- お役立ち記事
- Fundamentals of model predictive control technology and effective application points
月間76,176名の
製造業ご担当者様が閲覧しています*
*2025年3月31日現在のGoogle Analyticsのデータより
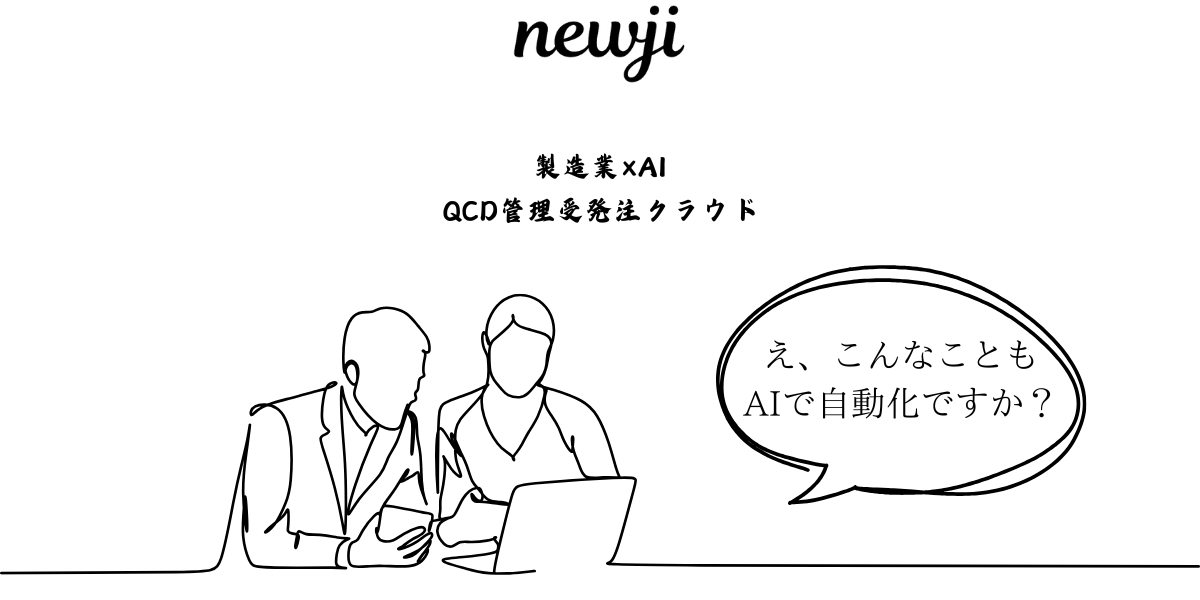
Fundamentals of model predictive control technology and effective application points
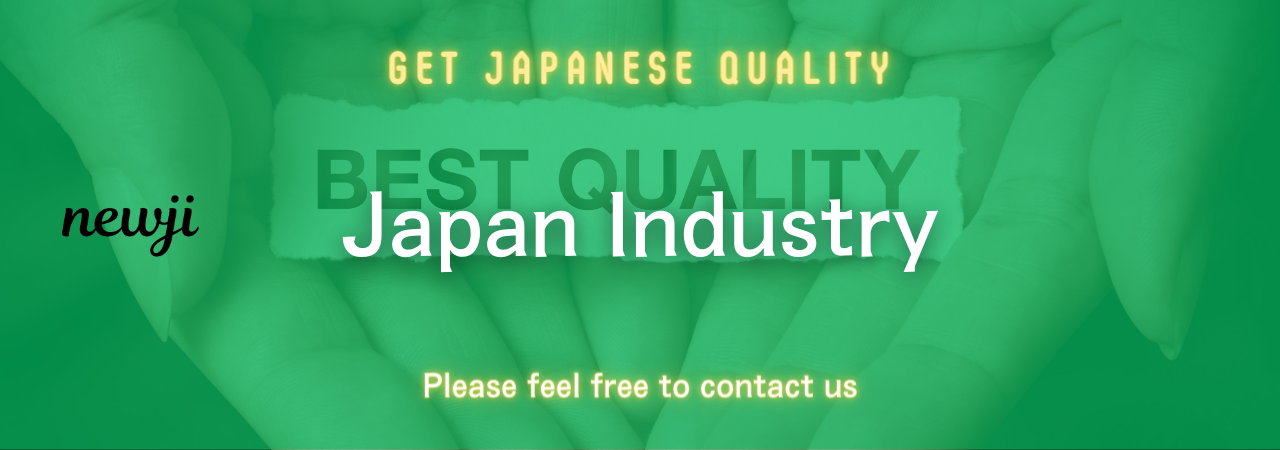
目次
Understanding Model Predictive Control (MPC)
Model Predictive Control, commonly known as MPC, is a sophisticated control strategy used in various industries to optimize the performance of complex systems.
It involves predicting future behavior and making decisions to guide the system to achieve desired outcomes.
This control technique is particularly useful in processes with multiple variables, constraints, and the necessity for efficient resource management.
MPC operates by using mathematical models to predict the future behavior of a system over a specified time horizon.
These models help in determining the best control actions by solving an optimization problem at each control interval.
This approach enables the controller to anticipate changes and adjust operational parameters accordingly.
The Significance of MPC
One of the primary benefits of MPC is its ability to handle multivariable control tasks effectively.
Unlike traditional control methods, which often struggle with interactions between various system components, MPC can manage these interactions seamlessly.
This capability is crucial in industries like chemical processing, manufacturing, and energy, where numerous variables must be controlled simultaneously.
Additionally, MPC takes constraints into account while deciding on control actions.
This ensures that the solutions are feasible and practical, considering limitations in system capacity, safety, and regulatory requirements.
As a result, MPC can significantly enhance the efficiency, safety, and reliability of operations.
How Model Predictive Control Works
The functionality of MPC is centered on a few core components: the prediction model, the optimization algorithm, and feedback.
Here’s a closer look at each element:
Prediction Model
The prediction model is the heart of MPC.
It is built using either first-principles modeling, data-driven methods, or a combination of both.
The model simulates the future behavior of the system based on current data and past performance.
These predictions help in anticipating how different control actions will influence the system over the specified time horizon.
Optimization Algorithm
Each time the system requires a control decision, MPC solves an optimization problem.
The algorithm considers the prediction model, objectives, and constraints to find the best control actions.
The optimization aims to minimize or maximize a specific performance criterion, such as reducing energy consumption or maximizing production yield
By continuously solving these problems in real time, MPC ensures that the system remains on the optimal path.
Feedback Mechanism
MPC relies on real-time feedback to enhance its accuracy and responsiveness.
It continuously receives data from the monitored process, allowing it to update predictions and adjust control actions accordingly.
This feedback loop helps MPC to remain effective even in the presence of disturbances and uncertainties.
Applications of Model Predictive Control
MPC is utilized in a variety of industries, driving improvements in efficiency and control precision.
Below are some noteworthy applications:
Chemical and Petrochemical Industries
In chemical and petrochemical processes, precise control of reaction conditions is essential for product quality and safety.
MPC manages variables such as temperature, pressure, and flow rates, ensuring optimal operating conditions while adhering to safety regulations.
Automotive Industry
MPC is implemented in advanced driver-assistance systems (ADAS) and autonomous vehicles.
By predicting the behavior of the vehicle and its surroundings, MPC helps in executing safe and efficient driving maneuvers, enhancing both safety and driving experience.
Renewable Energy
Renewable energy systems, like wind and solar power, face challenges due to the stochastic nature of their energy sources.
MPC helps in optimizing power output by managing the interaction between different components, such as converters and storage systems, and aligning them with grid demands.
Manufacturing
In manufacturing, MPC improves process stability and efficiency by controlling production lines involving multiple interdependent processes.
It ensures that resources are used optimally, reducing waste and improving product quality.
Effective Application Points for MPC
While MPC offers numerous benefits, its application must be approached strategically to maximize its potential.
Here’s how organizations can effectively implement MPC:
Identify the Right Applications
Before implementing MPC, it’s crucial to evaluate whether the process complexities and interactions justify its use.
Applications with multivariable interactions, constraints, and the potential for significant performance improvements are suitable candidates.
Develop Accurate Models
Accurate prediction models are instrumental for the successful application of MPC.
Developing these models involves selecting the right techniques, such as first-principles modeling or machine learning, and ensuring they are well-calibrated with real process data.
Ensure Real-Time Data Acquisition
Real-time data acquisition is essential for the efficient functioning of MPC.
Ensure the system can reliably collect, process, and analyze data at the speed required to keep predictions and control actions up-to-date.
Regularly Update and Maintain the System
The industrial environment is dynamic, with changes in process conditions and hardware updates.
Regularly updating the MPC system to reflect these changes is crucial for maintaining its effectiveness.
Periodic recalibration, model updates, and algorithm adjustments will help the system continue to deliver optimal performance.
Integrate with Existing Systems
MPC should be integrated seamlessly with existing control systems to deliver maximum benefits.
This might involve interconnecting with enterprise resource planning (ERP) systems or supervisory control and data acquisition (SCADA) systems, ensuring data flow and process connectivity remain intact.
Training and Skill Development
Investing in training and skill development for personnel is vital.
Understanding the principles of MPC, its configuration, and troubleshooting will empower operators and engineers to leverage the full potential of the technology.
Knowledgeable staff can help in fine-tuning the system, identifying potential improvements, and responding to system alerts effectively.
Model Predictive Control technology stands as a pivotal advancement in control engineering, offering superior operational efficiencies and processes optimization across diverse industries.
Its ability to predict future scenarios and optimize control actions makes it invaluable in applications requiring high precision and adaptability.
By understanding the fundamentals and applying the effective strategies outlined, businesses can unlock significant performance gains, harnessing the power of MPC to enhance their operations.
資料ダウンロード
QCD管理受発注クラウド「newji」は、受発注部門で必要なQCD管理全てを備えた、現場特化型兼クラウド型の今世紀最高の受発注管理システムとなります。
ユーザー登録
受発注業務の効率化だけでなく、システムを導入することで、コスト削減や製品・資材のステータス可視化のほか、属人化していた受発注情報の共有化による内部不正防止や統制にも役立ちます。
NEWJI DX
製造業に特化したデジタルトランスフォーメーション(DX)の実現を目指す請負開発型のコンサルティングサービスです。AI、iPaaS、および先端の技術を駆使して、製造プロセスの効率化、業務効率化、チームワーク強化、コスト削減、品質向上を実現します。このサービスは、製造業の課題を深く理解し、それに対する最適なデジタルソリューションを提供することで、企業が持続的な成長とイノベーションを達成できるようサポートします。
製造業ニュース解説
製造業、主に購買・調達部門にお勤めの方々に向けた情報を配信しております。
新任の方やベテランの方、管理職を対象とした幅広いコンテンツをご用意しております。
お問い合わせ
コストダウンが利益に直結する術だと理解していても、なかなか前に進めることができない状況。そんな時は、newjiのコストダウン自動化機能で大きく利益貢献しよう!
(β版非公開)