- お役立ち記事
- Fundamentals of new FMEA techniques, effective procedures, and application to trouble prevention
月間77,185名の
製造業ご担当者様が閲覧しています*
*2025年2月28日現在のGoogle Analyticsのデータより
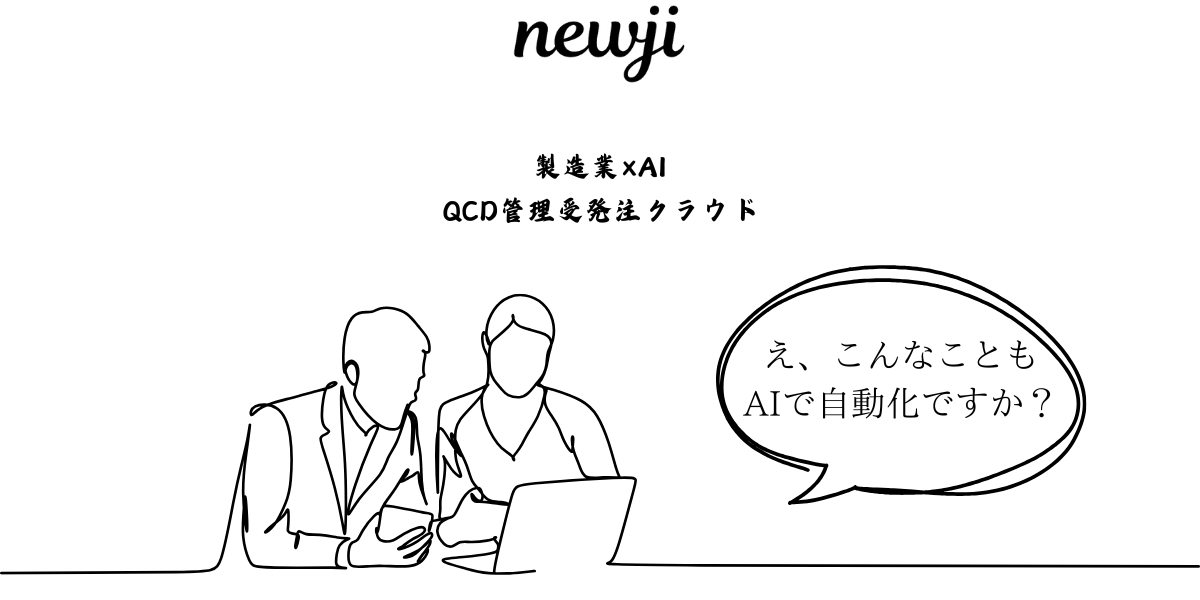
Fundamentals of new FMEA techniques, effective procedures, and application to trouble prevention
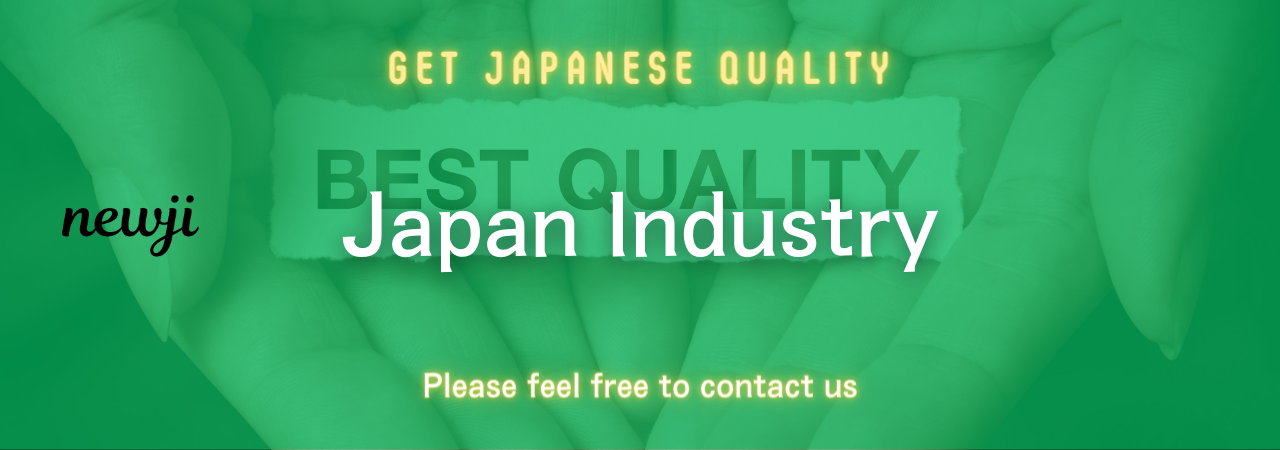
目次
Introduction to FMEA Techniques
Failure Modes and Effects Analysis (FMEA) is a systematic approach for identifying potential failures in products or processes and understanding their impact.
Originally developed in the aerospace industry, it has become an essential tool across various sectors, including automotive, manufacturing, and healthcare.
With evolving technologies and methodologies, new FMEA techniques have emerged that enhance its effectiveness and application in trouble prevention.
Understanding the Basics of FMEA
FMEA operates by examining potential failure modes within a system and assessing their effects.
It helps organizations prioritize their resources to mitigate risks that have the most significant impact.
Traditional FMEA involves creating a detailed list of possible failures, their causes, and potential effects, after which a team rates the severity, occurrence, and detection of each failure mode.
Severity, Occurrence, and Detection
These three parameters help evaluate risks associated with each failure mode:
– **Severity**: Measures the seriousness of the failure’s potential effect.
– **Occurrence**: Assesses the frequency of the failure.
– **Detection**: Evaluates the likelihood of detecting the failure before it reaches the customer.
Each factor is assigned a numerical value, and their product forms the Risk Priority Number (RPN), which assists in prioritizing issues.
New Techniques in FMEA
While the core principles of FMEA remain the same, new methodologies have evolved to enhance its efficiency and adaptability to modern industries.
Functional FMEA
Functional FMEA focuses on a system’s functions rather than its components.
It allows for a broader perspective and is particularly useful when dealing with complex systems.
By understanding what functions a product or process is intended to perform, teams can identify failures based on operational requirements rather than individual parts.
FMEA-MSR (Monitoring and System Response)
Monitoring and System Response (MSR) is an approach integrated into FMEA to incorporate real-time feedback and monitoring systems.
FMEA-MSR evaluates the system’s ability to monitor its performance and respond to potential failures autonomously.
It is especially beneficial for systems that rely on continuous operation, allowing dynamic and adaptive responses to occurring issues.
Hybrid FMEA
Hybrid FMEA combines traditional methods with other risk assessment tools such as Fault Tree Analysis (FTA) and Hazard and Operability Studies (HAZOP).
This integration allows for a more detailed and thorough analysis, catering to both functional and component-level issues.
Hybrid FMEA provides a comprehensive risk assessment that addresses different dimensions of system vulnerabilities.
Effective Procedures for Implementing FMEA
Implementing an FMEA requires a well-structured approach to ensure its success and effectiveness.
1. Form a Cross-Functional Team
The first step is assembling a diverse team with expertise in different aspects of the product or process.
This team should include engineers, designers, quality assurance professionals, and other relevant stakeholders.
The diversity ensures a comprehensive analysis as each team member brings unique insights into potential failure modes.
2. Define the Scope and Objectives
Clearly define the scope of the FMEA to focus efforts on specific systems, processes, or products.
Setting clear objectives helps in staying on track and ensures that the analysis aligns with the organization’s risk management goals.
3. Collect and Analyze Data
Gather historical data on previous failures and existing systems to provide a baseline for analysis.
Data collection assists in creating accurate failure mode scenarios and helps predict future possibilities.
4. Identify Potential Failure Modes
Conduct brainstorming sessions to list all potential failure modes, causes, and effects.
Encourage participation from all team members, as collaborative insight often uncovers overlooked aspects.
5. Analyze and Prioritize Risks
Use the RPN or any updated tools from new techniques to rank and prioritize identified risks.
Focus on high-priority risks that have severe consequences or higher likelihood of occurrence.
6. Develop and Implement Action Plans
Based on the analysis, create strategies to mitigate, eliminate, or transfer identified risks.
Interventions could include design changes, process modifications, or enhanced monitoring systems.
Implement the chosen actions, and ensure timely monitoring and evaluation.
Application of FMEA to Trouble Prevention
FMEA is not just a reactive tool but also plays a crucial role in proactive trouble prevention.
Product Design and Development
During the design phase, FMEA helps identify and address potential issues before products are manufactured.
This proactive analysis reduces costly recalls and redesigns, ensuring product reliability from the outset.
Manufacturing and Process Improvement
In manufacturing, FMEA highlights process vulnerabilities and opportunities for efficiency improvements.
By addressing potential failures in production processes, companies can reduce downtime and improve quality assurance.
Maintenance and Reliability Engineering
FMEA informs preventive maintenance strategies by pointing out critical systems prone to failure.
Regularly updated FMEA documentation ensures that maintenance efforts focus on areas of highest risk, optimizing resource allocation.
Conclusion
The fundamentals of FMEA remain a cornerstone in risk management and product development.
As industries evolve, new techniques offer enhanced flexibility and deeper insights, making FMEA an indispensable tool in trouble prevention.
By implementing effective procedures and leveraging new methodologies, organizations can ensure product reliability, minimize risks, and enhance overall efficiency.
資料ダウンロード
QCD管理受発注クラウド「newji」は、受発注部門で必要なQCD管理全てを備えた、現場特化型兼クラウド型の今世紀最高の受発注管理システムとなります。
ユーザー登録
受発注業務の効率化だけでなく、システムを導入することで、コスト削減や製品・資材のステータス可視化のほか、属人化していた受発注情報の共有化による内部不正防止や統制にも役立ちます。
NEWJI DX
製造業に特化したデジタルトランスフォーメーション(DX)の実現を目指す請負開発型のコンサルティングサービスです。AI、iPaaS、および先端の技術を駆使して、製造プロセスの効率化、業務効率化、チームワーク強化、コスト削減、品質向上を実現します。このサービスは、製造業の課題を深く理解し、それに対する最適なデジタルソリューションを提供することで、企業が持続的な成長とイノベーションを達成できるようサポートします。
製造業ニュース解説
製造業、主に購買・調達部門にお勤めの方々に向けた情報を配信しております。
新任の方やベテランの方、管理職を対象とした幅広いコンテンツをご用意しております。
お問い合わせ
コストダウンが利益に直結する術だと理解していても、なかなか前に進めることができない状況。そんな時は、newjiのコストダウン自動化機能で大きく利益貢献しよう!
(β版非公開)