- お役立ち記事
- Fundamentals of metal fatigue, fatigue design methods, and applications to fatigue life prediction
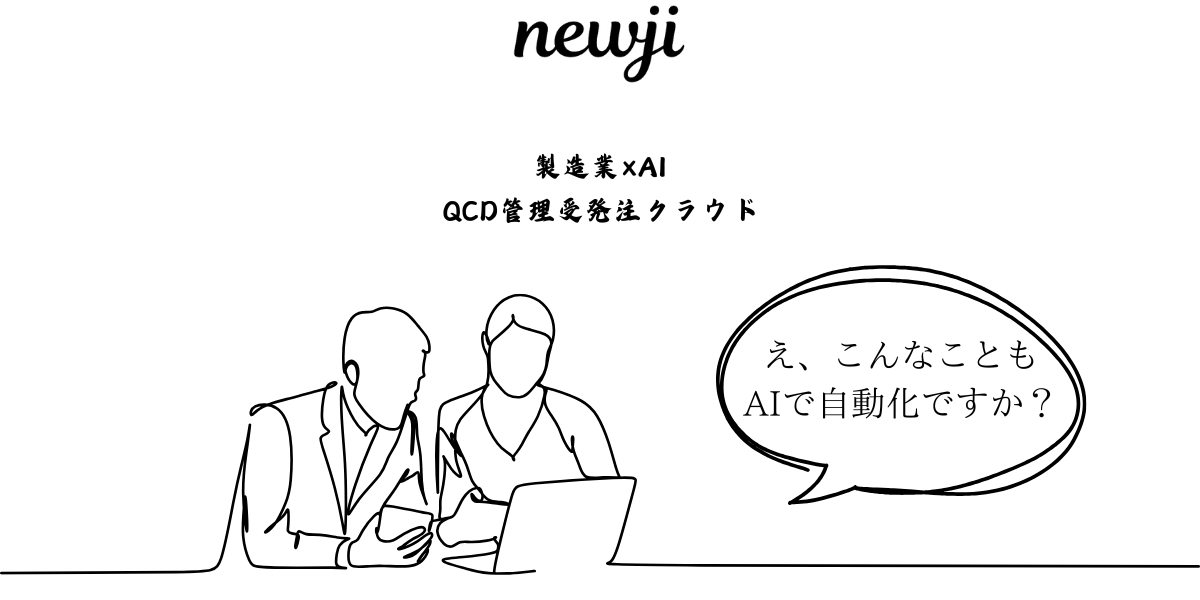
Fundamentals of metal fatigue, fatigue design methods, and applications to fatigue life prediction
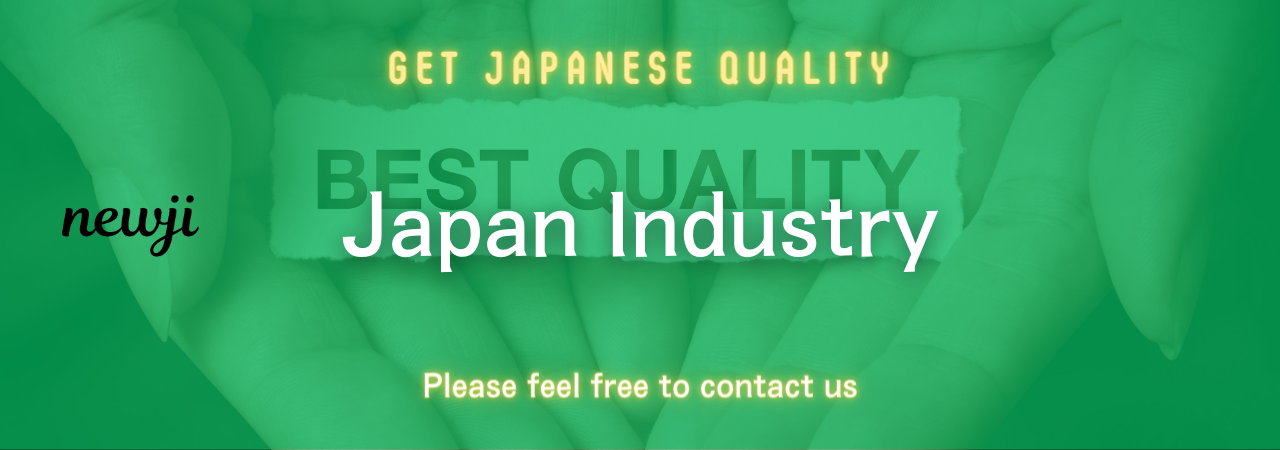
Metal fatigue is an essential concept in engineering and materials science, as it pertains to the weakening of materials subjected to cyclic loads over time.
Understanding the fundamentals of metal fatigue, fatigue design methods, and applications to predict fatigue life is crucial for engineers and designers to ensure the safety and longevity of structures and components.
目次
What is Metal Fatigue?
Metal fatigue occurs when a material is subjected to repeated cycles of stress or strain, leading to the initiation and growth of cracks.
These cracks can eventually result in catastrophic failure if not addressed.
Unlike a single overstress event that can cause immediate failure, fatigue failure occurs over time, often without any visible signs before the final fracture.
Several factors influence metal fatigue, including the amplitude of the stress cycle, the mean stress, the material’s properties, the environment, and the presence of stress concentrators like notches or holes.
Understanding these factors is crucial for predicting and preventing fatigue failures.
Stages of Metal Fatigue
Metal fatigue progresses through three primary stages:
1. Crack Initiation
During this initial stage, micro-cracks begin to form at stress concentrations such as surface imperfections, grain boundaries, or inclusions within the metal.
The cyclic loading contributes to the formation of these cracks, often starting at microscopic defects.
2. Crack Propagation
Once a crack has initiated, it begins to propagate with each additional cycle of loading.
The crack growth rate depends on the stress intensity factor, which itself depends on crack size, applied stress, and material properties.
This stage can represent the majority of the fatigue life for many materials.
3. Final Fracture
The final stage occurs when the crack has grown to a critical size.
At this point, the remaining cross-section of the material cannot support the applied load, leading to sudden and complete failure.
This stage usually happens swiftly and can result in catastrophic consequences if not predicted or detected in advance.
Fatigue Design Methods
To combat the effects of metal fatigue in engineering, various design methods are employed.
1. Safe-Life Design
The safe-life design approach involves designing components to withstand a predetermined number of cycles without failure.
This method requires extensive testing and analysis to establish the expected fatigue life and incorporates safety factors to account for uncertainties.
It’s generally applied to non-redundant components where failure cannot be tolerated.
2. Fail-Safe Design
Fail-safe design anticipates possible failure scenarios and ensures that such failures do not lead to catastrophic consequences.
This approach incorporates redundancy, allowing remaining structural elements to carry the load if one fails.
As a result, the system can maintain functionality until repairs or replacements are made.
3. Damage-Tolerant Design
This approach focuses on the ability of a structure to endure damage without catastrophic failure through regular inspections and maintenance.
Damage-tolerant design assumes that cracks or damage will occur and uses inspection techniques to monitor the size and growth of these defects.
These inspections are scheduled based on the predicted crack growth rates to ensure timely detection and intervention.
Applications to Fatigue Life Prediction
Fatigue life prediction is a crucial aspect of component and structure design, ensuring longevity and safety.
1. Stress-Life (S-N) Approach
The S-N approach involves plotting material stress (S) against the number of cycles to failure (N) to create an S-N curve.
This curve helps predict the fatigue life of a material under a specific stress amplitude.
Test data can develop S-N curves for different materials, with the endurance limit marking the stress level below which the material can withstand infinite cycles without failure.
2. Strain-Life (ε-N) Approach
For situations with significant plastic deformations, the strain-life approach is more appropriate.
This method focuses on the total strain experienced by a material, accounting for both elastic and plastic strain components.
The ε-N curve, like the S-N curve, plots strain against the number of cycles to failure, offering insights into low-cycle fatigue scenarios.
3. Fracture Mechanics Approach
Fracture mechanics provides a quantitative understanding of crack growth rates and allows for predicting the remaining life of a component with an existing crack.
The crack growth rate is modeled using parameters such as stress intensity factors and crack length, which are influenced by material properties and loading conditions.
This approach is particularly useful for damage-tolerant design, enabling the scheduling of inspections and maintenance activities based on crack growth predictions.
Conclusion
Understanding the fundamentals of metal fatigue, fatigue design methods, and applications for fatigue life prediction is vital in designing safe and reliable components and structures.
By taking into account factors such as material properties, loading conditions, and environmental influences, engineers can better anticipate fatigue-related failures and implement effective strategies to mitigate them.
Adopting suitable design methodologies ensures the safety of components and extends their service life, reducing maintenance costs and minimizing the risk of unexpected failures.
資料ダウンロード
QCD調達購買管理クラウド「newji」は、調達購買部門で必要なQCD管理全てを備えた、現場特化型兼クラウド型の今世紀最高の購買管理システムとなります。
ユーザー登録
調達購買業務の効率化だけでなく、システムを導入することで、コスト削減や製品・資材のステータス可視化のほか、属人化していた購買情報の共有化による内部不正防止や統制にも役立ちます。
NEWJI DX
製造業に特化したデジタルトランスフォーメーション(DX)の実現を目指す請負開発型のコンサルティングサービスです。AI、iPaaS、および先端の技術を駆使して、製造プロセスの効率化、業務効率化、チームワーク強化、コスト削減、品質向上を実現します。このサービスは、製造業の課題を深く理解し、それに対する最適なデジタルソリューションを提供することで、企業が持続的な成長とイノベーションを達成できるようサポートします。
オンライン講座
製造業、主に購買・調達部門にお勤めの方々に向けた情報を配信しております。
新任の方やベテランの方、管理職を対象とした幅広いコンテンツをご用意しております。
お問い合わせ
コストダウンが利益に直結する術だと理解していても、なかなか前に進めることができない状況。そんな時は、newjiのコストダウン自動化機能で大きく利益貢献しよう!
(Β版非公開)