- お役立ち記事
- Fundamentals of PID control and application to control system design
Fundamentals of PID control and application to control system design
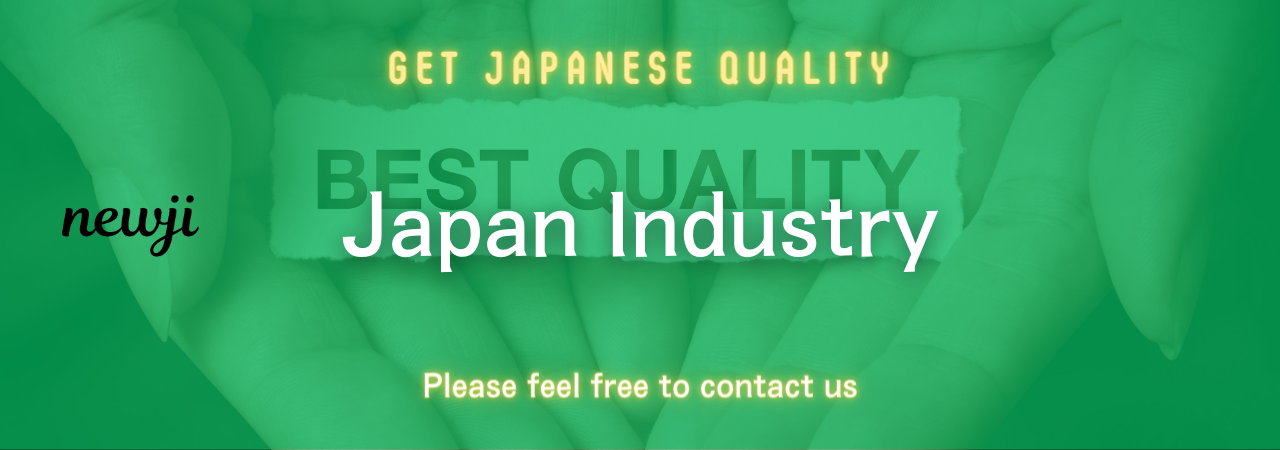
目次
Understanding PID Control
PID control stands for Proportional-Integral-Derivative control, which is a vital concept in the realm of control systems engineering.
It represents a control loop feedback mechanism that is widely used in industrial control systems.
The main objective of PID control is to maintain the desired output of a system by minimizing the error between the system’s setpoint and its actual output.
This is achieved by adjusting the inputs to the process.
Understanding the individual components of PID control is crucial to grasping how the system works.
Proportional Control
The Proportional (P) component of PID control correlates to the present error value.
This means that the response is proportional to the error.
The larger the error, the larger the proportional response.
However, simply using proportional control can lead to a steady state error, meaning that the system might not reach the exact setpoint.
Proportional control is most effective for large, rapid changes and can drive the system’s output towards the setpoint.
Integral Control
Integral (I) control addresses the accumulation of past errors.
Its goal is to eliminate the residual steady-state error that occurs with pure proportional control.
The integral controller integrates the error over time, and its output is proportional to the accumulated error.
This allows the system to eventually reach the exact setpoint by adjusting for past discrepancies.
Despite its advantages, integral control can introduce new issues, such as overshooting the setpoint or producing system oscillations.
Derivative Control
The Derivative (D) component predicts future error based on the rate of change of the error.
It responds to the speed at which the system deviates from the setpoint, by applying a damping effect.
Derivative control helps to provide stability and improve the transient response of the system.
It is particularly effective at reducing overshoot and settling time.
However, its sensitivity to noise can be a drawback, as it may amplify rapid changes in error resulting from disturbances or noise in the system.
Combining PID Components
When combined, the PID controller uses all three components to produce a control signal that aims to drive the system error towards zero.
Adjusting the proportional, integral, and derivative gains (KP, KI, KD) allows engineers to fine-tune the system response.
By tweaking these parameters, it is possible to control the speed and stability of a process.
For instance, increasing the proportional gain will decrease the rise time but may increase overshoot.
Enhancing the integral gain will eliminate steady-state error but could lengthen the settling time.
Meanwhile, adjusting the derivative gain can improve system stability and reduce overshoot.
Applications of PID Control
PID control is foundational to many applications across different industries.
Its versatility and effectiveness make it a go-to choice for industrial control tasks.
Temperature Control
In industrial settings, maintaining precise temperature is crucial for quality and efficiency.
PID controllers are employed in systems like ovens, furnaces, and reactors to ensure that the temperature remains at a setpoint.
By adjusting heaters or coolers based on the PID output, businesses can ensure consistent product quality.
Speed Control
Another common application of PID controllers is in DC motor speed control.
By regulating the voltage applied to the motor, the PID controller ensures that the motor maintains the desired speed despite load variations or changes in the system.
This is critical in manufacturing where precise motor speed is necessary for the production of quality items.
Position Control
PID control is equally vital in position control systems, such as those used in robotics and CNC machinery.
In these systems, the position of a component must be controlled precisely.
The PID controller adjusts to ensure the component reaches and maintains the desired position quickly and accurately.
Level Control
In processes where maintaining the level of a liquid or other substance is important, PID controllers are often used.
For example, in chemical processing, it is crucial to maintain specific fluid levels in tanks to ensure consistent reaction rates and product quality.
Designing a PID Control System
Creating a PID control system requires a methodical approach to ensure the system’s accuracy and stability.
Tuning the PID Controller
Tuning a PID controller involves selecting the appropriate values for the proportional, integral, and derivative gains.
There are several methods to tune these parameters, including manual tuning, software-based simulation, and automatic tuning processes.
Manual tuning requires the engineer to adjust the gains while observing system performance.
Ziegler-Nichols is a well-known heuristic tuning method that provides parameter suggestions based on the system’s response to specific test inputs.
Simulation tools can offer a more sophisticated approach to tuning, allowing engineers to model system dynamics and predict optimal parameter settings.
Testing and Validation
Once a PID controller is designed and tuned, it must undergo testing and validation within the real system.
This phase ensures that the controller behaves as expected under various operating conditions.
Testing can reveal unforeseen issues like actuator saturation or noise sensitivity, necessitating further refinements.
Validation ensures that the controller not only meets design specifications but also achieves the desired levels of performance and robustness in real-world applications.
The Future of PID Control
Even as new technologies emerge, PID control remains a robust tool in control system design.
Research continues into advancing tuning methods and integrating artificial intelligence to enhance PID control systems.
As the demand for precision and efficiency in industrial processes grows, PID control will continue to adapt and offer solutions that meet evolving technological needs.
資料ダウンロード
QCD調達購買管理クラウド「newji」は、調達購買部門で必要なQCD管理全てを備えた、現場特化型兼クラウド型の今世紀最高の購買管理システムとなります。
ユーザー登録
調達購買業務の効率化だけでなく、システムを導入することで、コスト削減や製品・資材のステータス可視化のほか、属人化していた購買情報の共有化による内部不正防止や統制にも役立ちます。
NEWJI DX
製造業に特化したデジタルトランスフォーメーション(DX)の実現を目指す請負開発型のコンサルティングサービスです。AI、iPaaS、および先端の技術を駆使して、製造プロセスの効率化、業務効率化、チームワーク強化、コスト削減、品質向上を実現します。このサービスは、製造業の課題を深く理解し、それに対する最適なデジタルソリューションを提供することで、企業が持続的な成長とイノベーションを達成できるようサポートします。
オンライン講座
製造業、主に購買・調達部門にお勤めの方々に向けた情報を配信しております。
新任の方やベテランの方、管理職を対象とした幅広いコンテンツをご用意しております。
お問い合わせ
コストダウンが利益に直結する術だと理解していても、なかなか前に進めることができない状況。そんな時は、newjiのコストダウン自動化機能で大きく利益貢献しよう!
(Β版非公開)