- お役立ち記事
- Fundamentals of metal heat treatment and countermeasures for deformation, cracking, and trouble
月間77,185名の
製造業ご担当者様が閲覧しています*
*2025年2月28日現在のGoogle Analyticsのデータより
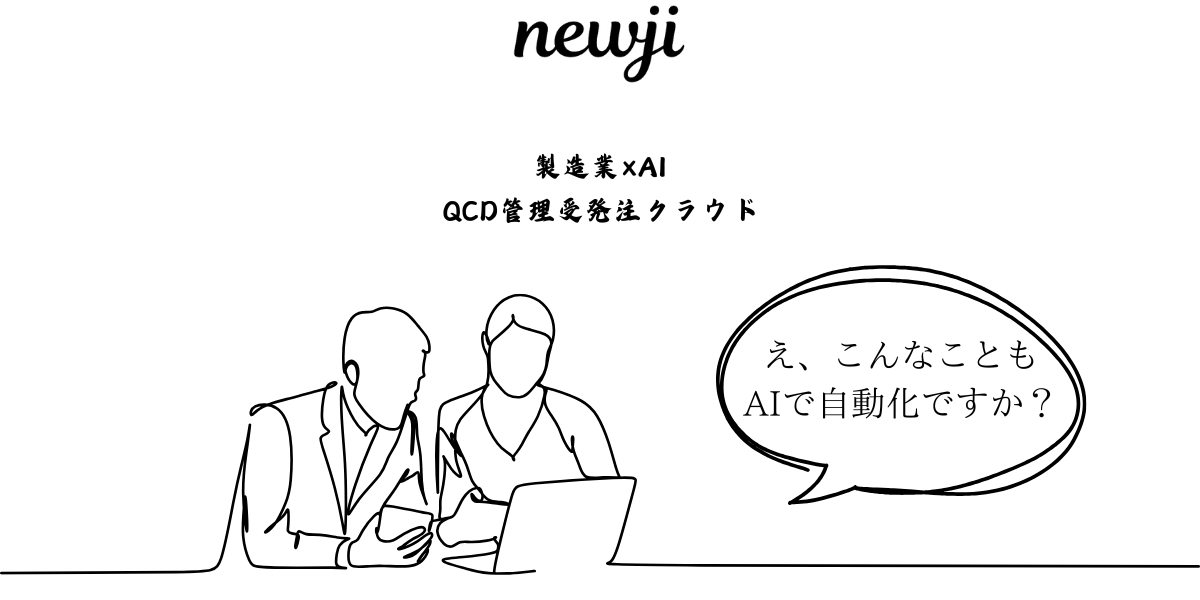
Fundamentals of metal heat treatment and countermeasures for deformation, cracking, and trouble
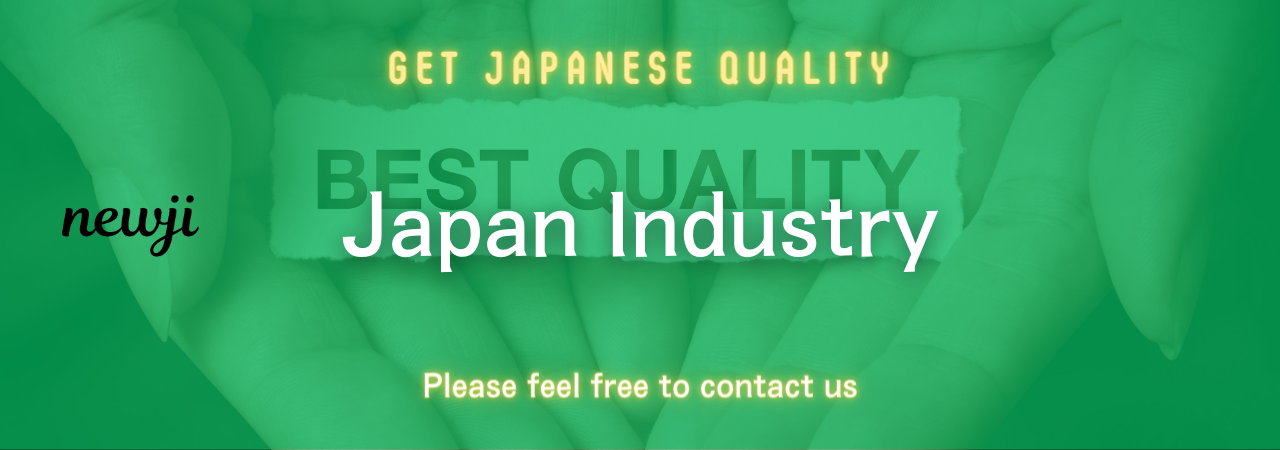
目次
Understanding Metal Heat Treatment
Metal heat treatment is a crucial process in the manufacturing and engineering industries, aimed at altering the physical and sometimes chemical properties of materials to achieve desired characteristics.
This process involves controlled heating and cooling of metals to change their structure and improve properties such as hardness, ductility, and strength.
Heat treatment processes are applied to metals to make them more suitable for specific applications.
This is achieved by manipulating properties through temperature regulation, leading to various end results like increased durability or enhanced resistance to wear.
Types of Heat Treatment Processes
There are several types of heat treatment processes, each serving different objectives based on the needs of the metal being treated.
Some of the most common methods include:
Annealing
Annealing involves heating the metal to a specific temperature and then slowly cooling it down.
The primary purpose of annealing is to soften the metal, improve its ductility, and relieve internal stresses.
This process helps in enhancing the machinability of metals, making them easier to form and cut.
Quenching
Quenching is a process wherein the metal is heated and then rapidly cooled in a quenching medium such as water, oil, or air.
This method is used primarily to increase the hardness of the metal.
Rapid cooling prevents the formation of unwanted microstructures, thereby achieving a harder metal surface.
Tempering
After quenching, metals are often too hard and brittle for practical use.
Tempering is used to alleviate this issue by reheating the metal to a lower temperature and then cooling it.
This reduces brittleness while maintaining its hardness and strength.
Normalizing
Normalizing involves heating the metal to a higher temperature and then allowing it to air cool.
This process aims to refine the grain structure of the metal, improving its toughness and making it less brittle.
Normalizing often results in a more uniform and consistent metal structure.
Countermeasures for Deformation, Cracking, and Trouble
During the heat treatment process, metals are susceptible to issues like deformation, cracking, and other types of trouble.
With a better understanding of the root causes, these problems can be addressed effectively.
Minimizing Deformation
Deformation can occur when there are uneven heating or cooling rates during the heat treatment process.
To minimize deformation, it is essential to ensure uniform temperature distribution.
Using appropriately sized furnaces, considering the orientation of parts, and employing pre-heating techniques are some methods to mitigate deformation.
Preventing Cracking
Cracking often results from excessive thermal stress or rapid temperature changes.
One effective countermeasure is to closely control the heating and cooling rates.
Maintaining a steady transition between temperatures helps prevent the extreme stresses that cause cracking.
Utilizing stress-relief methods like controlled cooling can also be beneficial.
Addressing Other Troubles
Heat treatment can sometimes lead to undesired changes in microstructure.
This can result in a reduction of metal performance.
To counter this, it is vital to use appropriate heat treatment parameters suited to the specific metal being treated.
Quality control measures, such as consistent monitoring and testing, ensure that the desired properties are achieved.
Optimizing Heat Treatment Processes
Achieving optimal results in heat treatment requires a well-thought-out approach.
One crucial aspect is choosing the correct method and understanding the specific transformations that occur at various temperatures.
Furthermore, precise process control and robust equipment play a pivotal role in achieving consistent and effective outcomes.
Leveraging Modern Technologies
Modern advancements in technology have introduced sophisticated equipment and techniques that aid in better heat treatment practices.
Computer simulations and modeling can predict the behavior of metals under different conditions, helping in planning and optimizing the heat treatment cycle.
Using these advanced tools leads to a more precise process, ensuring higher quality and performance of the treated metals.
Conclusion
Metal heat treatment is an indispensable part of modern manufacturing processes, offering flexibility in enhancing and customizing metal properties.
By understanding the fundamentals of different types of heat treatments and implementing effective countermeasures for potential issues, manufacturers can significantly improve the performance and lifespan of metal products.
Adopting modern technology and focusing on process optimization further enhances the ability to produce high-quality metals tailored to specific applications.
資料ダウンロード
QCD管理受発注クラウド「newji」は、受発注部門で必要なQCD管理全てを備えた、現場特化型兼クラウド型の今世紀最高の受発注管理システムとなります。
ユーザー登録
受発注業務の効率化だけでなく、システムを導入することで、コスト削減や製品・資材のステータス可視化のほか、属人化していた受発注情報の共有化による内部不正防止や統制にも役立ちます。
NEWJI DX
製造業に特化したデジタルトランスフォーメーション(DX)の実現を目指す請負開発型のコンサルティングサービスです。AI、iPaaS、および先端の技術を駆使して、製造プロセスの効率化、業務効率化、チームワーク強化、コスト削減、品質向上を実現します。このサービスは、製造業の課題を深く理解し、それに対する最適なデジタルソリューションを提供することで、企業が持続的な成長とイノベーションを達成できるようサポートします。
製造業ニュース解説
製造業、主に購買・調達部門にお勤めの方々に向けた情報を配信しております。
新任の方やベテランの方、管理職を対象とした幅広いコンテンツをご用意しております。
お問い合わせ
コストダウンが利益に直結する術だと理解していても、なかなか前に進めることができない状況。そんな時は、newjiのコストダウン自動化機能で大きく利益貢献しよう!
(β版非公開)