- お役立ち記事
- Fundamentals of motor control technology and key points of control design
月間77,185名の
製造業ご担当者様が閲覧しています*
*2025年2月28日現在のGoogle Analyticsのデータより
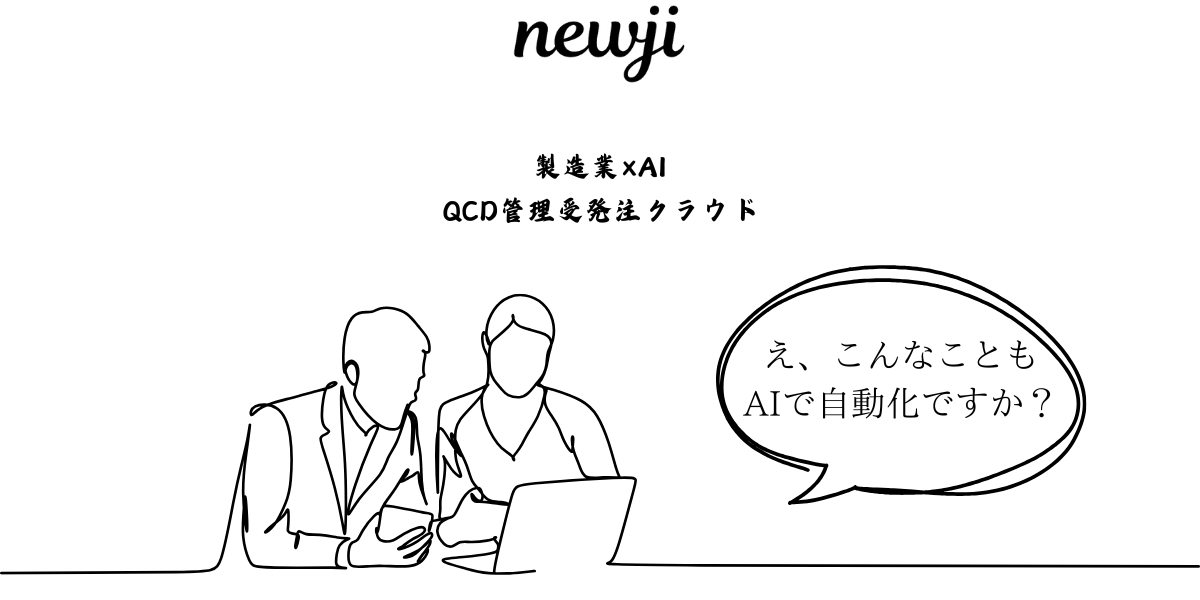
Fundamentals of motor control technology and key points of control design
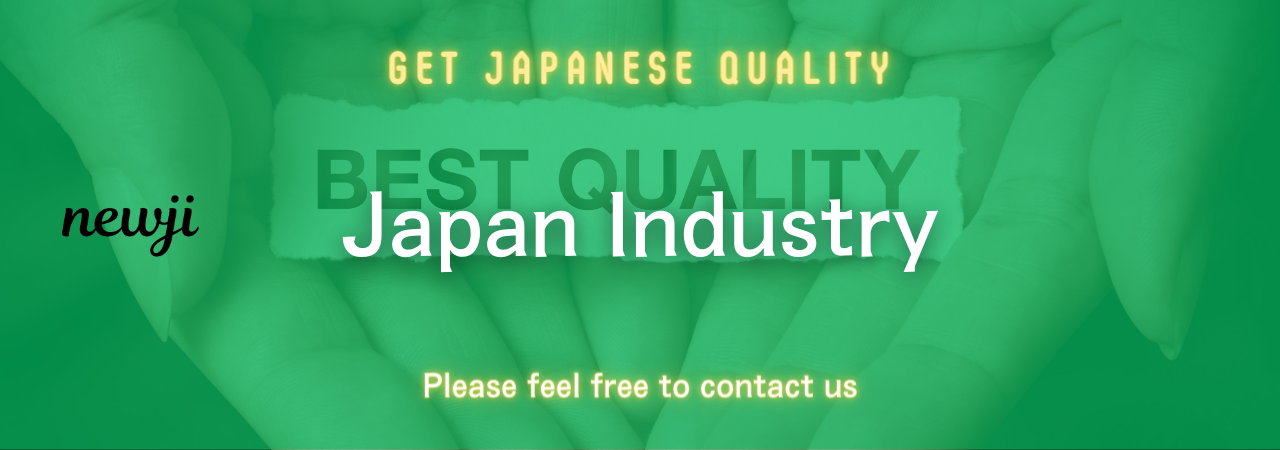
目次
Understanding Motor Control Technology
Motor control technology plays a crucial role in various applications across industries such as manufacturing, automotive, and robotics.
It involves the regulation of motor functions to achieve desired motion or force.
Learning the fundamentals of motor control and its design aspects is essential for creating efficient and reliable systems.
Motor control primarily revolves around the management of electric motors, which are integral components in mechanical systems.
Electric motors convert electrical energy into mechanical energy.
To ensure these motors function optimally, sophisticated control systems are employed.
Types of Electric Motors
Electric motors come in various types, each offering unique advantages for different applications.
The most common types include:
1. **AC Motors**: These are widely used in industries due to their robustness and efficiency.
They operate on alternating current and can be classified into synchronous and asynchronous (induction) motors.
2. **DC Motors**: These motors are powered by direct current and offer high starting torque, making them suitable for applications requiring precise speed control.
They are commonly used in applications like conveyors and elevators.
3. **Stepper Motors**: Ideal for applications requiring precise positioning and repeatability, stepper motors divide a full rotation into a number of steps.
They are prevalent in 3D printers and CNC machines.
4. **Servo Motors**: Known for their precise control of angular or linear position, velocity, and acceleration, servo motors are essential in robotics and automation.
Basic Principles of Motor Control
Effective motor control involves several key principles:
– **Feedback Mechanism**: This is crucial for adjusting the motor operation based on its actual performance compared to the desired output.
Feedback can be achieved through sensors that measure parameters such as speed, position, and torque.
– **Control Loops**: Control systems operate in loops, which can be open or closed.
Closed-loop systems use feedback to self-correct, while open-loop systems do not, relying on predefined instructions.
– **Modulation Techniques**: Techniques such as Pulse Width Modulation (PWM) help in regulating the power supplied to the motors, thus controlling the motor’s speed and direction.
– **Load Characteristics**: Understanding the load characteristics is vital for selecting the appropriate motor and designing an efficient control system.
Factors such as starting torque, running torque, and elasticity of the system must be considered.
Key Points in Control Design
Designing a motor control system involves careful consideration of various factors to ensure it meets the application’s requirements.
Motor Selection
The first step in control design is selecting the appropriate motor based on the application’s needs.
Considerations include:
– **Power and Torque Requirements**: Evaluate both the peak and operational requirements of the application.
Choose a motor with a power rating that can handle not only the operational load but also any potential overload situations.
– **Speed Requirements**: Determine the speed range needed and ensure the motor can deliver it consistently across all operating conditions.
– **Environmental Conditions**: Consider the environment in which the motor will operate.
Factors such as temperature, humidity, and exposure to chemicals should influence the motor choice.
Drive Systems
Selecting the right drive system is essential for controlling motor operation.
Drive systems manage the power and modulate it according to the control signals.
There are various types of drives, including variable frequency drives (VFDs) for AC motors and drive controllers for DC motors.
Control Methodologies
Different methodologies can be employed for controlling motors:
– **Proportional-Integral-Derivative (PID) Control**: A widely used control method, PID control adjusts the motor operation using a continuous feedback loop to minimize errors and achieve precise control.
– **Vector Control (Field-Oriented Control)**: This method is used for AC motors to achieve high performance by controlling the motor’s field orientation.
– **Sensorless Control**: In applications where installing sensors is impractical, advanced algorithms approximate the necessary feedback for control systems without physical sensors.
Implementation Considerations
A successful motor control system design should address the following implementation considerations:
– **System Integration**: Ensure seamless integration with existing systems and controls.
Compatibility with communication protocols and networking capabilities are vital for modern applications.
– **Safety Features**: Incorporate necessary safety features such as emergency stops, overload protection, and fail-safes to protect both the motor and the system.
– **Energy Efficiency**: Optimize the system to minimize energy consumption without sacrificing performance.
Consider using energy-efficient components and employing smart control algorithms.
– **Scalability and Flexibility**: Design with future expansions and modifications in mind to adapt to evolving technology and application requirements.
The Future of Motor Control Technology
As industries move towards smarter and more automated solutions, motor control technology continues to evolve.
Recent advancements in digital control systems, artificial intelligence, and IoT have opened new possibilities for enhanced precision and efficiency in motor control systems.
Future trends include:
– **Integrated Smart Features**: Incorporation of sensors and monitoring tools within motors for real-time diagnostics and proactive maintenance.
– **Machine Learning and AI**: Implementing algorithms that learn and adapt to optimize motor control based on historical data and performance analysis.
– **Wireless Control Systems**: Offering more flexible and less intrusive options for controls with advancements in wireless technology.
In conclusion, understanding the fundamentals and design aspects of motor control technology is crucial for engineers and developers involved in creating efficient, reliable, and future-ready motor systems.
By considering motor types, control principles, and crucial design factors, professionals can harness the full potential of motor control to drive innovation in various applications.
資料ダウンロード
QCD管理受発注クラウド「newji」は、受発注部門で必要なQCD管理全てを備えた、現場特化型兼クラウド型の今世紀最高の受発注管理システムとなります。
ユーザー登録
受発注業務の効率化だけでなく、システムを導入することで、コスト削減や製品・資材のステータス可視化のほか、属人化していた受発注情報の共有化による内部不正防止や統制にも役立ちます。
NEWJI DX
製造業に特化したデジタルトランスフォーメーション(DX)の実現を目指す請負開発型のコンサルティングサービスです。AI、iPaaS、および先端の技術を駆使して、製造プロセスの効率化、業務効率化、チームワーク強化、コスト削減、品質向上を実現します。このサービスは、製造業の課題を深く理解し、それに対する最適なデジタルソリューションを提供することで、企業が持続的な成長とイノベーションを達成できるようサポートします。
製造業ニュース解説
製造業、主に購買・調達部門にお勤めの方々に向けた情報を配信しております。
新任の方やベテランの方、管理職を対象とした幅広いコンテンツをご用意しております。
お問い合わせ
コストダウンが利益に直結する術だと理解していても、なかなか前に進めることができない状況。そんな時は、newjiのコストダウン自動化機能で大きく利益貢献しよう!
(β版非公開)