- お役立ち記事
- Fundamentals of plastic injection molding and technology to improve moldability and mold release properties
Fundamentals of plastic injection molding and technology to improve moldability and mold release properties
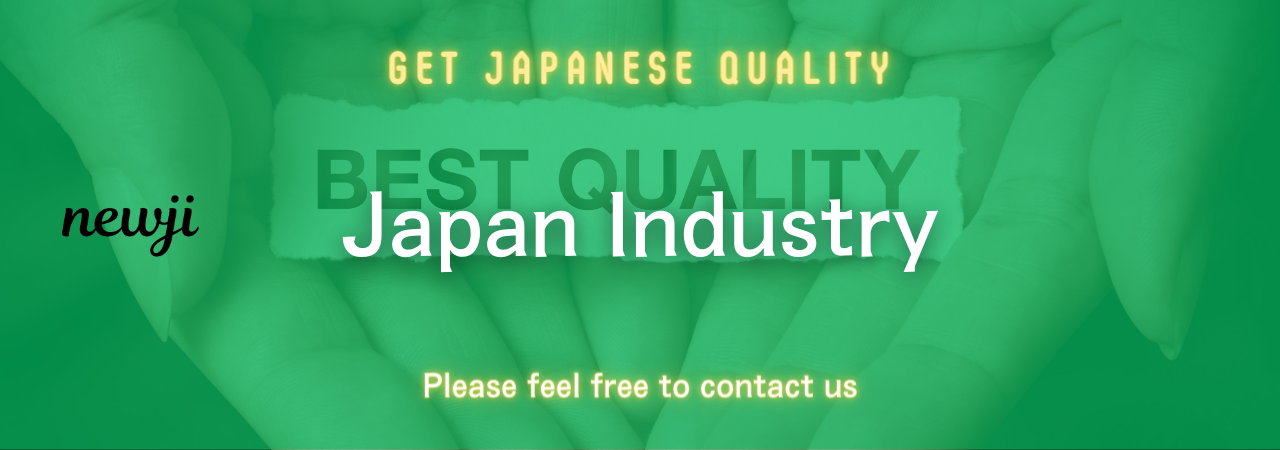
目次
Understanding Plastic Injection Molding
Plastic injection molding is a widely-used manufacturing process for producing plastic parts and products.
It involves injecting molten plastic material into a mold, where it cools and solidifies to form a specific shape.
This technique is popular due to its ability to produce complex shapes and high quantities of parts with consistent quality.
Understanding the fundamentals of this process is crucial for improving moldability and mold release properties, which are key factors in manufacturing efficiency and product quality.
The Process of Plastic Injection Molding
The injection molding process begins with the careful design of a mold, which is typically made from metal and consists of two halves—a mold cavity and a mold core.
Once the mold design is finalized, plastic pellets are fed into an injection molding machine where they are heated and melted.
The liquified plastic is then injected into the mold under high pressure.
Once the plastic fills the mold cavity, it is cooled to solidify.
The mold then opens, and the finished product is ejected.
The process is repeated for mass production.
Key Factors in Injection Molding
Mold Design
Mold design plays a significant role in moldability and mold release.
A well-designed mold ensures uniform filling, minimizes defects, and facilitates easy part removal.
Key considerations in mold design include the material to be used, the desired shape and size of the finished product, and potential cooling strategies.
Material Selection
Choosing the right plastic material is critical for successful injection molding.
Different plastics have unique properties, such as melting temperature, viscosity, and shrinkage rate, which must match the requirements of the specific application.
Commonly used materials include thermoplastics like polyethylene, polypropylene, and polystyrene.
Machine Parameters
Injection molding machines must be precisely controlled to maintain optimal parameters such as temperature, pressure, and injection speed.
Any variations can affect the quality of the final product, leading to issues like warping, surface defects, or incomplete parts.
Regular calibration and maintenance are essential to ensure machine reliability.
Improving Moldability
Optimizing Molding Conditions
Adjusting molding conditions can significantly improve moldability.
Factors like mold temperature, injection pressure, and cooling time need careful balancing to ensure the plastic flows smoothly into the mold and solidifies without defects.
Advanced techniques, such as computer-aided engineering (CAE) simulations, can help predict how changes in these conditions will affect moldability.
Enhancing Material Flow
Ensuring proper material flow through the mold is crucial for high-quality parts.
Design modifications, such as altering wall thickness or adding flow channels, can help achieve even distribution of molten plastic.
Additives can also improve flow by reducing viscosity or enhancing lubrication.
Use of Mold Release Agents
Mold release agents are used to prevent sticking and facilitate the easy release of molded parts.
These agents create a thin film between the mold surface and the plastic part, reducing friction.
Selecting the appropriate release agent type—whether silicon-based, water-based, or dry-film—is essential to avoid negative interactions with the plastic material.
Enhancing Mold Release Properties
Surface Treatments
Surface treatments and coatings can enhance the mold release properties.
Techniques like polishing or texturing mold surfaces can reduce the tendency for parts to stick.
Coatings, such as hard chrome or nickel plating, offer improved durability and reduced friction.
Temperature Control
Proper temperature control is critical for efficient mold release.
Maintaining the mold at an optimal temperature ensures that the plastic cools evenly and contracts as expected, reducing adhesion to the mold.
Advanced heating and cooling systems within molds help achieve precise temperature management.
Design Enhancements
Incorporating design features that assist with ejection can improve mold release properties.
Draft angles, which are slight taper angles on the mold surfaces, help parts separate more easily.
Ejection systems, such as pins, air jets, or ejector plates, can be strategically placed to aid in part removal without damaging the product.
Conclusion
Plastic injection molding is a complex but highly effective manufacturing process, and mastering its fundamentals is vital for producing high-quality plastic products.
By focusing on factors such as mold design, material selection, and machine parameters, manufacturers can enhance moldability and mold release properties.
Implementing strategies like optimizing molding conditions, using appropriate mold release agents, and surface treatments can further improve the efficiency and quality of the products produced.
With diligent attention to these areas, companies can achieve successful injection molding operations, ensuring their products meet the desired standards of performance and quality.
資料ダウンロード
QCD調達購買管理クラウド「newji」は、調達購買部門で必要なQCD管理全てを備えた、現場特化型兼クラウド型の今世紀最高の購買管理システムとなります。
ユーザー登録
調達購買業務の効率化だけでなく、システムを導入することで、コスト削減や製品・資材のステータス可視化のほか、属人化していた購買情報の共有化による内部不正防止や統制にも役立ちます。
NEWJI DX
製造業に特化したデジタルトランスフォーメーション(DX)の実現を目指す請負開発型のコンサルティングサービスです。AI、iPaaS、および先端の技術を駆使して、製造プロセスの効率化、業務効率化、チームワーク強化、コスト削減、品質向上を実現します。このサービスは、製造業の課題を深く理解し、それに対する最適なデジタルソリューションを提供することで、企業が持続的な成長とイノベーションを達成できるようサポートします。
オンライン講座
製造業、主に購買・調達部門にお勤めの方々に向けた情報を配信しております。
新任の方やベテランの方、管理職を対象とした幅広いコンテンツをご用意しております。
お問い合わせ
コストダウンが利益に直結する術だと理解していても、なかなか前に進めることができない状況。そんな時は、newjiのコストダウン自動化機能で大きく利益貢献しよう!
(Β版非公開)