- お役立ち記事
- Fundamentals of metal welding/laser welding technology and application to dissimilar metal joining
Fundamentals of metal welding/laser welding technology and application to dissimilar metal joining
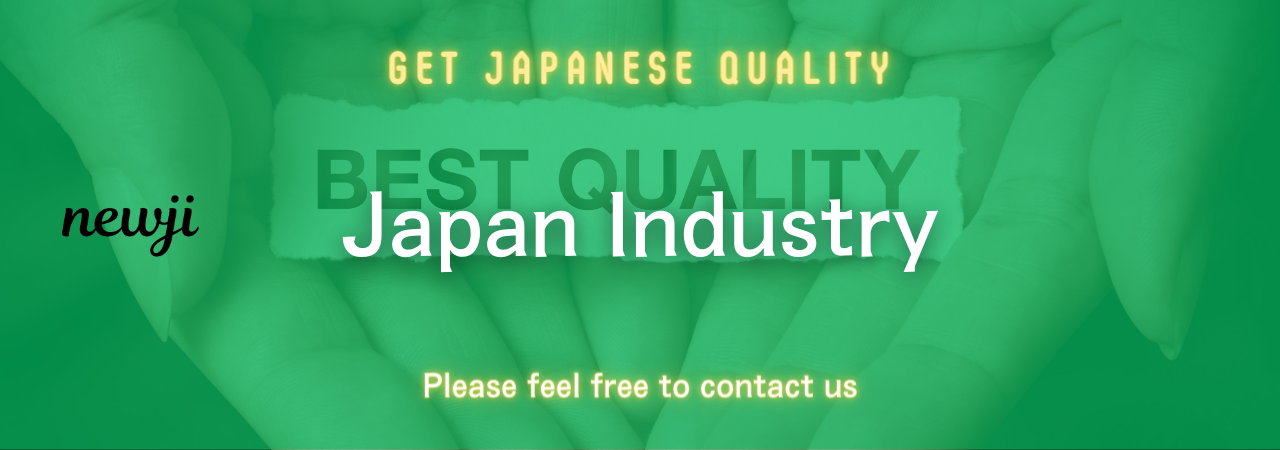
目次
Introduction to Metal Welding
Metal welding is a foundational process in fabrication and construction industries, allowing for the joining of two or more pieces of metal into a single structure.
Welding is achieved by melting the workpieces and adding a filler material to form a strong joint when cooled.
There are various welding techniques, each suitable for different types of metals and applications.
Traditional Welding Techniques
Traditional welding techniques, such as arc welding, utilize an electric arc to melt metals.
In gas welding, a flame produced by burning gas melts the metal.
These methods have been used for decades and are well-understood.
They are effective for working with similar metals as they ensure uniform properties at the joints.
However, when welding dissimilar metals, they may face challenges such as different melting points and thermal expansion rates, sometimes leading to weak or brittle joints.
Rise of Laser Welding Technology
The introduction of laser welding has brought significant advancements to the field.
This technology uses a highly focused laser beam to heat the metal, allowing for precision and control.
Laser welding offers several benefits over traditional methods, including faster processing speeds and higher precision, which reduces the likelihood of defects.
Additionally, the skill level required for operators is typically lower since the process is highly automated.
How Laser Welding Works
Laser welding involves focusing a concentrated laser beam onto the metal’s surface.
The intense energy from the laser melts a small area of the metal creating a pool of molten material.
Once cooled, this forms a solid joint.
This process can be continuous or pulsed, depending on the application’s requirements.
Types of Lasers Used
There are several types of lasers used in welding, each suitable for different tasks.
CO2 lasers are common for welding thick materials because of their high power.
On the other hand, fiber lasers are ideal for precision work due to their adaptability and efficiency.
Nd:YAG lasers are versatile and can be used for welding a variety of metals, offering a balance between power and precision.
Benefits of Laser Welding
One major advantage of laser welding is its ability to join dissimilar metals.
The precision of the laser allows for controlling the heat input carefully to accommodate differences in melting points and thermal properties.
This minimizes undesirable effects such as warping or structural weakness.
Furthermore, laser welding often requires less post-processing, as it produces cleaner and smoother welds.
Its high automation potential leads to increased productivity and consistency in output, making it suitable for high-volume manufacturing.
Application to Dissimilar Metal Joining
Joining dissimilar metals can be challenging due to differences in physical and chemical properties.
Laser welding addresses these challenges by providing localized, controlled heat input.
This allows the creation of robust joints without the need for additional materials or complex processes.
Common Challenges
When welding dissimilar metals, issues such as galvanic corrosion and cracking can occur.
Dissimilar metals often expand and contract at different rates, leading to structural weaknesses.
Their different melting points can also cause one material to overheat while the other remains solid, leading to incomplete fusion.
Strategies for Success
To overcome these challenges, specific strategies are employed within laser welding.
These include adjusting the laser’s focus and power to concentrate energy on one metal more heavily than the other.
Operators may also implement pulse-modulation techniques, allowing precise control over heat delivery.
In some cases, a filler material with intermediary properties is used to bridge the differences between the metals.
These methods help facilitate a stronger bond and reduce the potential for defects in the welds.
Industries and Innovations
Laser welding has made significant strides in various industries, driving innovations and improving production processes.
Automotive Industry
In the automotive industry, laser welding is used for joining light metals like aluminum and magnesium with steel.
This allows for lighter vehicle structures without compromising strength, resulting in better fuel efficiency.
Electronics and Microprocessing
The electronics industry benefits from laser welding for its precision in assembling small components such as sensors and connectors.
This is particularly relevant in the production of mobile devices and computers, where space is a premium.
Aerospace and Defense
In aerospace, the need for lightweight yet durable materials is critical.
Laser welding facilitates the joining of specialty metals like titanium with other components, enhancing performance and reducing weight.
Conclusion
Laser welding represents a significant advancement in metal joining technology, particularly for dissimilar metals.
Its precision and efficiency offer distinct advantages over traditional methods, making it integral to modern manufacturing.
With ongoing advancements, laser welding continues to expand its applications, paving the way for innovative solutions across various industries.
資料ダウンロード
QCD調達購買管理クラウド「newji」は、調達購買部門で必要なQCD管理全てを備えた、現場特化型兼クラウド型の今世紀最高の購買管理システムとなります。
ユーザー登録
調達購買業務の効率化だけでなく、システムを導入することで、コスト削減や製品・資材のステータス可視化のほか、属人化していた購買情報の共有化による内部不正防止や統制にも役立ちます。
NEWJI DX
製造業に特化したデジタルトランスフォーメーション(DX)の実現を目指す請負開発型のコンサルティングサービスです。AI、iPaaS、および先端の技術を駆使して、製造プロセスの効率化、業務効率化、チームワーク強化、コスト削減、品質向上を実現します。このサービスは、製造業の課題を深く理解し、それに対する最適なデジタルソリューションを提供することで、企業が持続的な成長とイノベーションを達成できるようサポートします。
オンライン講座
製造業、主に購買・調達部門にお勤めの方々に向けた情報を配信しております。
新任の方やベテランの方、管理職を対象とした幅広いコンテンツをご用意しております。
お問い合わせ
コストダウンが利益に直結する術だと理解していても、なかなか前に進めることができない状況。そんな時は、newjiのコストダウン自動化機能で大きく利益貢献しよう!
(Β版非公開)