- お役立ち記事
- Fundamentals of noise and vibration in fluid machinery, noise and vibration reduction measures, and examples
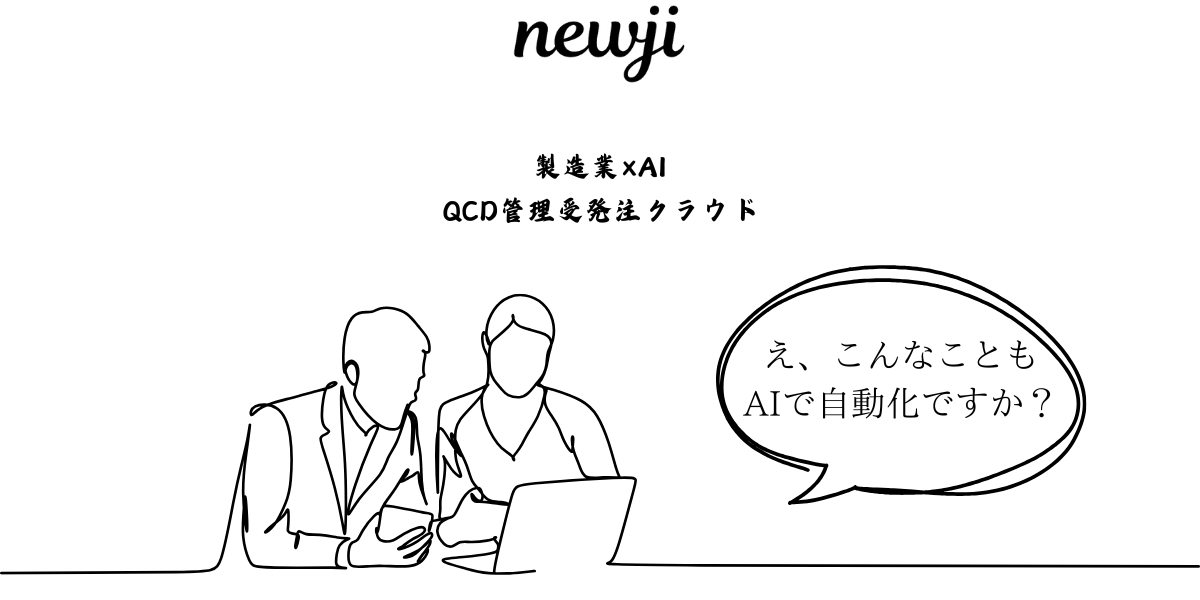
Fundamentals of noise and vibration in fluid machinery, noise and vibration reduction measures, and examples
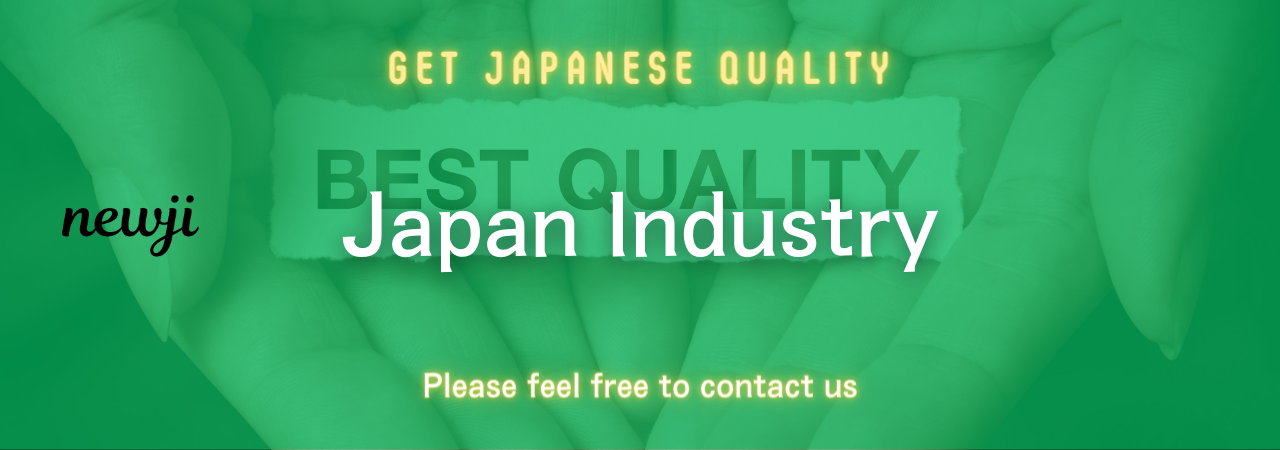
目次
Understanding Noise and Vibration in Fluid Machinery
When we talk about fluid machinery, it encompasses a wide range of devices, such as pumps, compressors, fans, and turbines, all of which play crucial roles in various industries.
These machines are integral to processes in sectors like oil and gas, water treatment, and power generation.
Despite their numerous benefits, these machines often come with the disadvantages of noise and vibration, which can pose challenges in terms of maintenance and comfort.
Understanding the fundamentals of noise and vibration is essential for mitigating these issues.
Noise in fluid machinery generally originates from different sources, such as mechanical vibrations, fluid dynamics, and acoustic emissions.
Mechanical vibrations are caused by unbalanced rotating parts, misalignments, and loosened components.
Fluid dynamics-related noise, often referred to as flow-induced noise, results from turbulence, cavitation, and pressure fluctuations within the machinery.
Additionally, acoustic emissions occur due to fast reciprocating movements and interactions within components.
Vibration, on the other hand, is an oscillatory motion that can be felt or seen in various parts of a machine.
Typically caused by imbalances and resonances, vibrations can lead to wear and tear, reducing the machinery’s efficiency and lifespan.
Understanding these basic concepts is the first step towards developing effective noise and vibration reduction strategies.
Importance of Noise and Vibration Control
The significance of controlling noise and vibration in fluid machinery cannot be overstated.
Excessive noise can have adverse effects on workers’ health, including hearing loss and increased stress levels.
In industrial settings, regulations often mandate specific noise level limits to ensure workers’ safety and wellbeing.
Beyond the impact on human health, noise can cause disturbances in surrounding environments, particularly in residential areas or quiet zones.
Vibration control is equally important, as unchecked vibrations can lead to machinery failure, costly downtime, and expensive repairs.
Prolonged exposure to vibrations can damage structural components and compromise the integrity of the machine.
Thus, effective control of noise and vibration not only extends the life and performance of the equipment but also aligns with health, safety, and environmental standards.
Noise and Vibration Reduction Measures
To reduce noise and vibration in fluid machinery, a combination of strategies and technologies is employed.
The first step is to ensure that machines are correctly installed and maintained.
Proper maintenance reduces mechanical wear and ensures that components like bearings, bolts, and seals are in good condition.
Regular inspection and alignment checks help in minimizing the root causes of noise and vibration.
Advanced design techniques also contribute significantly to noise and vibration reduction.
For instance, using computer-aided design (CAD) software, engineers can simulate fluid flow and identify potential noise issues before physical production.
This proactive approach allows for adjustments in design to mitigate problems.
Another effective method is the use of damping materials and vibration isolators.
Damping materials, such as rubber pads, foams, and elastomers, absorb vibrational energy and reduce its transmission to other parts.
Vibration isolation systems, including mounts and pads, prevent the transfer of vibrations from the machine to its surroundings.
Additionally, aerodynamic and hydrodynamic optimization in components, like impellers and blades, helps decrease flow-induced vibration and noise.
Techniques such as cutting-edge flow control devices, streamlined component shapes, and smooth surfaces reduce turbulence and cavitation impacts.
Increasingly, active noise and vibration control technologies are being incorporated.
These technologies utilize sensors and actuators to dynamically adjust and counteract noise and vibrations.
Real-time adjustments help maintain optimal performance under varying operational conditions.
Examples of Noise and Vibration Reduction in Practice
Several companies have implemented noise and vibration reduction measures successfully.
One example is a manufacturing plant that invested in soundproof enclosures for their fluid machinery.
These enclosures not only reduced noise levels significantly but also enhanced the aesthetic appeal of the facility.
Moreover, the plant installed vibration monitoring systems that allowed for real-time diagnostics and preventive maintenance.
By addressing issues before they escalated, they minimized downtime and repair costs.
In another case, a water treatment facility tackled cavitation and flow-induced noise by redesigning their pump system.
They employed computational fluid dynamics (CFD) to analyze flow patterns and pressure distributions, leading to design alterations that reduced noise by over 30%.
This adjustment not only lowered noise levels but also improved pump efficiency.
The wind energy sector has also embraced noise and vibration reduction measures.
Wind turbines, notorious for their characteristic noise, have seen improvements through the integration of serrated blade designs and optimized blade pitch angles.
These changes help minimize aerodynamic noise, making wind farms more harmonious with their environments.
Conclusion
Noise and vibration are inherent challenges in fluid machinery, but with a thorough understanding of their causes, industries can implement effective reduction strategies.
By prioritizing maintenance, using damping materials, optimizing designs, and adopting active control technologies, companies can enhance their machinery’s performance and safety.
With these measures in place, it’s possible to create quieter, more efficient, and longer-lasting fluid machinery, benefiting both industries and the communities they serve.
資料ダウンロード
QCD調達購買管理クラウド「newji」は、調達購買部門で必要なQCD管理全てを備えた、現場特化型兼クラウド型の今世紀最高の購買管理システムとなります。
ユーザー登録
調達購買業務の効率化だけでなく、システムを導入することで、コスト削減や製品・資材のステータス可視化のほか、属人化していた購買情報の共有化による内部不正防止や統制にも役立ちます。
NEWJI DX
製造業に特化したデジタルトランスフォーメーション(DX)の実現を目指す請負開発型のコンサルティングサービスです。AI、iPaaS、および先端の技術を駆使して、製造プロセスの効率化、業務効率化、チームワーク強化、コスト削減、品質向上を実現します。このサービスは、製造業の課題を深く理解し、それに対する最適なデジタルソリューションを提供することで、企業が持続的な成長とイノベーションを達成できるようサポートします。
オンライン講座
製造業、主に購買・調達部門にお勤めの方々に向けた情報を配信しております。
新任の方やベテランの方、管理職を対象とした幅広いコンテンツをご用意しております。
お問い合わせ
コストダウンが利益に直結する術だと理解していても、なかなか前に進めることができない状況。そんな時は、newjiのコストダウン自動化機能で大きく利益貢献しよう!
(Β版非公開)