- お役立ち記事
- Fundamentals of plastic deterioration analysis, durability evaluation technology, and application to reliability improvement
Fundamentals of plastic deterioration analysis, durability evaluation technology, and application to reliability improvement
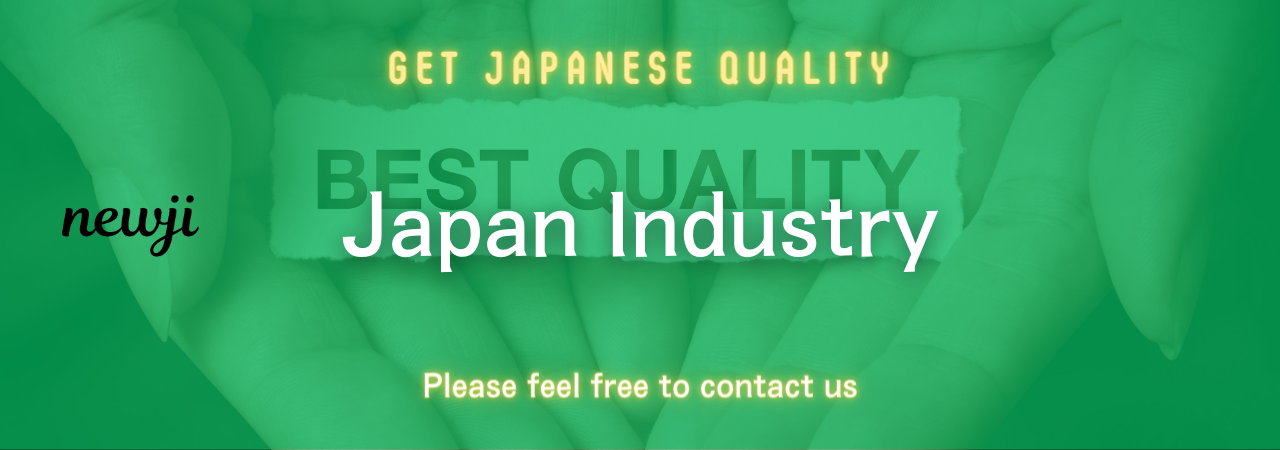
目次
Understanding Plastic Deterioration
Plastic deterioration is a critical aspect that affects the performance, safety, and longevity of plastic products.
Plastics are versatile materials used in various industries due to their lightweight nature, durability, and cost-effectiveness.
However, like all materials, plastics are susceptible to degradation over time.
Deterioration can occur due to several factors, including environmental exposure, mechanical stress, chemical interactions, and thermal effects.
Understanding these fundamental factors is essential for industries relying heavily on plastic components.
Environmental Factors
Exposure to sunlight is one of the primary causes of plastic degradation.
Ultraviolet (UV) radiation from the sun leads to photo-oxidation, which breaks down the chemical bonds in plastics, causing them to lose color and become brittle.
Moisture and humidity can also contribute to plastic deterioration.
Water can seep into the plastic, leading to hydrolytic degradation.
This is particularly significant for biodegradable plastics, which are designed to break down under moisture.
Mechanical Stress
Repeated mechanical stress and strain can cause plastics to develop fractures over time.
This is especially problematic in applications like automotive parts and construction materials, where plastic is subjected to constant pressure and movement.
Understanding the stress limits of different plastics is crucial for designing components that are both durable and reliable.
Fatigue testing can help predict when a plastic component might fail under repeated stress.
Chemical Interactions
Plastics can interact with chemicals in their environment, leading to chemical degradation.
This type of deterioration is common in plastics used for packaging food and chemicals, where exposure can result in contamination and leaching.
Selecting the right type of plastic for specific applications is essential to minimize chemical interactions.
For example, polyethylene is often chosen for chemical storage because it is resistant to many acids and bases.
Durability Evaluation Technology
To counter plastic deterioration, industries must employ durability evaluation technologies.
These techniques assess the long-term performance and reliability of plastic materials, ensuring they meet industry standards and customer expectations.
Analytical Techniques
Analytical techniques such as Fourier-transform infrared spectroscopy (FTIR) and gas chromatography can identify chemical changes in plastics.
These techniques help determine the extent of degradation and identify potential vulnerabilities in the plastic structure.
Testing for changes in molecular weight and thermal properties also provides insight into the material’s durability.
Understanding these properties helps in developing plastics with improved resistance to environmental stressors.
Accelerated Aging Tests
Accelerated aging tests simulate the long-term effects of environmental factors on plastics in a shorter timespan.
These tests expose plastic samples to conditions like UV radiation, temperature fluctuations, and humidity to predict their lifespan.
The results of accelerated aging tests are invaluable for manufacturers, enabling them to optimize plastic formulations and improve durability.
Mechanical Testing
Mechanical testing involves assessing the strength, flexibility, and impact resistance of plastics.
Tests like tensile, flexural, and impact tests help determine a material’s response to mechanical forces.
These tests provide a clearer understanding of a plastic’s durability under real-world conditions, guiding design decisions in engineering and product development.
Application to Reliability Improvement
Reliability improvement in plastic products involves implementing insights gained from durability evaluations to enhance the performance and lifespan of plastic components.
Material Selection and Design
Choosing the right plastic material for a given application is crucial.
Factors such as environmental exposure, mechanical load, and chemical resistance need to be considered.
Innovations in polymer blends and composites have improved the durability of plastics, allowing for applications in more demanding environments.
Design modifications, like adding protective coatings or UV stabilizers, can further enhance the reliability of plastics.
Quality Control and Monitoring
Implementing strict quality control measures during production ensures that plastic products meet durability and safety standards.
Continuous monitoring of performance indicators and feedback from users can highlight areas for improvement.
Regular maintenance and inspection of plastic components help detect early signs of deterioration, allowing for timely interventions and extending the service life of products.
Sustainability Considerations
As industries move towards sustainability, biodegradability and recyclability have become important factors.
While some biodegradable plastics are designed to break down under certain conditions, improving their reliability during their usage phase is equally important.
Recycling technologies are advancing, allowing for the repurposing of plastics while maintaining their structural integrity and performance.
Conclusion
Understanding plastic deterioration and employing durability evaluation technologies are essential in improving the reliability of plastic products.
By considering environmental factors, mechanical stress, and chemical interactions, industries can develop materials that offer enhanced performance and longevity.
With the integration of advanced analytical techniques, accelerated aging tests, and mechanical testing, manufacturers can predict a material’s lifespan and optimize its properties.
Finally, selecting appropriate materials, ensuring quality control, and focusing on sustainable practices contribute to the development of reliable, long-lasting plastic products.
資料ダウンロード
QCD調達購買管理クラウド「newji」は、調達購買部門で必要なQCD管理全てを備えた、現場特化型兼クラウド型の今世紀最高の購買管理システムとなります。
ユーザー登録
調達購買業務の効率化だけでなく、システムを導入することで、コスト削減や製品・資材のステータス可視化のほか、属人化していた購買情報の共有化による内部不正防止や統制にも役立ちます。
NEWJI DX
製造業に特化したデジタルトランスフォーメーション(DX)の実現を目指す請負開発型のコンサルティングサービスです。AI、iPaaS、および先端の技術を駆使して、製造プロセスの効率化、業務効率化、チームワーク強化、コスト削減、品質向上を実現します。このサービスは、製造業の課題を深く理解し、それに対する最適なデジタルソリューションを提供することで、企業が持続的な成長とイノベーションを達成できるようサポートします。
オンライン講座
製造業、主に購買・調達部門にお勤めの方々に向けた情報を配信しております。
新任の方やベテランの方、管理職を対象とした幅広いコンテンツをご用意しております。
お問い合わせ
コストダウンが利益に直結する術だと理解していても、なかなか前に進めることができない状況。そんな時は、newjiのコストダウン自動化機能で大きく利益貢献しよう!
(Β版非公開)