- お役立ち記事
- Fundamentals of plastic injection molding technology and key points to prevent molding defects
月間76,176名の
製造業ご担当者様が閲覧しています*
*2025年3月31日現在のGoogle Analyticsのデータより
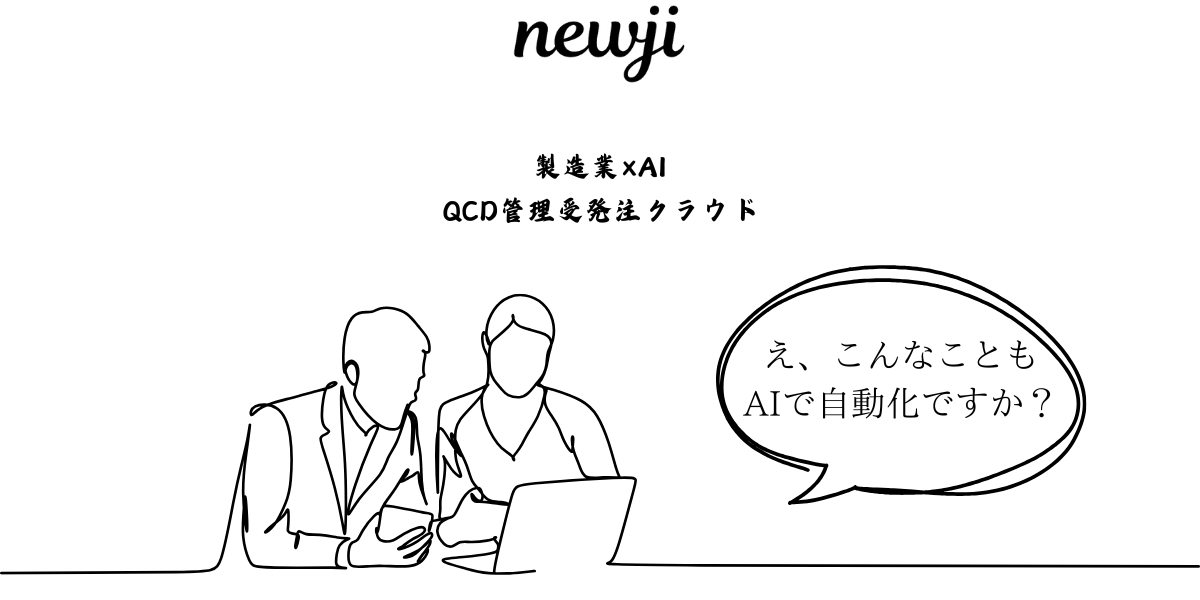
Fundamentals of plastic injection molding technology and key points to prevent molding defects
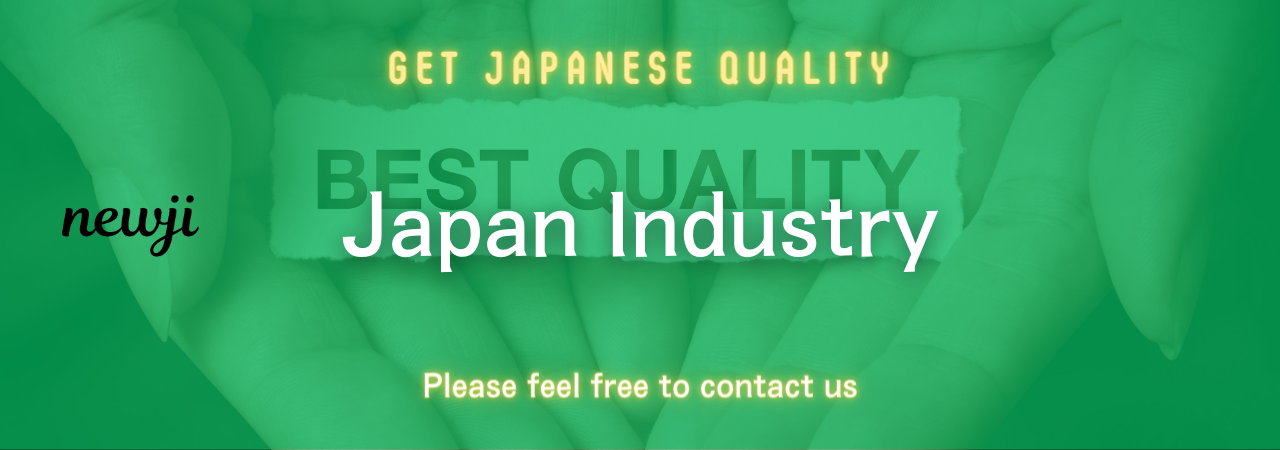
目次
Introduction to Plastic Injection Molding
Plastic injection molding is a pivotal process in the manufacturing industry, utilized to produce a wide variety of plastic parts and products.
This technique is favored for its efficiency, precision, and versatility, allowing for mass production of items with consistent quality.
Whether making tiny components or large parts, plastic injection molding provides a reliable solution to meet diverse industry needs.
Injection molding involves melting plastic granules, injecting the molten plastic into a mold, and cooling it to form the final product.
This method is suitable for producing complex shapes and designs, offering manufacturers the flexibility to create intricate, detailed parts with minimal waste.
The Process of Injection Molding
Understanding the injection molding process is crucial for those in the manufacturing industry.
The procedure can be broken down into several key steps: clamping, injection, cooling, and ejection.
In the clamping stage, two halves of the mold are securely closed using a clamping unit.
This ensures that the mold will withstand the high-pressure injection of molten plastic.
The injection phase follows, in which the plastic granules are melted and injected into the mold cavity through a barrel and screw arrangement.
The plastic is subjected to high heat and pressure during this stage, ensuring it flows uniformly throughout the mold.
Once the plastic has been injected, the cooling process commences.
The plastic cools and solidifies, taking on the shape of the mold.
The cooling time varies depending on the part’s size, thickness, and the type of plastic used.
Finally, the ejection step involves opening the mold and removing the solidified plastic part.
The mold is then closed, ready for the next cycle.
This entire process is typically fast, with cycle times ranging from a few seconds to minutes, depending on the product complexity.
Common Materials Used in Injection Molding
Several materials are used in plastic injection molding, each offering unique properties and benefits.
Common plastics include:
Polyethylene (PE)
Polyethylene is one of the most commonly used plastics in injection molding.
It is versatile, resistant to chemicals, and has excellent impact strength.
Used to manufacture items like containers, buckets, and consumer goods, polyethylene is durable and works well for products requiring flexibility and resilience.
Polypropylene (PP)
Polypropylene is another popular choice due to its toughness and resistance to chemicals and moisture.
It is frequently used for automotive parts, packaging, and textiles.
Polypropylene’s durability and ability to maintain its shape make it ideal for items that undergo repeated stress.
Acrylonitrile Butadiene Styrene (ABS)
ABS is renowned for its strength, rigidity, and lightweight properties.
Commonly used in electronic housings, toys, and automotive components, ABS offers excellent resistance to various environmental stressors, making it a reliable choice for sturdy applications.
Polystyrene (PS)
With its good clarity and rigidity, polystyrene is often used for food packaging, disposable cutlery, and laboratory equipment.
It offers good strength and an excellent option for applications needing clear or colored plastic products.
Key Points to Prevent Molding Defects
Despite the efficiencies offered by plastic injection molding, defects can occur during the manufacturing process.
Preventing these defects is critical for ensuring product quality and meeting customer expectations.
Understanding the common types of defects and how to mitigate them can save time, money, and resources.
Minimizing Warping
Warping occurs due to uneven cooling or inconsistent plastic shrinkage, resulting in a deformed final product.
To prevent warping, manufacturers should ensure uniform cooling by optimizing mold temperature and design.
Adjusting plastic flow rates and pressures can also help in reducing the chance of warping, resulting in products that retain their shape and dimensions accurately.
Eliminating Flash
Flash, or excess plastic that seeps out of the mold cavity, is often caused by high injection pressure or poorly designed molds.
To prevent flash, it is essential to accurately set the injection parameters and ensure molds are precisely aligned and closed during the clamping process.
Regular maintenance and inspection of molds can further help in reducing the occurrence of flash.
Avoiding Burn Marks
Burn marks are unsightly discolorations that appear when the plastic overheats in the mold.
To minimize burn marks, manufacturers can optimize the injection speed, temperature, and pressure settings.
Adequate venting of the mold is also crucial to release trapped gases, which can contribute to overheating.
Preventing Sink Marks
Sink marks are depressions or indentations that form on the surface of the molded part, typically due to differential cooling and shrinkage.
To prevent sink marks, manufacturers should ensure consistent wall thickness in their designs and optimize packing and holding times during the injection cycle.
Adjusting the cooling rate and incorporating uniform mold temperature can also support in maintaining the surface integrity of the product.
Conclusion
As a versatile and efficient manufacturing process, plastic injection molding continues to play a vital role in producing a wide range of products.
Understanding the fundamentals of the injection molding process and the critical points for preventing defects can significantly enhance production quality and efficiency.
By carefully selecting materials, maintaining optimal settings, and regularly inspecting molds, manufacturers can reduce defect rates and produce high-quality plastic parts that meet industry standards and customer expectations.
This thorough understanding of plastic injection molding technology empowers industries to produce reliable and durable products, reinforcing the significance of this process in today’s manufacturing landscape.
資料ダウンロード
QCD管理受発注クラウド「newji」は、受発注部門で必要なQCD管理全てを備えた、現場特化型兼クラウド型の今世紀最高の受発注管理システムとなります。
ユーザー登録
受発注業務の効率化だけでなく、システムを導入することで、コスト削減や製品・資材のステータス可視化のほか、属人化していた受発注情報の共有化による内部不正防止や統制にも役立ちます。
NEWJI DX
製造業に特化したデジタルトランスフォーメーション(DX)の実現を目指す請負開発型のコンサルティングサービスです。AI、iPaaS、および先端の技術を駆使して、製造プロセスの効率化、業務効率化、チームワーク強化、コスト削減、品質向上を実現します。このサービスは、製造業の課題を深く理解し、それに対する最適なデジタルソリューションを提供することで、企業が持続的な成長とイノベーションを達成できるようサポートします。
製造業ニュース解説
製造業、主に購買・調達部門にお勤めの方々に向けた情報を配信しております。
新任の方やベテランの方、管理職を対象とした幅広いコンテンツをご用意しております。
お問い合わせ
コストダウンが利益に直結する術だと理解していても、なかなか前に進めることができない状況。そんな時は、newjiのコストダウン自動化機能で大きく利益貢献しよう!
(β版非公開)