- お役立ち記事
- Fundamentals of permanent magnet synchronous motor design and how to effectively utilize machine learning data for motor design
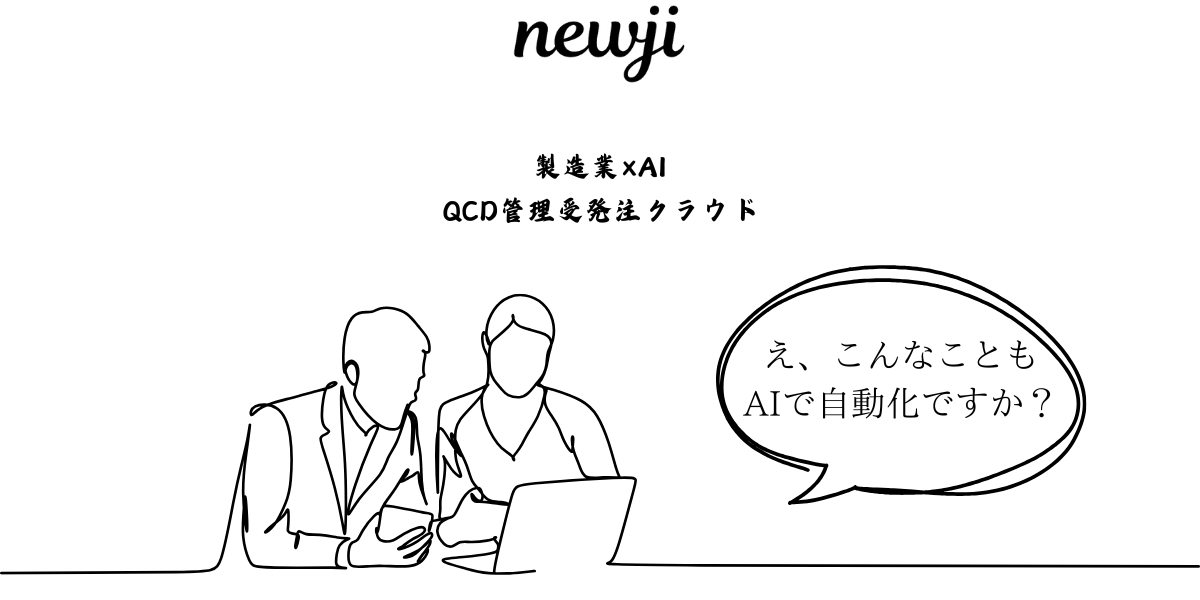
Fundamentals of permanent magnet synchronous motor design and how to effectively utilize machine learning data for motor design
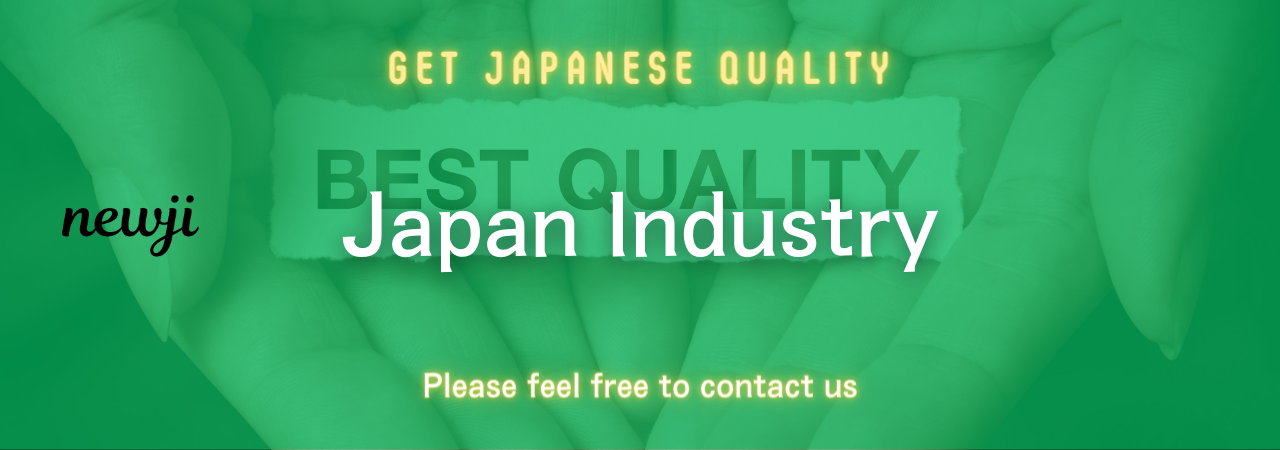
目次
Understanding Permanent Magnet Synchronous Motors (PMSMs)
Permanent Magnet Synchronous Motors, commonly known as PMSMs, are a type of electric motor widely used in various applications due to their high efficiency, compact size, and reliability.
These motors work based on the interaction between a permanent magnet’s magnetic field and the stator windings’ rotating field.
They are favored in industries such as automotive, aerospace, and robotics, where performance and efficiency are paramount.
Components of PMSMs
PMSMs consist of several key components, each playing a vital role in their operation.
The primary components include the rotor, which houses the permanent magnets, and the stator, which contains the windings.
Together, they create the necessary electromagnetic forces to produce torque and rotation.
In PMSMs, the rotor does not contain windings; instead, it relies on the magnetic field generated by the permanent magnets.
This design reduces energy losses associated with rotor current flow, making PMSMs more efficient than other motor types.
Working Principle of PMSMs
The basic principle behind PMSMs is the synchronous interaction between the rotor and stator.
When an alternating current (AC) is supplied to the stator windings, it creates a rotating magnetic field.
This magnetic field interacts with the rotor’s permanent magnets, producing torque that drives the motor.
The speed of PMSMs is proportional to the frequency of the AC supply.
As the name suggests, the motor maintains synchronous operation, meaning the rotor speed matches the rotating field speed.
This synchronous characteristic is a critical advantage, particularly in applications where precise speed control is crucial.
Design Considerations for PMSMs
Designing a Permanent Magnet Synchronous Motor requires careful consideration of several factors to achieve optimal performance.
Key aspects include rotor design, stator winding configuration, magnet selection, and thermal management.
Rotor Design
The rotor’s design is critical, as it houses the permanent magnets.
Engineers must consider factors such as the magnet material, shape, and arrangement to maximize magnetic flux and torque production.
Common materials used for permanent magnets include Neodymium Iron Boron (NdFeB) and Samarium Cobalt (SmCo), known for their high energy density.
The rotor must also be balanced to minimize vibration and reduce wear on bearings, ensuring smooth operation over time.
Techniques like finite element analysis (FEA) are often employed to simulate and optimize rotor designs.
Stator Winding Configuration
The stator winding configuration significantly impacts a PMSM’s performance and efficiency.
Designers must choose between single-layer and double-layer windings, considering factors such as power density and thermal conductivity.
Additionally, winding arrangements like distributed or concentrated windings play a role in torque ripple, electromagnetic noise, and overall efficiency.
Selecting the appropriate configuration is crucial for achieving the desired motor characteristics.
Magnet Selection
The selection of permanent magnets is critical to the PMSM design process.
Magnets with high energy density offer greater torque and efficiency but may come at a higher cost.
Conversely, lower-cost magnets may require compromises in performance.
Factors such as operating temperature, demagnetization risk, and cost must be weighed when selecting the appropriate magnet material for a given application.
Thermal Management
Thermal management is vital to ensure a PMSM’s longevity and performance.
Excessive heat can lead to the degradation of materials, reduced efficiency, and potentially premature failure.
Designers must incorporate effective cooling methods, such as air or liquid cooling, to dissipate heat generated during operation.
These strategies help maintain temperature within safe limits and extend the motor’s lifespan.
Incorporating Machine Learning for PMSM Design
With advancements in machine learning, the design and optimization of Permanent Magnet Synchronous Motors have reached new levels of sophistication.
Machine learning techniques can help analyze vast datasets, identify patterns, and make predictions to optimize motor design efficiently.
Data Collection and Analysis
The first step in leveraging machine learning for PMSM design is data collection.
Engineers gather performance data from existing motor designs, test results, and simulations.
This data serves as the foundation for training machine learning models to understand complex relationships between design parameters and performance.
Once collected, data analysis techniques like clustering and regression help identify patterns and correlations that inform design decisions.
This analysis can reveal insights that may not be apparent through traditional design methods.
Optimization Algorithms
Machine learning utilizes optimization algorithms to fine-tune motor designs.
Commonly used algorithms include Genetic Algorithms (GA), Particle Swarm Optimization (PSO), and Bayesian optimization.
These algorithms explore design spaces efficiently, searching for optimal combinations of parameters that meet the desired performance criteria.
By employing these algorithms, designers can achieve better results in terms of efficiency, torque, and thermal management than traditional approaches.
Predictive Modeling
Predictive modeling with machine learning offers the ability to forecast a motor’s performance based on design parameters.
This capability allows engineers to experiment with different configurations before physical prototypes are built.
By reducing the need for multiple iteration cycles and prototyping, predictive modeling significantly cuts down development time and cost.
Additionally, it enhances the accuracy of performance predictions, leading to more reliable motor designs.
Conclusion
Permanent Magnet Synchronous Motors are a cornerstone of modern industry, delivering high efficiency and precise speed control in a variety of applications.
Understanding their design and operation is key to harnessing their full potential.
By incorporating machine learning techniques, engineers can optimize PMSM designs more effectively, resulting in improved performance and reduced development costs.
This synergy between traditional engineering and cutting-edge technology paves the way for innovation in electric motor design, driving advancements in efficiency and sustainability.
資料ダウンロード
QCD調達購買管理クラウド「newji」は、調達購買部門で必要なQCD管理全てを備えた、現場特化型兼クラウド型の今世紀最高の購買管理システムとなります。
ユーザー登録
調達購買業務の効率化だけでなく、システムを導入することで、コスト削減や製品・資材のステータス可視化のほか、属人化していた購買情報の共有化による内部不正防止や統制にも役立ちます。
NEWJI DX
製造業に特化したデジタルトランスフォーメーション(DX)の実現を目指す請負開発型のコンサルティングサービスです。AI、iPaaS、および先端の技術を駆使して、製造プロセスの効率化、業務効率化、チームワーク強化、コスト削減、品質向上を実現します。このサービスは、製造業の課題を深く理解し、それに対する最適なデジタルソリューションを提供することで、企業が持続的な成長とイノベーションを達成できるようサポートします。
オンライン講座
製造業、主に購買・調達部門にお勤めの方々に向けた情報を配信しております。
新任の方やベテランの方、管理職を対象とした幅広いコンテンツをご用意しております。
お問い合わせ
コストダウンが利益に直結する術だと理解していても、なかなか前に進めることができない状況。そんな時は、newjiのコストダウン自動化機能で大きく利益貢献しよう!
(Β版非公開)