- お役立ち記事
- Fundamentals of plastic injection molding technology and key points to prevent defects in molded products
月間76,176名の
製造業ご担当者様が閲覧しています*
*2025年3月31日現在のGoogle Analyticsのデータより
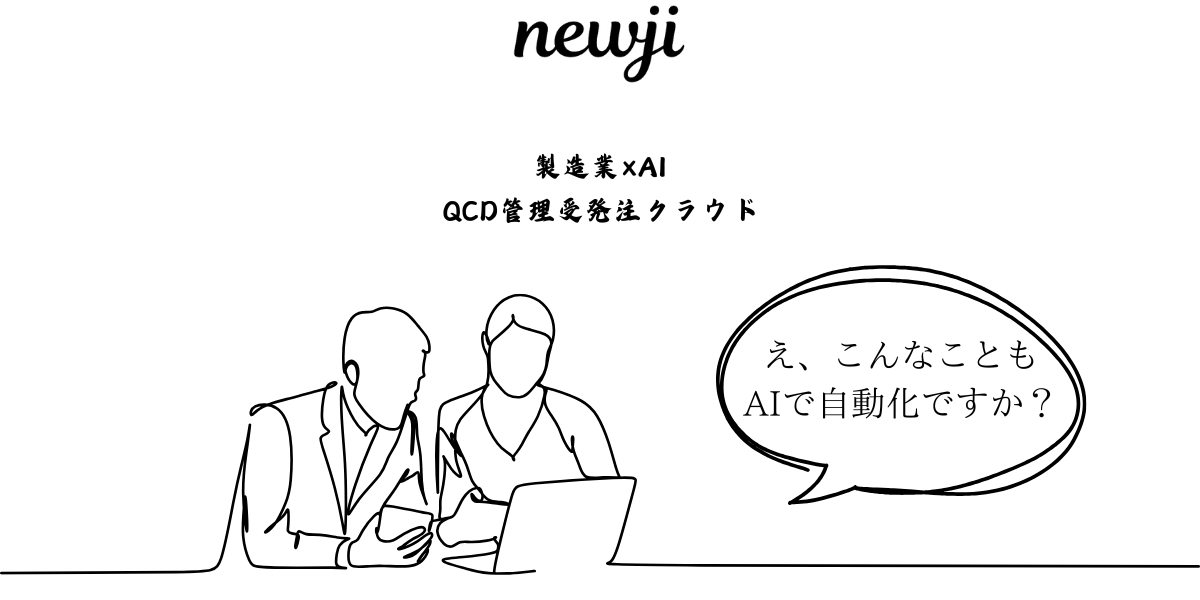
Fundamentals of plastic injection molding technology and key points to prevent defects in molded products
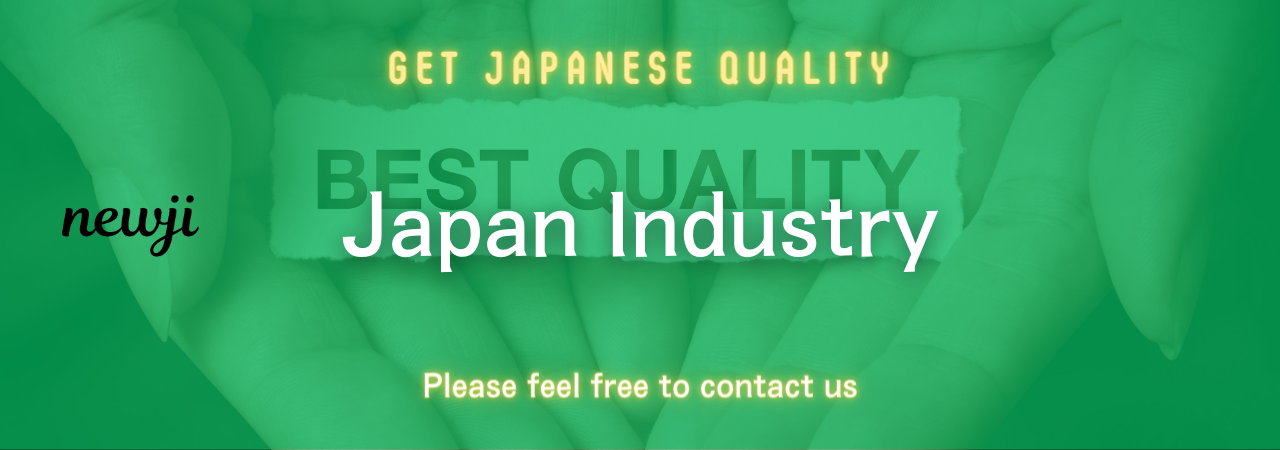
目次
Understanding Plastic Injection Molding
Plastic injection molding is a widely used manufacturing process that involves the production of plastic parts by injecting molten plastic material into a mold.
This technique is highly favored in industries for its ability to produce intricate shapes and designs with precision and consistency.
The process begins with the plastic material, usually in the form of small pellets or granules, being fed into a heated barrel.
Here, it is melted into a molten state.
Once the plastic is melted, it is injected into a metal mold cavity where it cools and solidifies into the shape of the desired part.
The beauty of plastic injection molding lies in its versatility.
It can produce parts of varying complexity and size, from tiny components for medical devices to large parts for automotive applications.
Moreover, the process allows for high-volume production, making it cost-effective for mass production.
Key Components of the Injection Molding Process
To understand injection molding technology, it’s essential to familiarize yourself with its key components:
The Mold
The mold is a crucial element in the injection molding process as it determines the final shape and features of the part.
Made typically from steel or aluminum, the mold consists of two halves—referred to as the cavity and the core—that form the desired shape when combined.
The quality of the mold greatly impacts the quality of the finished product, and thus, precise and careful design is imperative.
The Injection Unit
The injection unit comprises the parts of the machine where plastic is melted and injected into the mold.
It includes the hopper where plastic granules are loaded, the barrel where they are heated and melted, and the screw mechanism that injects the plastic into the mold.
The Clamping Unit
This unit holds the mold together under pressure during injection and cooling, ensuring the mold halves are perfectly aligned.
The clamping force is critical, as insufficient force can lead to manufacturing defects.
Preventing Defects in Molded Products
While plastic injection molding is a highly efficient process, it is not devoid of challenges.
Defects in molded products can arise due to various reasons.
Understanding these potential issues and implementing strategies to prevent them is crucial for ensuring the quality of the final product.
Common Defects in Injection Molding
Some of the most common defects in injection molding include:
– **Warpage:** This occurs when different parts of the molded product cool at different rates, leading to deformation.
– **Sink Marks:** These are depressions or voids on the surface of the product caused by shrinkage.
– **Flow Lines:** Visible lines or patterns on the surface of the product that result from variations in material flow rates.
– **Burn Marks:** These are discolorations or charred areas caused by excessive heating of the plastic.
– **Air Traps:** Pockets of air trapped within the product that create imperfections and weaken the structure.
Key Points to Minimize Defects
To prevent these defects, manufacturers should consider the following key points:
– **Optimal Design:** Proper design of the mold and product is crucial.
Considerations should include uniform wall thickness, adequate draft angles, and well-placed ribs and bosses to ensure even material flow and cooling.
– **Material Selection:** The choice of plastic material should align with the product’s requirements.
Different plastics have varied properties, including melting points, flow rates, and shrinkage rates.
– **Process Parameters:** Fine-tuning the injection molding parameters—such as temperature, pressure, and cooling time—is essential.
The settings should be carefully adjusted and monitored to optimize the process.
– **Regular Maintenance:** Keeping the equipment in good working condition is vital.
Routine maintenance of the machine and mold ensures consistent performance and reduces the chances of defects.
Conclusion
Plastic injection molding is a powerful technology that significantly impacts modern manufacturing.
Its ability to produce high-quality, intricate parts makes it indispensable in various industries.
Understanding the fundamentals of the process and being proactive in preventing defects can greatly enhance production efficiency and product quality.
By focusing on optimal design, material selection, process parameters, and equipment maintenance, manufacturers can achieve defect-free molded products and maintain their competitive edge in the market.
資料ダウンロード
QCD管理受発注クラウド「newji」は、受発注部門で必要なQCD管理全てを備えた、現場特化型兼クラウド型の今世紀最高の受発注管理システムとなります。
ユーザー登録
受発注業務の効率化だけでなく、システムを導入することで、コスト削減や製品・資材のステータス可視化のほか、属人化していた受発注情報の共有化による内部不正防止や統制にも役立ちます。
NEWJI DX
製造業に特化したデジタルトランスフォーメーション(DX)の実現を目指す請負開発型のコンサルティングサービスです。AI、iPaaS、および先端の技術を駆使して、製造プロセスの効率化、業務効率化、チームワーク強化、コスト削減、品質向上を実現します。このサービスは、製造業の課題を深く理解し、それに対する最適なデジタルソリューションを提供することで、企業が持続的な成長とイノベーションを達成できるようサポートします。
製造業ニュース解説
製造業、主に購買・調達部門にお勤めの方々に向けた情報を配信しております。
新任の方やベテランの方、管理職を対象とした幅広いコンテンツをご用意しております。
お問い合わせ
コストダウンが利益に直結する術だと理解していても、なかなか前に進めることができない状況。そんな時は、newjiのコストダウン自動化機能で大きく利益貢献しよう!
(β版非公開)