- お役立ち記事
- Fundamentals of methods to reduce toughness deterioration in metals and applications to rust and hydrogen embrittlement of metal materials
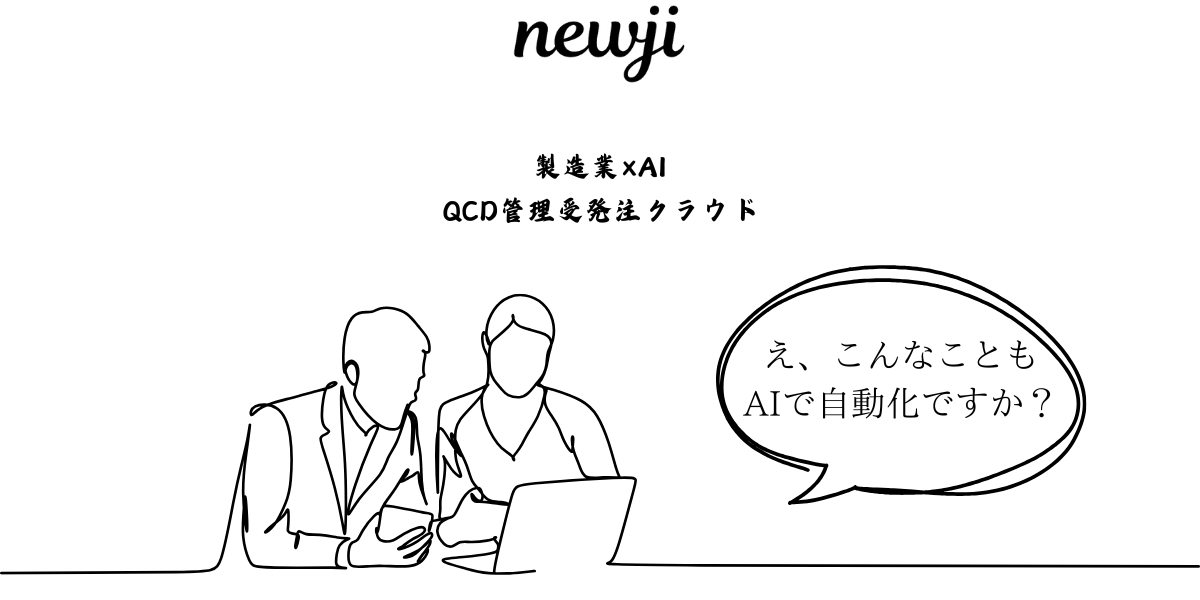
Fundamentals of methods to reduce toughness deterioration in metals and applications to rust and hydrogen embrittlement of metal materials
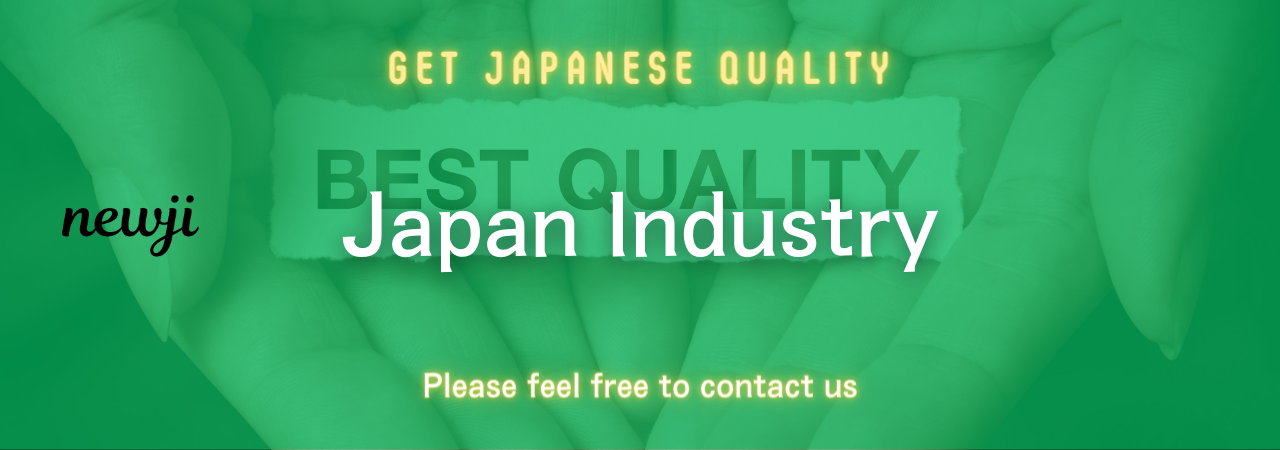
目次
Understanding Metal Toughness
Metal toughness refers to the ability of a metal to absorb energy and deform without fracturing.
It is a critical property for many applications, including construction, automotive, and aerospace industries.
However, metals can experience toughness deterioration due to various environmental and operational factors.
Understanding these factors and the methods to mitigate them can help maintain the integrity and longevity of metal structures and components.
Factors Affecting Metal Toughness
Several factors can contribute to the deterioration of metal toughness.
These include:
1. **Temperature**: Exposure to extreme temperatures can alter the microstructure of metals, leading to reduced toughness.
Cold temperatures, in particular, can make metals more brittle.
2. **Deformation**: Repeated or excessive deformation can cause the work-hardening effect, which can reduce metal ductility and toughness.
3. **Environmental Conditions**: Corrosive environments, such as exposure to seawater or industrial atmospheres, can induce rust formation, leading to the deterioration of metal toughness.
4. **Presence of Impurities**: Impurities and inclusions within the metal matrix can act as stress concentrators, promoting crack initiation and propagation.
5. **Hydrogen Embrittlement**: The absorption of hydrogen into metals can lead to embrittlement, a process where the metal becomes brittle and more prone to cracking.
Methods to Reduce Toughness Deterioration
Understanding and implementing techniques to reduce toughness deterioration is vital for extending the life of metal components.
Temperature Control
Temperature control is essential for maintaining metal toughness.
Here are some approaches:
– **Heat Treatments**: Heat treatments, such as annealing and tempering, can be used to alter the microstructure of metals, improving their toughness and resistance to brittleness.
– **Design Considerations**: Designing components with protective coverings or coatings can prevent unnecessary exposure to extreme temperatures.
Minimizing Deformation
To prevent toughness reduction due to deformation:
– **Load Management**: Ensure that metal components are not subjected to loads beyond their rated capacity.
– **Fatigue Analysis**: Regularly monitor components that are subject to cyclic loading to detect early signs of fatigue failure.
Corrosion Prevention
Preventing rust and other forms of corrosion is crucial for maintaining toughness.
– **Coatings and Paints**: Applying protective coatings or paints can create a barrier against environmental factors that promote rust formation.
– **Cathodic Protection**: This method involves using a sacrificial anode made of a more easily corroded metal to protect the primary metal structure.
Purity Control
Maintaining metal purity is important in preventing toughness degradation.
– **Quality Material Selection**: Utilize high-quality, purified metals with controlled alloys to minimize the presence of harmful inclusions and impurities.
– **Regular Inspections**: Conducting regular inspections can help identify inclusions and impurities before they become a problem.
Addressing Hydrogen Embrittlement
Hydrogen embrittlement is a significant cause of toughness deterioration in metals, especially in high-strength steels and alloys.
This condition occurs when hydrogen atoms infiltrate the metal, accumulating at grain boundaries and leading to brittle fractures.
Prevention Strategies
Several prevention strategies can be employed to address hydrogen embrittlement:
– **Material Selection**: Use materials that are less susceptible to hydrogen penetration and retention, especially for applications with high exposure to hydrogen.
– **Hydrogen Absorber Elements**: Incorporate elements like titanium or zirconium in alloys that can reduce hydrogen permeability.
– **Post-Process Treatments**: Methods like baking or heat treatment after galvanizing or plating can help to drive out hydrogen from the metal matrix.
Regular Monitoring and Maintenance
Regular monitoring and maintenance are critical in managing hydrogen embrittlement risks.
– **Non-Destructive Testing (NDT)**: Techniques like ultrasonic testing and radiography can help detect incipient cracks or stress points caused by hydrogen embrittlement.
– **Maintenance Schedules**: Implementing strict maintenance schedules ensures that any signs of hydrogen embrittlement are addressed promptly.
Applications and Future Perspectives
Understanding and implementing ways to maintain metal toughness is pivotal across various industries.
The construction industry relies heavily on metals for the structural integrity of buildings and bridges, demanding a keen focus on preventing deterioration.
In the automotive and aerospace sectors, where safety and performance are paramount, the role of metal toughness cannot be overstated.
Innovations in Metal Science
The field of materials science continues to progress, offering new techniques and materials to combat toughness deterioration.
– **Advanced Alloys**: Development of new alloy compositions that offer improved resistance to environmental factors is a promising area of research.
– **Surface Treatments**: Innovations in surface treatments, such as laser cladding or nanoparticle reinforcement, can significantly enhance metal toughness.
Visualization tools and computer modeling techniques are becoming integral to understanding how metals will perform under various conditions.
These advancements provide insights into stress distribution and potential sites for toughness deterioration.
Conclusion
Maintaining the toughness of metals is crucial for their reliability and durability in various applications.
By understanding the factors that contribute to toughness deterioration and implementing effective prevention methods, industries can ensure the longevity and integrity of metal components.
As technologies evolve, continued research and innovation will further enhance our abilities to combat toughness deterioration and address challenges such as rust and hydrogen embrittlement efficiently.
資料ダウンロード
QCD調達購買管理クラウド「newji」は、調達購買部門で必要なQCD管理全てを備えた、現場特化型兼クラウド型の今世紀最高の購買管理システムとなります。
ユーザー登録
調達購買業務の効率化だけでなく、システムを導入することで、コスト削減や製品・資材のステータス可視化のほか、属人化していた購買情報の共有化による内部不正防止や統制にも役立ちます。
NEWJI DX
製造業に特化したデジタルトランスフォーメーション(DX)の実現を目指す請負開発型のコンサルティングサービスです。AI、iPaaS、および先端の技術を駆使して、製造プロセスの効率化、業務効率化、チームワーク強化、コスト削減、品質向上を実現します。このサービスは、製造業の課題を深く理解し、それに対する最適なデジタルソリューションを提供することで、企業が持続的な成長とイノベーションを達成できるようサポートします。
オンライン講座
製造業、主に購買・調達部門にお勤めの方々に向けた情報を配信しております。
新任の方やベテランの方、管理職を対象とした幅広いコンテンツをご用意しております。
お問い合わせ
コストダウンが利益に直結する術だと理解していても、なかなか前に進めることができない状況。そんな時は、newjiのコストダウン自動化機能で大きく利益貢献しよう!
(Β版非公開)