- お役立ち記事
- Fundamentals of metal fatigue and design guidelines
Fundamentals of metal fatigue and design guidelines
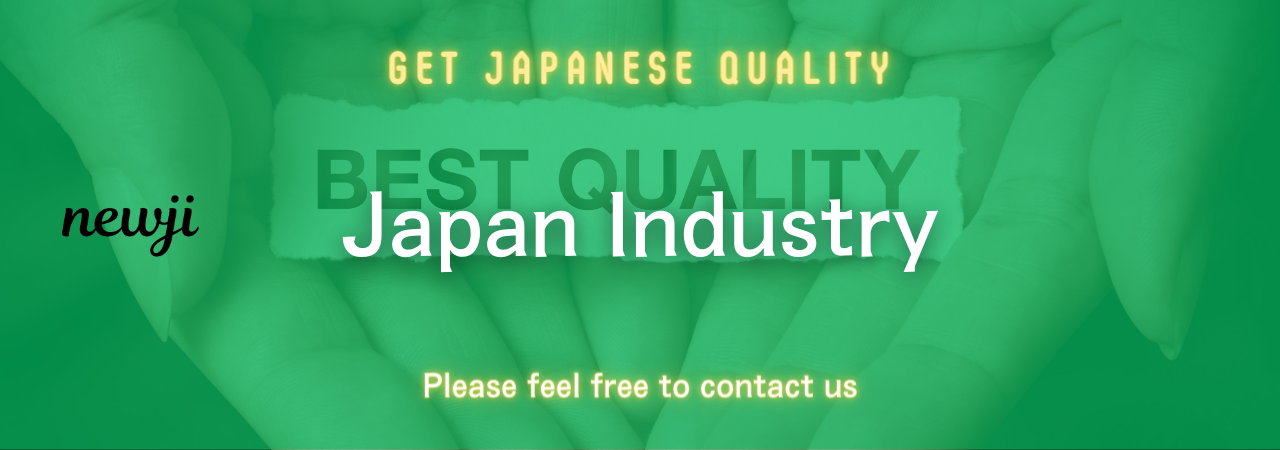
目次
Understanding Metal Fatigue
Metal fatigue is an important concept in engineering, particularly when designing structures and machinery that are subject to repetitive stress and strain.
It occurs when a metal or an alloy undergoes repeated cyclic loading, which leads to the gradual formation and growth of cracks.
Understanding metal fatigue is crucial for ensuring the longevity and safety of various applications, from bridges and airplanes to mechanical components and automotive parts.
What Causes Metal Fatigue?
Metal fatigue is primarily caused by the repeated application of stress, which can be far lower than the metal’s ultimate tensile strength.
When objects are continuously stressed, even under minimal pressure, microscopic cracks can form within the material.
These cracks expand over time, eventually leading to catastrophic failure if not properly addressed.
Several factors can contribute to metal fatigue, including:
1. **Load Cycles:** The number and frequency of stress cycles.
High-frequency repeated loads can accelerate fatigue.
2. **Stress Range:** The variation between the stress levels during loading and unloading.
Higher stress ranges hasten fatigue development.
3. **Material Properties:** Different metals and alloys possess varying resistances to fatigue.
Properties such as hardness, ductility, and tensile strength impact fatigue resistance.
4. **Environmental Factors:** Exposure to corrosive environments can exacerbate fatigue by weakening the structural integrity of the material.
5. **Surface Conditions:** Surface imperfections, such as scratches or notches, can serve as stress concentrators that intensify fatigue effects.
Recognizing the Signs of Metal Fatigue
Detecting metal fatigue early plays a significant role in preemptive maintenance and safety assurance.
Common signs of impending failure include:
– **Visible Cracks:** These usually occur on the surface and are often the most overt indication.
– **Deformations:** Bending or warping that does not go away, even after the removal of stress.
– **Unusual Noises:** Such as creaking or popping sounds, often occurring just before failure.
Early identification allows for timely intervention, preventing dangerous breakdowns.
Design Guidelines to Mitigate Metal Fatigue
Designers and engineers take several strategic approaches to mitigate the risks associated with metal fatigue.
Understanding and incorporating these guidelines into the design phases can lead to safer, more durable metal structures and components.
Selecting Appropriate Materials
Choosing the right material is a foundational step in combating metal fatigue.
The ideal material should possess a combination of strength and ductility to withstand daily wear and tear.
Materials known for their fatigue resistance include:
– **Stainless Steel:** Offers a commendable balance between strength and flexibility.
– **Titanium Alloys:** Known for their high strength-to-weight ratio and exceptional corrosion resistance.
– **Aluminum Alloys:** Lightweight yet strong, great for applications where weight is a concern.
The specific choice of material will depend on the particular application and environmental conditions expected.
Engineering the Right Design
Optimizing the design can significantly enhance a structure’s ability to resist fatigue.
Key design principles include:
– **Avoiding Stress Concentrators:** Design components with smooth transitions and rounded edges to reduce the concentration of stress.
– **Load Distribution:** Use design techniques that distribute loads evenly across the structure rather than concentrating them in one area.
– **Proper Joint and Connection Design:** Ensure joints and connections are strong and resilient enough to handle stresses. Bolted and riveted joints should be designed with fatigue strength in mind.
Regular Maintenance Checks
Implementing a consistent schedule of inspections is crucial for early fault detection and extending the lifespan of metal structures.
Routine checks should focus on identifying early signs of wear or distress, like cracks or other deformities.
– **Visual Inspections:** Simple but effective, carried out regularly to spot obvious damage.
– **Non-Destructive Testing (NDT):** Techniques such as ultrasonic testing or radiography can detect internal imperfections before they reach the surface.
– **Load Testing:** Simulate operational conditions to ensure components can withstand expected strains.
Effective Use of Coatings and Treatments
Another method to combat fatigue is by applying protective coatings or treatments, which can help shield metals from external variables like moisture, chemicals, or other environmental hazards.
– **Anodizing:** Often used for aluminum, creating a protective oxide layer to resist corrosion and wear.
– **Case Hardening:** Involves hardening the surface while maintaining a softer, ductile core, ideal for components subjected to high wear.
– **Painting or Plating:** Simple coatings that provide an additional barrier against environmental elements.
These protective measures can significantly reduce the risk of fatigue by improving surface conditions and preventing early initiation of cracks.
The Role of Fatigue Testing in Design
Fatigue testing is a vital phase in product development, providing critical data on how materials and designs will behave under repeated stress.
Conducting rigorous fatigue tests allows designers to better predict when and how failures might occur, leading to improved safety and performance in real-world applications.
By embracing these guidelines and continually advancing testing methodologies, engineers can effectively manage the challenges posed by metal fatigue.
These strategies ensure the structural integrity and longevity of metal components, averting potential risks and safeguarding both human lives and economic investments.
資料ダウンロード
QCD調達購買管理クラウド「newji」は、調達購買部門で必要なQCD管理全てを備えた、現場特化型兼クラウド型の今世紀最高の購買管理システムとなります。
ユーザー登録
調達購買業務の効率化だけでなく、システムを導入することで、コスト削減や製品・資材のステータス可視化のほか、属人化していた購買情報の共有化による内部不正防止や統制にも役立ちます。
NEWJI DX
製造業に特化したデジタルトランスフォーメーション(DX)の実現を目指す請負開発型のコンサルティングサービスです。AI、iPaaS、および先端の技術を駆使して、製造プロセスの効率化、業務効率化、チームワーク強化、コスト削減、品質向上を実現します。このサービスは、製造業の課題を深く理解し、それに対する最適なデジタルソリューションを提供することで、企業が持続的な成長とイノベーションを達成できるようサポートします。
オンライン講座
製造業、主に購買・調達部門にお勤めの方々に向けた情報を配信しております。
新任の方やベテランの方、管理職を対象とした幅広いコンテンツをご用意しております。
お問い合わせ
コストダウンが利益に直結する術だと理解していても、なかなか前に進めることができない状況。そんな時は、newjiのコストダウン自動化機能で大きく利益貢献しよう!
(Β版非公開)