- お役立ち記事
- Fundamentals of metal fatigue and its application to fatigue life prediction and fatigue-resistant design using FEM and its key points
Fundamentals of metal fatigue and its application to fatigue life prediction and fatigue-resistant design using FEM and its key points
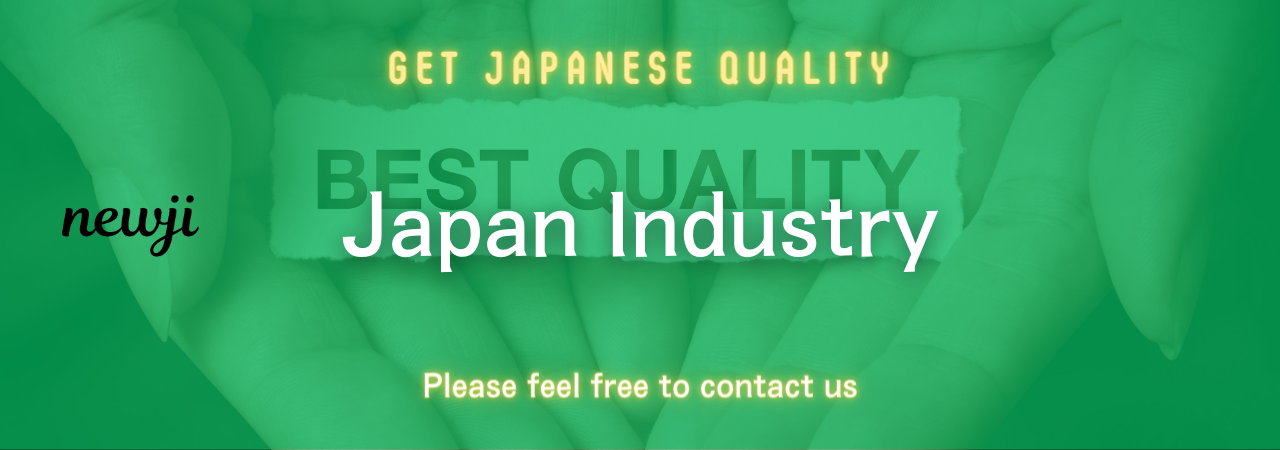
目次
Understanding Metal Fatigue
Metal fatigue is a critical consideration in the design and durability of materials and structures.
It refers to the progressive and localized structural damage that occurs when a material is subjected to cyclic loading.
This damage often happens at stress levels below the material’s yield strength.
Over time, repeated loading can lead to the initiation and propagation of cracks, potentially resulting in catastrophic failure.
Metal fatigue is particularly significant in industries such as aerospace, automotive, and construction, where safety and reliability are paramount.
Understanding the fundamentals of metal fatigue is crucial for engineers and designers to predict fatigue life accurately and develop fatigue-resistant designs.
Causes and Mechanisms of Metal Fatigue
Metal fatigue occurs due to continuous cyclic stresses that materials experience during their service life.
These stresses can arise from mechanical loads, thermal fluctuations, or even vibratory motion.
The key factors that influence metal fatigue include the magnitude of stress, stress concentration, and the nature of the material itself.
The process of metal fatigue can be broken down into three stages:
Stage 1: Crack Initiation
During this initial phase, microscopic cracks form at points of high-stress concentration.
These points are often found at material discontinuities such as sharp corners, notches, or welds.
The repeated stress cycles cause these tiny cracks to initiate and grow, albeit slowly, into larger cracks over time.
Stage 2: Crack Propagation
Once a crack has initiated, it enters the propagation stage.
In this phase, the crack starts to grow steadily under the continued influence of cyclic loading.
It extends with each load cycle, gradually weakening the structure until it becomes critical.
Crack propagation is influenced by factors such as environmental conditions, material properties, and loading frequency.
Stage 3: Final Fracture
The final fracture stage is the culmination of the crack propagation phase.
At this point, the crack has grown large enough to cause a sudden failure of the material or structure.
The fracture typically occurs within a few load cycles after reaching a critical crack size.
This catastrophic failure can have severe consequences, especially in sectors where safety is a primary concern.
Fatigue Life Prediction Techniques
Predicting the fatigue life of a material or structure is essential for ensuring its safety and reliability.
Several established methods are used to estimate fatigue life, with the Finite Element Method (FEM) being one of the most advanced techniques.
Finite Element Method (FEM)
The Finite Element Method is a numerical technique used for solving complex engineering problems.
It involves dividing a structure into smaller, simpler parts called finite elements.
These elements are then analyzed to estimate the stresses and strains experienced by the material.
FEM is particularly effective in fatigue life prediction because it allows for detailed analysis of stress concentrations and loading conditions.
By simulating the cyclic loading conditions a structure will face in real-world scenarios, engineers can predict the initiation and growth of cracks, thereby estimating the fatigue life accurately.
Stress-Life (S-N) Approach
The Stress-Life method, also known as the S-N approach, is one of the oldest techniques for predicting fatigue life.
It involves constructing an S-N curve, which plots the number of cycles to failure (N) against the stress amplitude (S).
This approach is particularly useful for high-cycle fatigue scenarios where the material remains predominantly elastic.
The S-N curve is often derived from experimental data and provides a reliable basis for predicting the fatigue life of a component under specific conditions.
Strain-Life (ε-N) Approach
The Strain-Life method, or ε-N approach, is used for predicting fatigue life in situations where plastic deformation occurs.
This method focuses on the strain experienced by the material rather than just the stress.
The ε-N curve is generated by testing samples under controlled conditions to determine the number of cycles to failure at different strain amplitudes.
This technique is especially valuable for low-cycle fatigue applications where the material undergoes significant plasticity.
Designing Fatigue-Resistant Structures
To ensure the longevity and safety of components subjected to cyclic loading, engineers must incorporate fatigue-resistant design principles.
Material Selection
Choosing the right material is fundamental to creating fatigue-resistant structures.
Materials with high fatigue strength, such as certain alloys and composites, are preferred for applications that endure cyclic stresses.
Additionally, treatments like surface hardening or shot peening can enhance a material’s fatigue resistance.
Geometry and Stress Concentration
Designing components with smooth transitions and avoiding sharp corners can minimize stress concentration areas, reducing the likelihood of crack initiation.
Engineers often use fillets and chamfers to distribute stress more evenly across a structure.
Load Management
Controlling the loads that a structure experiences can significantly impact its fatigue life.
By ensuring that components operate within safe stress levels, fatigue damage can be minimized.
Regular maintenance and inspection can also help identify and address potential issues before they lead to failure.
Conclusion
Understanding the fundamentals of metal fatigue and applying effective fatigue life prediction methods are essential for designing safe and reliable components.
By utilizing techniques like the Finite Element Method and implementing fatigue-resistant design principles, engineers can enhance the durability of structures.
As industries continue to evolve, the importance of addressing metal fatigue cannot be overstated.
Through proper understanding and innovative design, we can ensure that the structures and materials we rely on remain safe and dependable throughout their service life.
資料ダウンロード
QCD調達購買管理クラウド「newji」は、調達購買部門で必要なQCD管理全てを備えた、現場特化型兼クラウド型の今世紀最高の購買管理システムとなります。
ユーザー登録
調達購買業務の効率化だけでなく、システムを導入することで、コスト削減や製品・資材のステータス可視化のほか、属人化していた購買情報の共有化による内部不正防止や統制にも役立ちます。
NEWJI DX
製造業に特化したデジタルトランスフォーメーション(DX)の実現を目指す請負開発型のコンサルティングサービスです。AI、iPaaS、および先端の技術を駆使して、製造プロセスの効率化、業務効率化、チームワーク強化、コスト削減、品質向上を実現します。このサービスは、製造業の課題を深く理解し、それに対する最適なデジタルソリューションを提供することで、企業が持続的な成長とイノベーションを達成できるようサポートします。
オンライン講座
製造業、主に購買・調達部門にお勤めの方々に向けた情報を配信しております。
新任の方やベテランの方、管理職を対象とした幅広いコンテンツをご用意しております。
お問い合わせ
コストダウンが利益に直結する術だと理解していても、なかなか前に進めることができない状況。そんな時は、newjiのコストダウン自動化機能で大きく利益貢献しよう!
(Β版非公開)