- お役立ち記事
- Fundamentals of metal powder injection molding method, application to metal parts manufacturing, and design technology
月間77,185名の
製造業ご担当者様が閲覧しています*
*2025年2月28日現在のGoogle Analyticsのデータより
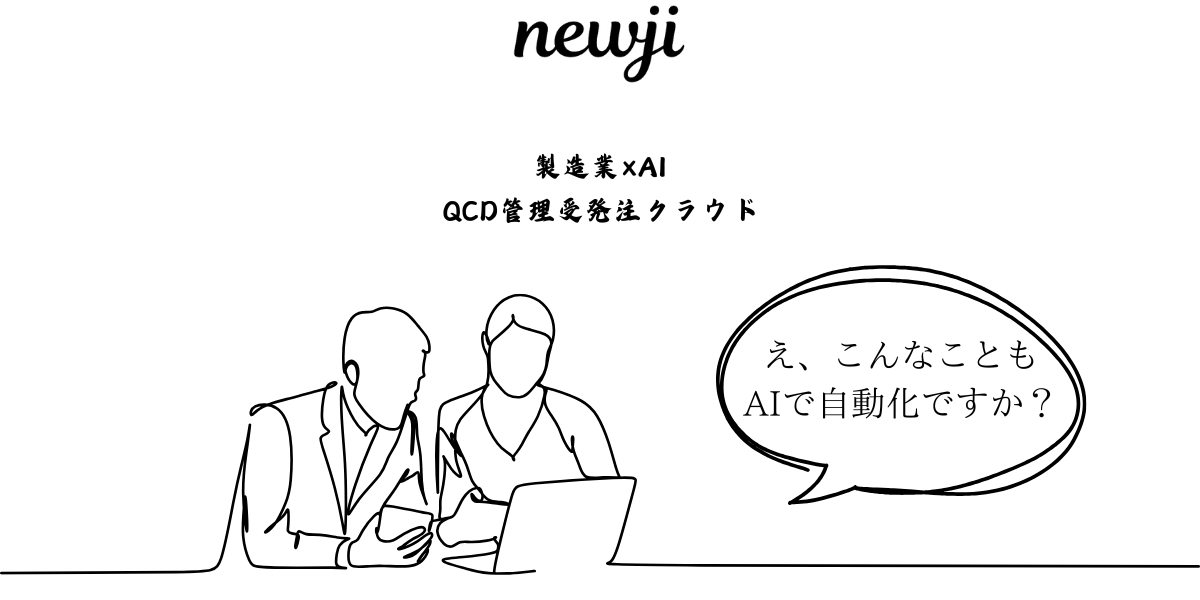
Fundamentals of metal powder injection molding method, application to metal parts manufacturing, and design technology
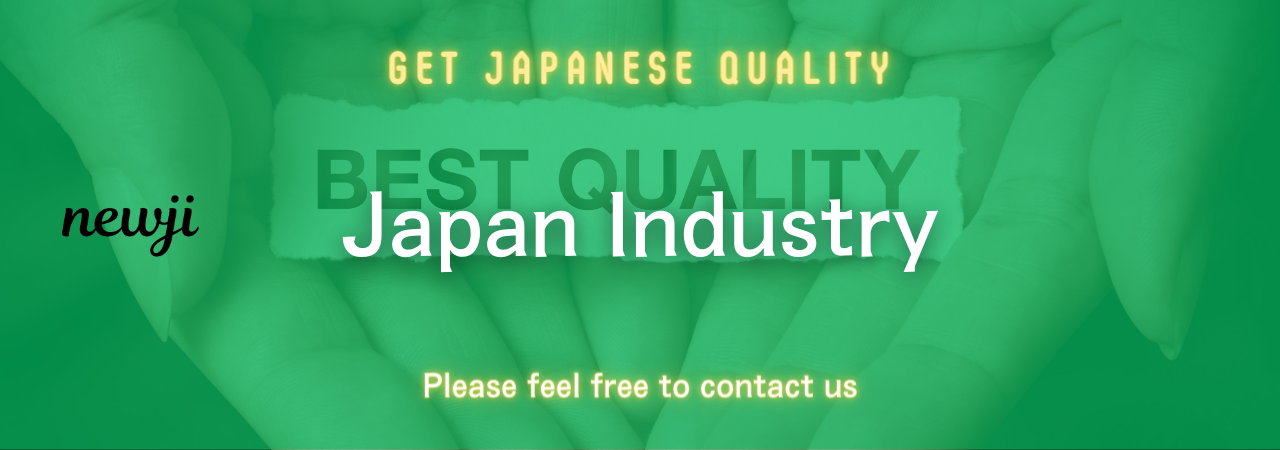
目次
Introduction to Metal Powder Injection Molding (MIM)
Metal Powder Injection Molding (MIM) is an advanced manufacturing process that blends the versatility of plastic injection molding with the strength and integrity of powdered metallurgy.
This innovative technology allows the production of complex metal parts with high precision and excellent mechanical properties.
MIM plays a significant role in producing small to medium-sized metal components used in various industries, including automotive, aerospace, medical, and consumer electronics.
MIM offers several advantages over traditional manufacturing methods, such as the ability to produce parts with intricate designs, reduce material wastage, and achieve high production speeds.
Additionally, MIM is cost-effective for creating large quantities of parts, as it minimizes the need for costly secondary operations.
The technology’s ability to use a wide range of metals, including stainless steel, titanium, and aluminum, further enhances its appeal across different applications.
The Metal Powder Injection Molding Process
The MIM process consists of several key stages that work together to transform metal powders into functional components.
Here’s a step-by-step overview of how MIM works:
Feedstock Preparation
The first step in the MIM process is the preparation of the feedstock.
This involves blending fine metal powders with a thermoplastic binder to create a homogeneous mixture.
The binder acts as a vehicle for the powder during the molding process, providing the necessary flow characteristics.
The feedstock must be meticulously prepared to ensure consistent and high-quality results in the final product.
Injection Molding
Once the feedstock is ready, it is heated and injected into a mold using an injection molding machine.
The mold shape is designed to match the desired geometry of the finished part.
Under high pressure and temperature, the feedstock fills the mold cavity, taking its shape.
This step is crucial, as it determines the dimensions and features of the metal component.
Debinding
After the injection molding process, the component, known as the “green part,” contains both metal powder and binder.
The next phase is debinding, which involves removing the binder through a series of thermal or solvent treatment processes.
Debinding must be done carefully to avoid damaging the part’s structure or causing defects.
Sintering
The final stage in the MIM process is sintering.
During sintering, the debound part is subjected to high temperatures, just below the melting point of the metal.
This allows the metal particles to bond together, densifying the part and significantly increasing its strength.
The sintering process reduces the part’s volume slightly, requiring precise calculations to achieve the desired final size.
Applications of Metal Powder Injection Molding
MIM is utilized in a wide range of industries, thanks to its ability to produce complex geometries from a variety of materials.
Here are some notable applications:
Automotive Industry
In the automotive sector, MIM is used to create small, intricate parts like gears, fasteners, and sensors.
The process supports the high-volume production required by this industry while maintaining the necessary quality and precision standards.
Aerospace and Defense
MIM is ideal for manufacturing lightweight and strong components, such as brackets, bushings, and connectors in the aerospace and defense industries.
The ability to use materials like titanium adds to the appeal of MIM for these high-performance applications.
Medical Devices
In the medical field, MIM produces components for surgical instruments, orthodontic appliances, and implants.
The biocompatibility of certain metals used in MIM makes it suitable for medical applications where safety and reliability are paramount.
Electronics and Consumer Goods
MIM is employed in the production of various electronic components and consumer goods, from connectors to casings.
The precision and efficiency of MIM make it ideal for mass-producing high-quality components cost-effectively.
Design Technology for Metal Injection Molding
Designing for MIM requires a different approach compared to traditional manufacturing processes, due to the unique properties of the feedstock and the molding process.
Here are some key considerations for designing MIM parts:
Geometry Complexity
One of the significant advantages of MIM is its ability to produce complex geometries which would be challenging or impossible with other methods.
Designers should leverage this capability by incorporating intricate features such as undercuts, thin walls, and complex curves.
Tolerances and Surface Finish
While MIM offers high precision, certain factors, like shrinkage during sintering, must be accounted for in the design phase.
Engineers should specify realistic tolerances and understand that additional finishing processes may be required to achieve the desired surface quality.
Material Selection
Choosing the right material is critical in MIM design.
The selected metal must meet the mechanical, thermal, and chemical properties required for the application.
Collaborating with material scientists can help in identifying the optimal material for a specific design.
Cost Efficiency
Designers must consider the cost implications of MIM at every stage.
Minimizing material wastage, optimizing the design for molding efficiency, and reducing secondary operations are essential strategies to keep production costs manageable.
Conclusion
Metal Powder Injection Molding is a revolutionary technique that bridges the gap between plastic injection molding and metalworking.
Its unique capabilities allow for the efficient production of high-quality metal components with complex geometries.
Through an understanding of the MIM process, applications, and design principles, industries can harness this technology to create innovative products and meet the ever-growing demands of modern markets.
As MIM technology continues to evolve, it holds the promise of further expanding the possibilities for metal part manufacturing, offering enhanced performance, reduced costs, and increased environmental sustainability.
資料ダウンロード
QCD管理受発注クラウド「newji」は、受発注部門で必要なQCD管理全てを備えた、現場特化型兼クラウド型の今世紀最高の受発注管理システムとなります。
ユーザー登録
受発注業務の効率化だけでなく、システムを導入することで、コスト削減や製品・資材のステータス可視化のほか、属人化していた受発注情報の共有化による内部不正防止や統制にも役立ちます。
NEWJI DX
製造業に特化したデジタルトランスフォーメーション(DX)の実現を目指す請負開発型のコンサルティングサービスです。AI、iPaaS、および先端の技術を駆使して、製造プロセスの効率化、業務効率化、チームワーク強化、コスト削減、品質向上を実現します。このサービスは、製造業の課題を深く理解し、それに対する最適なデジタルソリューションを提供することで、企業が持続的な成長とイノベーションを達成できるようサポートします。
製造業ニュース解説
製造業、主に購買・調達部門にお勤めの方々に向けた情報を配信しております。
新任の方やベテランの方、管理職を対象とした幅広いコンテンツをご用意しております。
お問い合わせ
コストダウンが利益に直結する術だと理解していても、なかなか前に進めることができない状況。そんな時は、newjiのコストダウン自動化機能で大きく利益貢献しよう!
(β版非公開)