- お役立ち記事
- Fundamentals of plastic injection molding technology and key points to prevent molding defects
月間77,185名の
製造業ご担当者様が閲覧しています*
*2025年2月28日現在のGoogle Analyticsのデータより
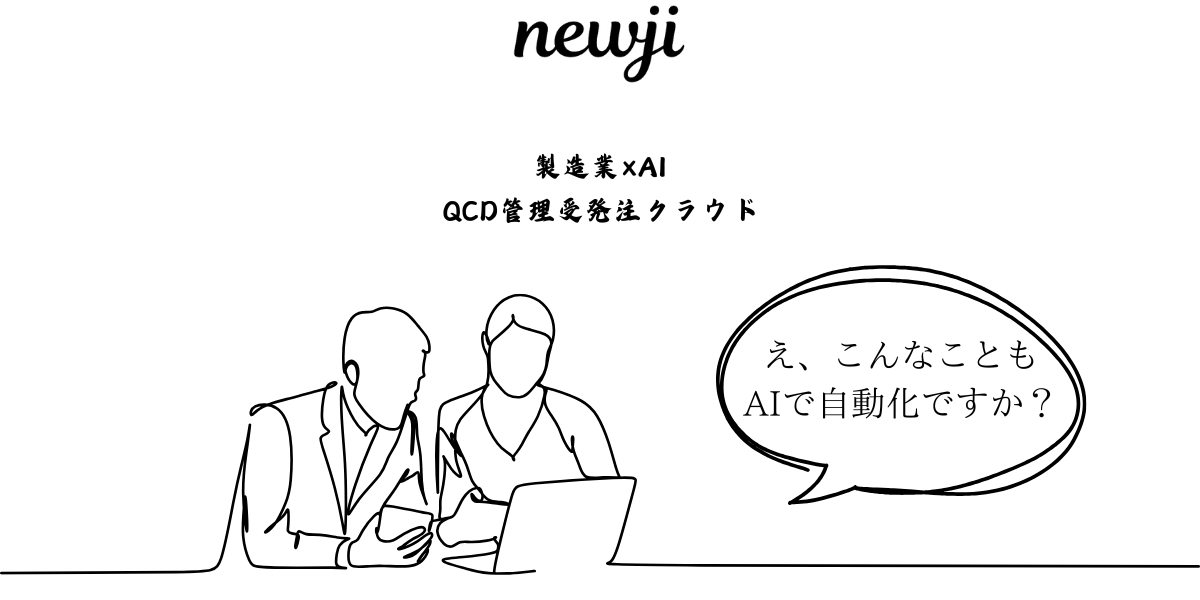
Fundamentals of plastic injection molding technology and key points to prevent molding defects
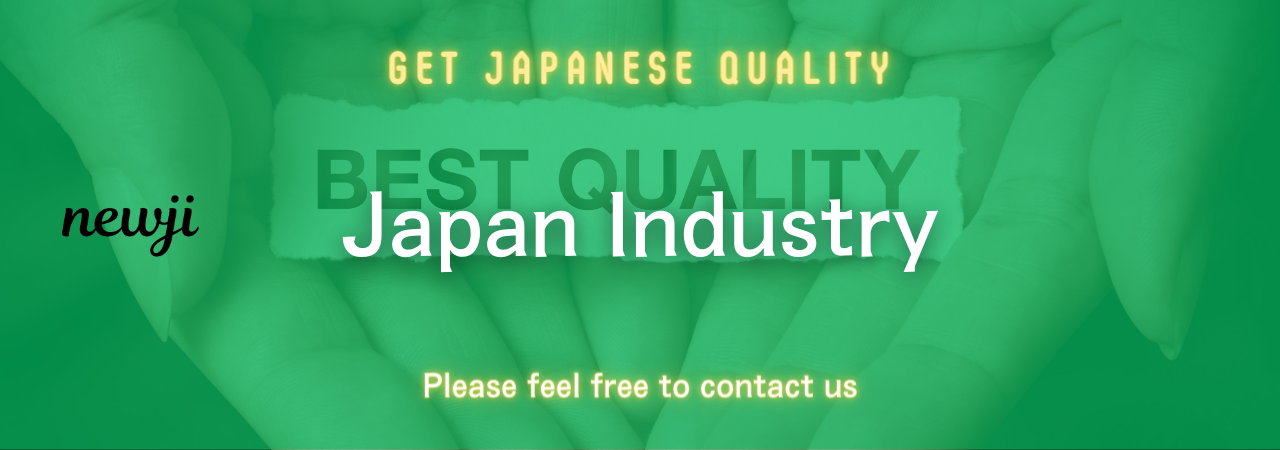
目次
Understanding Plastic Injection Molding Technology
Plastic injection molding is a highly advanced manufacturing process used to create a wide variety of products.
It involves injecting molten plastic material into a mold cavity, which then cools and hardens to form the desired part or product.
This technology is crucial in producing everything from small components to large automotive parts.
Understanding the fundamentals of plastic injection molding can help manufacturers optimize production and minimize defects, ensuring both efficiency and quality.
The Basic Process of Injection Molding
The injection molding process begins with the feeding of plastic granules or pellets into the injection molding machine’s hopper.
These materials are then heated and melted into a viscous fluid in a barrel.
Once the plastic is adequately melted, it is injected into a mold cavity under high pressure through a screw or plunger system.
The material fills the mold, capturing every detail of its shape.
After the plastic fills the mold, it is cooled to solidify.
This cooling phase is critical, as it affects the final quality of the part.
The mold is then opened, and the newly formed component is ejected.
The cycle then repeats, allowing for mass production of identical parts.
Key Elements of Injection Molding
Several elements are crucial in the injection molding process to ensure success and high-quality outcomes.
Material Selection
The choice of plastic material significantly affects the molding process.
Each type of plastic has different physical properties, such as melting temperature, durability, and flexibility, dictating how it behaves during injection and cooling.
Selecting the right material is vital for producing parts that meet required specifications and performance standards.
Mold Design
The design of the mold directly impacts the success of the injection molding process.
The mold must be precisely engineered to accommodate the thermal and mechanical stresses of molding.
It should allow for uniform cooling and easy ejection of the finished part.
Additionally, mold design should consider potential areas for defects, such as warping or air entrapment, and incorporate features to minimize these risks.
Machine Parameters
Operating the injection molding machine with the correct parameters is essential to ensure optimal performance.
Key parameters include injection pressure, temperature, and cycle time.
Adjustments to these settings can help achieve the desired quality of the molded parts and reduce the risk of defects.
Preventing Common Molding Defects
Defects in molded parts can occur due to various factors, such as mold design, material properties, and processing conditions.
Recognizing and addressing these potential issues is vital for maintaining high manufacturing standards.
Flash
Flash occurs when excess material escapes from the mold cavity and creates thin protrusions on the part.
This defect is often due to poorly fitting mold halves or insufficient clamping pressure during injection.
To prevent flash, ensure that the mold is properly aligned and that the machine settings are correctly calibrated to maintain adequate clamping force.
Warping
Warping results in a distortion of the finished part, usually caused by uneven cooling in the mold.
It can also stem from material inconsistencies or poor mold design.
To minimize warping, focus on uniform cooling across the entire part and select materials with similar shrinkage rates.
Additionally, ensure the mold design supports even material flow and cooling.
Sink Marks
Sink marks appear as small depressions or indentations on the surface of a molded part.
They often occur when thicker sections of the part cool and contract slower than thinner areas.
To avoid sink marks, design parts with uniform wall thickness and optimize cooling times.
Reducing the material at thick sections and increasing cooling time can mitigate this defect.
Short Shots
A short shot is a defect where the molded part is incomplete due to material not filling the entire mold cavity.
This issue can arise from too low a temperature or inadequate injection pressure.
Increasing the material temperature and pressure can help ensure sufficient filling of the mold.
Checking the design for any existing obstructions that may impede material flow is also important.
Optimizing the Injection Molding Process
Manufacturers can implement several strategies to enhance the injection molding process, minimizing defects and improving overall efficiency.
Regular Maintenance
Regular maintenance of injection molding machines and molds is crucial to prevent unexpected breakdowns and ensure optimal performance.
Regularly inspecting and servicing equipment helps maintain consistency in production and prolongs the lifespan of machinery and molds.
Quality Control
Establishing comprehensive quality control measures is vital for identifying defects early in the production process.
Implementing standardized inspection protocols can help detect and address issues quickly, reducing waste and improving product quality.
Continuous Training
Investing in training programs for operators and engineers can enhance their skills and understanding of the injection molding process.
Educated personnel can better identify potential problems and implement effective solutions, leading to higher efficiency and reduced defect rates.
Conclusion
Mastering the fundamentals of plastic injection molding technology is key to successful manufacturing.
By understanding the process, selecting appropriate materials, designing efficient molds, and optimizing machine parameters, manufacturers can reduce defects and improve product quality.
Preventing common defects such as flash, warping, sink marks, and short shots requires careful attention to detail and continuous process optimization.
With the right strategies and a focus on quality, injection molding can yield highly efficient and effective production outcomes.
資料ダウンロード
QCD管理受発注クラウド「newji」は、受発注部門で必要なQCD管理全てを備えた、現場特化型兼クラウド型の今世紀最高の受発注管理システムとなります。
ユーザー登録
受発注業務の効率化だけでなく、システムを導入することで、コスト削減や製品・資材のステータス可視化のほか、属人化していた受発注情報の共有化による内部不正防止や統制にも役立ちます。
NEWJI DX
製造業に特化したデジタルトランスフォーメーション(DX)の実現を目指す請負開発型のコンサルティングサービスです。AI、iPaaS、および先端の技術を駆使して、製造プロセスの効率化、業務効率化、チームワーク強化、コスト削減、品質向上を実現します。このサービスは、製造業の課題を深く理解し、それに対する最適なデジタルソリューションを提供することで、企業が持続的な成長とイノベーションを達成できるようサポートします。
製造業ニュース解説
製造業、主に購買・調達部門にお勤めの方々に向けた情報を配信しております。
新任の方やベテランの方、管理職を対象とした幅広いコンテンツをご用意しております。
お問い合わせ
コストダウンが利益に直結する術だと理解していても、なかなか前に進めることができない状況。そんな時は、newjiのコストダウン自動化機能で大きく利益貢献しよう!
(β版非公開)