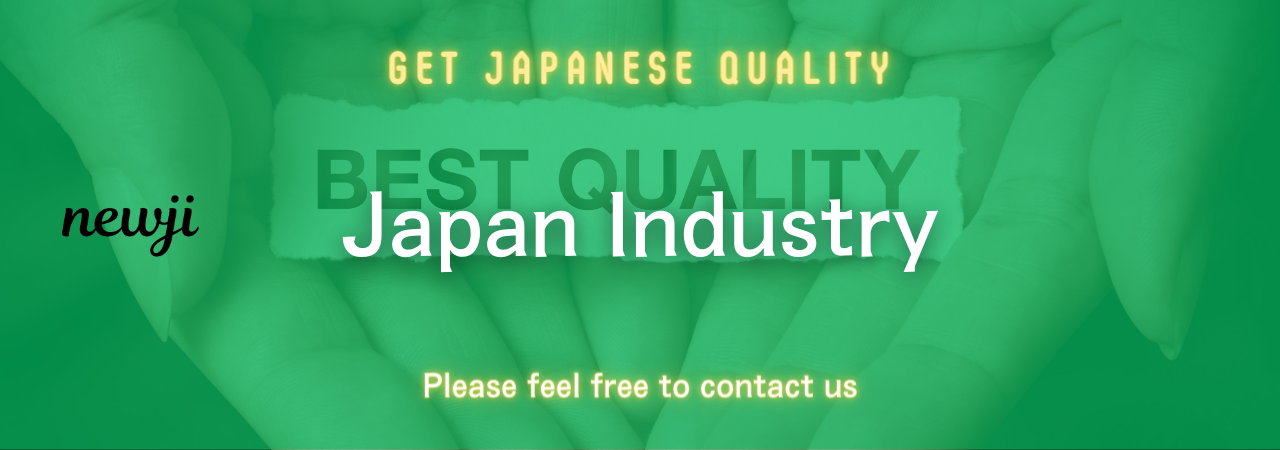
目次
Introduction to Metal 3D Printing
Metal 3D printing, often referred to as additive manufacturing, is a cutting-edge technology that is revolutionizing the way we build and design objects.
Unlike traditional manufacturing methods that involve cutting away material from a solid block, 3D printing constructs objects layer by layer.
This technology has garnered considerable attention in various industries for its ability to create complex geometries, reduce waste, and accelerate the prototyping process.
How Metal 3D Printing Works
Metal 3D printing employs several processes, but the most common involves the use of a high-powered laser or electron beam to selectively melt or fuse metallic powders, layer by layer.
Among the diverse techniques in metal 3D printing, Selective Laser Melting (SLM), Electron Beam Melting (EBM), and Direct Metal Laser Sintering (DMLS) are leading the way.
In SLM, a laser is used to fully melt the powder layers into the desired shape, offering high strength and density of the produced parts.
Similarly, EBM utilizes an electron beam, which can be advantageous for working with titanium and other reactive metals, as it operates in a vacuum environment.
DMLS, on the other hand, only partially melts the powder, sintering it together, which can offer different mechanical properties compared to full melting.
Materials Used in Metal 3D Printing
Metal 3D printing allows for the use of various metals and alloys, expanding the possibilities of this technology across multiple fields.
The most common materials include titanium, stainless steel, aluminum, and cobalt-chrome.
Each material has its own unique properties, such as strength, conductivity, and resistance to heat and corrosion, which dictate its applications.
Titanium, for instance, is lightweight and extremely strong, making it a preferred choice in aerospace and medical industries.
Stainless steel offers good corrosion resistance and is extensively used in automotive and tooling applications.
Aluminum is favored for its lightweight nature and is widely used in aerospace and automotive industries to improve fuel efficiency.
Cobalt-chrome alloys are known for their wear resistance and biocompatibility, making them ideal for medical implants.
Applications of Metal 3D Printing
The flexibility of metal 3D printing opens up a plethora of applications across different sectors.
In the aerospace industry, it is used to manufacture lightweight yet strong components, such as brackets and engine parts, helping reduce overall weight and fuel consumption.
The medical field benefits from this technology through the production of customized implants, prostheses, and surgical tools, tailored to the specific needs of patients.
In the automotive industry, metal 3D printing is employed to create complex parts that are difficult to manufacture with traditional techniques.
This includes lightweight structural components, engine parts, and exhaust systems.
Additionally, metal 3D printing is gaining traction in the tooling sector for the production of molds, dies, and fixtures that need to withstand high pressures and temperatures.
Challenges in Metal 3D Printing
Despite its numerous advantages, metal 3D printing is not without challenges.
One significant hurdle is the presence of defects in the printed parts, such as porosity, warping, and residual stresses, which can compromise the mechanical properties and performance.
These defects often arise from the complex thermal cycles involved in the printing process and the interactions between the laser or electron beam and the metal powders.
The surface finish of 3D printed metal parts is another concern, as it often requires additional post-processing steps to achieve the desired smoothness and tolerances.
Moreover, the cost of metal 3D printing, including the prices of equipment, materials, and energy consumption, remains higher compared to traditional manufacturing techniques, limiting its widespread adoption.
Defect Suppression Technologies
To address the challenges of defects in metal 3D printing, researchers and engineers are actively developing various technologies and strategies.
One approach is optimizing the process parameters, such as laser power, scanning speed, and layer thickness, to reduce thermal gradients and minimize residual stresses.
Advanced simulation and modeling tools are also being utilized to predict the behaviors of powders and thermal interactions during printing, allowing for better control over the process.
Quality control is another critical area, and the integration of in-situ monitoring systems can help detect defects in real time, enabling immediate corrective adjustments.
Post-processing techniques, such as heat treatment and surface finishing, play essential roles in enhancing the mechanical properties and aesthetics of the printed parts.
Some emerging technologies, such as hot isostatic pressing, can eliminate internal porosity and improve density and strength.
The Future of Metal 3D Printing
The future of metal 3D printing holds promising potential, with continuous advancements in materials, process optimization, and defect suppression technologies.
As costs decrease and quality improves, the adoption of metal 3D printing is expected to increase across various industries.
Innovations, such as the development of hybrid manufacturing processes that combine additive and subtractive techniques, are set to expand the capabilities of metal 3D printing.
Furthermore, the ongoing exploration of new metal alloys and composite materials will likely unlock new applications and enhance the performance of 3D-printed components.
Metal 3D printing is positioned to become a cornerstone of modern manufacturing, offering unprecedented design flexibility and efficiency.
With ongoing research and investment, the role of metal 3D printing is set to expand further, transforming industries and reshaping the way we approach manufacturing challenges.
資料ダウンロード
QCD管理受発注クラウド「newji」は、受発注部門で必要なQCD管理全てを備えた、現場特化型兼クラウド型の今世紀最高の受発注管理システムとなります。
ユーザー登録
受発注業務の効率化だけでなく、システムを導入することで、コスト削減や製品・資材のステータス可視化のほか、属人化していた受発注情報の共有化による内部不正防止や統制にも役立ちます。
NEWJI DX
製造業に特化したデジタルトランスフォーメーション(DX)の実現を目指す請負開発型のコンサルティングサービスです。AI、iPaaS、および先端の技術を駆使して、製造プロセスの効率化、業務効率化、チームワーク強化、コスト削減、品質向上を実現します。このサービスは、製造業の課題を深く理解し、それに対する最適なデジタルソリューションを提供することで、企業が持続的な成長とイノベーションを達成できるようサポートします。
製造業ニュース解説
製造業、主に購買・調達部門にお勤めの方々に向けた情報を配信しております。
新任の方やベテランの方、管理職を対象とした幅広いコンテンツをご用意しております。
お問い合わせ
コストダウンが利益に直結する術だと理解していても、なかなか前に進めることができない状況。そんな時は、newjiのコストダウン自動化機能で大きく利益貢献しよう!
(β版非公開)