- お役立ち記事
- Fundamentals of PID control and effective use points of PID tuning method
Fundamentals of PID control and effective use points of PID tuning method
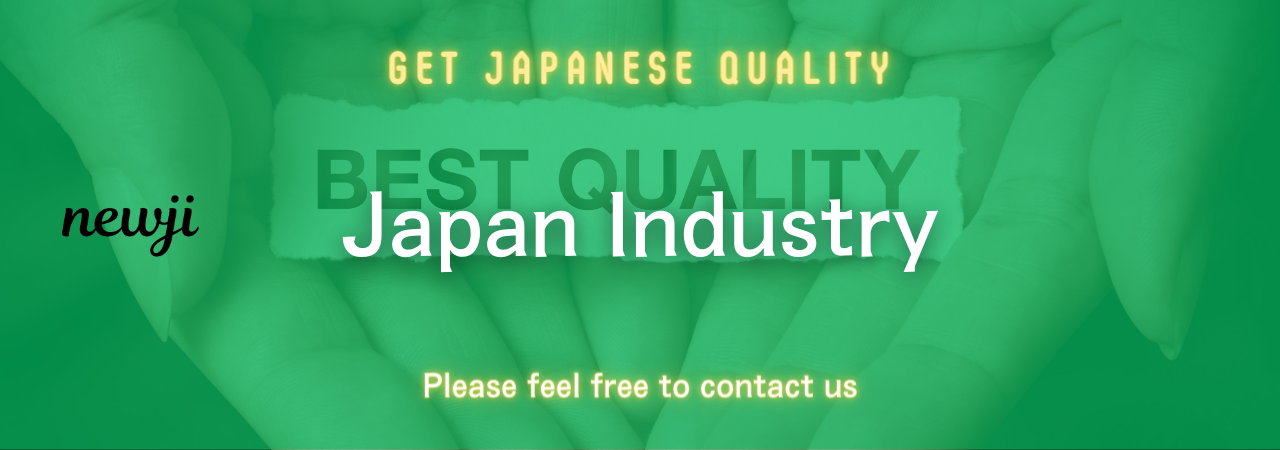
目次
Understanding PID Control Basics
PID control, which stands for Proportional-Integral-Derivative control, is a common feedback loop mechanism widely used in industrial control systems.
Its primary purpose is to maintain a system’s desired output by minimizing the error between the process variable (actual output) and the set point (desired output).
PID controllers are simple yet powerful tools for achieving precise control in various applications ranging from temperature regulation to motor speed control.
Proportional Control
The proportional control part of PID is often denoted as ‘P.’
It determines the controller’s output based on the current error value.
The proportional term is calculated by multiplying the error by a constant known as the proportional gain (Kp).
A higher proportional gain results in a system that responds quickly to errors, but it can also lead to instability if too large.
The primary advantage of proportional control is its simplicity and immediate effect on reducing the error.
However, solely relying on proportional control might not eliminate steady-state errors completely, especially in systems with constant disturbances.
Integral Control
The integral control part, represented by ‘I,’ accounts for past errors.
It integrates the error over time, providing a cumulative sum that affects the controller’s output.
The integral term is scaled by the integral gain (Ki).
Integral control is instrumental in eliminating persistent errors, as it continues to adjust until the accumulated error is minimal.
However, excessive integral action can lead to an overshoot and potentially destabilize the system due to its tendency to accumulate errors over time.
Derivative Control
The derivative control component, indicated as ‘D,’ reacts to the rate of error change.
It predicts future error based on its current rate of change, achieving this by differentiating the error over time.
The derivative gain (Kd) scales the contribution from this derivative term.
Derivative control adds an anticipatory element to the PID system, which can be helpful in mitigating rapid changes and overshoots.
Too much derivative action, however, can introduce noise sensitivity and oscillations.
Effectiveness of PID Tuning
PID tuning involves adjusting the proportional, integral, and derivative gains to ensure optimal control performance.
Effective tuning helps achieve desired system behaviors such as stability, fast response time, minimal overshoot, and reduced steady-state error.
Common PID Tuning Methods
Several techniques are used to tune PID controllers, each suited for different types of systems and user preferences:
Ziegler-Nichols Method
The Ziegler-Nichols method is one of the most famous heuristic tuning methods.
It involves setting the integral and derivative gains to zero initially and gradually increasing the proportional gain until the system reaches sustained oscillations.
The critical gain and oscillation period derived from this setup are used to determine the optimal PID parameters.
Trial and Error
This method, although simple, requires the user to manually adjust the PID gains while observing the system’s response.
Through experimentation, the gains are finetuned to achieve the desired performance specifications.
Though it can be time-intensive, this approach allows for hands-on understanding and immediate feedback.
Software-Based Optimization
Modern control systems often take advantage of software tools and algorithms that automate the PID tuning process.
These tools simulate the system’s response and adjust the PID parameters accordingly.
This method is efficient and effective for complex systems where manual tuning might be challenging.
Effective Use Points for PID Tuning
To make the most out of PID tuning, keep the following considerations in mind:
Understand the System
Before tuning, it’s crucial to have a thorough understanding of the system being controlled.
This includes the dynamics of the process, potential sources of disturbance, and specific requirements for system performance.
Minimize External Disturbances
Reducing external disturbances like noise and sudden load changes can simplify the tuning process, leading to more accurate PID settings.
Isolating the system during testing can help in achieving this.
Use a Structured Approach
Approaching the tuning process methodically—starting with identifying current system dynamics, then evaluating performance, and systematically adjusting control gains—ensures consistency and repeatability.
Monitor Performance Over Time
Once tuning is performed, continuously monitor the system’s performance to ensure it maintains stability and meets required specifications.
Real-world systems often experience changes, so periodic reevaluation of PID settings may be needed.
Conclusion
PID control’s significance in modern control systems stems from its ability to provide precise and stable control for a variety of applications.
Understanding the fundamentals of proportional, integral, and derivative actions allows for better tuning and enhanced system performance.
By employing structured tuning methods and considering specific system behaviors, engineers can optimize PID parameters to achieve desired control objectives seamlessly.
資料ダウンロード
QCD調達購買管理クラウド「newji」は、調達購買部門で必要なQCD管理全てを備えた、現場特化型兼クラウド型の今世紀最高の購買管理システムとなります。
ユーザー登録
調達購買業務の効率化だけでなく、システムを導入することで、コスト削減や製品・資材のステータス可視化のほか、属人化していた購買情報の共有化による内部不正防止や統制にも役立ちます。
NEWJI DX
製造業に特化したデジタルトランスフォーメーション(DX)の実現を目指す請負開発型のコンサルティングサービスです。AI、iPaaS、および先端の技術を駆使して、製造プロセスの効率化、業務効率化、チームワーク強化、コスト削減、品質向上を実現します。このサービスは、製造業の課題を深く理解し、それに対する最適なデジタルソリューションを提供することで、企業が持続的な成長とイノベーションを達成できるようサポートします。
オンライン講座
製造業、主に購買・調達部門にお勤めの方々に向けた情報を配信しております。
新任の方やベテランの方、管理職を対象とした幅広いコンテンツをご用意しております。
お問い合わせ
コストダウンが利益に直結する術だと理解していても、なかなか前に進めることができない状況。そんな時は、newjiのコストダウン自動化機能で大きく利益貢献しよう!
(Β版非公開)