- お役立ち記事
- Fundamentals of metal fracture surface analysis and application to estimating fracture mechanisms and causes of damage
月間76,176名の
製造業ご担当者様が閲覧しています*
*2025年3月31日現在のGoogle Analyticsのデータより
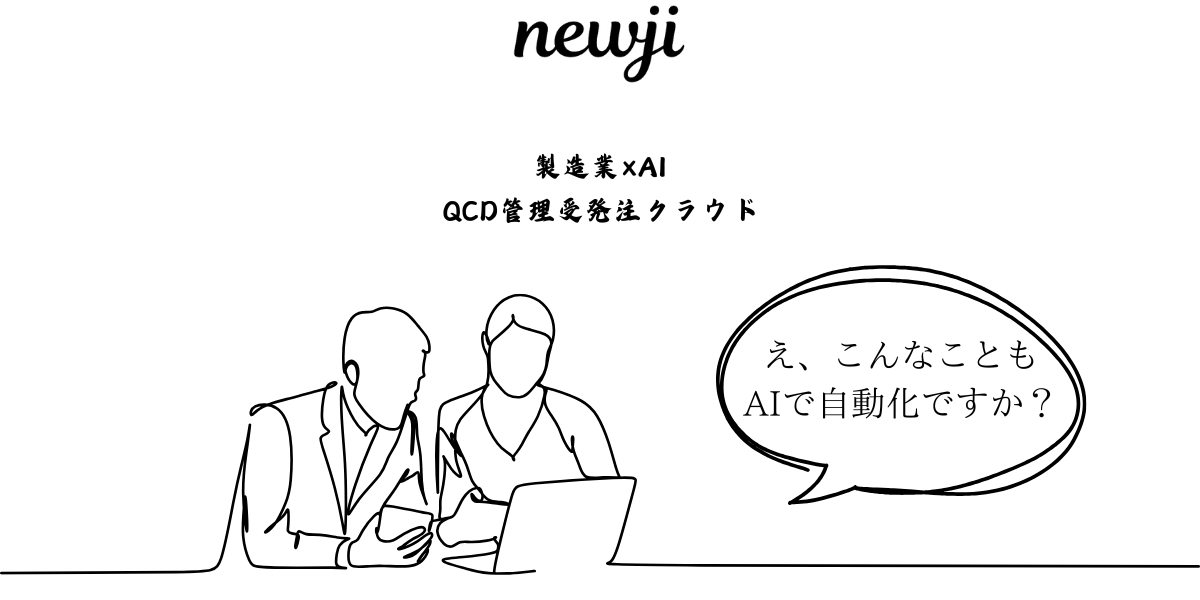
Fundamentals of metal fracture surface analysis and application to estimating fracture mechanisms and causes of damage
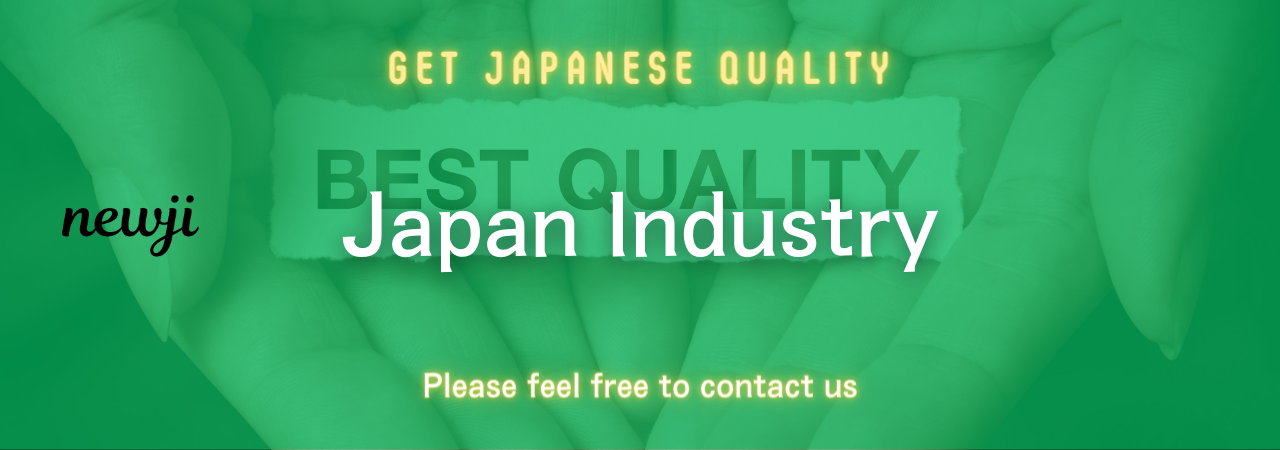
目次
Understanding Metal Fracture Surface Analysis
Metal fracture surface analysis is a crucial process used to study the characteristics and causes of fractures in metal materials.
It involves examining the fractured surface of a metal component to understand how and why the failure occurred.
This type of analysis helps in predicting failure patterns, estimating fracture mechanisms, and identifying causes of damage.
By doing so, industries can improve product designs, enhance safety standards, and prevent future failures.
Understanding the fundamentals of metal fracture surface analysis is essential for engineers, metallurgists, and researchers involved in materials science and failure analysis.
The Importance of Analyzing Metal Fractures
Metal fracture analysis plays a key role in various fields such as aerospace, automotive, construction, and manufacturing.
When a metal component fails, it is crucial to determine the cause to prevent similar incidents and improve materials and design processes.
By studying the fracture surface, experts can provide insights into the fracture mechanism, the stress levels, and the environmental factors involved in the failure.
This information is invaluable for developing more durable materials, optimizing production techniques, and ensuring the safety and reliability of metal structures and components.
Types of Metal Fractures
Understanding the type of fracture is an important step in metal fracture surface analysis.
There are two primary types of fractures: ductile and brittle fractures.
Ductile fractures occur when a metal undergoes significant plastic deformation before fracturing.
These fractures typically exhibit a characteristic dimpled appearance on the fractured surface.
Brittle fractures, on the other hand, happen with minimal plastic deformation.
They often occur suddenly and can be catastrophic, displaying a smooth and shiny surface with features like cleavage facets or river patterns.
Identifying whether a fracture is ductile or brittle helps in determining the fracture mechanism and underlying cause of the failure.
Fracture Mechanisms
Different mechanisms can lead to metal fracture, each resulting in distinct surface features.
One common mechanism is fatigue fracture, which occurs due to cyclic loading over time, even at stress levels below the material’s yield strength.
Fatigue fractures often display a repetitive pattern of striations or beach marks on the surface.
Another mechanism is stress corrosion cracking (SCC), where the metal degrades due to a combination of tensile stress and a corrosive environment.
SCC fractures may show intergranular or transgranular cracking patterns.
Understanding the fracture mechanism is crucial for diagnosing the root cause of failure and taking preventive measures.
Establishing the Cause of Damage
Through metal fracture surface analysis, experts can identify the specific causes of damage leading to the failure.
For instance, observations of certain surface features may suggest poor material quality, improper heat treatment, or design flaws.
External factors like environmental conditions, mechanical stresses, and chemical exposure can also contribute to the failure.
By correlating the fracture surface features with material properties and service conditions, experts can pinpoint the root cause and recommend necessary corrective actions.
This is an essential process for improving the reliability and lifespan of metal components.
Steps in Metal Fracture Surface Analysis
The process of analyzing metal fracture surfaces usually involves a few key steps that experts follow systematically.
Visual Inspection
The analysis typically begins with a visual inspection of the fractured surface using optical microscopes or magnifying lenses.
This step helps in identifying macroscopic features like color variations, surface texture, and fracture patterns that provide initial clues about the fracture type and possible mechanisms involved.
Microscopic Examination
After the visual inspection, a more detailed examination is conducted using advanced techniques such as scanning electron microscopy (SEM).
SEM provides high-resolution images of the fracture surface, revealing microscopic features that are not visible to the naked eye.
These features include dimples, striations, cleavage facets, and microcracks, which are crucial for determining the fracture mechanism and cause.
Chemical and Mechanical Analysis
Apart from surface examination, chemical analysis and mechanical testing may also be conducted as part of the analysis process.
Chemical analysis helps in identifying any alterations or corrosion products on the metal surface, while mechanical testing evaluates the material’s properties in the failed state.
These tests provide comprehensive data that support the findings from the visual and microscopic examinations.
Applications of Metal Fracture Surface Analysis
Metal fracture surface analysis is applied across various industries to enhance material performance, ensure safety, and reduce failure risks.
Material Development
In material development, the insights gained from fracture surface analysis aid in designing metal alloys with improved mechanical properties and resistance to fracture.
It helps in understanding the behavior of different alloy compositions under various service conditions.
Failure Prevention
By identifying the causes of previous failures, companies can take corrective actions to prevent similar incidents.
This involves optimizing design, material choice, and processing techniques, as well as implementing regular maintenance and inspection schedules.
Quality Assurance
In manufacturing, fracture surface analysis is used as a quality assurance tool to evaluate the integrity of components and ensure they meet the required standards.
It helps in detecting defects and weaknesses that may lead to premature failure.
Safety and Reliability
For critical structures like bridges, airplanes, and nuclear reactors, ensuring safety and reliability is essential.
Fracture surface analysis provides crucial information that helps in assessing the structural health of these components and preventing catastrophic failures that could lead to serious safety issues.
Conclusion
In summary, metal fracture surface analysis is a fundamental technique for understanding fracture mechanisms and diagnosing the causes of metal failure.
By analyzing the surface features, experts can identify the type of fracture, determine the fracture mechanism, and establish the cause of damage.
This information is invaluable for developing better materials, improving product designs, and ensuring the safety and reliability of metal components across various industries.
As technology and analytical methods continue to advance, the field of metal fracture analysis will play an increasingly vital role in advancing the science of materials engineering and failure analysis.
資料ダウンロード
QCD管理受発注クラウド「newji」は、受発注部門で必要なQCD管理全てを備えた、現場特化型兼クラウド型の今世紀最高の受発注管理システムとなります。
ユーザー登録
受発注業務の効率化だけでなく、システムを導入することで、コスト削減や製品・資材のステータス可視化のほか、属人化していた受発注情報の共有化による内部不正防止や統制にも役立ちます。
NEWJI DX
製造業に特化したデジタルトランスフォーメーション(DX)の実現を目指す請負開発型のコンサルティングサービスです。AI、iPaaS、および先端の技術を駆使して、製造プロセスの効率化、業務効率化、チームワーク強化、コスト削減、品質向上を実現します。このサービスは、製造業の課題を深く理解し、それに対する最適なデジタルソリューションを提供することで、企業が持続的な成長とイノベーションを達成できるようサポートします。
製造業ニュース解説
製造業、主に購買・調達部門にお勤めの方々に向けた情報を配信しております。
新任の方やベテランの方、管理職を対象とした幅広いコンテンツをご用意しております。
お問い合わせ
コストダウンが利益に直結する術だと理解していても、なかなか前に進めることができない状況。そんな時は、newjiのコストダウン自動化機能で大きく利益貢献しよう!
(β版非公開)