- お役立ち記事
- Fundamentals of metal fatigue and applications to fracture surface analysis and strength design
月間76,176名の
製造業ご担当者様が閲覧しています*
*2025年3月31日現在のGoogle Analyticsのデータより
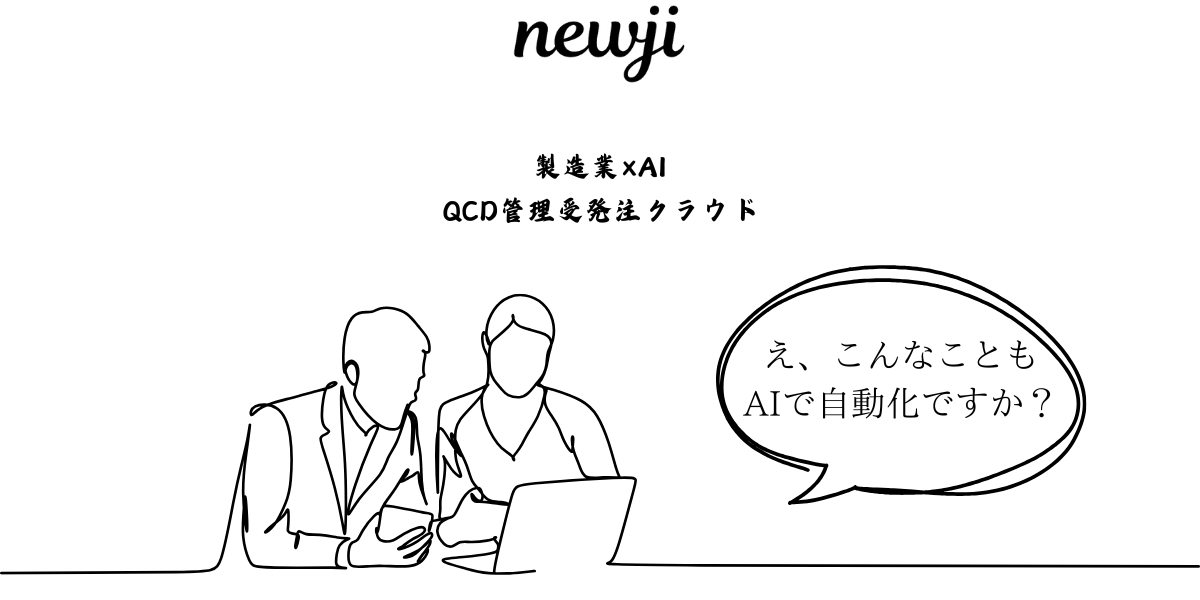
Fundamentals of metal fatigue and applications to fracture surface analysis and strength design
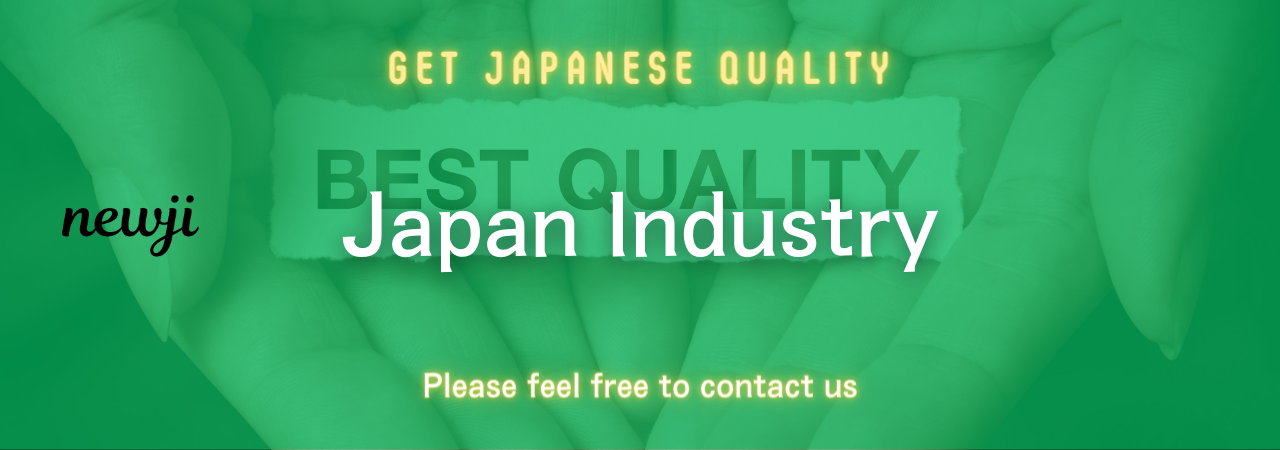
目次
Understanding Metal Fatigue
Metal fatigue is a critical concept that describes how materials undergo weakening or failure after repeated stress or strain over time.
This process is not immediately apparent, as it usually occurs after the metal has experienced numerous cycles of loading and unloading.
Fatigue can lead to cracks and fractures, which may have severe consequences in engineering and structural applications.
Understanding metal fatigue is crucial for ensuring the longevity and safety of metal components in various industries.
Metals are often subjected to cyclic stresses in real-world applications.
These can arise from moving parts, temperature changes, or vibration.
When metal components remain under cycling conditions, they may start to develop tiny cracks that grow over time.
If not addressed, these cracks can lead to catastrophic failures.
The study of metal fatigue involves investigating how materials withstand cyclical loading and predicting the lifespan before significant damage or failure occurs.
Researchers employ various testing methods, such as rotating-bend and axial fatigue tests, to simulate the conditions that metals might experience in practical applications.
These tests help determine the fatigue limit or the stress level below which a metal can endure an infinite number of cycles without failing.
Fracture Surface Analysis
Fracture surface analysis plays a vital role in evaluating the causes and processes involved in metal fatigue.
When a metal fracture occurs, the surface provides essential information regarding the history and progression of the crack.
Analyzing fracture surfaces can reveal whether a failure was due to metal fatigue, overloading, or another factor.
Expert analysis often involves examining the microscopic features present on the fracture surface.
One common feature is the presence of striations, which are microscopic lines that indicate cyclic loading.
By analyzing striations, engineers and scientists can estimate the direction and number of cycles that contributed to crack growth.
Another important aspect in fracture surface analysis is identifying the origin of the crack.
The point where the fracture began is often recognizable by a smooth, polished area known as the “origin” or “nucleus” of failure.
From this point, crack propagation is generally more discernible, showcasing patterns that depict how the failure spread across the material.
Tools Used in Fracture Surface Analysis
There are several tools and techniques used in fracture surface analysis.
Scanning electron microscopy (SEM) is one such tool, which allows researchers to observe microscopic details.
SEM provides high-resolution images highlighting the minute characteristics of fracture surfaces.
Energy-dispersive X-ray spectroscopy (EDX) is another technique employed to determine the elemental composition of materials.
This information can help identify contaminants or inclusions that may have contributed to metal fatigue.
Additionally, optical microscopy remains a prevalent method for initial fracture analysis.
While not as detailed as SEM, optical microscopy affords a quick and cost-effective means to survey fracture surfaces.
Strength Design Considerations
Strength design in engineering involves creating components that can withstand expected stress levels and conditions throughout their service life.
Considering metal fatigue during the design process is essential to prevent unwanted failures.
Understanding the factors that influence metal fatigue can lead to more effective strength design strategies.
One fundamental element in strength design is choosing appropriate materials.
Different metals have varying resistance to fatigue depending on their composition, treatment, and microstructure.
Selecting alloys or materials with higher fatigue limits can enhance the durability of the components.
Design Techniques to Combat Metal Fatigue
Designers employ several techniques to reduce the risk of metal fatigue, enhancing the lifespan of structures under cyclic stress.
One common technique is to incorporate fillets or rounded edges rather than sharp corners.
Sharp corners act as stress concentrators that can initiate cracks more easily.
Another strategy is surface treatment, such as shot peening or surface hardening, which improve fatigue resistance.
These treatments introduce compressive residual stresses on the surface, reducing the likelihood of crack initiation and propagation.
Fatigue analysis tools and simulations help designers predict how components will perform under cyclic loading conditions.
Using finite element analysis (FEA), engineers can model the stress distribution and identify potential failure points within the design.
This proactive approach allows for adjustments before manufacturing begins.
The Importance of Proper Maintenance
Once a metal component is in use, maintenance practices become vital to ensure structural integrity and mitigate metal fatigue.
Regular inspections can identify early signs of fatigue, such as small cracks or surface irregularities that may otherwise go unnoticed.
Implementing maintenance schedules and inspections based on predicted fatigue life can significantly extend the operational lifespan of metal components.
By identifying potential issues early, costly and dangerous failures can often be prevented.
Monitoring Techniques
Advanced monitoring techniques, such as non-destructive testing (NDT), play a crucial role in maintaining safety.
Ultrasonic testing and radiography are commonly used NDT methods that can detect internal cracks without causing further damage to the component.
Acoustic emission monitoring is another technique used to observe in-service components.
By capturing the sound waves emitted by crack growth, engineers can detect and address issues before they become critical.
Conclusion
The fundamentals of metal fatigue inform a broad spectrum of practices in fracture surface analysis and strength design.
Recognizing and analyzing fatigue can significantly enhance the safety and longevity of metal components and structures.
Combining the right materials, design strategies, and maintenance practices ensures components achieve their maximum potential without premature failure.
Understanding metal fatigue and its implications helps engineers produce designs that withstand the test of time while maintaining safety and efficiency across various sectors.
Through continuous research and analysis, advancements in these practices will contribute to improved performance and reliability of metals in engineering applications.
資料ダウンロード
QCD管理受発注クラウド「newji」は、受発注部門で必要なQCD管理全てを備えた、現場特化型兼クラウド型の今世紀最高の受発注管理システムとなります。
ユーザー登録
受発注業務の効率化だけでなく、システムを導入することで、コスト削減や製品・資材のステータス可視化のほか、属人化していた受発注情報の共有化による内部不正防止や統制にも役立ちます。
NEWJI DX
製造業に特化したデジタルトランスフォーメーション(DX)の実現を目指す請負開発型のコンサルティングサービスです。AI、iPaaS、および先端の技術を駆使して、製造プロセスの効率化、業務効率化、チームワーク強化、コスト削減、品質向上を実現します。このサービスは、製造業の課題を深く理解し、それに対する最適なデジタルソリューションを提供することで、企業が持続的な成長とイノベーションを達成できるようサポートします。
製造業ニュース解説
製造業、主に購買・調達部門にお勤めの方々に向けた情報を配信しております。
新任の方やベテランの方、管理職を対象とした幅広いコンテンツをご用意しております。
お問い合わせ
コストダウンが利益に直結する術だと理解していても、なかなか前に進めることができない状況。そんな時は、newjiのコストダウン自動化機能で大きく利益貢献しよう!
(β版非公開)