- お役立ち記事
- Fundamentals of PID control and key points of parameter tuning technology
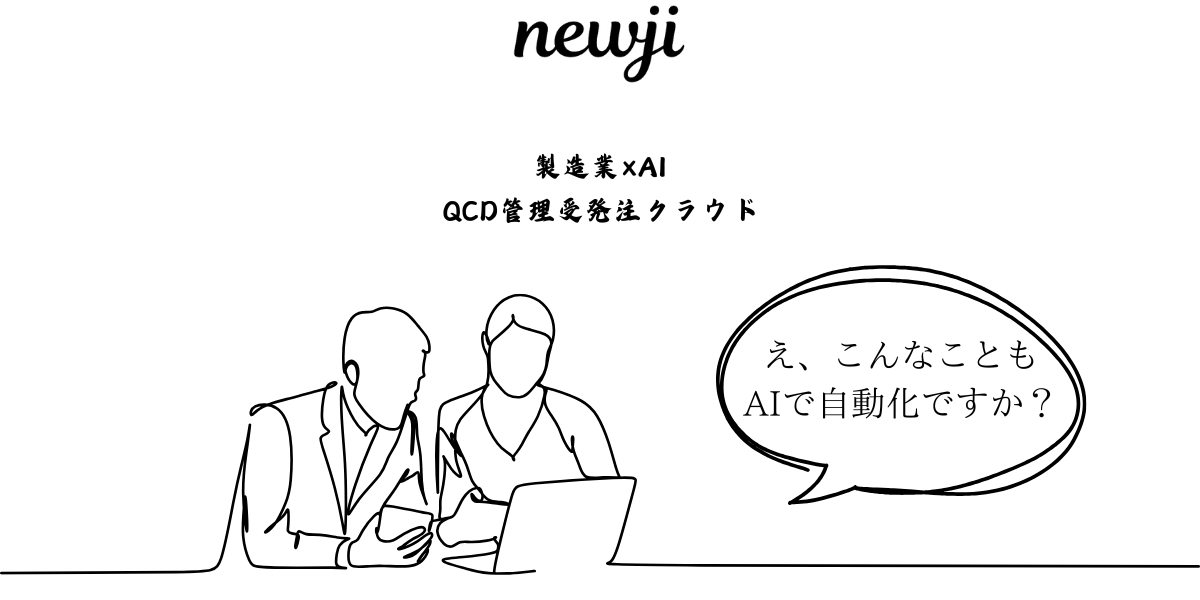
Fundamentals of PID control and key points of parameter tuning technology
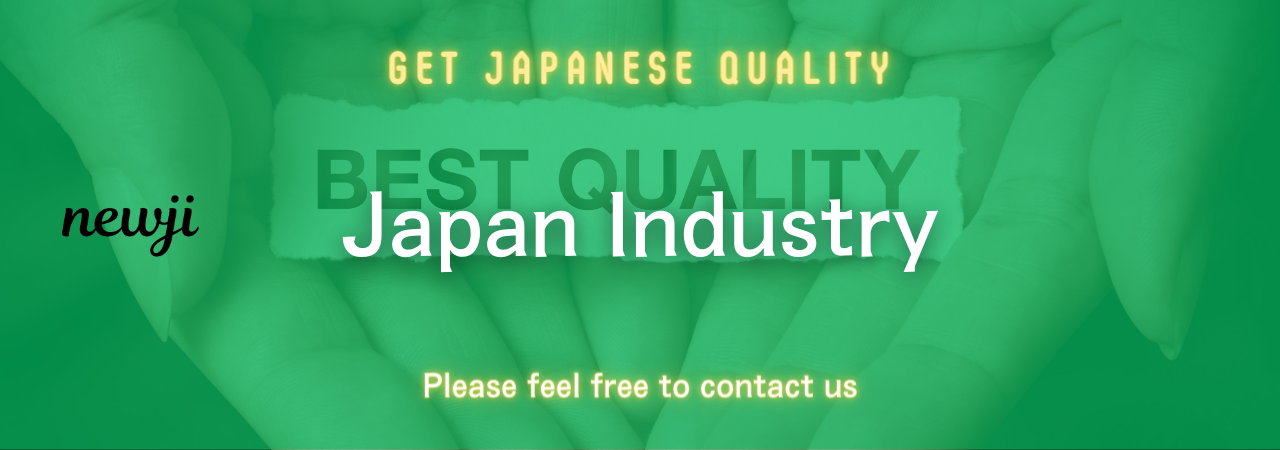
目次
Introduction to PID Control
The Proportional-Integral-Derivative (PID) controller is a staple in control systems engineering.
It is widely used in various applications due to its simplicity, effectiveness, and ease of implementation.
From household appliances to complex industrial processes, PID control helps maintain desired levels of system performance.
Understanding PID Control
PID control involves three main components: proportional, integral, and derivative.
Each of these parts plays a crucial role in ensuring that a system behaves as desired.
Proportional Control
Proportional control is the primary component and is responsible for responding to the error between a setpoint and the current process variable.
It adjusts the output proportionally to the error.
For instance, if the error is large, the proportional control will apply a large correction.
Integral Control
The integral component addresses the accumulated errors over time.
It is particularly useful for eliminating steady-state errors, which occur when the system maintains a small error for an extended period.
Integral control continuously sums the error, providing additional corrective action as needed.
Derivative Control
Derivative control predicts future error behavior by considering its rate of change.
It provides a damping effect, reducing overshoot and improving system stability.
By computing the error’s derivative, this component anticipates where the system is headed, making preemptive adjustments.
Benefits of PID Controllers
PID controllers have been popular for decades due to their numerous benefits.
They are simple to understand and implement, yet versatile enough for a wide range of applications.
Improved Stability: With the proportional, integral, and derivative actions working together, PID controllers are adept at stabilizing systems.
They help systems quickly reach the setpoint with minimal oscillation.
Flexibility: The components of a PID can be adjusted to suit specific needs.
By tuning, you can balance between responsiveness and stability.
Robustness: Many systems can be controlled using PID without requiring detailed physical models.
This makes PID controllers suitable for processes where exact modeling is challenging or impossible.
Key Parameter Tuning Techniques
Parameter tuning is essential for maximizing the performance of PID controllers.
Proper tuning adjusts the proportional (Kp), integral (Ki), and derivative (Kd) gains.
Finding the optimal values leads to better control, improved response times, and reduced errors.
Manual Tuning
Manual tuning is the simplest method, often used by experienced engineers.
It involves adjusting each parameter by hand and observing the system’s response.
Here’s a basic approach:
1. Set Ki and Kd to zero initially.
2. Gradually increase Kp until the system begins oscillating, then scale back until the oscillations are minimal.
3. Introduce Ki to eliminate any steady-state error, increasing it until you achieve the desired accuracy.
4. Finally, adjust Kd to dampen any oscillation and improve stability.
Ziegler-Nichols Method
The Ziegler-Nichols method is a more systematic approach to tuning.
Developed in the 1940s, it provides a heuristic method to apply to PID controllers.
It uses specific criteria to adjust controller parameters, starting by setting Ki and Kd to zero and systematically finding the ultimate gains for Kp.
Software-Based Tuning
Advancements in technology have led to software-based tuning tools.
These tools can automatically adjust PID parameters, providing a potentially quicker and more efficient alternative to manual tuning.
Software-based methods often involve simulations or real-time adjustments and can significantly streamline the tuning process.
Challenges in PID Controller Implementation
Despite their advantages, PID controllers can present challenges, particularly in complex systems.
One common issue is the potential for instability if parameters are incorrectly tuned.
Overly aggressive tuning can lead to excessive oscillation, while conservative settings might result in sluggish response times.
Achieving the right balance is critical.
Moreover, PID controllers are less effective in systems with significant delays or non-linear characteristics.
In such cases, advanced control strategies or supplementary models might be necessary.
Conclusion
Understanding the fundamentals of PID control and mastering parameter tuning techniques are crucial for effective system management.
By adjusting the proportional, integral, and derivative gains appropriately, you can significantly enhance system performance.
While tuning can be challenging, the benefits of a well-tuned PID controller are invaluable.
With a bit of practice and the right tools, achieving optimal control becomes an attainable goal.
資料ダウンロード
QCD調達購買管理クラウド「newji」は、調達購買部門で必要なQCD管理全てを備えた、現場特化型兼クラウド型の今世紀最高の購買管理システムとなります。
ユーザー登録
調達購買業務の効率化だけでなく、システムを導入することで、コスト削減や製品・資材のステータス可視化のほか、属人化していた購買情報の共有化による内部不正防止や統制にも役立ちます。
NEWJI DX
製造業に特化したデジタルトランスフォーメーション(DX)の実現を目指す請負開発型のコンサルティングサービスです。AI、iPaaS、および先端の技術を駆使して、製造プロセスの効率化、業務効率化、チームワーク強化、コスト削減、品質向上を実現します。このサービスは、製造業の課題を深く理解し、それに対する最適なデジタルソリューションを提供することで、企業が持続的な成長とイノベーションを達成できるようサポートします。
オンライン講座
製造業、主に購買・調達部門にお勤めの方々に向けた情報を配信しております。
新任の方やベテランの方、管理職を対象とした幅広いコンテンツをご用意しております。
お問い合わせ
コストダウンが利益に直結する術だと理解していても、なかなか前に進めることができない状況。そんな時は、newjiのコストダウン自動化機能で大きく利益貢献しよう!
(Β版非公開)