- お役立ち記事
- Fundamentals of modeling technology using metal 3D printers, technology to improve manufacturing speed and high precision
Fundamentals of modeling technology using metal 3D printers, technology to improve manufacturing speed and high precision
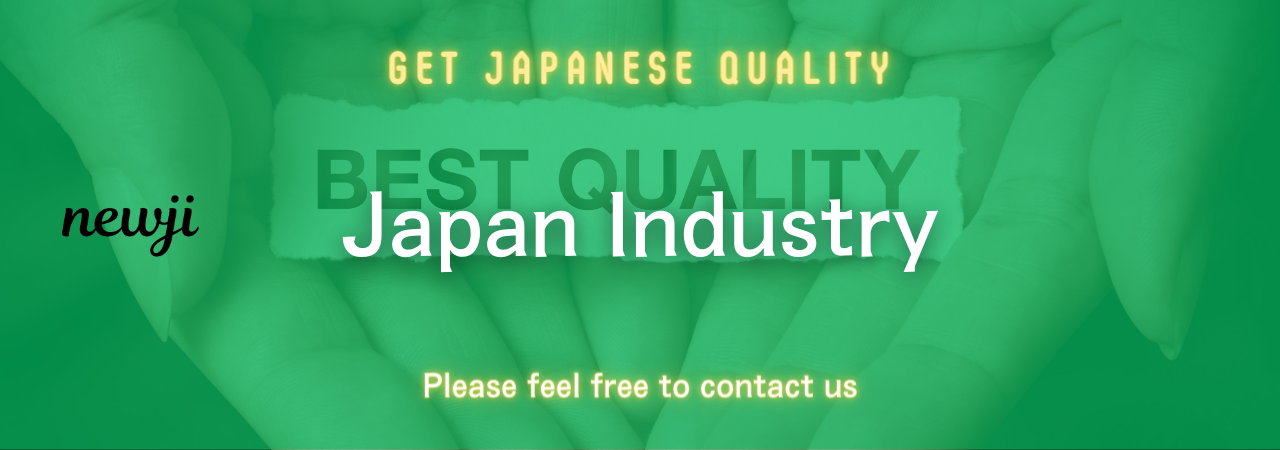
Metal 3D printing has become a groundbreaking technology in the field of manufacturing, driving innovations across various industries.
Its ability to produce complex parts with high precision and reduced material waste sets it apart from traditional manufacturing methods.
But to fully appreciate its potential, one must understand the fundamentals of modeling technology and the strategies used to improve manufacturing speed and precision.
目次
Understanding Metal 3D Printing
Metal 3D printing, also known as additive manufacturing, involves creating three-dimensional metal objects from digital models.
This process builds objects layer by layer, allowing for intricate designs that are difficult or impossible to achieve with conventional methods.
The typical metal 3D printing process might involve several steps, including designing the model, preparing it for printing, layering the material, and finally post-processing the finished product.
Several types of technology fall under the umbrella of metal 3D printing, including Selective Laser Melting (SLM), Direct Metal Laser Sintering (DMLS), Electron Beam Melting (EBM), and Binder Jetting.
Each method has unique applications, materials, and benefits depending on the specifics of the project and industry requirements.
The Importance of Modeling Technology
The foundation of any successful 3D printing endeavor is a robust digital model.
Modeling technology is the backbone of the 3D printing process, as it dictates the structure, dimensions, and tolerances of the final product.
Some common software tools used for creating digital models are CAD (Computer-Aided Design) programs such as SolidWorks, AutoCAD, and Fusion 360.
Designing a model for metal 3D printing requires careful consideration of factors like structural integrity, heat distribution during printing, and potential stress points.
Advanced modeling technology enables engineers to simulate these physical effects in a virtual environment, optimizing designs before the actual printing process begins.
This not only ensures the quality of the final product but also minimizes the risk of costly mistakes and wasted materials.
Improving Manufacturing Speed
Speed is a significant factor in any manufacturing environment, and metal 3D printing is no different.
Enhancing the speed of metal 3D printing involves addressing several components of the process, from reducing the design and testing time to increasing the printing speed itself.
One key strategy is to optimize the printing process through parallelization.
Modern metal 3D printers can incorporate multiple lasers or electron beams working simultaneously to increase the production rate.
This method allows different sections of a part to be printed at the same time, significantly reducing the build time.
Another approach involves improving the software algorithms that control printing.
By refining how the printer interprets digital models and manages layers, manufacturers can reduce time-consuming errors and adjustments.
Additionally, the development of quicker-curing binders and materials that sinter at lower temperatures can also contribute to faster production times.
Material Considerations
The choice of material has a considerable impact on the speed of metal 3D printing.
Different metals have varying melting points and cooling rates, which can affect how quickly a part can be printed.
For instance, aluminum and titanium are often favored for their lower weight and faster processing times compared to denser materials like steel or nickel-based alloys.
Developments in material science continue to introduce new alloys that are specifically designed for the 3D printing process.
These innovations can lead to materials that print faster without compromising on the mechanical properties of the finished product.
Achieving High Precision
Achieving high precision in metal 3D printing is essential for producing components that meet strict industrial standards.
Precision can influence a part’s function, its fit within a larger assembly, and its durability.
One method to enhance precision is the use of advanced calibration and control systems within the printer.
These systems ensure that each layer is deposited with incredible accuracy, maintaining the correct dimensions throughout the print process.
Supporting structures are also vital for maintaining precision in complex parts.
These structures prevent warping or shifting during printing, ensuring the part maintains its intended shape and dimensions.
While supportive structures are often removed in the post-processing phase, their design and implementation are crucial during the modeling stage.
Post-processing techniques like surface finishing, heat treatment, and machining can further refine the precision of a 3D printed part.
These processes address any imperfections and fine-tune the part to meet exact specifications.
Quality Control and Testing
To maintain high precision, rigorous quality control and testing protocols are essential.
Non-destructive testing (NDT) methods can inspect the structural integrity of the 3D printed components without damaging them.
Techniques like X-ray computed tomography (CT) scans, ultrasonic testing, or laser scanning ensure that internal and external features meet the desired criteria.
Moreover, real-time monitoring technologies are increasingly incorporated into 3D printers.
These systems provide feedback on the quality of each layer as it is printed, allowing manufacturers to make adjustments on-the-fly if any deviations are detected.
The Future of Metal 3D Printing
The future of metal 3D printing promises exciting advancements in both speed and precision.
Researchers and engineers are continuously working to develop smarter printers, better materials, and more efficient processes.
These efforts aim to expand the capabilities of metal 3D printing, making it viable for an even wider range of applications.
As the technology matures, we may see faster printers that are capable of producing larger and more complex components with the same level of detail and accuracy.
Also, integrating artificial intelligence (AI) and machine learning (ML) could further refine modeling and printing processes, improving overall efficiency and product quality.
In summary, the fundamentals of modeling technology in metal 3D printing, coupled with innovations aimed at enhancing speed and precision, are driving the future of manufacturing.
By understanding and embracing these technologies, industries can unlock new potentials, revolutionizing how they approach design, production, and supply chains.
資料ダウンロード
QCD調達購買管理クラウド「newji」は、調達購買部門で必要なQCD管理全てを備えた、現場特化型兼クラウド型の今世紀最高の購買管理システムとなります。
ユーザー登録
調達購買業務の効率化だけでなく、システムを導入することで、コスト削減や製品・資材のステータス可視化のほか、属人化していた購買情報の共有化による内部不正防止や統制にも役立ちます。
NEWJI DX
製造業に特化したデジタルトランスフォーメーション(DX)の実現を目指す請負開発型のコンサルティングサービスです。AI、iPaaS、および先端の技術を駆使して、製造プロセスの効率化、業務効率化、チームワーク強化、コスト削減、品質向上を実現します。このサービスは、製造業の課題を深く理解し、それに対する最適なデジタルソリューションを提供することで、企業が持続的な成長とイノベーションを達成できるようサポートします。
オンライン講座
製造業、主に購買・調達部門にお勤めの方々に向けた情報を配信しております。
新任の方やベテランの方、管理職を対象とした幅広いコンテンツをご用意しております。
お問い合わせ
コストダウンが利益に直結する術だと理解していても、なかなか前に進めることができない状況。そんな時は、newjiのコストダウン自動化機能で大きく利益貢献しよう!
(Β版非公開)