- お役立ち記事
- Fundamentals of plastic injection molding technology and key points to prevent molding defects
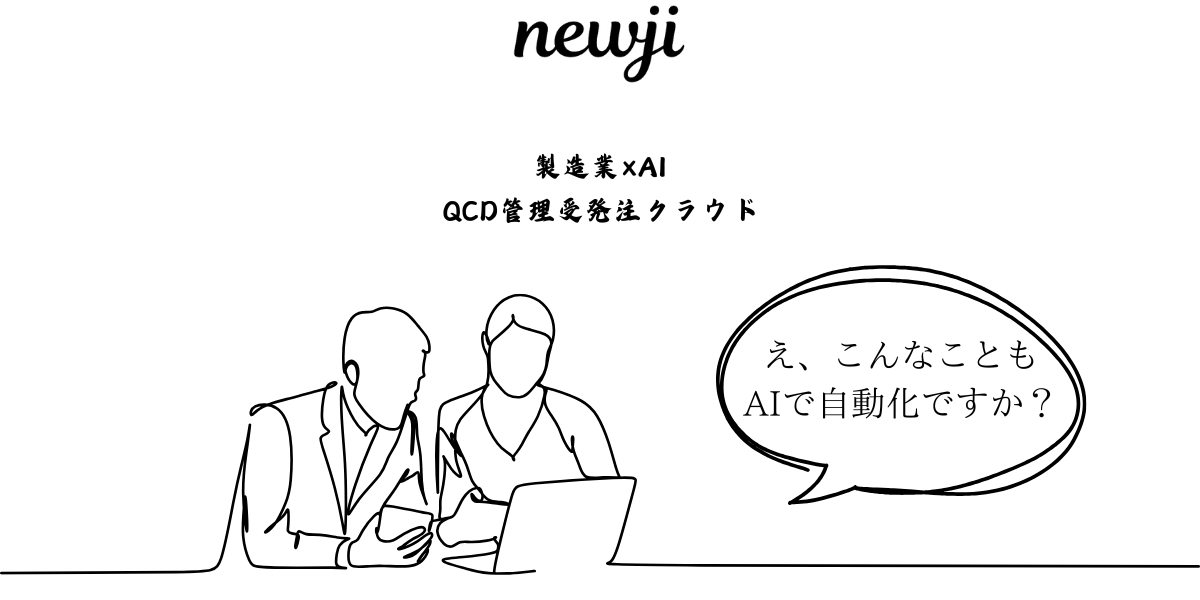
Fundamentals of plastic injection molding technology and key points to prevent molding defects
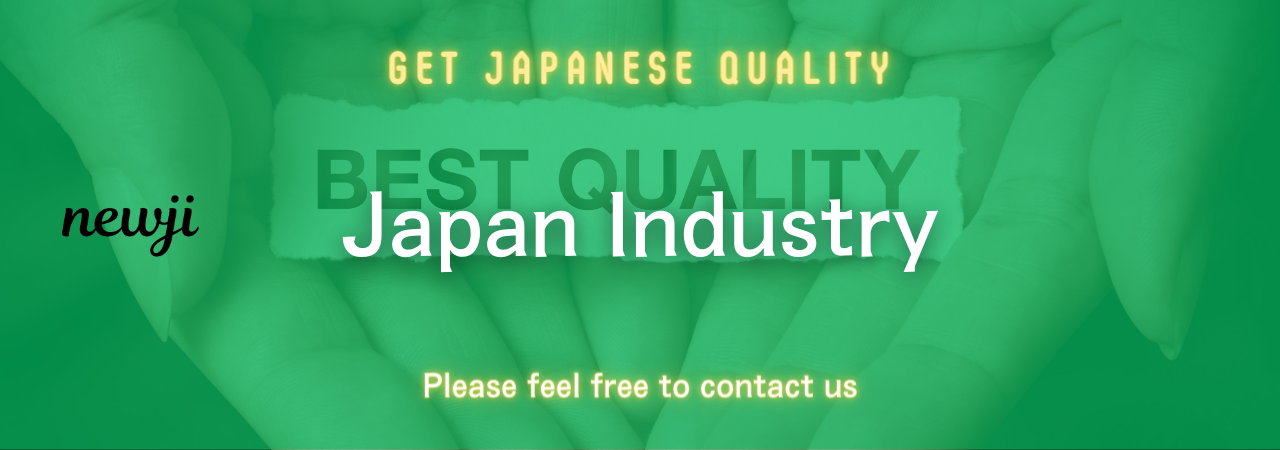
目次
Understanding Plastic Injection Molding Technology
Plastic injection molding is a popular and highly efficient manufacturing process used across a multitude of industries to produce a wide range of plastic products.
This technology involves injecting molten plastic into a mold cavity and allowing it to cool and solidify before being ejected as a finished part.
The process is widely used due to its ability to produce high volumes of parts with excellent precision and repeatability.
The injection molding process starts with feeding plastic pellets from a hopper into a heated barrel.
Once heated to a molten state, the plastic is injected under pressure into a mold.
The mold consists of two halves – an A-side (the cavity side) and the B-side (the core side).
When the mold is closed, these halves form a cavity that reflects the desired shape of the final product.
Components of the Injection Molding Machine
An injection molding machine consists of three major components: the injection unit, the mold, and the clamping unit.
The injection unit is responsible for melting the plastic and injecting it into the mold.
The mold is the tool that shapes the molten plastic into the desired product.
Finally, the clamping unit is responsible for holding the mold halves together during injection and cooling.
Materials Used in Injection Molding
A wide variety of thermoplastic polymers can be used in injection molding, each with specific properties that suit different applications.
Common materials include polypropylene, polyethylene, polystyrene, and polycarbonate, among others.
The choice of material depends on factors such as the product’s mechanical strength, flexibility, clarity, and chemical resistance.
Key Steps in the Injection Molding Process
The injection molding process can be broken down into several key steps:
1. Mold Design
The design of the mold is crucial in ensuring a defect-free final product.
This includes considerations for the shrinkage of the material and designing the runners, gates, and cooling channels to optimize flow and solidification.
2. Injection
Once the mold is designed and set up, the plastic pellets are melted in the injection unit and injected into the mold under high pressure.
The pressure ensures that the entire cavity is filled and that the part maintains a uniform density.
3. Cooling
After injection, the plastic begins to cool and harden in the mold.
The cooling time depends on the thickness and complexity of the part.
Uniform cooling is critical to minimizing shrinkage and warping.
4. Ejection
Once the part has sufficiently cooled, the mold opens, and the part is ejected.
It’s important that the ejection system does not damage the part as it leaves the mold.
Preventing Common Molding Defects
Understanding the fundamentals of injection molding is essential in preventing defects.
Here are some key points to mitigate common issues:
1. Warping
Warping occurs when there is uneven shrinkage, causing parts to twist or bend.
To prevent this, ensure uniform cooling by designing effective cooling channels within the mold.
2. Sink Marks
Sink marks are indentations that can appear on the surface of the molded part.
These can be avoided by adjusting the packing pressure and ensuring the section thickness is uniform.
3. Flash
Flash is excess material that forms around the edges of the part.
This occurs when the mold does not close properly or when the injection pressure is too high.
Regular maintenance of the mold and appropriate pressure settings can help prevent flash.
4. Short Shot
A short shot happens when the mold cavity is not filled completely.
This can be due to low injection pressure, insufficient material, or an improper gate design.
Adjusting the filling pattern and increasing the injection pressure can solve this issue.
5. Bubbles and Voids
These defects are voids or small bubbles that form within the part.
Bubbles and voids often result from inadequate pressure in the mold cavity or excessive moisture in the material.
Ensuring proper drying of the material and increasing the injection pressure can help eliminate these defects.
Optimizing the Injection Molding Process
To achieve the best results in plastic injection molding, continuous optimization is necessary.
This involves fine-tuning the process parameters such as temperature, pressure, and cycle time to suit each specific material and part design.
Regular Maintenance
Regular maintenance of injection molding machines and molds is crucial.
This not only prevents defects but also extends the lifespan of the equipment, ensuring consistent quality in production.
Training and Development
Continuous training and development of personnel involved in the injection molding process is another key factor.
An experienced and knowledgeable team can identify and solve potential issues swiftly, leading to more efficient production cycles and higher quality parts.
Conclusion
Plastic injection molding is a powerful technology in the manufacturing industry, capable of producing detailed and complex parts at high volumes.
By understanding the fundamentals of the process and addressing potential defects proactively, manufacturers can ensure high-quality outputs.
This not only saves time and costs in production but also advances innovation and growth in various industrial sectors.
資料ダウンロード
QCD調達購買管理クラウド「newji」は、調達購買部門で必要なQCD管理全てを備えた、現場特化型兼クラウド型の今世紀最高の購買管理システムとなります。
ユーザー登録
調達購買業務の効率化だけでなく、システムを導入することで、コスト削減や製品・資材のステータス可視化のほか、属人化していた購買情報の共有化による内部不正防止や統制にも役立ちます。
NEWJI DX
製造業に特化したデジタルトランスフォーメーション(DX)の実現を目指す請負開発型のコンサルティングサービスです。AI、iPaaS、および先端の技術を駆使して、製造プロセスの効率化、業務効率化、チームワーク強化、コスト削減、品質向上を実現します。このサービスは、製造業の課題を深く理解し、それに対する最適なデジタルソリューションを提供することで、企業が持続的な成長とイノベーションを達成できるようサポートします。
オンライン講座
製造業、主に購買・調達部門にお勤めの方々に向けた情報を配信しております。
新任の方やベテランの方、管理職を対象とした幅広いコンテンツをご用意しております。
お問い合わせ
コストダウンが利益に直結する術だと理解していても、なかなか前に進めることができない状況。そんな時は、newjiのコストダウン自動化機能で大きく利益貢献しよう!
(Β版非公開)