- お役立ち記事
- Fundamentals of permanent magnet synchronous motor design technology and key points for high efficiency
月間76,176名の
製造業ご担当者様が閲覧しています*
*2025年3月31日現在のGoogle Analyticsのデータより
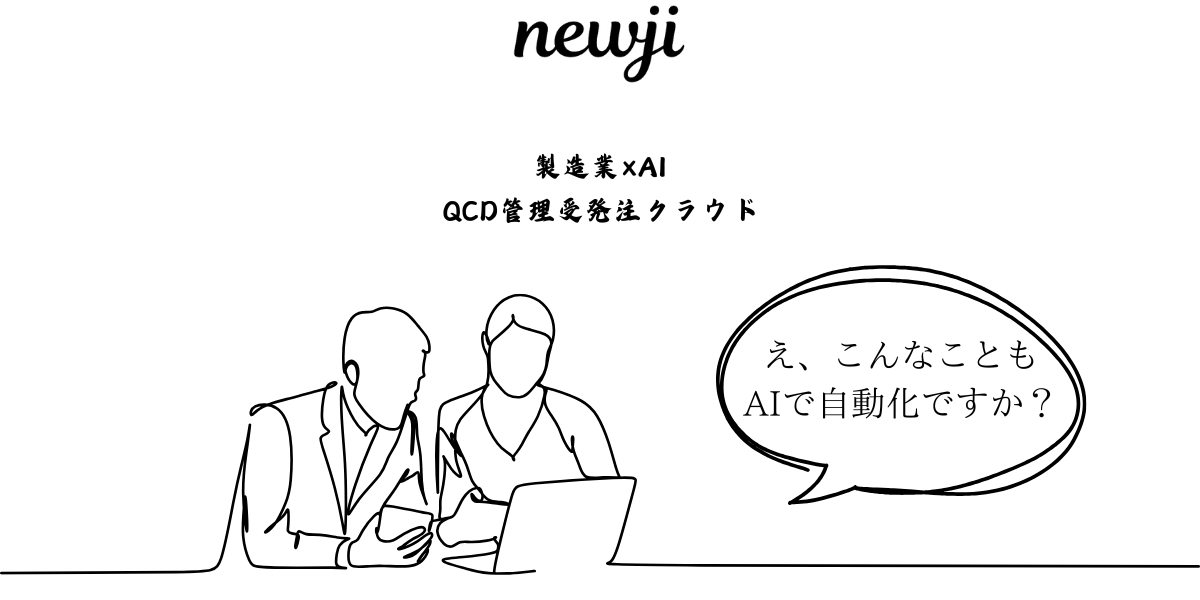
Fundamentals of permanent magnet synchronous motor design technology and key points for high efficiency
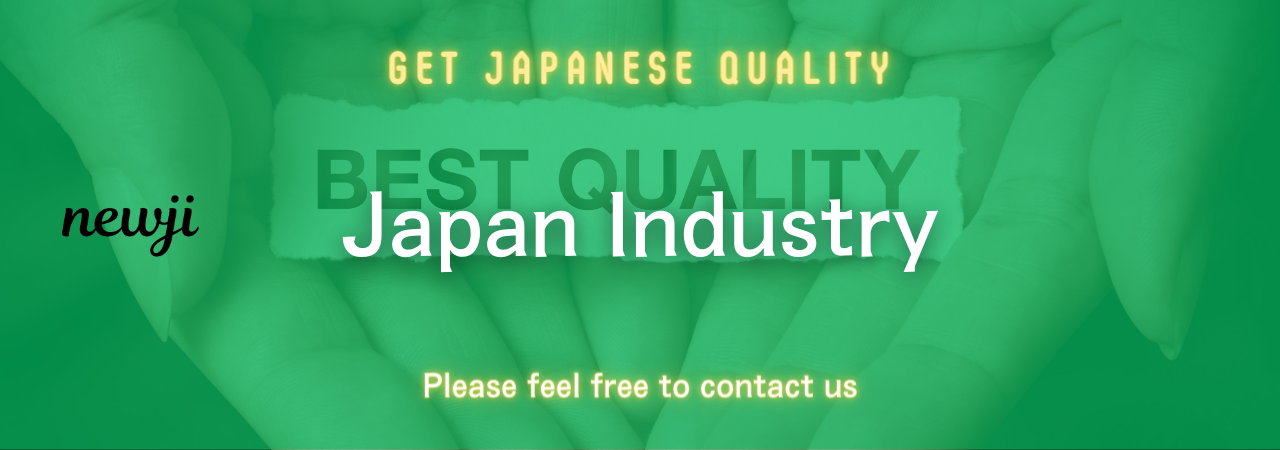
目次
Understanding Permanent Magnet Synchronous Motors
Permanent magnet synchronous motors (PMSMs) are a type of electric motor that utilizes permanent magnets in the rotor, as opposed to traditional motors that use coils to magnetize the core.
These motors are known for their efficiency, reliability, and ability to generate a high torque-to-inertia ratio.
This makes them ideal for a range of applications, including industrial machines, electric vehicles, and domestic appliances.
The fundamental advantage of using permanent magnets in the rotor is that they provide a constant magnetic field, which results in higher efficiency compared to induction motors.
Because PMSMs don’t rely on the slip necessary for inducing current in the rotor, they experience less energy loss.
Furthermore, they tend to have simpler construction and reduced maintenance costs with fewer components like brushes or commutators, which wear out over time in brushed DC motors.
Key Components of PMSM Design
Rotor and Stator Configuration
The rotor and stator are critical components in the design of a PMSM.
The rotor houses the permanent magnets, which can be arranged in various configurations, including surface-mounted and interior-mounted designs.
Surface-mounted rotors have magnets affixed directly to the rotor surface, which simplifies manufacturing and reduces cost.
Interior-mounted rotors have embedded magnets, which improve torque density and mechanical strength.
The stator, the stationary part of the motor, contains windings that create a rotating magnetic field when supplied with alternating current.
The interaction between the rotor’s magnetic field and the stator’s magnetic field generates torque, propelling the motor.
Magnet Material Selection
Choosing the right magnet material is crucial for optimal motor performance.
Common materials include ferrite, neodymium iron boron (NdFeB), and samarium cobalt (SmCo).
Neodymium magnets are the most powerful and are preferred for high-performance applications due to their strength and compact size.
However, they can be costly and sensitive to high temperatures, which may require additional cooling solutions.
SmCo magnets, while slightly less powerful, offer excellent temperature resistance, making them suitable for applications in harsh environments.
Cooling Systems
Effective heat management is essential for the reliable operation of PMSMs.
As motors operate, they generate heat due to electrical losses in the stator windings and friction.
Excessive heat can demagnetize the rotor magnets and damage the windings, thereby reducing efficiency and motor life.
Various cooling methods are integrated into motor designs, such as air cooling, liquid cooling, or adding fans and heat sinks to dissipate heat actively.
Control Systems
Proper control of PMSMs significantly impacts their efficiency and torque delivery.
Vector control and field-oriented control (FOC) are common techniques used to manage voltage and current to the motor for precise speed and torque control.
FOC, in particular, allows independent control of the motor’s magnetic field and torque, ensuring optimized performance across various operating conditions.
Designing for High Efficiency
Optimizing Electromagnetic Design
To achieve high efficiency in PMSMs, optimizing the electromagnetic design is crucial.
This involves minimizing electrical losses, such as copper losses in the stator windings and iron losses in the core material.
Using high-quality materials with low resistivity and loss characteristics can greatly enhance motor performance.
Furthermore, advanced simulation tools can be employed to model and analyze the electromagnetic fields, allowing engineers to refine the geometry of the stator slots and winding configurations.
Minimizing Losses and Enhancing Performance
Efforts to minimize losses play a significant role in enhancing the performance of PMSMs.
This includes reducing harmonic losses which arise from non-linear loads and abrupt changes in current.
One effective way to do this is by selecting an optimal number of poles and utilizing fractional slot windings.
These strategies help in reducing unwanted harmonics and improving overall motor efficiency.
Additionally, efficient control algorithms can be implemented to minimize energy consumption, especially during low-load and transient conditions.
Applications and Advancements
Wide Range of Applications
Due to their high efficiency and robust performance, PMSMs find applications across various industries.
In the automotive sector, they are widely used in electric and hybrid vehicles for propulsion, taking advantage of their high torque output and compact size.
In industrial applications, they drive pumps, compressors, and fans due to their ability to maintain consistent speed under variable load conditions.
Furthermore, home appliances like washing machines and air conditioners also utilize PMSMs for their quiet operation and energy efficiency.
Recent Technological Advancements
With ongoing advancements in material science and manufacturing technologies, the design and performance of PMSMs continue to improve.
Developments in high-temperature magnet materials and more sophisticated manufacturing techniques are paving the way for lighter motors with even greater power density.
Additionally, the integration of IoT and smart control systems is enhancing the functionality of PMSMs, enabling predictive maintenance and real-time performance monitoring.
Conclusion
The design of permanent magnet synchronous motors holds immense potential for high efficiency and performance across various applications.
By focusing on key elements such as magnetic materials, cooling systems, and advanced control strategies, engineers can optimize these motors for diverse needs.
As technology progresses, the evolution of PMSM designs will continue, paving the way for innovative applications and cleaner, more sustainable energy solutions.
Understanding the fundamentals and staying abreast of advancements will provide engineers and designers with the tools necessary to unlock the full potential of PMSMs.
資料ダウンロード
QCD管理受発注クラウド「newji」は、受発注部門で必要なQCD管理全てを備えた、現場特化型兼クラウド型の今世紀最高の受発注管理システムとなります。
ユーザー登録
受発注業務の効率化だけでなく、システムを導入することで、コスト削減や製品・資材のステータス可視化のほか、属人化していた受発注情報の共有化による内部不正防止や統制にも役立ちます。
NEWJI DX
製造業に特化したデジタルトランスフォーメーション(DX)の実現を目指す請負開発型のコンサルティングサービスです。AI、iPaaS、および先端の技術を駆使して、製造プロセスの効率化、業務効率化、チームワーク強化、コスト削減、品質向上を実現します。このサービスは、製造業の課題を深く理解し、それに対する最適なデジタルソリューションを提供することで、企業が持続的な成長とイノベーションを達成できるようサポートします。
製造業ニュース解説
製造業、主に購買・調達部門にお勤めの方々に向けた情報を配信しております。
新任の方やベテランの方、管理職を対象とした幅広いコンテンツをご用意しております。
お問い合わせ
コストダウンが利益に直結する術だと理解していても、なかなか前に進めることができない状況。そんな時は、newjiのコストダウン自動化機能で大きく利益貢献しよう!
(β版非公開)