- お役立ち記事
- Fundamentals of metal fatigue and techniques to prevent fatigue fractures
Fundamentals of metal fatigue and techniques to prevent fatigue fractures
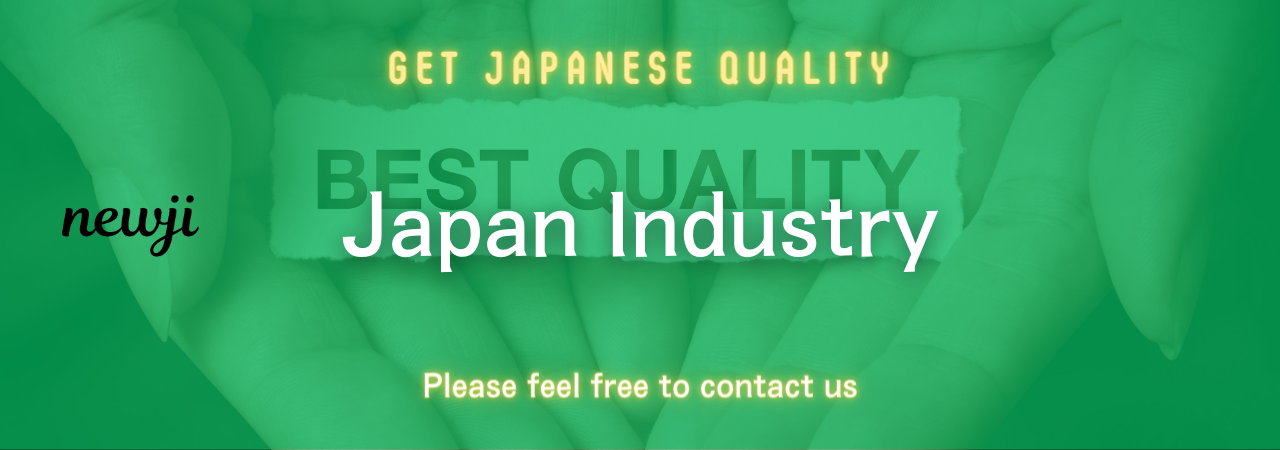
目次
Understanding Metal Fatigue
Metal fatigue is a critical phenomenon that occurs when a material undergoes repeated stress cycles, leading to the initiation and growth of cracks which can ultimately result in fractures.
This is a progressive and localized structural damage that metals experience when subjected to cyclic loading.
The nature of metal fatigue makes it highly unpredictable, which makes it both a fascinating and challenging aspect of material science.
Generally, metal fatigue is characterized by phases that consist of crack initiation, crack propagation, and final sudden fracture.
Understanding the basic principles of metal fatigue is essential for engineers and designers who seek to extend the lifespan of metal components and prevent catastrophic failures.
Even though metal fatigue was first recognized in the 19th century, it remains a crucial area of study due to its relevance across multiple industries such as automotive, aerospace, and civil infrastructure.
Stages of Metal Fatigue
Crack Initiation
The first stage of metal fatigue is crack initiation.
This phase is where microscopic cracks begin to form in the surface or subsurface of the metal.
Factors such as surface roughness, material defects, and environmental conditions can significantly influence the initiation of cracks.
Typically, areas with stress concentrations, such as sharp corners or notches, are more susceptible to crack initiation.
This phase is critical as it sets the stage for the subsequent growth of cracks during fatigue loading.
Crack Propagation
Once a crack has formed, it enters the crack propagation stage.
In this phase, the existing crack begins to grow incrementally with each loading cycle.
The rate of crack propagation is influenced by several factors, including the magnitude of cyclic stresses, material properties, and the environment.
During this stage, cracks tend to grow perpendicularly to the directions of maximum tensile stress.
As the crack grows, it reduces the load-bearing capacity of the metal, making the material increasingly vulnerable to failure.
Final Sudden Fracture
The final stage of metal fatigue is the sudden fracture.
After the crack has reached a critical size, the remaining material can no longer sustain the applied loads, leading to a rapid failure.
This sudden fracture can occur with little to no warning, which is why metal fatigue is often seen as particularly dangerous.
The time from crack initiation to fracture can vary significantly, depending on the stress levels and the material’s resistance to fatigue.
Factors Affecting Metal Fatigue
Material Properties
Different materials have varying resistance to fatigue.
For instance, ferrous metals like steel generally have high fatigue strength compared to non-ferrous metals.
Alloying elements and heat treatment processes can also influence a metal’s fatigue properties.
Understanding the material’s properties is essential for predicting its fatigue behavior and selecting the appropriate material for specific applications.
Surface Condition
The surface condition of a metal component plays a significant role in metal fatigue.
Rough or damaged surfaces can act as initiation sites for cracks.
Processes such as polishing, coating, and shot peening can improve surface conditions, thus enhancing fatigue resistance.
Maintaining a smooth and defect-free surface is critical in preventing premature fatigue failures.
Loading Conditions
Loading conditions, including the magnitude, frequency, and direction of applied loads, directly affect metal fatigue.
Higher cyclic stresses lead to faster crack initiation and growth.
Additionally, varying load directions can introduce complex stress states, promoting fatigue damage.
Design considerations must account for various loading scenarios to optimize fatigue performance.
Preventive Techniques for Metal Fatigue
Design Optimization
Designing against fatigue involves minimizing stress concentrations and optimizing the geometry of components.
This can be achieved through techniques such as filleting sharp corners, avoiding abrupt changes in cross-sections, and using uniform load distributions.
Finite element analysis (FEA) is commonly used in the design phase to simulate stress distribution and highlight potential areas of fatigue concern.
Material Selection
Selecting the right material is crucial in preventing fatigue failures.
Materials with high fatigue strength and resistance to crack growth are preferred for applications subject to cyclic loading.
Engineers must carefully evaluate the material properties, environmental conditions, and cost factors to make informed material choices.
Surface Treatments
Surface treatments like shot peening, carburizing, and nitriding can improve fatigue resistance.
These processes enhance surface hardness and introduce compressive residual stresses, which counteract the tensile stresses that drive crack initiation.
Regular maintenance and inspection of surfaces are also vital in detecting and addressing early signs of fatigue.
Load Management
Controlling the magnitude and frequency of loads experienced by a component can significantly reduce fatigue risks.
Implementing load limiters, shock absorbers, and isolators can help reduce excessive loads and damping vibrations.
Proper maintenance schedules ensure that components are not exposed to conditions beyond their design limits.
The Future of Metal Fatigue Research
As technology advances, new methods and materials continue to emerge in the field of fatigue research.
Innovative techniques such as advanced monitoring systems, smart materials, and predictive maintenance strategies offer promising solutions to combat metal fatigue.
Developing more accurate predictive models and simulation tools will further enhance our ability to prevent fatigue failures.
The knowledge gained from ongoing research will continue to drive improvements in the reliability and safety of critical structures, reducing the risks associated with metal fatigue.
By investing in this area, industries can minimize downtime, extend the lifespan of components, and ensure the safety and efficiency of engineering systems.
In conclusion, understanding the fundamentals of metal fatigue and employing preventive techniques are essential for maintaining the integrity of metal components subjected to cyclic loading.
By addressing the challenges associated with fatigue, industries can enhance durability and performance, safeguarding against unexpected failures.
資料ダウンロード
QCD調達購買管理クラウド「newji」は、調達購買部門で必要なQCD管理全てを備えた、現場特化型兼クラウド型の今世紀最高の購買管理システムとなります。
ユーザー登録
調達購買業務の効率化だけでなく、システムを導入することで、コスト削減や製品・資材のステータス可視化のほか、属人化していた購買情報の共有化による内部不正防止や統制にも役立ちます。
NEWJI DX
製造業に特化したデジタルトランスフォーメーション(DX)の実現を目指す請負開発型のコンサルティングサービスです。AI、iPaaS、および先端の技術を駆使して、製造プロセスの効率化、業務効率化、チームワーク強化、コスト削減、品質向上を実現します。このサービスは、製造業の課題を深く理解し、それに対する最適なデジタルソリューションを提供することで、企業が持続的な成長とイノベーションを達成できるようサポートします。
オンライン講座
製造業、主に購買・調達部門にお勤めの方々に向けた情報を配信しております。
新任の方やベテランの方、管理職を対象とした幅広いコンテンツをご用意しております。
お問い合わせ
コストダウンが利益に直結する術だと理解していても、なかなか前に進めることができない状況。そんな時は、newjiのコストダウン自動化機能で大きく利益貢献しよう!
(Β版非公開)