- お役立ち記事
- Fundamentals of permanent magnet synchronous motor design and practical points for optimal motor design
Fundamentals of permanent magnet synchronous motor design and practical points for optimal motor design
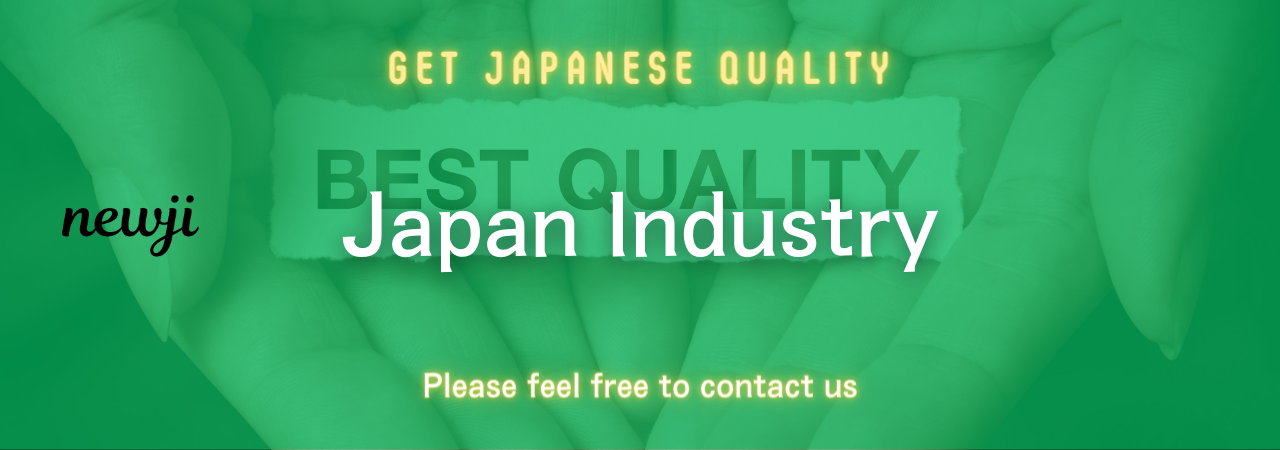
目次
Introduction to Permanent Magnet Synchronous Motors (PMSMs)
Permanent Magnet Synchronous Motors, often abbreviated as PMSMs, are widely used in various applications due to their high efficiency and high power density.
These motors are utilized in areas such as electric vehicles, industrial machinery, and wind power generation.
Understanding the fundamentals of their design and the practical points for achieving optimal motor performance can prove essential for engineers looking to maximize their effectiveness.
Basic Principles of PMSM Design
Magnetic Materials and Their Impact
At the heart of PMSM design is the choice of magnetic materials.
Permanent magnets are used in these motors, which are typically composed of rare earth materials like Neodymium or Samarium Cobalt.
These materials provide strong magnetic fields, which are crucial for the motor’s efficiency and torque output.
The selection of the right magnetic material impacts the motor’s performance, cost, and operational limits.
Stator and Rotor Structure
The design of the stator and rotor is critical in PMSM.
The stator is usually equipped with three-phase windings, which create a rotating magnetic field when AC voltage is applied.
The rotor, embedded with permanent magnets, interacts with this magnetic field, which results in motion.
The number of poles, the winding arrangement, and the slot design of the stator must be carefully considered to ensure efficient interaction with the rotor.
Importance of the Air Gap
The air gap between the stator and rotor should be minimized as much as possible since it affects the motor’s torque production and efficiency.
A smaller air gap increases the magnetic field intensity and improves motor performance, but it should be designed with precision to avoid mechanical reliability issues.
Practical Considerations for Optimal Motor Design
Maximizing Efficiency
Efficiency is key in motor design, especially for applications like electric vehicles, where energy conservation is paramount.
Factors like winding resistance, core losses, and magnet losses need to be minimized.
Advanced cooling techniques and the use of novel materials can help in dissipating heat effectively, thus maintaining higher efficiency levels.
Thermal Management
PMSM’s performance can be significantly affected by temperature variations.
Effective thermal management involves selecting materials with good thermal conductivity and implementing cooling mechanisms like air or liquid cooling.
Thermal simulations during the design phase can help predict heat distribution and inform better design choices.
Control Strategies
To achieve optimal performance, implementing advanced control strategies like Vector Control or Field-Oriented Control (FOC) is essential.
These control methods ensure the motor operates at its maximum efficiency by optimally controlling the current supplied to the motor.
Precision control can substantially lower power losses and improve torque output.
Scalability and Adaptability
When designing PMSMs, it is crucial to ensure their scalability and adaptability to different applications and power ratings.
Customizable design elements like the number of poles and winding configurations make it easier to tailor the motor for specific requirements without extensive redesign efforts.
Advanced Techniques in PMSM Optimization
Finite Element Analysis (FEA)
Finite Element Analysis is a powerful tool used to simulate the magnetic, thermal, and structural behavior of motors under various conditions.
By assessing different design parameters through simulations, engineers can predict performance outcomes and optimize them prior to physical prototyping.
Machine Learning and AI Enhancement
The use of machine learning and artificial intelligence in motor design allows for pattern recognition and predictive analytics.
These technologies can streamline the iteration process and rapidly suggest design improvements based on large datasets of previous motor designs.
Challenges and Future Outlook
Though PMSM offers numerous advantages, challenges such as high manufacturing costs, dependence on rare earth materials, and sophisticated design requirements remain.
Ongoing research into alternative materials and manufacturing techniques is vital to reduce dependence on expensive resources.
Emerging technologies like additive manufacturing and recycling methods for rare earth magnets hold promise for the future of PMSM design.
As the demand for energy-efficient motors grows, PMSMs remain at the forefront of innovation, driving changes in renewable energy and transportation sectors.
Understanding the core principles and practical considerations for PMSM design can significantly impact the performance outcomes and operational efficiency of the applications they power.
As technology continues to evolve, so too will the methods and materials that define permanent magnet synchronous motor design.
資料ダウンロード
QCD調達購買管理クラウド「newji」は、調達購買部門で必要なQCD管理全てを備えた、現場特化型兼クラウド型の今世紀最高の購買管理システムとなります。
ユーザー登録
調達購買業務の効率化だけでなく、システムを導入することで、コスト削減や製品・資材のステータス可視化のほか、属人化していた購買情報の共有化による内部不正防止や統制にも役立ちます。
NEWJI DX
製造業に特化したデジタルトランスフォーメーション(DX)の実現を目指す請負開発型のコンサルティングサービスです。AI、iPaaS、および先端の技術を駆使して、製造プロセスの効率化、業務効率化、チームワーク強化、コスト削減、品質向上を実現します。このサービスは、製造業の課題を深く理解し、それに対する最適なデジタルソリューションを提供することで、企業が持続的な成長とイノベーションを達成できるようサポートします。
オンライン講座
製造業、主に購買・調達部門にお勤めの方々に向けた情報を配信しております。
新任の方やベテランの方、管理職を対象とした幅広いコンテンツをご用意しております。
お問い合わせ
コストダウンが利益に直結する術だと理解していても、なかなか前に進めることができない状況。そんな時は、newjiのコストダウン自動化機能で大きく利益貢献しよう!
(Β版非公開)