- お役立ち記事
- Fundamentals of metal fatigue and applications to fatigue design and life prediction
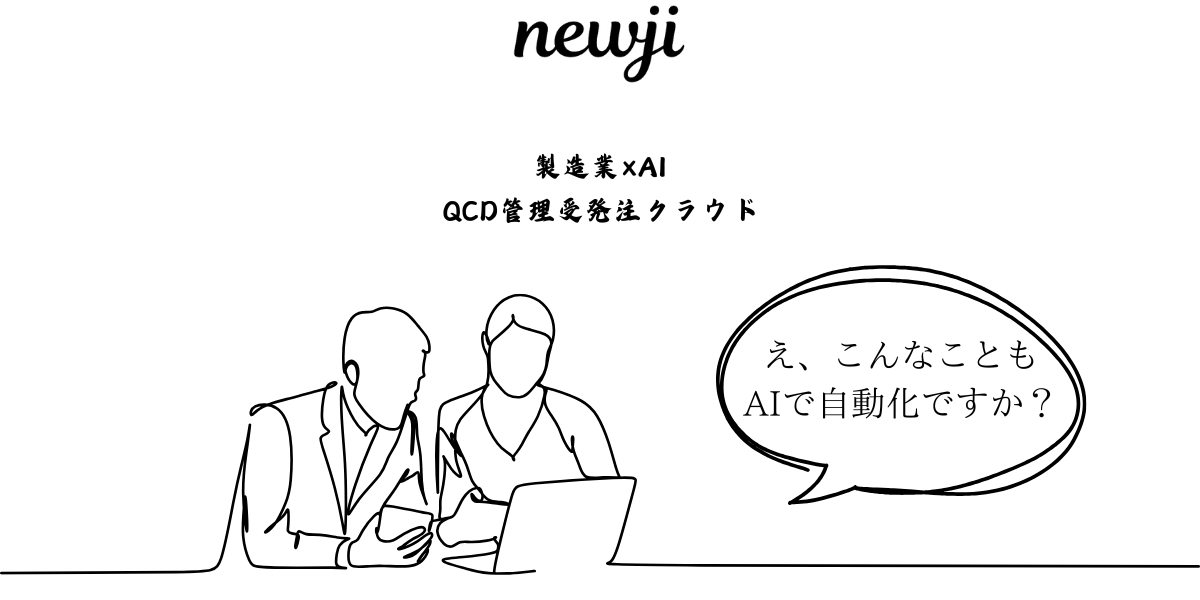
Fundamentals of metal fatigue and applications to fatigue design and life prediction
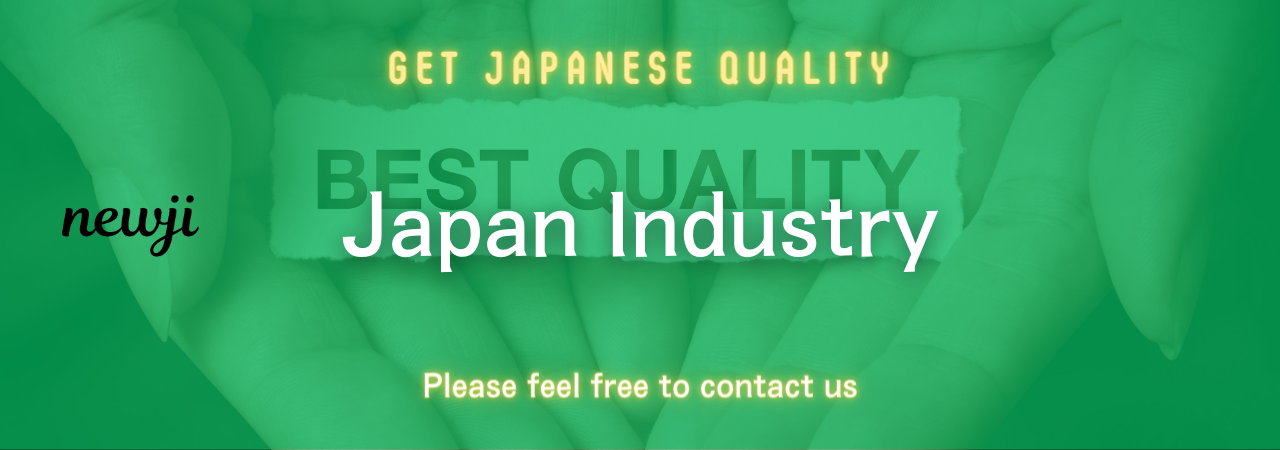
目次
Understanding Metal Fatigue
Metal fatigue refers to the progressive structural damage that occurs when a material is subjected to cyclic loading.
Understanding metal fatigue is critical in the field of engineering as it can lead to catastrophic failures if not properly anticipated and managed.
This phenomenon is particularly important in areas such as aerospace, automotive, and construction, where reliability and safety are paramount.
Metal fatigue is not necessarily intuitive.
While it is easy to understand that a bridge, plane, or car might eventually break under constant stress, metal fatigue involves the accumulation of small, often unseen stresses that eventually lead to failure.
The process begins at the microscopic level with small cracks developing inside the material structure.
Over repeated cycles of stress and strain, these cracks can grow, culminating in failure.
The concept of metal fatigue was first discovered in the 19th century, but it wasn’t until later that researchers developed a full understanding of its complexity.
Engineers now use specific techniques to predict and design against fatigue, effectively improving the durability and safety of products.
The Causes of Metal Fatigue
The causes of metal fatigue are varied but typically include repeated loading and unloading of a component.
This could involve any cyclical action such as vibration, pressure fluctuations, thermal cycling, or mechanical loading.
Every cycle contributes to the growth of microscopic cracks within the material, and the accumulation of these minute damages eventually results in fatigue failure.
Environmental factors also play a role in metal fatigue.
Corrosion can increase the rate of fatigue damage by attacking the surfaces of metals, creating easier paths for cracks to start and grow.
Likewise, temperature variations can provoke additional stress within a metal due to expansion and contraction.
It’s important to consider design factors and material selection in combatting metal fatigue.
Using appropriate materials that have high fatigue limits and designing structures that minimize stress concentrations can significantly increase the lifespan of a component.
An improperly designed product may concentrate stresses at specific points, making them potential failure sites.
Cyclical Loading
Cyclical loading can occur in various ways, most commonly in the form of repeated rolling, bending, or twisting motions.
Even if the stress imposed on a metal component during each cycle is below its tensile strength, fatigue can still set in over time.
It is crucial to understand the nature of the cyclic loads a material will undergo during its service life to predict fatigue life accurately.
Applications of Fatigue Design
Fatigue design is the process of designing against the material fatigue.
It encompasses selecting the right materials, creating suitable designs, and establishing maintenance schedules to ensure that materials won’t prematurely fail under cyclical stresses.
Material Selection
One of the first steps in fatigue design is material selection.
Engineers leverage materials that demonstrate higher fatigue strength for applications prone to cyclic loading.
For instance, alloys with fine-grained microstructures or specific heat treatments can exhibit much better fatigue properties.
Advanced materials, including composites and hybrid metals, are also a part of modern fatigue design strategies.
These materials often combine high fatigue strength with other advantageous properties like lightweight, which is essential in sectors such as aerospace.
Design Considerations
Alongside selecting the right materials, design considerations play a pivotal role in preventing metal fatigue.
Engineers focus on eliminating or managing stress concentration sites—such as notches, holes, or sharp corners—that could serve as initiation points for fatigue cracks.
Applying the principles of redundancy and load distribution in a design are also effective ways to manage stresses.
By spreading the stress over a larger area or incorporating backup systems, engineers can reduce the impact of localized stress, thereby mitigating the risk of fatigue failure.
Predictive Maintenance
Fatigue design also involves calculating the expected life of a component and scheduling maintenance before a failure occurs.
Using historical data and predictive modeling tools, engineers can estimate the lifespan of materials under specific conditions.
Regular inspections for cracks, signs of stress, or unusual wear can identify potential issues before they develop into critical problems.
Life Prediction Techniques
Life prediction techniques are essential tools in fatigue management.
Various methodologies help predict how long a component can withstand repeated stress before fatigue failure occurs.
SN Curves
One common approach involves using S-N (stress-number) curves, which graphically represent the relationship between the cyclic stress a material can endure and the number of cycles it can sustain before failing.
By analyzing the S-N curves, engineers can predict the fatigue life of materials under different loading conditions.
Fracture Mechanics
Fracture mechanics is a more advanced method that analyzes the growth rate of existing cracks.
This approach considers the size and shape of a crack, the material properties, and the loading conditions to calculate the rate at which a crack will propagate.
By understanding how quickly a crack will grow, engineers can predict the remaining life of a component and manage inspections and replacements appropriately.
Finite Element Analysis
Finite Element Analysis (FEA) is a powerful computational tool that allows engineers to simulate the stresses and strains on complex structures.
Through FEA, engineers can identify potential fatigue issues in a design before prototyping and manufacturing, potentially saving time and resources by addressing weaknesses early in the design process.
Understanding metal fatigue and its implications on materials and structures is crucial for engineers and designers involved in creating safe and reliable products.
By employing fatigue design principles and life prediction techniques, the risks associated with this often unseen threat can be effectively managed, ensuring longer-lasting, safer products in industries where failure is not an option.
資料ダウンロード
QCD調達購買管理クラウド「newji」は、調達購買部門で必要なQCD管理全てを備えた、現場特化型兼クラウド型の今世紀最高の購買管理システムとなります。
ユーザー登録
調達購買業務の効率化だけでなく、システムを導入することで、コスト削減や製品・資材のステータス可視化のほか、属人化していた購買情報の共有化による内部不正防止や統制にも役立ちます。
NEWJI DX
製造業に特化したデジタルトランスフォーメーション(DX)の実現を目指す請負開発型のコンサルティングサービスです。AI、iPaaS、および先端の技術を駆使して、製造プロセスの効率化、業務効率化、チームワーク強化、コスト削減、品質向上を実現します。このサービスは、製造業の課題を深く理解し、それに対する最適なデジタルソリューションを提供することで、企業が持続的な成長とイノベーションを達成できるようサポートします。
オンライン講座
製造業、主に購買・調達部門にお勤めの方々に向けた情報を配信しております。
新任の方やベテランの方、管理職を対象とした幅広いコンテンツをご用意しております。
お問い合わせ
コストダウンが利益に直結する術だと理解していても、なかなか前に進めることができない状況。そんな時は、newjiのコストダウン自動化機能で大きく利益貢献しよう!
(Β版非公開)