- お役立ち記事
- Fundamentals of permanent magnet synchronous motor control and application to control design
月間76,176名の
製造業ご担当者様が閲覧しています*
*2025年3月31日現在のGoogle Analyticsのデータより
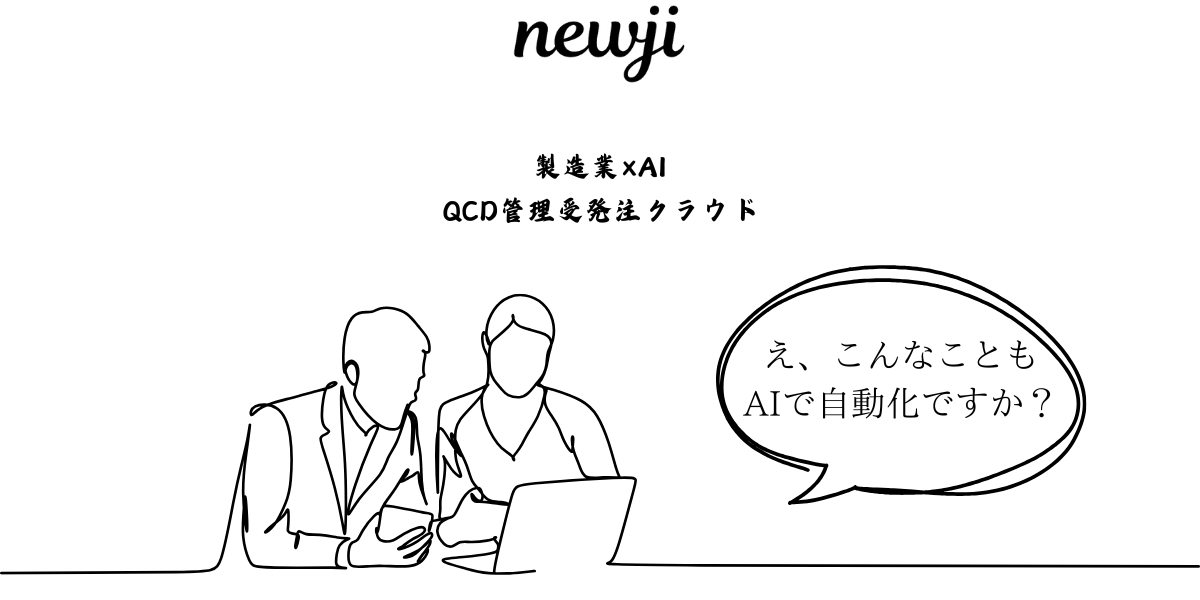
Fundamentals of permanent magnet synchronous motor control and application to control design
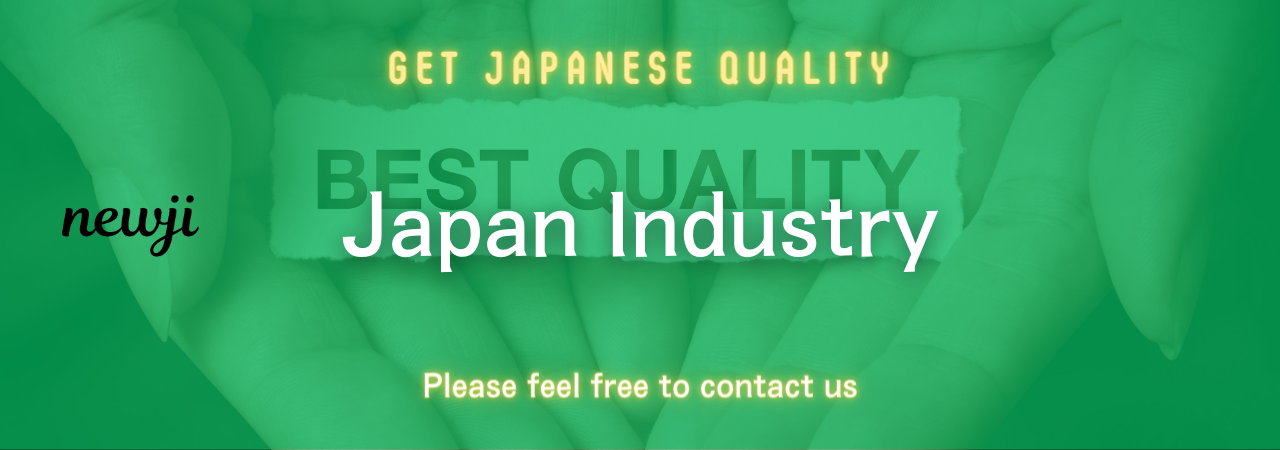
目次
Introduction to Permanent Magnet Synchronous Motors
Permanent Magnet Synchronous Motors (PMSMs) are gaining traction in various applications due to their efficiency, reliability, and robust performance characteristics.
These motors operate on the principle of magnetic fields generated by permanent magnets interacting with the stator’s magnetic field to produce torque.
PMSMs are widely used in household appliances, electric vehicles, and industrial machines, making them a pivotal component in modern engineering applications.
Understanding the Basic Structure of PMSMs
The core structure of a PMSM consists of two main parts: the rotor and the stator.
The rotor contains permanent magnets, which are positioned in such a way that they generate a strong magnetic field.
The stator, on the other hand, is wound with coils of wire, which, when energized with current, create a rotating magnetic field that interacts with the permanent magnets in the rotor.
This interaction is responsible for generating torque and motion in the motor.
The Role of Permanent Magnets
Permanent magnets in PMSMs play a critical role as they eliminate the need for an external excitation field.
This leads to a more efficient design as there is no need for brushes or slip rings, which are common in other motor types.
As a result, PMSMs are characterized by less maintenance and longer operational lifespan, making them ideal for strategic applications where reliability is essential.
Control Strategies for PMSMs
Controlling a PMSM involves managing the torque, speed, and position of the motor to achieve desired performance outcomes.
Efficient control is achieved through various control strategies, such as Field-Oriented Control (FOC) and Direct Torque Control (DTC).
These strategies are employed to ensure the motor operates smoothly, efficiently, and at optimal performance levels.
Field-Oriented Control (FOC)
FOC is a control strategy that aligns the stator current vector with the rotor flux vector.
This method allows for independent control of the motor’s torque and magnetic flux, leading to improved efficiency and performance.
FOC is particularly beneficial in applications requiring precise speed and position control, such as robotics and CNC machines.
Direct Torque Control (DTC)
DTC is another popular control method that directly controls the motor’s torque and flux.
Unlike FOC, DTC does not require a rotor position sensor, making it less complex and more cost-effective.
DTC delivers high dynamic performance and is typically used in applications where torque control is prioritized, such as in conveyor systems.
Application Areas of PMSMs
PMSMs are highly versatile and are employed across a myriad of industries owing to their high efficiency and performance consistency.
Electric Vehicles
PMSMs are extensively used in electric vehicles due to their ability to provide high torque at low speeds and efficiency at high speeds.
This makes them ideal for traction applications, improving the overall performance and range of electric vehicles.
Industrial Automation
In industrial settings, PMSMs are used in automation systems that require precise and efficient motion control.
They find applications in conveyor belts, robotic arms, and manufacturing equipment where constant speed and low maintenance are critical.
Household Appliances
In household appliances, PMSMs are present in washing machines, refrigerators, and air conditioners.
Their low noise and high efficiency make them suitable for home environments where operational noise and energy consumption are concerns.
Renewable Energy
PMSMs also play a crucial role in renewable energy systems, particularly in wind turbines and solar trackers.
In these applications, PMSMs contribute to converting renewable energy into electric power with high efficiency and reliability.
Challenges in PMSM Control Design
While PMSMs offer numerous advantages, designing control systems for these motors presents several challenges.
Non-linear Characteristics
PMSMs exhibit non-linear behavior due to magnetic saturation and temperature variations.
This non-linearity poses significant control challenges, requiring advanced control strategies and algorithms to maintain optimal performance.
Sensorless Control
Sensorless control strategies are often sought to reduce costs and improve reliability.
However, designing control systems that maintain performance without position feedback from sensors adds complexity to the control design process.
Harmonic Distortion
Harmonic distortion in the electrical supply can lead to undesirable performance characteristics, such as vibrations and losses.
Addressing these issues requires sophisticated control algorithms and filtering techniques to ensure smooth motor operation.
Conclusion
Permanent Magnet Synchronous Motors are integral to a variety of modern applications due to their efficiency and reliability.
They continue to be developed and refined to meet the increasingly demanding requirements of industrial automation, electric mobility, and renewable energy.
Understanding their fundamentals and applications can help engineers design more effective control systems, optimizing the performance and reliability of these pivotal motors for years to come.
資料ダウンロード
QCD管理受発注クラウド「newji」は、受発注部門で必要なQCD管理全てを備えた、現場特化型兼クラウド型の今世紀最高の受発注管理システムとなります。
ユーザー登録
受発注業務の効率化だけでなく、システムを導入することで、コスト削減や製品・資材のステータス可視化のほか、属人化していた受発注情報の共有化による内部不正防止や統制にも役立ちます。
NEWJI DX
製造業に特化したデジタルトランスフォーメーション(DX)の実現を目指す請負開発型のコンサルティングサービスです。AI、iPaaS、および先端の技術を駆使して、製造プロセスの効率化、業務効率化、チームワーク強化、コスト削減、品質向上を実現します。このサービスは、製造業の課題を深く理解し、それに対する最適なデジタルソリューションを提供することで、企業が持続的な成長とイノベーションを達成できるようサポートします。
製造業ニュース解説
製造業、主に購買・調達部門にお勤めの方々に向けた情報を配信しております。
新任の方やベテランの方、管理職を対象とした幅広いコンテンツをご用意しております。
お問い合わせ
コストダウンが利益に直結する術だと理解していても、なかなか前に進めることができない状況。そんな時は、newjiのコストダウン自動化機能で大きく利益貢献しよう!
(β版非公開)