- お役立ち記事
- Fundamentals of metal fatigue fracture, failure analysis, failure examples, and failure prevention measures
月間77,185名の
製造業ご担当者様が閲覧しています*
*2025年2月28日現在のGoogle Analyticsのデータより
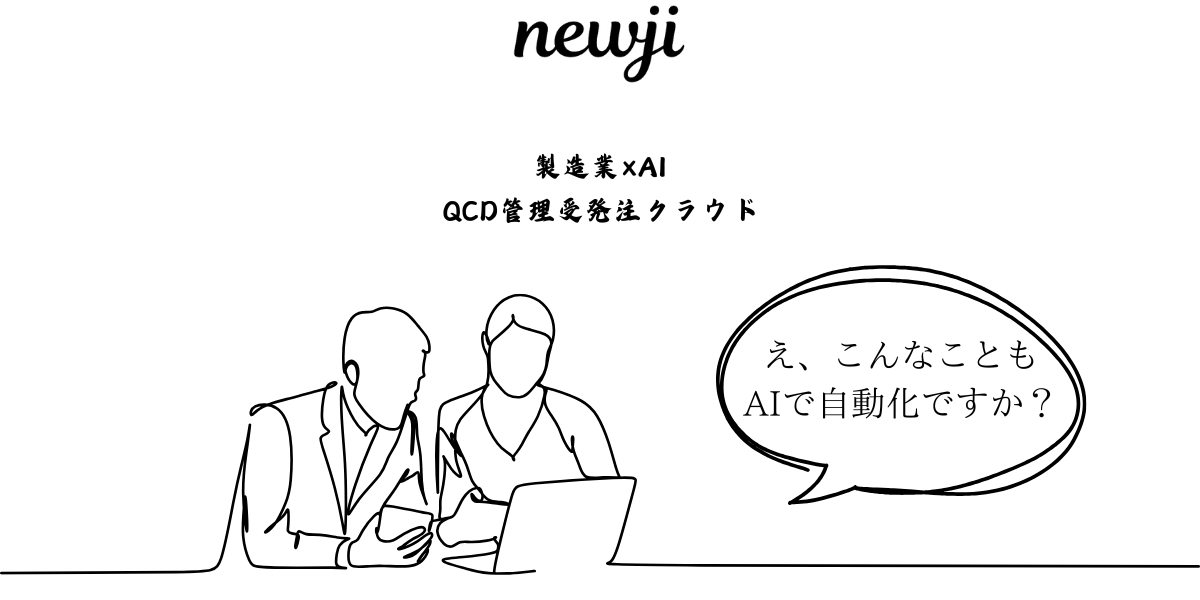
Fundamentals of metal fatigue fracture, failure analysis, failure examples, and failure prevention measures
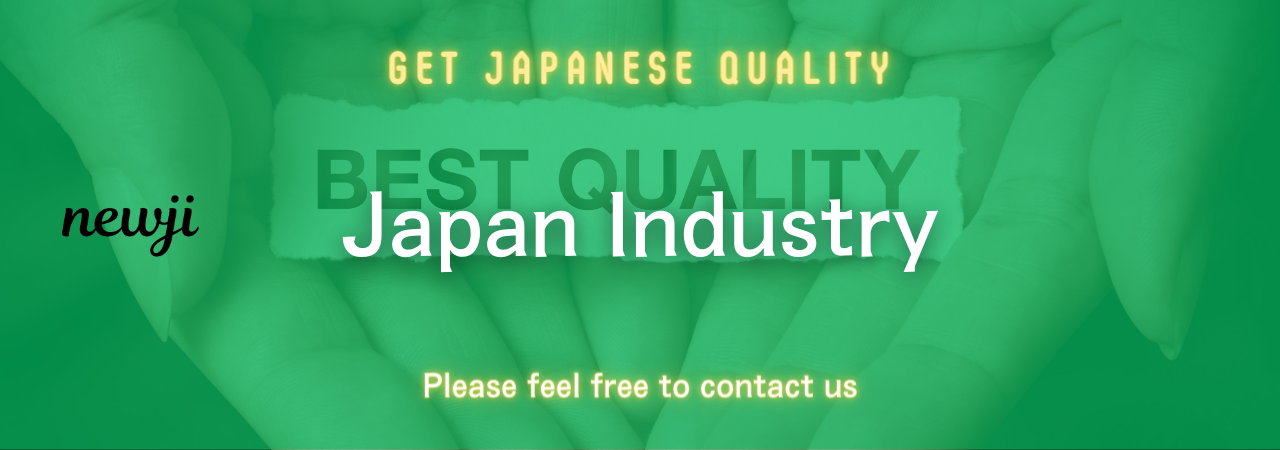
Metal fatigue fracture is an important topic in engineering and materials science, impacting everything from bridges to airplanes.
Understanding the fundamentals of this phenomenon, its analysis, example cases, and ways to prevent it are critical to ensuring the safety and longevity of structures and machinery.
目次
Understanding Metal Fatigue Fracture
Metal fatigue is a progressive and localized structural damage that occurs when a material is subjected to cyclic loading.
Unlike other forms of failure, fatigue fracture can happen at stress levels below the ultimate tensile strength of the material.
This makes it particularly challenging to predict and manage.
Fatigue fracture begins with the generation of small cracks on the surface.
These cracks grow over time with continued stress, eventually leading to a complete fracture.
The process is divided into three main stages: crack initiation, crack propagation, and final fracture.
Stages of Metal Fatigue
The first stage, crack initiation, involves the formation of microscopic cracks.
These are usually caused by surface irregularities, such as scratches or notches, where stress concentrations occur.
Next, during crack propagation, these small cracks expand progressively with each load cycle.
Finally, in the final fracture stage, the crack has grown sufficiently large that the remaining material can no longer withstand even a single cycle of the applied load, leading to complete failure.
Failure Analysis
Conducting a failure analysis is crucial for understanding the cause of a metal fatigue fracture and preventing future occurrences.
The analysis typically involves examining the fractured components, identifying the fatigue crack, and looking for characteristics like beach marks or striations that indicate the direction and growth of the crack.
Understanding the loading history is also vital, as it helps to recreate the stress environment leading to the failure.
Additionally, evaluating the material properties provides insight into how the metal performed under cyclic loading.
Tools and Techniques for Analysis
There are several tools and techniques used in failure analysis.
Microscopic examination, often with the aid of a scanning electron microscope (SEM), is used to assess crack features and material characteristics at a microscopic level.
Fractography, the study of the fracture surface, is an essential method to determine whether a failure was due to fatigue.
Advanced computational simulations can also offer insights by creating models that mimic the stress conditions experienced by the material.
Examples of Metal Fatigue Failure
Real-world examples of metal fatigue underscore the need for vigilance and proper engineering practices.
Perhaps the most famous case is the de Havilland Comet, the world’s first commercial jet airliner.
In the 1950s, multiple crashes were traced back to metal fatigue caused by repeated pressurization cycles.
Automotive parts, such as connecting rods in engines, are also susceptible to fatigue.
Another example is the collapse of the Silver Bridge in 1967, which was attributed to metal fatigue in an eyebar chain.
Avoiding Known Pitfalls
Learning from past failures involves identifying contributing factors such as design flaws, material defects, and improper maintenance practices.
Poor design choices like sharp corners, which create stress concentrations, and the use of materials with low fatigue resistance are common pitfalls.
Regular maintenance checks and timely repairs of detected cracks can also play a role in preventing failure.
Prevention Measures
Prevention is key to mitigating the risks of metal fatigue.
There are several strategies that engineers and manufacturers can employ to enhance fatigue resistance and prolong the life of metal components.
Design Improvements
Designing components with rounded edges, smooth surfaces, and avoiding stress concentrators can significantly reduce the likelihood of fatigue.
It’s important to incorporate enough safety margins in the design to accommodate for unexpected loads or conditions.
Material Selection
Selecting materials with high fatigue strength is crucial.
Alloys such as stainless steel and titanium are often preferred in applications where fatigue resistance is vital.
In addition, processes like surface hardening, which include case hardening or shot peening, increase the surface strength and delay crack initiation.
Regular Inspection and Maintenance
Routine inspections using non-destructive testing (NDT) techniques allow for the detection of fatigue cracks before they reach critical size.
Techniques like ultrasonic testing, magnetic particle inspection, and dye penetrant inspection are employed to find surface and subsurface cracks.
Implementing a strict maintenance schedule ensures that potential issues are identified and addressed promptly.
The Role of Fatigue Testing
Before a new product is launched, fatigue testing is often conducted to predict its lifespan under stress conditions similar to actual usage.
There are various methods for fatigue testing, such as low-cycle fatigue (LCF) and high-cycle fatigue (HCF) tests, each suited to different applications.
These tests provide valuable data for improving design, material choice, and understanding the loading conditions that can lead to fatigue failure.
Conclusion
Metal fatigue fracture is a complex phenomenon but understanding its fundamentals, conducting thorough failure analysis, learning from failure examples, and implementing robust prevention measures are all critical to managing its risks.
By applying these strategies, engineers can design safer and more reliable structures and components, effectively extending their service life and ensuring safety.
資料ダウンロード
QCD管理受発注クラウド「newji」は、受発注部門で必要なQCD管理全てを備えた、現場特化型兼クラウド型の今世紀最高の受発注管理システムとなります。
ユーザー登録
受発注業務の効率化だけでなく、システムを導入することで、コスト削減や製品・資材のステータス可視化のほか、属人化していた受発注情報の共有化による内部不正防止や統制にも役立ちます。
NEWJI DX
製造業に特化したデジタルトランスフォーメーション(DX)の実現を目指す請負開発型のコンサルティングサービスです。AI、iPaaS、および先端の技術を駆使して、製造プロセスの効率化、業務効率化、チームワーク強化、コスト削減、品質向上を実現します。このサービスは、製造業の課題を深く理解し、それに対する最適なデジタルソリューションを提供することで、企業が持続的な成長とイノベーションを達成できるようサポートします。
製造業ニュース解説
製造業、主に購買・調達部門にお勤めの方々に向けた情報を配信しております。
新任の方やベテランの方、管理職を対象とした幅広いコンテンツをご用意しております。
お問い合わせ
コストダウンが利益に直結する術だと理解していても、なかなか前に進めることができない状況。そんな時は、newjiのコストダウン自動化機能で大きく利益貢献しよう!
(β版非公開)