- お役立ち記事
- Fundamentals of PID control and key points of digital control and parameter tuning
月間77,185名の
製造業ご担当者様が閲覧しています*
*2025年2月28日現在のGoogle Analyticsのデータより
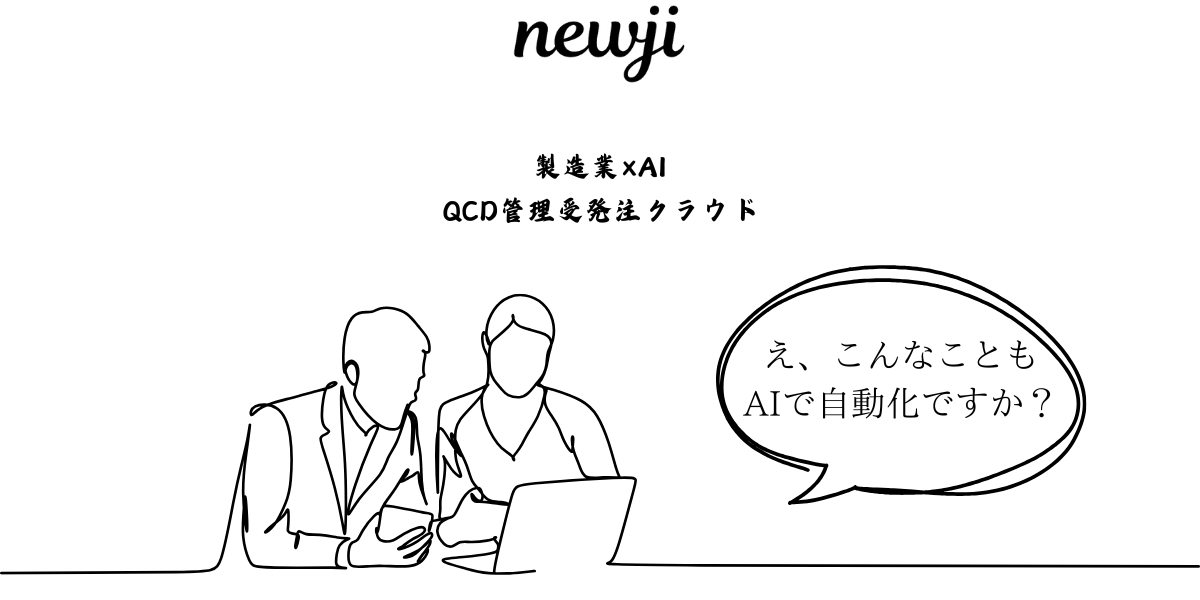
Fundamentals of PID control and key points of digital control and parameter tuning
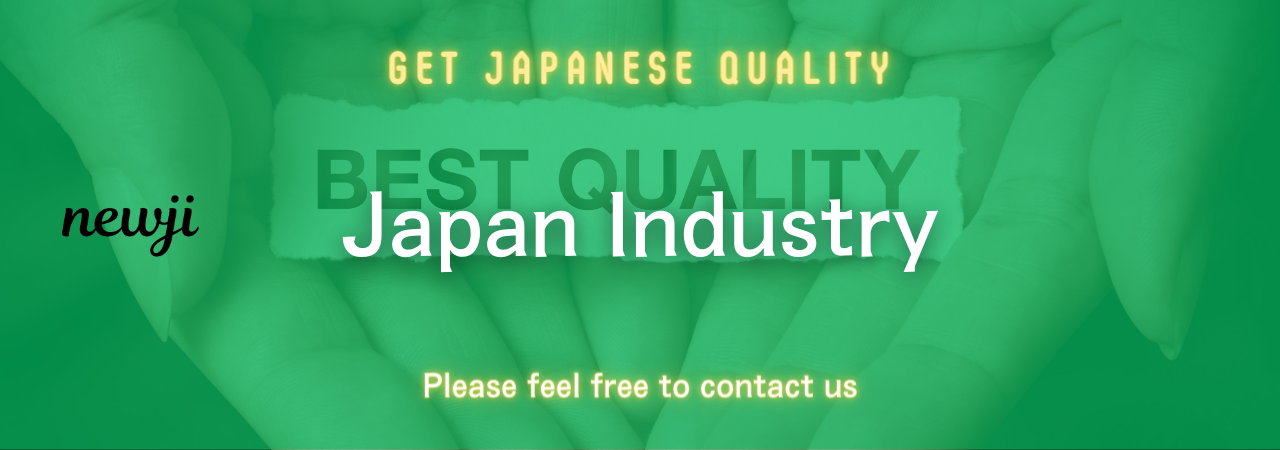
目次
Understanding PID Control
Proportional-Integral-Derivative (PID) control is a widely used control algorithm in various industries, including manufacturing, robotics, and process control.
At its core, PID control aims to maintain a desired output by adjusting a control variable based on three distinct factors: proportional, integral, and derivative.
Each of these components plays a vital role in ensuring the system behaves as expected.
The Proportional Component
The proportional component is responsible for responding to the current error.
Error, in this context, refers to the difference between a process variable’s current value and the desired setpoint.
The proportional component adjusts the control output proportionally to the error magnitude.
In essence, the larger the error, the more significant the response from the proportional component.
This ensures that the system quickly remains within a permissible range of the setpoint.
The Integral Component
The integral component addresses the accumulation of past errors.
In some systems, you might notice that over time, even a steady state error accumulates, preventing the system from achieving the desired setpoint.
The integral component helps eliminate this sustained error by integrating the error over time and making necessary adjustments.
This adjustment ensures that any offset is corrected, leading the process variable to match the setpoint more accurately.
The Derivative Component
The derivative component predicts future behavior based on the rate of error change.
It measures how quickly the error has been changing and responds accordingly.
By doing so, the derivative component can dampen the system’s response to sudden changes, reducing overshoot and minimizing oscillations.
This component helps ensure smoother transitions and prevents the system from becoming unstable.
Getting to Know Digital Control
Digital control plays a crucial role in implementing PID algorithms, especially in modern contexts where computers and microcontrollers are prevalent.
Unlike analog control, digital control involves sampling the process at discrete intervals and processing these samples to make control decisions.
Advantages of Digital Control
One of the primary advantages of digital control is versatility.
Since digital controllers can be programmed, they can be easily adjusted or reconfigured according to system requirements.
Moreover, digital control facilitates data storage, processing, and advanced algorithms like machine learning.
It is inherently resistant to noise and other disturbances, often problematic in analog systems.
Sampling Considerations
A critical aspect of digital control is the sampling frequency.
The frequency at which you sample data significantly impacts system performance.
A low sampling frequency may lead to aliasing, where changes in the process go undetected.
Conversely, a too high sampling frequency can result in excessive computational demands, potentially leading to resource constraints.
Striking the right balance is essential to ensure optimal system performance.
Quantization and Precision
Digital systems quantize continuous signals into discrete values.
This quantization introduces a degree of precision limitation inherent in any digital system.
Higher resolution implies better precision, allowing the digital system to better approximate the continuous signal.
However, increased resolution demands more storage and processing power, so it is essential to balance these factors effectively.
Techniques for Parameter Tuning
Proper PID parameter tuning is crucial to achieving desired control system performance.
Without proper tuning, the PID controller might underperform or even destabilize the system.
Manual Tuning
Manual tuning involves adjusting the proportional, integral, and derivative gains based on experience or established rules of thumb.
This approach requires experimenting with each parameter to understand its effect on the system until an optimal set of gains is determined.
Despite being time-consuming, manual tuning can be effective when the system dynamics are well-understood.
Ziegler-Nichols Method
The Ziegler-Nichols method is a popular heuristic technique for tuning PID controllers.
This method involves setting the integral and derivative gains to zero and increasing the proportional gain until the system oscillates at a constant amplitude.
Once this critical gain is found, specific formulas help determine the integral and derivative gains for desired system performance.
Software-Based Methods
Modern digital control systems often leverage software solutions to automate parameter tuning.
These software tools perform system identification and simulate various configurations to recommend optimal PID gains.
Using algorithms and simulations, they identify the most effective parameter settings, reducing the need for extensive manual adjustments.
Common Challenges and Solutions
While PID control is effective in many applications, it is not without challenges.
Understanding potential pitfalls can help in developing strategies to address them.
System Delay
A considerable challenge in many systems is the inherent delay between the control action and the system response.
This delay can make it difficult for the PID controller to respond appropriately, leading to overshoot or instability.
To counteract this, consider incorporating a predictive element or using an advanced control algorithm that accounts for system delays.
Nonlinearities
Many real-world systems exhibit non-linear behavior, which can complicate PID tuning.
In such cases, linear PID schemes may be insufficient.
One solution involves segmenting the system into linear approximations and tuning each segment separately.
Alternatively, adaptive control strategies can dynamically adjust PID parameters in response to changing system characteristics.
Noise and Disturbances
Noise and disturbances can degrade PID performance, particularly when influencing the measurement signal.
Implementing filtering techniques or enhancing the robustness of the control system can mitigate these effects.
Derivative filtering, in particular, can help ensure the derivative component does not unnecessarily exacerbate noise effects.
Understanding the fundamentals of PID control, digital control intricacies, and parameter tuning techniques can significantly enhance a control system’s effectiveness.
By addressing common challenges and leveraging digital control’s benefits, systems can achieve more precise and stable operations across a range of applications.
資料ダウンロード
QCD管理受発注クラウド「newji」は、受発注部門で必要なQCD管理全てを備えた、現場特化型兼クラウド型の今世紀最高の受発注管理システムとなります。
ユーザー登録
受発注業務の効率化だけでなく、システムを導入することで、コスト削減や製品・資材のステータス可視化のほか、属人化していた受発注情報の共有化による内部不正防止や統制にも役立ちます。
NEWJI DX
製造業に特化したデジタルトランスフォーメーション(DX)の実現を目指す請負開発型のコンサルティングサービスです。AI、iPaaS、および先端の技術を駆使して、製造プロセスの効率化、業務効率化、チームワーク強化、コスト削減、品質向上を実現します。このサービスは、製造業の課題を深く理解し、それに対する最適なデジタルソリューションを提供することで、企業が持続的な成長とイノベーションを達成できるようサポートします。
製造業ニュース解説
製造業、主に購買・調達部門にお勤めの方々に向けた情報を配信しております。
新任の方やベテランの方、管理職を対象とした幅広いコンテンツをご用意しております。
お問い合わせ
コストダウンが利益に直結する術だと理解していても、なかなか前に進めることができない状況。そんな時は、newjiのコストダウン自動化機能で大きく利益貢献しよう!
(β版非公開)