- お役立ち記事
- Fundamentals of PID control, tuning methods, and application to control system design
月間76,176名の
製造業ご担当者様が閲覧しています*
*2025年3月31日現在のGoogle Analyticsのデータより
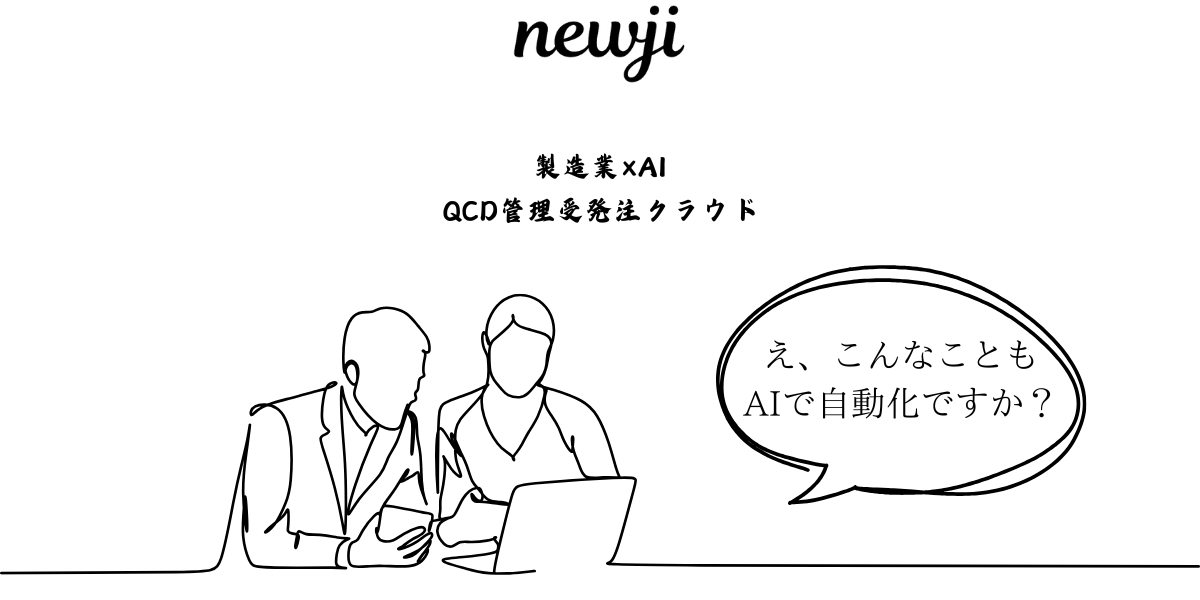
Fundamentals of PID control, tuning methods, and application to control system design
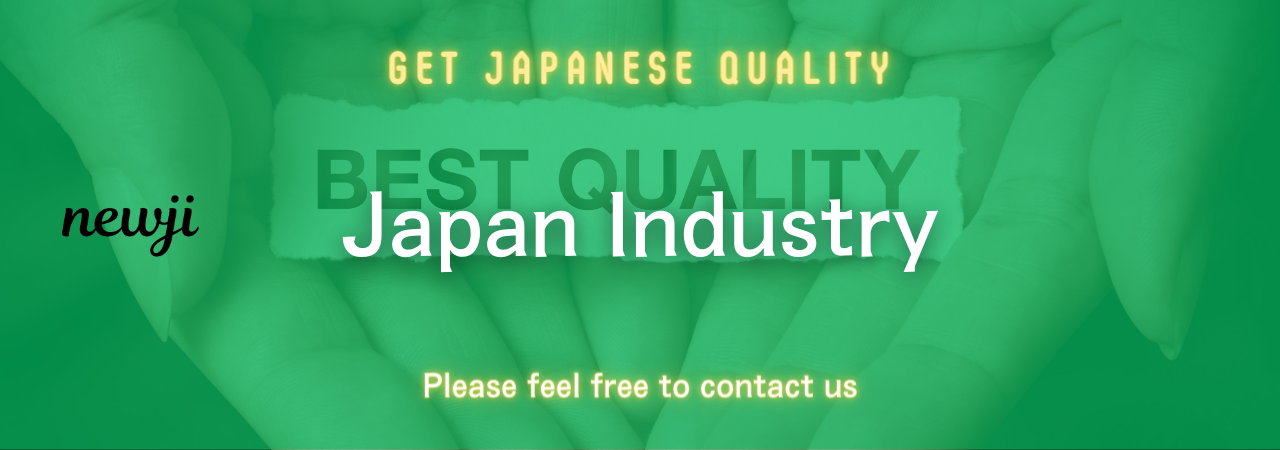
目次
Understanding PID Control
PID control is a fundamental concept in control systems, widely used in industrial applications to maintain a desired output despite disturbances.
It stands for Proportional-Integral-Derivative control, which refers to the three basic mathematical functions it uses to keep a control variable at a desired set point.
The Proportional Component
The proportional part of the PID controller is the most straightforward.
It generates an output that is directly proportional to the error, the difference between the set point and the process variable.
The proportional gain, denoted by the constant ‘Kp,’ determines how much correction is applied.
A higher Kp means more aggressive response to error, which could lead to oscillations if too high.
The Integral Component
The integral component is crucial for eliminating steady-state error.
It sums the errors over time, known as integrating, and applies a correction based on this accumulated error.
The integral gain, ‘Ki,’ impacts how quickly the accumulated error is corrected.
However, if set too high, it can lead to instability and overshoot, causing sluggish response and system instability.
The Derivative Component
The derivative component predicts future errors by calculating the rate of change.
It reacts to changes in error, smoothing out the response and anticipating future destabilizing effects.
Damping oscillations and improving stability are key roles of the derivative gain, ‘Kd.’
Nevertheless, excessive derivative gain can amplify noise, leading to erratic control action.
Tuning PID Controllers
Effective PID control depends on tuning these three gains (Kp, Ki, Kd) to balance performance and stability.
Several methods can achieve optimal or satisfactory tuning.
Trial and Error Method
Starting with all gains set to zero, the proportional gain is gradually increased until the system oscillates.
Then, the integral and derivative gains are adjusted to reach acceptable performance.
Although time-consuming, this method provides a practical way to reach a functional set of parameters.
Ziegler-Nichols Method
This popular method involves setting the integral and derivative gains to zero initially and increasing the proportional gain until sustained oscillations are observed.
The critical gain (Kcr) and oscillation period (Pcr) are recorded to calculate the appropriate PID values using certain formulas.
Despite its effectiveness in many cases, it may not yield optimal results for all systems.
Cohen-Coon Method
Particularly suited for systems with dead time or delay, the Cohen-Coon method considers open-loop response to a step input.
This approach requires gathering specific time-based data about the system response to adjust the PID parameters precisely.
It’s advantageous for processes with significant delays but can be intricate to implement.
Software-Based Tuning
With advancements in digital technology, software tools have become essential for PID tuning.
Simulation software can model the process and automatically suggest the best parameters based on algorithms.
These tools save time while providing solutions that might not be attainable manually, ensuring enhanced control system performance.
Application in Control System Design
PID controllers are pivotal in various control system designs due to their versatility.
Manufacturing Processes
In manufacturing, PID control is prevalent, maintaining temperatures, pressures, and fluid levels.
For instance, in chemical plants, PID controllers regulate the reaction conditions to ensure optimal product quality.
Precision is vital in such applications, given the potential risks involved with materials and chemical balances.
Automotive Systems
In the automotive industry, PID controllers are integral to functions like cruise control and engine management.
They enhance the driving experience by ensuring smooth acceleration and maintaining desired speed despite changes in terrain.
This adaptability makes PID control ideal for dynamic automotive environments.
Robotics
Robots increasingly rely on PID controllers for motion control, offering precise adjustments in robotics applications.
Whether for maintaining balance in two-legged robots or ensuring accurate movements in industrial robots, PID ensures smooth and reliable operations.
This flexibility helps address the delicate dynamics of robotic systems handling varied tasks.
Conclusion
Understanding the fundamentals of PID control is crucial for designing effective control systems.
By mastering the tuning methods and recognizing their application in different industries, engineers can harness PID’s potential to optimize system performance.
Overall, PID remains a cornerstone of control systems engineering, offering solutions that balance simplicity and efficacy across a myriad of applications.
資料ダウンロード
QCD管理受発注クラウド「newji」は、受発注部門で必要なQCD管理全てを備えた、現場特化型兼クラウド型の今世紀最高の受発注管理システムとなります。
ユーザー登録
受発注業務の効率化だけでなく、システムを導入することで、コスト削減や製品・資材のステータス可視化のほか、属人化していた受発注情報の共有化による内部不正防止や統制にも役立ちます。
NEWJI DX
製造業に特化したデジタルトランスフォーメーション(DX)の実現を目指す請負開発型のコンサルティングサービスです。AI、iPaaS、および先端の技術を駆使して、製造プロセスの効率化、業務効率化、チームワーク強化、コスト削減、品質向上を実現します。このサービスは、製造業の課題を深く理解し、それに対する最適なデジタルソリューションを提供することで、企業が持続的な成長とイノベーションを達成できるようサポートします。
製造業ニュース解説
製造業、主に購買・調達部門にお勤めの方々に向けた情報を配信しております。
新任の方やベテランの方、管理職を対象とした幅広いコンテンツをご用意しております。
お問い合わせ
コストダウンが利益に直結する術だと理解していても、なかなか前に進めることができない状況。そんな時は、newjiのコストダウン自動化機能で大きく利益貢献しよう!
(β版非公開)